Filling the job vacancies left in the wake of the Baby Boomer Retirement Wave is proving to be particularly difficult for the manufacturing sector.
According to the latest “Skills Gap and Future of Work” study by Deloitte and The Manufacturing Institute, most manufacturers believe that the number-one cause of the current skills shortage is a “shifting skill set due to the introduction of new advanced technology and automation,” followed by “negative perception of students/their parents toward the manufacturing industry.”
To counter this one-two punch – finding technologically savvy job applicants who also appreciate the value of the manufacturing sector – the petrochemical and refining industries made a concerted effort over a decade ago to expand and improve their internship and apprenticeship programs.
And those efforts are paying off.
“Back in 2005, INEOS, one of the world’s largest petrochemical producers, had the foresight to recognize that many job applicants simply didn’t have the technological skillsets that we needed,” said Kay Ellison, Maintenance Training Coordinator for INEOS Battleground Manufacturing Complex in LaPorte, Texas. “Specifically, we looked at the technical capabilities of the people applying for our millwright positions and saw an educational gap.”
So INEOS and several other companies in the area partnered with the College of the Mainland, a public community college in Texas City, to create a curriculum designed to teach the skillsets needed for millwrights to be able to repair today’s more technologically advanced equipment.
According to Kay, it took a couple of years to build out the program to a point where “we could hire individuals while they were still taking classes at school and have them work in the plant as paid apprentices, side by side with our maintenance technicians.” Now, “not only are they receiving the formal training that the company has blessed, these apprentices are also in the plant, applying the skills they learned on a daily basis.”
After completing this three-year overlapping apprenticeship program, successful candidates will have the education and skillsets that INEOS demands in the millwrights they hire. But just being selected for the apprentice program is a dream come true for people like Kyle Platt.
“It was one of those moments when you tell your parents and they start crying,” Kyle said.
As an apprentice, Kyle received a salary and benefits, including a 20 percent bonus every year. He began at $17.50 an hour and got a raise every 6 months, and once he finished his apprenticeship, his pay went up significantly. By the time Kyle was just 25, he was making six figures.
Today Kyle is a top INEOS technician who trains new apprentices as they come in.
Kyle said his method “is to slow down, never rush.”
“I took what they taught me and then adapted it to reflect my own style of teaching,” he said. “I speak more slowly and let them get a solid grasp on the concept before moving onto the next lesson.”
Teaching the student to become the master is a fundamental part of the industries’ internship and apprenticeship programs.
As experienced employees retire and innovation continues to transform every facet of the manufacturing sector, young employees are being called on to help train their peers.
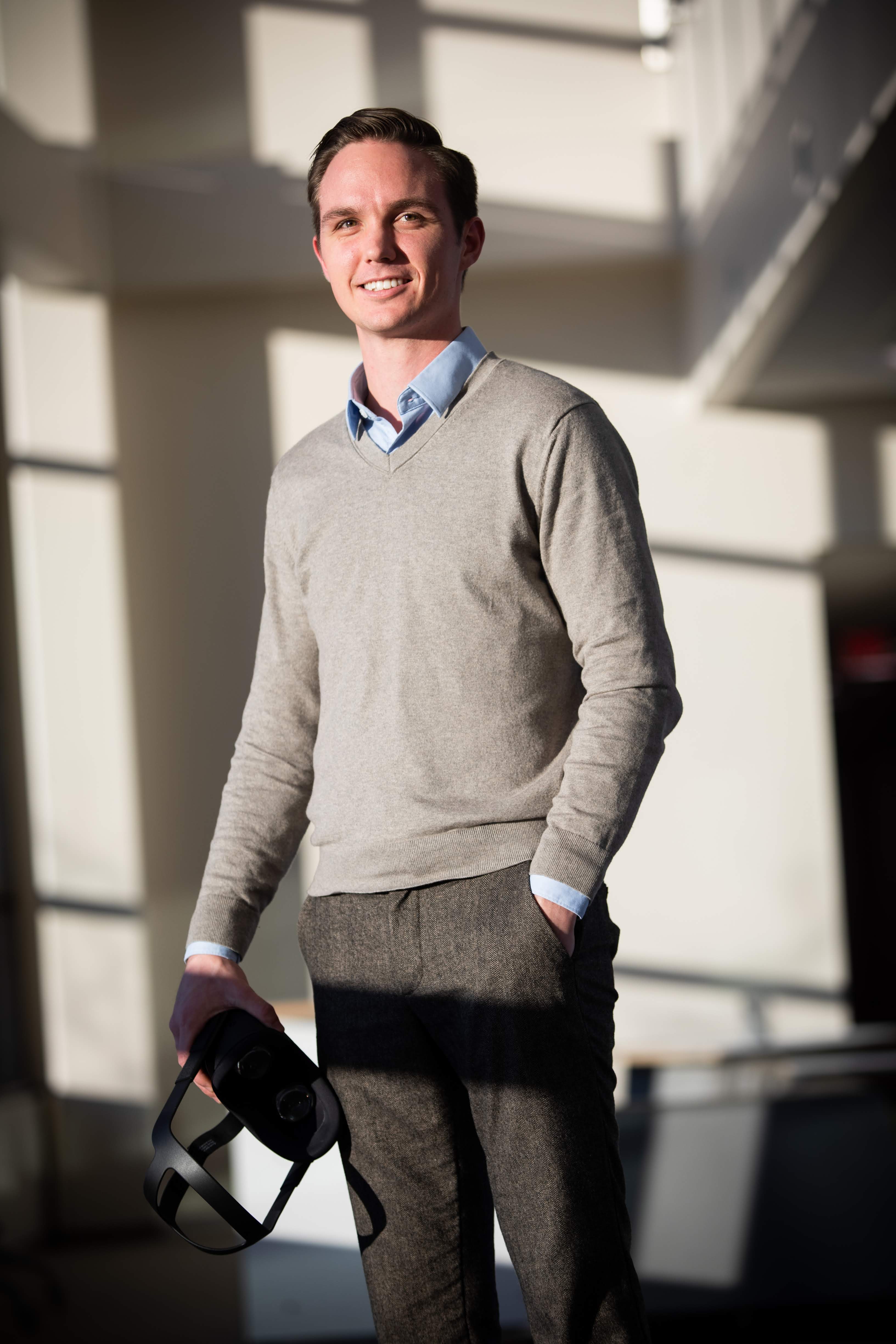
Dane Laughlin started as an intern at INVISTA, a subsidiary of Koch Industries that brings to market the proprietary ingredients for nylon and recognized brands including STAINMASTER®, CORDURA® and ANTRON®. Today he works there as an innovation engineer. “Innovation engineers are like forward-looking specialists for the company,” he said. “We look for ways to use our technology to make people’s lives easier or their jobs more efficient.”
Part of his job is to train employees using virtual reality (VR) and augmented reality (AR) technology.
“As part of manufacturing process, we take molten nylon and turn it into string that goes onto spools,” he said. “In the past, it has been difficult to teach this process. It involves manual dexterity that requires a lot of practice, and it’s a loud environment that requires hearing protection so it can be a challenge to communicate. But virtual reality is ideal for this. It’s easy to practice and can be done in a more learning conducive environment.”
“The other cool thing about VR is that you can have three to four people in one room going through the same training at once,” he said. “And as a trainer I can watch them on the split screen and give them feedback in real time.”
One key to success with today’s internship and apprenticeship programs lies in finding applicants with the right attitude. Where once prior experience or a particular aptitude for mechanics might get your foot in the door, today it’s all about attitude.
Kyle said he wasn’t particularly mechanically inclined before starting at INEOS. But he knew he had the desire and the ambition to be a successful millwright. “It’s all about the ‘want,’” he said. “Once you want to do something, it all comes together.”
Despite the challenges brought by the COVID-19 pandemic, our industries are continuing to train their future workforce and ensure they will have the talent needed to continue innovating to meet the world’s fuel and petrochemical needs.