Question 11: What changes have refiners made in metallurgy from design specifications? What recommendations have the licensors incorporated into new specifications based on experience and user feedback? Comment on both HF and sulfuric acid alkylation.
STREIT (KBC Advanced Technologies, Inc.)
The short answer is that there are not very many deviations from the design metallurgy in HF units. Any changes that have been made are based on observed corrosion rates within the unit. In some cases, valve bodies and trim have been upgraded based on the experience in the unit.
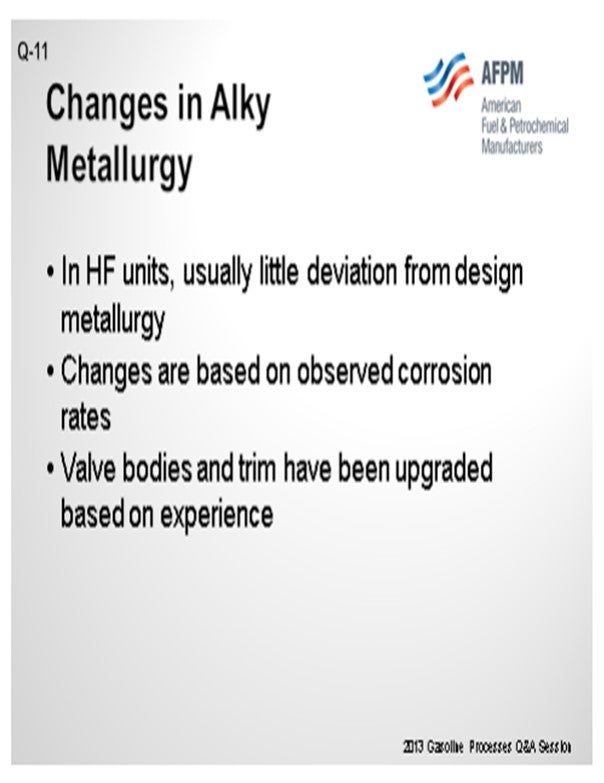
ADAMS (HollyFrontier Corporation)
We have followed API 751, the specification of lower residual element steel in either acid services or trace acid services developed, depending on temperature and on the potential for water to condense out and attack the steel. The trace elements are really copper, nickel, and chrome, and usually the rule of thumb is that the combination of those three needs to be less than two-tenths of a percent in the steel. This is a cross-section of a fractionator feed line that was shown in a 1993 NACE (National Association of Corrosion Engineers) study. On the right, you can see the higher residual element steel; and on the left, the low residual element steel and the difference in the corrosion rates there.
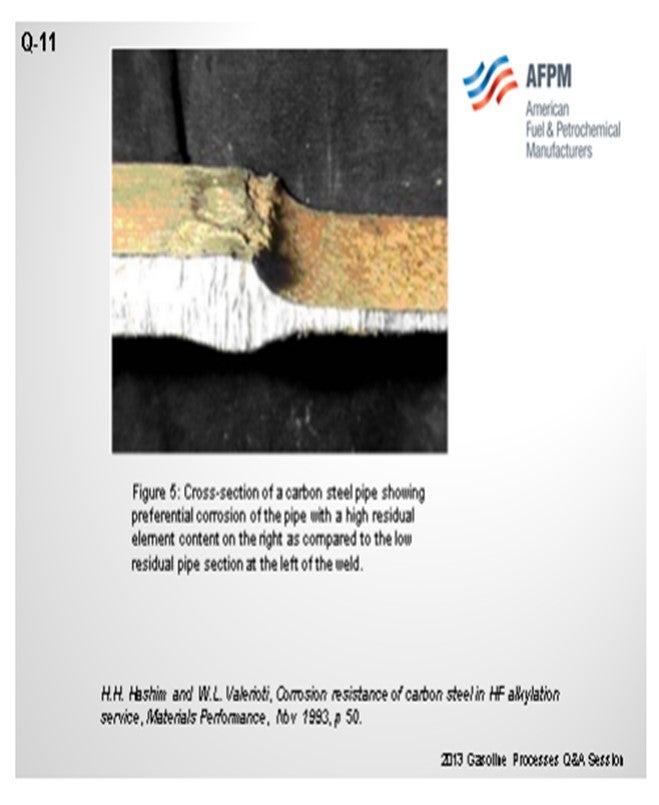
BULLEN (UOP LLC, A Honeywell Company)
Regarding the earlier question related to the isostripper feed pre-heaters, some refiners have upgraded them to Monel™ and 70/30 Cu-Ni, but we still specify carbon steel for new units. Some refiners have upgraded the isostripper main fractionator depropanizer overhead systems with cladding of Monel™ and have used Monel™ pipe in the overhead lines and Monel™ tubes in the overhead condensers to address corrosion issues. Again, we still recommend using carbon steel in these services.
However, where we have changed is in using Monel™ piping in PSV (pressure safety valve) lines where the PSV is coming from a hot service. These services are the bottom of the isostripper main fractionator, the bottom of the depropanizer, and the alumina treater PSV inlet lines because we are seeing corrosion in those areas. Upgrading the metallurgy is the best way to address that issue. On the rerun column and regenerator bottoms line to the neutralizer, you can have relatively high corrosion rates. Some refiners also have upgraded this to Monel™, and UOP has also incorporated this into the original design.
MARK ADAMS (HollyFrontier Corporation)
The biggest issue for HollyFrontier in HF alkylation (and the industry) is accelerated corrosion of carbon steel with low residual elements (RE). Piping and components made from recycled steel contain these elements (%Cu + %Ni + %Cr), and corrosion rates can increase tenfold versus “virgin” carbon steel.
It has been shown in the literature that if the sum of the residuals [Cr, Ni and Cu (chrome, nickel, and copper)] exceeds 0.20%, the carbon steel components used in HF alkylation processes will likely experience a preferentially accelerated corrosion rate. In general, a level between 0.15% and 0.20% of the sum of the three key residuals is deemed optimal, depending on the component, its use, and its location in the unit.
We now specify low RE carbon steel material in all of our HF plants. This is a change from original specification.
PATRICK BULLEN (UOP LLC, A Honeywell Company)
As described in UOP’s response to Question 8, some HF alkylation process units have changed the isostripper feed pre-heater tubes to 70/30 Cu-Ni or Monel™. Corrosion of the carbon steel tubes in these exchangers can be avoided by proper design and operation, so carbon steel is still typically the recommended tube material in a new unit design.
In the isostripper, main fractionator, or depropanizer, some HF alky units have installed Monel™ cladding in the top part of the tower, Monel™ pipe on the overhead line, and Monel™ tubes in the overhead condenser. Corrosion in these areas is normally caused by operation at excessive hydrocarbon flow rate through the settler or by excessive water content in the acid. Carbon steel remains the recommended material of construction in these areas of a new unit design.
Some refiners have installed Monel™ piping on the PSV inlet lines on the bottom of the isostripper, main fractionator, and depropanizer columns and on the alumina treater PSV inlet lines due to corrosion that has been experienced in these hot, high-point dead ends. Based on this industry experience, UOP current design practice is to specify Monel™ for these hot, high-point dead end PSV inlet lines.
Industry experience has shown that the corrosion rate of carbon steel piping on the rerun or regenerator bottoms line upstream of the neutralizer can be relatively high. Many refiners have replaced this line with Monel™. UOP has also incorporated this change into our design.
ERIC STREIT (KBC Advanced Technologies, Inc.)
In most instances for HF alkylation units, there is little deviation from the metallurgical specification. The only changes are based upon observed corrosion rates that may suggest upgrading or cladding to mitigate further losses. In some cases, valve types and trim have been upgraded through service experience.
Most refiners maintain close review of operations and process data such as moisture, acid strength, and polymer content and the source and cause of values out of the boundaries of acceptable operation. Identifying the source issues, like high water content in feed or diolefins, provides the basis to address root cause issues.
JOHN WODARCYK (Phillips 66)
HF Process:
• Low RE (residual element) carbon steel meeting the requirements of Cu + Ni < 0.15 with C >0.18.
• PWHT (post-weld heat treatment) for alloy 400 welds at temperature of 1300 ± 25°F.
• PWHT for all carbon steel components installed in HF service. Licensor recommends using CE for all new equipment and piping. Several companies are using PWHT for hardness and corrosion control.
Sulfuric Acid Process:
• Use of A990 valves for sulfuric acid service may be a challenge to get them specified as A990 if large quantities are not ordered.
• There has been some discussion at NACE that the castings used should be sand castings rather than investment castings. It has been reported that a significant number of the investment cast components cannot meet the A990 requirements. Some have suggested specifically requiring not using investment castings if ordering alloy 20 components.
• A new ASTM A477 CN2MCU J80020 was approved by ASME, so be on the lookout for this material. It has less chemistry control than A990.
• When small quantities are needed, several companies have reported purchasing standard ASTM A743 by putting requirements similar to those required by A990 on that material.