Question 56: With the current domestic conventional and unconventional crudes available, what incompatibility issues are observed from the tank farm through the crude unit? What mechanical, operational, and chemical strategies are employed to minimize these impacts?
PRIBNOW (CITGO Petroleum Corporation)
Incompatibility issues are mostly observed in the desalter and downstream pre-heat train and heater as the asphaltenes precipitate and cause stabilized emulsions. Some of our observations include salted crude carryover from the desalter. The water and contaminants exit the desalter and foul all of your downstream pre-heat exchangers and heaters. It may even upset your crude tower if it is bad enough. We have had a couple of instances where we have carried over badly and have pressured up the crude tower. So we have to really watch desalter operation when incompatibility issues arise. With the desalter, we will see level instability from false level readings and increased solids exiting with the brine. We will have oil undercarry with the brine from the desalter because regulator outputs will increase. We have also observed tight emulsions in the desalter.
Finally, since the last turnaround, we have observed more cold pre-heat train following in the first couple of exchangers. Exchangers that had not fouled in six to eight years are now fouling in six to eight months. So there is an increase in fouling that we are observing in our cold pre-heat train. We blend our crude types out in the tank farm prior to their entrance into the crude unit. When we start observing increased asphaltene precipitation, we will change the ratios of the different light/heavy crudes or paraffinic crudes and will usually see that phenomenon subside.
We use three proactive operational strategies. One is the ASIT method or the Asphaltene Stability Index Test. We have an analyzer onsite. We will test incoming crudes with that analyzer and fill out a database. We will also blend the crudes together to obtain the stability of the different blends. This is an analytical predictive tool which has worked well for us. We will segregate crudes based on type and compatibility so they can be safely blended. We also employ the ASIT method, which is a mathematical model used to isolate the incompatible crudes during the storage and blending phases. Then lastly, we employ upstream tank blending sequencing. We fill with the asphaltenic crude component first, and then we fill the paraffinic crude on the top. If it is done the opposite way, we have observed problems.
Chemical Strategy: We are injecting asphaltene stabilizer in our crudes when they come into the gate, before they enter the tank. We have had success with this strategy, and we have seen positive results with that chemistry. In order to be successful, we must inject far enough upstream. If injecting chemistry where crudes are blended, it is too late. The stabilizer must be injected way upstream to make sure that it is thoroughly mixed with the crude prior to meeting any light or heavy components. As I said, we have had some positive results to date with that chemistry.
HERLEVICH (Marathon Petroleum Corporation)
I want to follow up by sharing some very similar experiences that occurred at one of our plants. We run heavy Canadian crude. Because of the lack of receipt tankage, in order to retain containment, we ended up putting heavy Canadian crude on top of a light paraffinic crude. It resulted in 4 to 6 feet of precipitate in the bottom of the tank. While aware of the phenomenon, we still managed to get into this predicament. More common for us, though, is getting crude blends that, despite our best efforts to segregate in the tank farm, end up precipitating slightly and charging to the crude unit with some suspended particles. These particles result in fouling of the pre-heat exchanger and sometimes lead to emulsion growth in the desalter.
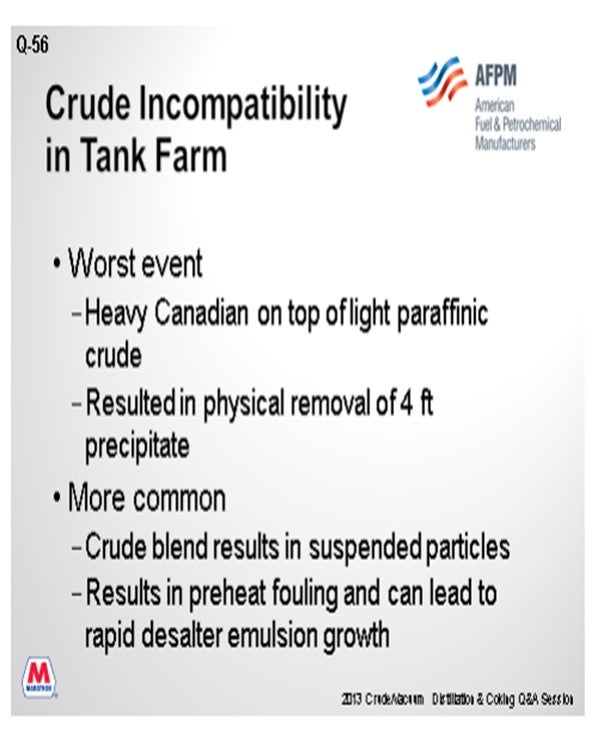
The next graphic is a sonar image of the precipitate on the tank bottom. The scanning company was able to lower a portable sonar device into tank and actually map it to determine the magnitude of the problem. This tank was out of service for a long time to remove the material.
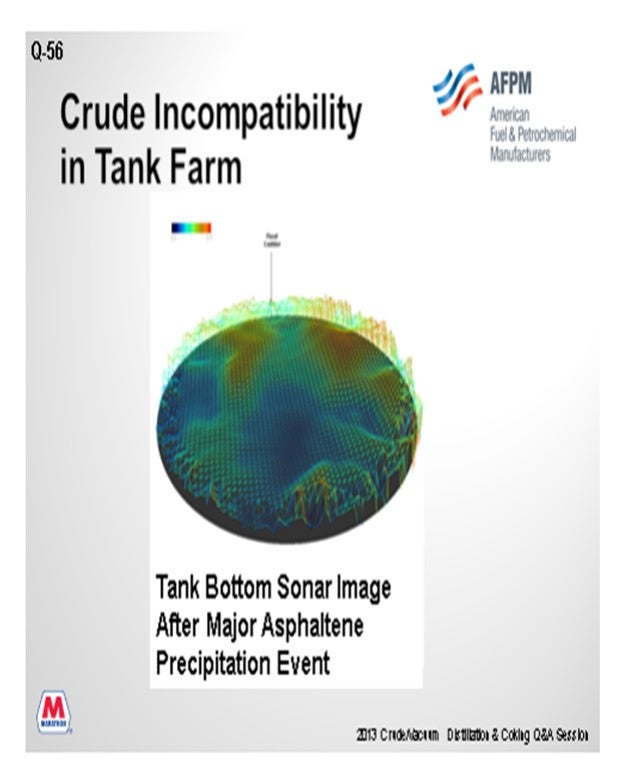
Similarly, in the tank farm we use asphalt stabilizers and a demulsifier chemical treatment program. In at least one of our refineries, we do the chemistry substantially upstream in the pipeline terminal system which is many miles away. This seems to work really well for that plant. We have also become very serious about our desalter agar probes. In the last several years, we have made big efforts to train the operators and engineers on the agar systems. As a result, the operators have been very successful with early identification of rag layer growth, even before a major desalter upset. I encourage you to get your control board operators to use desalter monitoring systems proactively. Our operators now reduce charge rate proactively if the agars indicate a problem. We also routinely monitor our heat exchanger performance, typically through the efforts of our college co-ops.
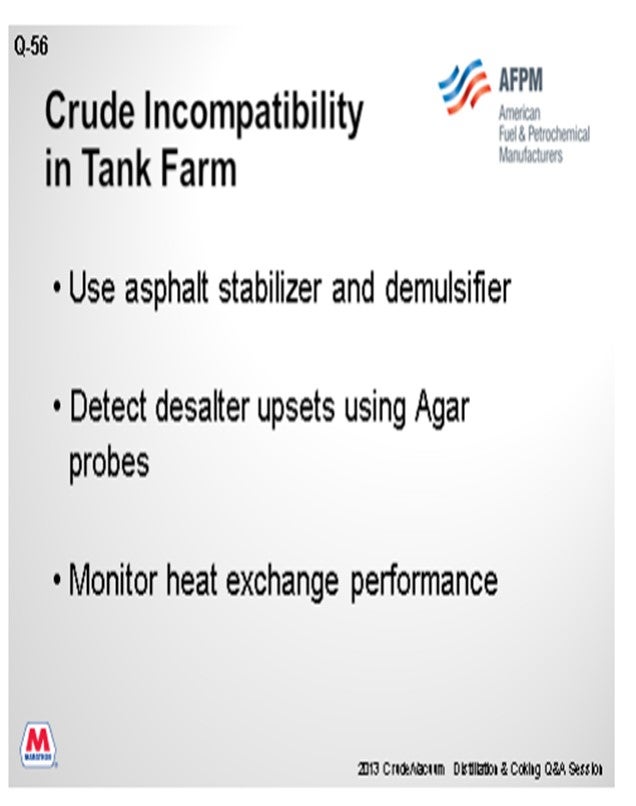
The next slide is a graphic of two water samples. On the left, you see the normal brine from one of our desalters; and on the right, you see what the brine looks like when we start experiencing an upset. It is really easy to observe upsets and early precipitation by looking at the brine draws.
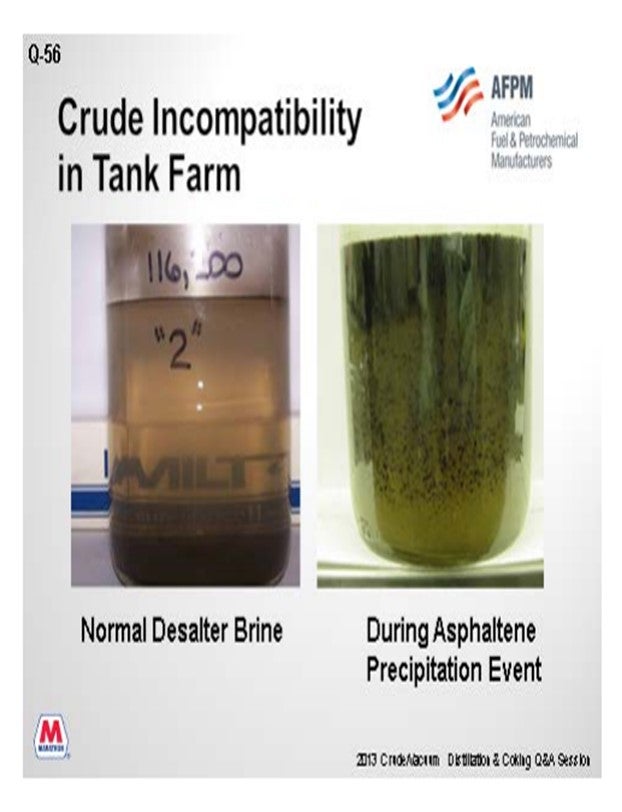
HODGES (Athlon Solutions)
There is a general awareness that tight oil processing requires a comprehensive management program encompassing several key factors including transportation, storage and blending, the impact on the LP (linear program) model, and the impact on finished fuel specifications. I encourage everyone to attend the P&P session this afternoon at 2:00 PM. There will be a lot more detailed discussion of tight oil processing, and I think you will get a lot out of that.
From a transportation, storage and blending perspective, you must focus on making sure you have an excellent surveillance program on your incoming shipments. There is great variability from tank truck to tank truck or railcar to railcar in tight crude. This is non-obvious unless you have taken the time to check it. With this information, you can develop the appropriate management strategies to assist you in segregation and blending.
The use of non-nitrogen, non-corrosive H2S scavengers is also a Best Practice when these oils are being shipped, either by rail or tank truck. By using these types of technologies and making sure they are specified in your incoming shipments, you can mitigate corrosion and salting associated with amine-based scavengers in your crude tower.
Another item to consider is use of novel wax inhibitors to prevent wax dropout, both in transit and in your onsite crude storage tanks. Also, be aware that there is a completely new host of upstream additives used in the completion of tight oil production. These additives can and do impact your desalting, fractionation, and downstream catalytic units. Develop a well thought-out management strategy with your chemical supplier to address the impact of these upstream additives as there are many options with upsides and downsides to consider. Finally, use a compatibility model, as discussed by Phil and others, to minimize your asphaltene insolubility and wax precipitation that results in feed line plugging, cold train fouling, and desalting problems. As Phil mentioned, if you use an asphaltene dispersant, we recommend that you feed it as far upstream as possible.
JESUS CABELLO (Foster Wheeler USA Corporation)
Have you seen any premature coking in the fire heaters?
PRIBNOW (CITGO Petroleum Corporation)
Yes. Since we had a turnaround and started seeing increased fouling in our cold pre-heat, we did start to see an increase in coker heater fouling.
HAROLD EGGERT (Athlon Solutions)
I want to add a second commercial. Tomorrow morning, there is also a P&P specifically focusing on tight oil issues. I encourage people to attend that. My question is probably for Phil. The asphaltene dispersant that you are adding, do you add it to the heavier of the crudes or to the lighter paraffinic crude?
PRIBNOW (CITGO Petroleum Corporation)
We add the stabilizer to only the heavy crude entering the refinery.
UNIDENTIFIED SPEAKER (Shell Global Solutions U.S.)
A question for Phil. You are popular! You mentioned that you used ASIT online analyzers to test the potential for compatibility problems. But for the crude purchase and crude delivery, as well as potential blends onsite, do you have enough lead time or storage time to do all of these blending trials before the site actually processes the crude? How do you manage that?
PRIBNOW (CITGO Petroleum Corporation)
We do not have enough storage and would like to have an infinite number of tanks. You are correct. As these tank shipments come in, it is hard to obtain the data and make those ratios or blends. Sometimes we do know that certain crudes are coming in which are more problematic because we have seen them before and have that database. In that case, we will make sure that when we do start that crude into the crude unit, we adjust the blend or know we need to have a stable percentage of that difficult crude coming in. Like you said, we are still learning that process, but it is difficult trying to obtain real-time data and passing it to the consoles, so they know what ratios to set.
JIM PROROK (Husky Oil Operations Ltd.) \
There was a question about whether we see an impact in the coking in the furnaces. We are mostly a light sweet and synthetic crude refinery, but they slip in a little bit of heavy and occasionally some lighter materials. We have had instances where the asphaltene precipitation appears to have coked the convection section in the crude furnace, as well as shock tubes, creating unexpected hot spots and coking. We also saw extreme fouling in the coker furnace, including not just the tubes, but also the transfer lines over to the coke drums.
GLENN SCATTERGOOD (Nalco Champion Energy Services)
Slop oil addition to crude slate may destabilize asphaltenes in the crude. Onsite testing of the proposed blend may predict the asphaltene stability. Careful blending of the slop oil and/or low addition rates may reduce or eliminate fouling due to asphaltene destabilization. Chemical additives are available to keep the asphaltene in solution and reduce fouling of the desalter and hot crude unit pre-heat exchangers.
DENNIS HAYNES (Nalco Champion Energy Services)
Incompatibility issues may occur if crudes are blended in a non-uniform way, inappropriate order, or incorrect amount. First, evaluate crude blends to determine relative compatibility and confirm a planned blend is not in an envelope that will cause challenges; next regarding order of addition, add a destabilizing crude to one that has the potential to destabilize; and not in the reverse order. Then, be cognizant of areas in the process, such as tank storage, where stratification may lead to variation in blend component concentrations impacting blend compatibility. When there is concern regarding blend compatibility, application of an asphaltene stabilizer additive may assist in minimizing deposition on process equipment or reducing interference in areas such as desalter interfaces.
GREG SAVAGE (Nalco Champion Energy Services)
Blends of heavy asphaltenic Canadian crudes and highly aliphatic shale oil condensates can result in severe incompatibilities and impact crude tankage sludge formation, desalter operation, and crude pre-heat fouling. Understanding the intrinsic stability of the individual crudes and the stability of crude blends provides guidance on how to control asphaltene stability in desalters and crude pre-heat fouling control programs. Sludge formation in crude tankage resulting from asphaltene destabilization, when asphaltenic and paraffinic crudes are blended, can be expected.
Sludge formation in crude tankage can reduce the available crude storage capacity and promote underdeposit corrosion. Cleaning out crude tanks can be an expensive, time-consuming process. Crude tanks can be heated and stirred to mitigate sludge formation. Additionally, asphaltenic and paraffinic crude segregation can minimize the potential for asphaltene destabilization. Asphaltene stabilizers, wax crystal modifiers, and wax dispersants can help mitigate the formation of sludge. Monitoring incompatible blends and the wax appearance temperature, as well as thermal and gamma scans of the crude tanks, can enable the refiner to evaluate the risks for sludge buildup and determine if additional mechanical, operational, or chemical options are required.
Tight oils blended with asphaltenic crudes can precipitate asphaltenes; and when thermally stressed, tight oil has formed polar aromatic particles which are unstable in the bulk fluid. Also, high inorganic solids levels have been seen to bind with organic foulants depositing on heat transfer surfaces. Consequently, crude pre-heat and furnace fouling is a common problem in processing tight oil. The crude contaminants that cause fouling are frequently not identified in conventional crude assays. Deposition lowers the heat transfer rates; thus, increasing the heater’s tube metal temperature or decreasing the temperature of the crude as it enters the heater. This results in greater energy usage, lower unit throughput, and more frequent heater decoking. Crude pre-heat fouling forces the heater to make up the duty lost from fouling, which can increase fouling risks in the heater by increasing the heater duty and tube metal temperatures.
The fouling rate can be reduced through mechanical and operational changes such as increasing heat transfer surface area and velocity, installing new advanced low fouling exchanger designs, improving light ends separation in a pre-flash column, minimizing the use of desalter additives known to promote fouling, and following Best Practices on caustic addition. Other options to reduce the fouling rate include the use of dispersants and other antifoulant additives.
GARY HAWKINS (Emerson Process Management)
Issues with accelerated fouling in heat exchangers due to crude instability are well documented. Emerson Process Management offers a heat exchanger health monitoring solution that calculates the duty on both the hot and cold sides (should be the same, alerts if too much deviation) and the current value of the heat exchanger coefficient. Changes in the heat exchanger coefficient are indicative of fouling. The rate of change of fouling is also calculated, and alerts can be generated to warn of potential crude instability leading to accelerated fouling of the exchangers. Also see Question 62.