Editor’s note: After participating in this interview and before this publication, Dr. Ron Abbott retired from Chevron Phillips Chemical after 31 years with the company.
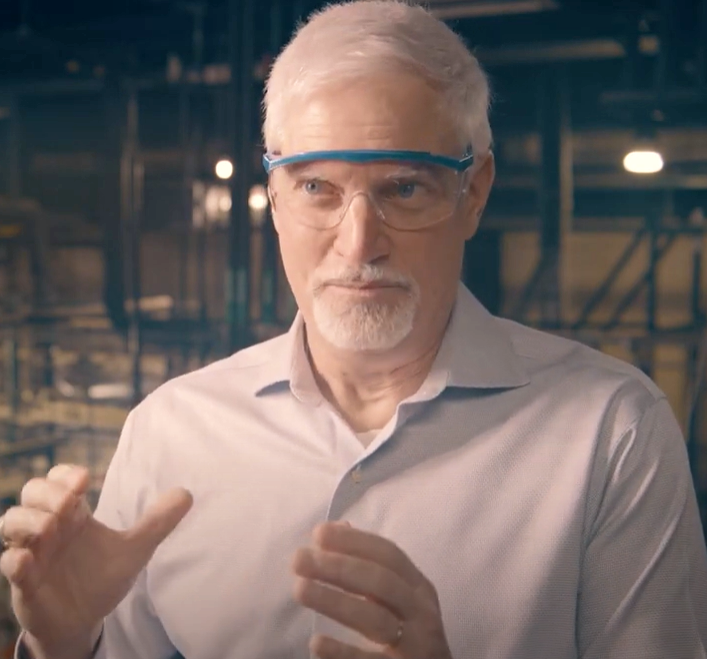
AFPM sat down with Dr. Ron Abbott, Ph.D., the Sustainability Technology Manager at Chevron Phillips Chemical. A 31-year veteran of the company and holder of 26 patents, Dr. Abbott is responsible for technical programs that advance long-term global sustainability objectives, like advanced recycling. Dr. Abbott was recently featured in AFPM’s recent “Recycling Reimagined” video.
You’re the sustainability technology manager for Chevron Phillips Chemical. What does that job entail?
My job is to work on advanced recycling to get plastic waste out of the landfill and back into commerce by creating feedstock from that waste, which we can then reuse to make circular plastic.
I was asked to take on this role because we wanted to leverage new technologies to enhance what was currently being done with mechanical recycling and layer on a complementary approach that involves difficult-to-recycle waste plastics.
Why are plastics so important?
Plastics are light, durable and energy efficient. It helps make our day-to-day lives possible.
For example, plastics play a critical role in food packaging and food management by helping prevent food spoilage. For example, 1.5 grams of plastic film around a cucumber will extend the shelf life of that cucumber from three days to up to 17 days.
Plastics play an essential role in modern society, but we have to find a way to deal with those materials at the end of their useful life. By reusing plastics, we keep the benefits of all those applications and minimize plastic waste.
Has the plastic waste problem changed over time?
Yes. Packaging around the world used to be very simple, but over the years packaging has become much more sophisticated. Years ago, there might just be one simple polymer component. But today, where the trends have been to get lower-carbon, more fuel-efficient packaging options out into the public, we now have sophisticated packaging made with all kinds of plastic materials — multilayer structures that meet the current demand for lightweight, high-performing packaging applications. But this packaging can't be mechanically recycled.
So we can’t just recycle more plastic waste with current systems?
Today in the US, we recycle only about 9% of all plastics. Another 70% or so ends up in landfills and the balance is typically converted in waste-to-energy processes to fuel utilities.
Ideally, we would want to take that 70% of material that goes to landfill today, retrieve those valuable molecules and bring them back into commerce. And not just one time. We want to use them again and again.
And now that legislators, brand owners and society in general are demanding higher recycled content, advanced recycling is a very important part of the circular economy because we have both the technology to convert plastic waste back into feedstock and a growing market demand for more recycled content in packaging today.
What are the limits of mechanical recycling?
Mechanical recycling is when you take a plastic component and you grind it, wash it, dry it, and then you remold it into something new. So, for example, you take a milk jug that's been used, you clean it, you grind it up and you can make another jug out of that. And that process works really well for certain streams – streams that are clean, that are typically comprised of one polymer type and that are suitable for the next application.
But that means that you generally can't use mechanical recycling for sensitive applications that are highly regulated, like food contact or pharmaceutical use. So, while that milk jug could be mechanically recycled into another jug, unless it's food-grade mechanical recycling, it could not be used for food contact.
How does advanced recycling help?
What we’re doing with advanced recycling is taking those hard-to-recycle plastics – say a mixture of polypropylene and polyethylene, for example – and we’re decomposing them in an air-free environment to reduce them to a liquid. Then we take a long-chain hydrocarbon and make a short-chain hydrocarbon, and that's our feedstock.
The beauty of this is that you can take that feedstock and make it into a brand-new plastic component that's 100% recycled. And because it has the same specificities as a virgin polymer, it’s suitable for food contact or for pharmaceutical use.
That's why advanced recycling fits so nicely as a complementary approach to mechanical recycling. Because now in addition to mechanical recycling – keep doing that – we can take the materials that are not suitable for mechanical recycling and find a home for those hydrocarbons, too.
You’re saying that plastic waste has value, that it’s a resource?
Yes, it is. And if we don’t recycle plastics, we’re wasting that resource. Our goal is to grow the circular economy, to get these valuable molecules, these hydrocarbons out of landfill and put them to work again and again. And advanced recycling can help us achieve that goal.
You sound very passionate about this.
I'm a grandfather now. I have a 14-month-old granddaughter and she's beautiful. We need to be thinking about what her world will look like in 20, 30, 40 years, what her life is going to look like. Having a granddaughter has just amplified, in my mind, the significance of what we're doing in this technology because we've got to find a way to have a clean and low-carbon future for all of us.
Today, we've got to do a better job as a society. This isn't just an industry thing. This is a societal thing. We have got to reuse our resources and we have to use our resources wisely. Right now, most materials, packages of all types, for glass, paper, aluminum, plastic, most materials go through our system one time, and then they go to a landfill. And that's not acceptable.