This article originally appeared on Politico.
In 2019, Chevron Phillips Chemical (CPChem)’s Sustainability Technical Manager Ron Abbott was given a seemingly insurmountable challenge: by 2020, make CPChem the first company in the U.S. to announce commercial production of a circular polymer made by converting plastic waste into the chemical building blocks for new plastic. A cross-functional team was launched and started chipping away at the goal.
Fast forward to October of 2020 — CPChem’s team announced successful commercial scale production of Marlex® Anew™ Circular Polyethylene. The material is physically identical to polyethylene resins normally produced from ethane, the natural gas liquid feedstock (the raw materials used for plastic production), but it is produced from a liquid feedstock created by breaking down and recycling waste plastic. This process both diverts difficult-to-recycle plastics from landfills and reduces the amount of conventional feedstock required.
“We identified a few companies with the commercial scale technology to take difficult-to-recycle materials and reclaim their hydrocarbons in a form suitable for our production process,” Abbott said. “The long-term goal is to get polyethylene out of landfills and back into circulation. We must convert our economy to a circular economy where we reclaim these valuable resources we are currently landfilling.”
The company has already set a new goal: produce 1 billion pounds of Marlex® Anew™ Circular Polyethylene from recycled plastic by 2030.
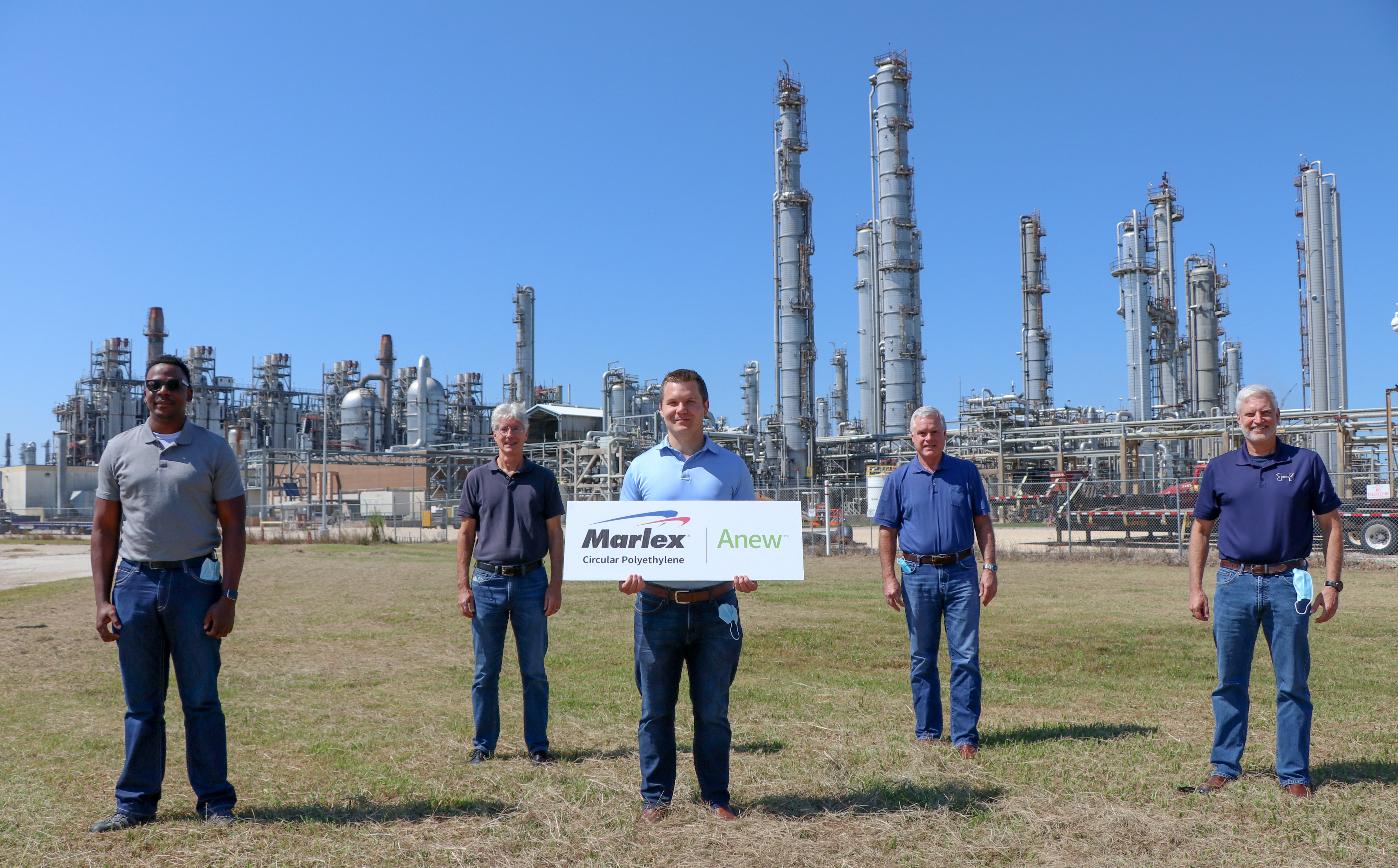
CPChem’s achievement marks a critical turning point for advanced plastic recycling in the U.S. where customers, driven by concerns about plastic waste entering the environment, are demanding that more products be produced using recycled materials, rather than virgin plastic. This concept of transforming plastic waste to usable feedstocks to produce more products is being embraced and advanced, not only by CPChem, but by the broader petrochemical industry as they look for solutions to address mismanaged plastic waste.
While most petrochemical manufacturers do not produce plastic feedstocks directly, they do produce the petrochemicals from these feedstocks, which are then processed into resins and pellets that their customers ultimately mold into a variety of plastic products. The entire plastics value chain sees advanced recycling technology as a complementary component to meet ambitious recycling goals and address plastic wastes challenges.
And it all starts with petrochemical manufacturers.
“A big part of the solution is going to come from the petrochemical industry because they have the scale, the knowledge and the reach to really change how things are done with consumer packaging going forward,” said Professor Mike Hickner, a chemical engineering professor at Penn State University, who studies polymers. “The fact of the matter is that we are only making more plastic materials overall,” he said. “We are never going to use fewer materials than we use today. The population and demand are continuing to grow.”
To meet this challenge, petrochemical companies are scaling advanced recycling — a new frontier in recycling that deconstructs difficult-to-recycle plastics at the molecular level so they can re-enter the value chain.
Traditional, mechanical recycling systems take used plastic products, sort them by type, grind, wash and then re-melt them into new plastic objects. This process does not intentionally break the polymers’ chemical bonds. Mechanical recycling enables various common products to be made from recycled content, but has limitations — for example, not all plastic products can be used in the process, and others can only be recycled a handful of times before key properties, like strength, diminish.
But through advanced recycling (also called chemical or molecular recycling), a wider range of used plastic products can be broken down at the chemical level and converted to feedstocks for new polymers, which can then be transformed into thousands of consumer products. Since the polymer is transformed back to basic building blocks, this process can be repeated multiple times without jeopardizing the strength and quality of the final polymer. This enables manufacturers to expand the boundaries of how, and where, recycled plastics are used.
“New and innovative recycling technologies enable us to capture a broader spectrum of our plastic waste, processing materials at higher contamination levels,” said Cassie Bradley, sustainability and circular economy commercial manager at INEOS Styrolution America, one of the largest global producers of polystyrene, commonly used in packaging for food and other goods. Polystyrene’s unique chemical makeup allows it to be easily sorted from other polymers using infrared sorting technology. “Polystyrene’s inherent properties are so well suited for advanced recycling that it is leading the way in adoption of this groundbreaking technology,” Bradley explained.
Polystyrene is incredibly versatile and can be used in both mechanical and advanced recycling. Now, its long polymer chains can be “unzipped” to bring the material back to its original monomer form, offering a truly circular solution.
“Just think if you had a stack of toy blocks and you broke it up into individual blocks, you could then reattach those [pieces] back into that tower again, which is what we are doing when we are repolymerizing it,” Bradley said.
ExxonMobil is also expanding its recycling efforts, investing heavily in Vistamaxx performance polymers, which can blend two types of plastics, polyethylene and polypropylene, in mechanical recycling processes, eliminating the need to separate them. The company’s $2 billion Baytown chemical plant expansion project, expected to start up in 2022, includes a new performance polymer unit, which is on track to produce about 400,000 tons of Vistamaxx polymers each year. ExxonMobil has also announced advanced recycling efforts at its Baytown, Texas, facilities — highlighting that mechanical recycling and advanced recycling are complementary approaches to mitigating plastic waste.
In January, Tennessee Governor Bill Lee joined Eastman Chemical Company CEO Mark Costa in announcing the company’s plans to build one of the world’s largest plastic-to-plastic molecular recycling facilities at its site in Kingsport, Tennessee, an anticipated investment of more than $250 million over the next two years.
“With the growing demand for products made with recycled content and the urgent need to address the global plastic waste crisis, now is the time for Eastman to take this step,” said Costa. “This will be a great investment for our local community and our customers, while also creating small business jobs to develop the recycling infrastructure necessary to support investment in a sustainable future.”
LyondellBasell has taken a multifaceted approach to meet its ambitious goal to produce and market 2 million metric tons of recycled and renewable-based polymers by 2030. This approach includes the startup of an advanced recycling pilot plant to test the application of the company’s MoReTec technology on an industrial scale. It will expand the capacity of the company’s mechanical recycling joint venture — Quality Circular Polymers — to 55,000 tons per year and launch a new suite of advanced recycling products under its Circulen brand name.
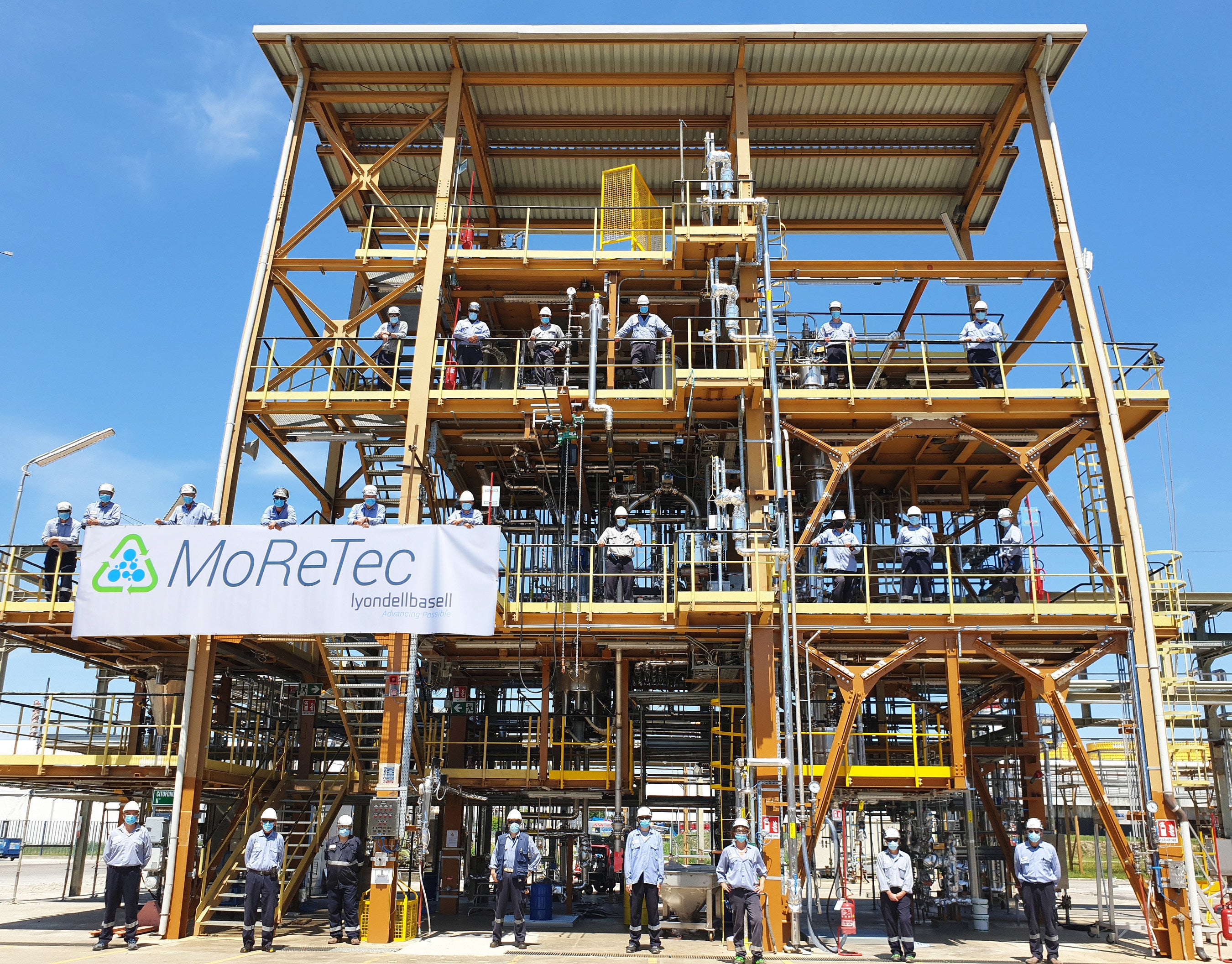
“LyondellBasell’s deliberate approach to providing more sustainable solutions helps address some of the world’s most pressing challenges,” said Andrea Brown, LyondellBasell director of global sustainability. “The work we are doing drives meaningful progress toward reducing plastic waste in the environment, helping to mitigate climate change and contributing to a thriving society for our employees, the communities where we operate and the people who depend on our products.”
Dow has seen strategic partnerships as key to achieving their goal to enable 100 percent of its products sold into packaging applications to be reusable or recyclable and to enable more than 1 million metric tons of plastic to be collected, reused or recycled. Overseas, Dow — in partnership with Fuenix Ecogy and Mura Technology — is developing circular polymers and scaling advanced recycling operations at its European facilities. Dow has even partnered with local governments and community leaders in areas where they operate to turn plastic waste into asphalt pavement for local roads and parking lots.
The global community is also recognizing the promise and progress in advanced recycling. In fact, International Sustainability & Carbon Certification (ISCC), an internationally recognized independent organization that provides a global certification system for the sustainability of raw materials and products, has awarded a number of petrochemical facilities in the U.S. (including certain facilities belonging to CPChem, INEOS, LyondellBasell and ExxonMobil), with its ISCC PLUS certification for a company’s successful, commercial-scale production of advanced recycling technologies.
As more of these projects come online, petrochemical companies are now navigating a regulatory environment that is not yet reflective of this new technology. “Instead of fostering these innovations, we are facing state and federal legislation that would institute all-out bans on various plastic products,” said Rob Benedict, vice president, petrochemicals and midstream for the American Fuel & Petrochemical Manufacturers (AFPM) trade association. “The regulatory environment here in the U.S. must remove regulatory barriers and leverage our petrochemical industry’s expertise so that the U.S. can seize the opportunity to become a global leader in advanced recycling.”
“Plastics enable incredible things in our lives — it is impossible to imagine a modern hospital, grocery store, school or workplace without them,” said Chet Thompson, president and CEO of AFPM. “Our commitment to sustainability includes working to advance data-driven public policies that recognize plastics’ benefits, while also addressing mismanaged plastic waste and encouraging advanced recycling projects. This technology is completely redefining what is possible through recycling, and it is a critical part of the cross-value chain approach to keeping plastic waste out of the environment.”
Abbott from CPChem agrees.
“This is the environmental challenge of our generation,” said Abbott. “We have to fix this together. I think we’re well on our way.”