Question 37: What programs have you implemented to improve reliability and life of the coke drums including inspection and maintenance?
THEISS (Marathon Petroleum Corporation)
Obviously, with coke drum failures, you see a lot of the cyclic operation – a lot of temperature cooling and temperature heat-up – which leads to additional stresses being put on the coke drums. Two primary coke reliability issues we see are shell bulging; and with that shell bulging, you get some cracking. An example of that situation is shown in the upper left-hand picture. You can see some circumferential weld seam cracking as well. It is another issue that we encounter when it comes to coke drum reliability. Within Marathon, we have also recently experienced these two issues being pronounced with single-side feed entry on the coke drum, thus creating somewhat of a banana effect. We have seen more of this type of phenomenon happening in those systems recently.
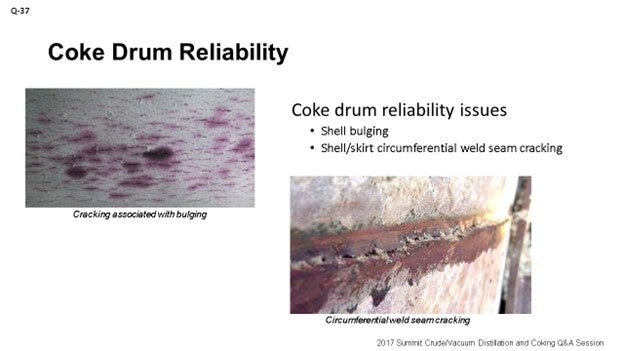
On the next slide is an example of what the coke drum goes through during a cycle. You can just see how the hoop stress and axial stress change as your temperature changes. As you go through the cycle and heat up – I believe that is the red temperature line, you can see how your stresses are impacted during those cycles. So, in an effort to minimize coke drum stress, you want to make sure you are evenly distributing heating and cooling during the cycle; that means, during your back-warming, quenching, and feed introduction. Those are the primary times at which you will be introducing the most stresses, because that is when your temperature will start changing the most. During quenches, we generally have DCS ramp logic that provides even quenching throughout the process. The automation tries to evenly distribute the quench a little better by going through a controlled ramp. Also, during the back-warming cycle, you want to confirm that you have the proper length to back-warm. Typically, this is around 500°F to back-warm, but we will allow it to go to around 400°F on our back-warming process in some applications.
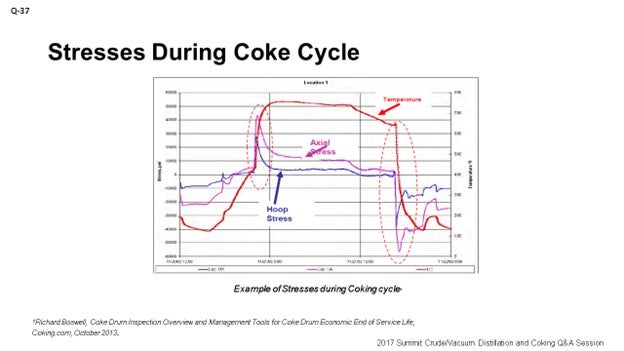
The last piece of the question asked about inspection and identification of cracking or failures. Really, you have to start at the beginning by checking that you have a good, proper base scan. We learned this lesson when we changed inspection companies. The same base scan may not translate to another company’s scanning technology. So, it is important to get a base scan and make sure that you are comfortable using that same technology and the same vendor going forward; because if you do not, the results can vary. You also want to do some continual scanning throughout your turnaround cycle. Your frequency will be dependent upon the severity of your operations. If you have a single-side entry and have seen some effects of drum deflection banana, you may want to increase those scanning frequencies.
There are different techniques: video and visual. There are some techniques that allow you to actually get inside the drum while it is not online but while you are potentially in another, adjacent coke drum. The only issue with video is that it is difficult to see hairline cracks as you are looking at them. During turnaround at Marathon, we then do some acoustic emission testing prior to a shutdown to see if there is any indication that we know we will have to address during our shutdown. If we find any active indications, we will make sure to tackle them during the turnaround.
LÉGARÉ (Andeavor Martinez Refinery)
I want to start by saying that Andeavor is part of an API Task Group that is looking at the issue of coke drum reliability, maintenance, and repair. A technical report – Reference #934-G – is now available to the public. Since we are part of the group, I had an advanced copy. It helped me develop this answer.
Some of the operational changes, as Jeremy touched upon, that can be implemented to help improve reliability in life of your coke drums include cycle time optimization, quench cycle medium, drum preheat temperatures, and feed injection design. We will go over those in a little detail.
Cycle time optimization is a tricky subject, because you will start talking about modifying the cycle time of your coker, which obviously modifies the coker rates and is of interest to the Planning Department. But something to think about is that if you are going to decrease cycle duration from 18 to 12 hours, you will increase the number of cycles by 300 over the course of a year. You will go from 490 thermal cycles to 790 thermal cycles. So, you can see the relationship right there between thermal cycles and length of cycle on the drum itself.
Quench cycle medium: Some folks use water; some folks use steam. Steam will probably be a better choice for long-term reliability. The problem with water is that the water can channel and result in cold pockets along the walls of the drum, resulting in some thermal stress there.
Drum preheat temperatures: Jeremy already discussed that topic.
Feed injection design: single-entry versus the dual-entry design. As far as what operational steps that can be done to improve reliability, we recommend that you look at preheat and the quench cycle, if the piping is in place. The cycle time is a more delicate subject, because then you are getting the Planning Group involved and looking at potentially limiting your coker rates. Feed injection is a big capital project. That will be a turnaround focus if you have a single-entry and want to consider a dual-entry design.
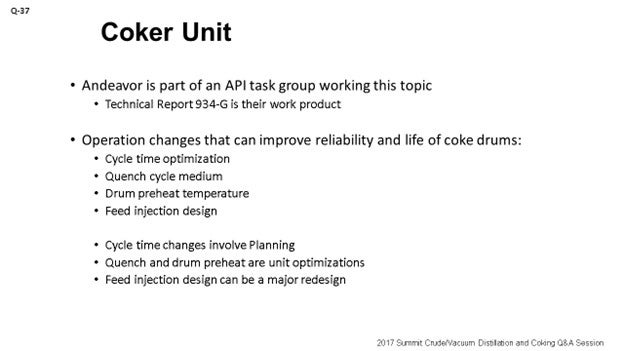
Similar to what Jeremy just mentioned, getting a good baseline scan or laser scan on new drums becomes the future comparison point. The technical reports say that after four to six years, you can do your first inspection. Really, our practice is just to go after that first inspection within the first few years; and then, based on the history of that initial inspection finding, establish the frequency for future inspections. We perform annual inspections on our drums. As Jeremy mentioned about inspection techniques, you have visual and magnetic particle testing, dye penetrant testing, and ultrasonic testing.
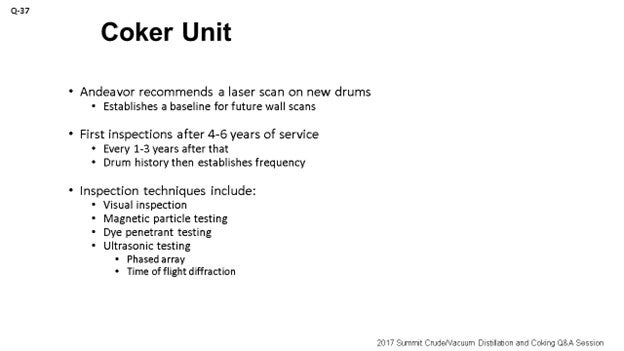
Lastly, a little about repairs: I am a chemical engineer; I am not a repair specialist. The standard has talked about controlled deposition welding, or CDW, as being a method that has definitely shown benefits, as far as repairs are concerned. It gets you out of the post-weld heat-treats that is common to many repairs. So, there is a big benefit there, if you are talking about a coke drum repair. Inconel consumables are going to work well for about two to four years before you will have revisit those repairs. For weld overlays, using Inco 625 with the CDW technique has proven to be effective in achieving long-term repairs.
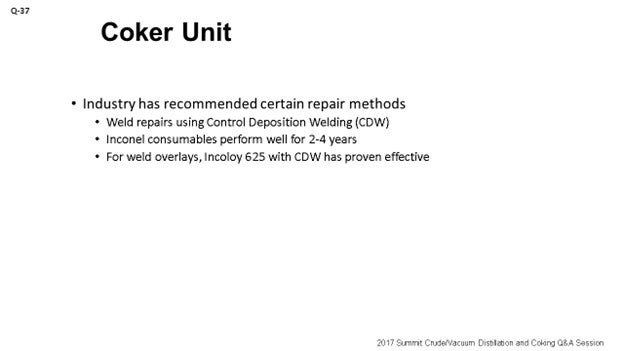
UNIDENTIFIED SPEAKER
Good morning. There is one new proposal that suggests that during the coker step, there are benefits to injecting water by pressure controlling the drum. Is there any experience regarding the extension of the life of coker drums or using that kind of alternative in your quench step? If it is not clear, I can repeat the question.
LÉGARÉ (Andeavor Martinez Refinery)
It is clear. We just do not have any experience with it.
THEISS (Marathon Petroleum Corporation)
I do not either.
TARIQ MALIK (CITGO Petroleum Corporation)
If you are doing pressure quenching, cooling the coke drum under pressure, and holding a back-pressure on the drum, you will get uniform cooling. You will avoid channeling if you do it after first depressurizing and then cooling with water. There are definitely advantages doing pressure quenching. You can hold back-pressure, depending on your system, whether you have fuel gas or a closed loop flare recovery or whatever back-pressure you can maintain. Or if you are going back to the fractionator, you can hold a higher pressure initially and then drop down to the flare recovery header pressure. So, it all depends on what system you have in place. Not everyone can do pressure quenching. Some can, and some cannot if the infrastructure is not in place.
ALBERT MEZA (KP Engineering, LP)
I want to share a little information here with regard to coke drum reliability. I spent 10 years designing coke drums and their mechanical design integrity, so I have learned that coke drum reliability and the need for inspection after the coke drum has been in service are heavily dependent on the mechanical design features. So, programs for inspection of coke drums need to start at the beginning of the design phase of the coke drum.
I want to mention a few design features. We all know about the uniform wall thickness and chemistry restrictions in the materials and special forging. And obviously, we mentioned that the feed systems also help in that reliability of coke drums. So, it is my experience, simply, that the more mechanical design features are implemented in new coke drums, the more reliable the coke drum will be and consequently, the less frequent the need for inspections. Thank you.
JEREMY THEISS (Marathon Petroleum Corporation)
The refining industry is continuously experiencing coke drum problems and failures due to low cycle fatigue. The two main problems caused by the cyclical operation of coke drums are shell bulging and shell/skirt circumferential weld-seam cracking. Shell bulging is typically identified and monitored by laser scanning the coke drums. Coke drum bulging and cracking has become more pronounced with the installation of the bottom un-heading device with single side feed entry.
Minimizing Coke Drum Stress
Flow channels through the coke bed are formed during the coking cycle. It is important to keep these channels open throughout the coking and quenching cycle to provide even heating and cooling of the coke drum. Higher operating temperature during the coking cycle improves coke bed porosity, which improves water distribution during the quench.
After a drum switch, the duration and amount of steam used during the steam stripping step is important to keep the channels open for water quenching. All MPC cokers target at least an hour of steam stripping prior to water-quenching. After steam stripping, water-quench should start at a low rate until the cone section is covered with water. Use of a logic-based controlled ramp will provide a consistent quench. We recommend analyzing drum stress using strain gauges to determine the optimum quench ramp rate based on your cycle time target.
Ideally, we would backwarm the coke drum above 500ºF to reduce stress during drum switch. This target is just a guideline as some of our cokers that are limited by cycle time have a minimum skin temperature target of 400ºF before drum switch: the higher the back-warm temperature, the better for drum life. So, there needs to be a balance between drum life and cycle time.
Most of MPC’s coke drums are equipped with coke drum health monitoring system (strain gauge and TIs (temperature indicators). One of our locations has a third-party perform analysis of its strain gauge every three months. This same location has observed strain gauge readings double the amount from when we installed single side entry. We also recommend using a strain gauge when optimizing quench and backwarm to understand the impact to drum life. We are evaluating the value of installing a center feed device to provide a more uniform feed and quench distribution in the drum to reduce stress.
Inspection and Identifying Bulging and Cracking
All of our cokers installed since 2000 have baseline laser scans. One of our site’s plans includes performing laser and video/visual inspections every three years until critical bulging or cracking is identified, while another site performs a laser scan one to two years prior to turnaround and Acoustic Emissions Testing (AET) six months prior to turnaround. The laser scan is used to complete Bulging Stress Concentration Factor (BSCF) analysis. If significant bulging or cracking is identified, the plan calls for laser and video/visual inspections annually.
Some disadvantages of video inspection are the inability to identify subsurface cracks and the difficulty of discovering hairline surface cracks. Secondary methods such as AET, ultrasonic testing (UT) shear wave, Alternating Current Field Measurement (ACFM), and phased array are used to determine weld seam cracking.
Our inspection plan is to perform an online AET inspection to identify any active indications one year before the scheduled unit turnaround. All active indications will be further characterized with the appropriate secondary nondestructive evaluation (i.e., UT shear wave, ACFM, phased array, etc.). One of our refineries performs UT shear wave inspection on the coke drums’ skirt-to-shell weld seam every turnaround cycle.
ERIC LÉGARÉ (Andeavor Martinez Refinery)
Andeavor is part of an API Task Group that has developed a technical report on coke drums and peripheral components in delayed coking unit. The reference is API Technical Report 934-G.
Operational decisions that can impact coke drum reliability include:
-
Cycle time where minimizing cycle time increases the thermal cycles of the drum and its component over any defined period of time. For example, decreasing cycle from 18 hours to 12 hours increases the number of thermal cycles from 490 to 790 on an annual basis.
-
Quench cycle where steam injection can help lower the thermal stresses on the coke drum as compared to direct water injection. Water can flow unequally, resulting in larger thermal gradients along the shell of the coke drum.
-
Feed injection using a dual-feed nozzle system versus a single-feed nozzle will result in lower thermal stress over the life of the drum.
-
Drum preheat temperatures which are close to the temperature in the feed will also help lower the thermal stresses experienced by the drums.
Having your process engineers work with your Inspection Department will help optimize coker operations to improve the overall reliability of the coke drums. Changes to quench rates and drum preheat temperature are easier to implement using existing controls and piping, in most cases. Changes to cycle times will involve conversations with your Planning Department if your site is coker-limited. Feed injection system modifications will require a turnaround and may be coordinated with a future coke drum replacement.
It is recommended that refiners perform a laser scan of the new drum(s) to establish a baseline for the drum walls. In general, new drums do not require an initial inspection until after the first four to six years of service. After an initial inspection, subsequent inspections will need to be planned based on the level of cracking and bulging that has been observed during the initial inspection. Each drum in a coking unit may need to have a different inspection plan as experience shows that each drum can display a unique damage pattern over time. For example, some drums have experienced through-wall cracking in the drum to skirt weld in less than four years. External inspection frequency is not to exceed three years; however, the recommendation is to inspect annually once the drum has been in service for more than four years.
Techniques used for the inspection of the coke drums are:
-
Visual inspection,
-
Magnetic particle testing,
-
Dye penetrant testing, and
-
Ultrasonic testing, including phased-array and time-of-flight diffraction.
Maintenance Repairs
In general, industry has determined some methods of repair have improved the reliability of the coke drums. They include:
-
Weld repairs using control deposition welding (CDW) with low carbon content consumable matching the base metal have been used in order to lower the hardness of the weld deposits by tempering the subsequent weld passes. This methodology has been used with fewer cracks developing afterwards.
-
The use of Inconel consumables is another option; however, it is normally considered as a temporary repair as these weld repairs tend to crack again in a period of two to four years.
-
For weld overlays, when bulging is a concern for mechanical integrity, Incoloy 625 utilizing a CDW procedure has been used extending the life of the repair by up to three times.
The audit process that Andeavor has implemented prior to any repair job provides a high level of reliability of all weld repairs to be performed on our coke drums. The audit process covers weld repair procedures, QA/QC programs, welding procedures, and an emphasis on NDE criteria for acceptance and rejection.