Question 79: How do you mitigate the risk of falling coke deposits from the reactor plenum chamber and vapor line during initial vessel entry?
INKIM (PETROTRIN)
We have not had the experience of falling coke deposits on vessel entry. We usually experience difficulty in removing the coke deposits, and we do this by mechanical means. Prior to entry into the reactor, a visual inspection is made from the manway. It is typical to see stalactites from the reactor plenum. However, there have not been any cases of falling coke deposits. On the reactor vapor line, there is usually a thin coating of coke throughout. Generally, the vessel entry is done from the manway above the reactor stripper. Scaffolding is built from the top of the reactor stripper upwards. During the coke removal process, the top section of the reactor is totally boarded off to prevent any coke from falling to the areas below where work may be ongoing.
BULL (Valero Energy Corporation)
are various methods to mitigate the risk of coke falling. One of them is a proactive approach we have taken in various locations where we have seen coke form. We installed anchors to try and stabilize the coke. On our initial entry, we will go from the top to the bottom; starting at the plenum chamber. From the manways, they will initially go in and probe for coke and try to knock it down. From there, we will go down the reactor structure and then install seal decks at different locations in the structure.
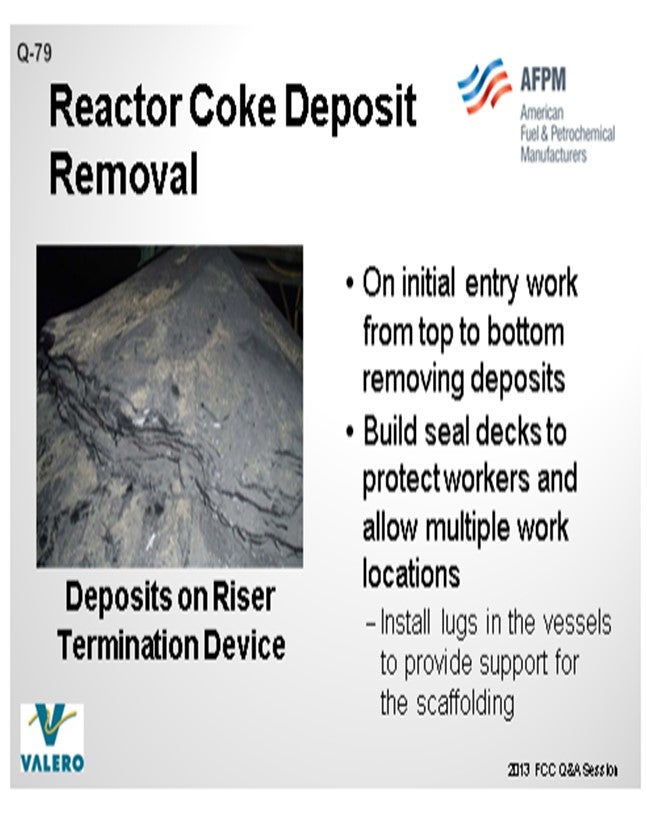
As part of the coke removal process, we have also put lugs at various locations inside the reactors to allow scaffolding to be put in more quickly. From a process standpoint, we also attempt to maintain a high enough flux to the reactor and vapor line to minimize the amount of coke that is formed. If there are any stagnant areas, we will also use a steam flow to try and keep some flux in the area. The last part of the question is about the vapor line. Before we startup, we will look at how much coke formation is there; and then depending on the quantity, we will actually go in to clean that out as well.
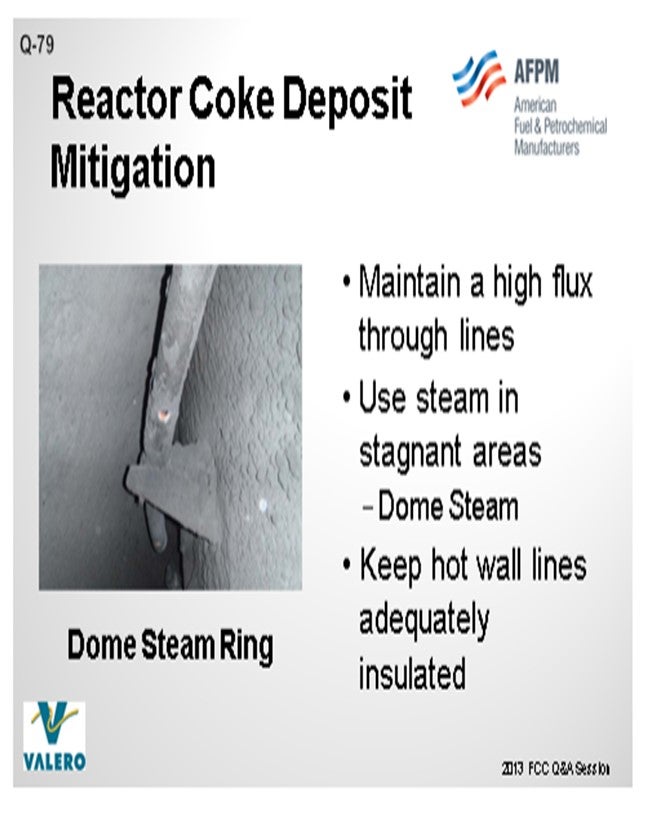
ROBERT “BOB” LUDOLPH [Shell Global Solutions (US) Inc.]
I have found the effectiveness of dome steam to be hit-or-miss. What are the experiences of the panelists?
BULL (Valero Energy Corporation)
We have standards, Bob, that we work towards at each refinery. We have significantly increased our dome steam rates to four or five times the early design numbers, and we have seen improvements in those reactors after we have left.
INKIM (PETROTRIN)
When our reactor was replaced, we initially did not have any dome steam. At the first turnaround following the replacement, we found a heavy layer of coke deposits in the reactor dome which we had to jackhammer out. We have subsequently introduced dome steam, and now we have just the stalactites that could be removed. That was what worked for us.
LARSON (KBC Advanced Technologies, Inc.)
I agree with you that it is hit-and-miss over the number of cat crackers I have been on and on which I have worked with clients. I would lump them into this statement: Those people who have it in believe it works, as opposed to really having done any analysis to prove that it is positively giving a value. I have been in places where they do not use it all, and they are quite happy not to put it in. They do not see a benefit one way or the other. So, I agree with you that there is not a single answer. I think configuration of how that dome and the disengages are being put in has changed the industry quite a bit, so it is not clear to us. Opinion seems to be a bigger issue than hard analytics.
PUI-NANG LIN (Flint Hills Resources)
We do have dome steam application in our cat reactors. The key appears to be the ability to maintain a good steam chamber seal because the steam purge velocity is always hard to maintain after one or two turnarounds. These seal baffle gaps get bigger and bigger because they get warped from coke buildup. When we cannot maintain that perfect seal between the baffle plate, vessel wall, and explosion doors, we end up with even more coke buildup, both above and below the baffle. So, I think after the first turnaround, if you can maintain a good steam chamber seal, you should be fine.
CATHERINE INKIM (PETROTRIN)
We have not had the experience of falling coke deposits on vessel entry. We usually experience difficulty in removing coke deposits which is done by mechanical means.
Prior to entry to the reactor, a visual inspection is made from the manways. It is usual to see stalactites from the reactor; however, there have been no cases of falling coke deposits. On the reactor vapor line, there is usually only a thin coating of coke throughout.
Generally, vessel entry is done from the manway above the reactor stripper. Scaffolding is built from the top of the stripper section upwards. During the coke removal process, the top section of the reactor – plenum and cyclone area – is totally boarded off to prevent coke falling to areas below where work may be ongoing. Tarpaulin is used to aid in the collection of falling coke material.
JEFFREY BULL (Valero Energy Corporation)
We have used various methods to mitigate the risk of falling coke. One of those methods is to place anchors in areas where coke has historically formed in the reactor to give the coke a surface to which to adhere so that it is not prone to falling off either by being thermally shocked or during initial vessel entry. At most of our refineries, we will open all the manways on the reactor and probe for heavy coke deposits prior to entry. We start at the plenum chamber and move down the reactor structure. Most of the time, we are able to knock down some of the deposits from the support beams. The coke on the cyclone exteriors is normally much harder, and we have found that part difficult to remove. We then enter below the plenum at the manways and start chipping away where we can. This can be a slow process. In some cases, a seal deck is installed to allow work at multiple levels in the vessel. We have installed lugs in several sections of our reactors to provide extra support for the scaffolding. First, the reactor vapor line is often hydroblasted, and then another apparatus is used to remove the remaining deposits.
From a process standpoint, we try to maintain a high enough flux through the reactor and vapor line to minimize the amount of coke that is formed. In stagnant areas, we will use a steam flow to keep some flux in that area. Dome steam is common in the top of many of our reactors. We also try to keep our hot wall lines adequately insulated to keep cold spots from forming.