Question 98: What is your experience with the use of ammonia or steam in the FCC flue gas line in order to improve the operation of the ESP? Please comment on system configuration and operational issues
PIMENTEL (CITGO Petroleum Corporation)
We have extensive experience with the use of ammonia in the FCC flue gas line in order to improve the conductivity of the particles and improve the operation of the ESP. We inject ammonia at the target level of 10 parts per million or less. It is very effective at that concentration and has helped us reduce our baseline opacity level from about 15% to less than 10% or 5%. It also reduced the peaks. The peaks that you see in the chart are related to soot blower operations of the waste heat boiler. Thanks to the ammonia, we now operate the soot blowers more often without the fear of violating the opacity limit. So it is also an energy-saving project.
In our unit, the ammonia is injected directly downstream of the waste heat boiler from cylinders or from a storage tank located outside of the FCC battery limits. The only issue I can recall with this operation has been the loss of ammonia flow due to the regulators plugging with ice. If the ammonia is not completely dry, it will freeze in your regulator. That is easy to fix by putting some steam tracing in the lines. The chart shows typical performance before and after starting the injection of ammonia. As you can see in the chart, it helps us operate the soot blowers more often.
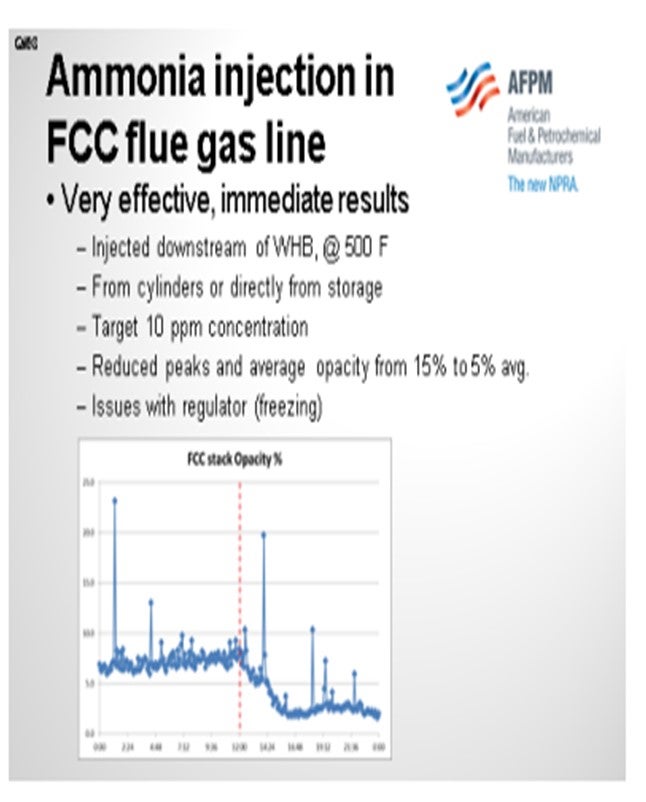
BROOKS (BP Refining)
As Sergio mentioned, the common use for putting in steam and ammonia is to reduce the resistivity of the particulate so it can be picked up easier in the ESP. We do not have a lot of experience with steam helping our ESP operations, apart from the example I mentioned about using steam on start-up before meeting temperatures necessary to use ammonia.
We do have quite a bit of experience with ammonia injection. All of our ammonia injection systems are fairly similar because, again, we use the same consultant for the vast majority of our ESPs. We also found that it is key to focus on your ammonia injection system providing good dispersion in the flue gas stack and good vaporization of your ammonia. Typically, all of our systems include heaters for vaporization and metering injection pumps, so we know how much ammonia we are injecting. The systems also include good dispersion nozzles for the flue gas stacks.
When we use ammonia in our unit, we typically try to optimize it. As shown in the example of an ammonia step test in the slide, the blue and orange lines are essentially the same. They both tell you how much ammonia we are injecting. However, we tend to double-check the meter on the pump stroke versus the actual amount coming in just to make sure we are getting good readings.
You can see that the test includes our stepping up injection rates until we meet a level where we feel like the opacity – the green line – has leveled out. You keep stepping up your ammonia until you believe you have leveled that on opacity, and then you step back down until you feel like your opacity has gone back up. Those are the areas where you would target your ammonia injection rates because you know that is the minimum necessary to maintain your opacity.
I also want to add that I am not sure if other sites have seen instances similar to what we have noticed. Some, but not all, of our sites with ammonia injection into their ESPs also saw a reduction in NOx as a result. It makes sense because you use ammonia in a SNCR (selective non-catalytic reduction) and also in a SCR (selective catalytic reduction) to reduce NOx. However, we do not see it in all of our units.
Those units with high NOx tended to show a good step down and leveling out similar to what we saw with the opacity, which can be seen in the purple line representing NOx. So, you may get an added NOx reduction benefit if you use ammonia on some of your units. We also did the same step test on other units and saw no response to NOx; so, it is not a guarantee.
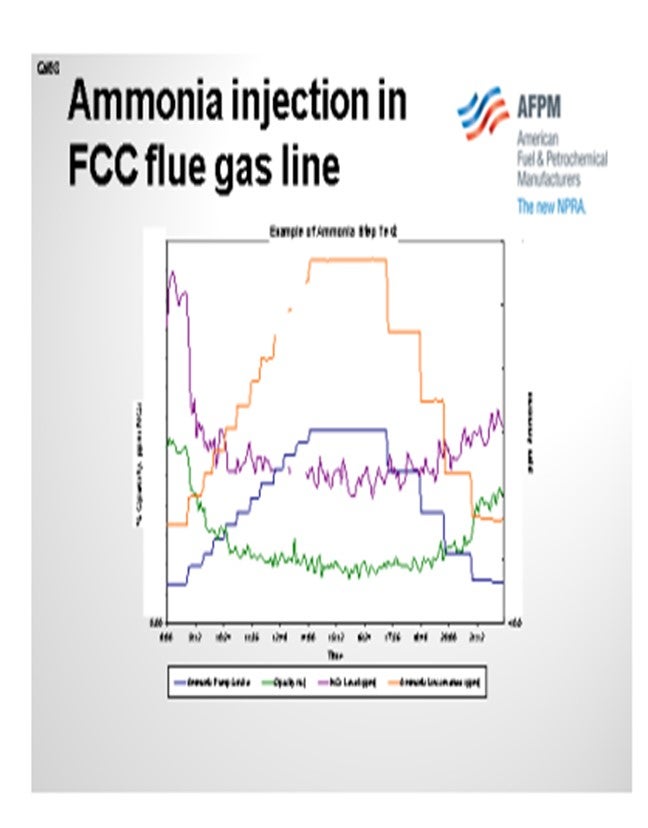
SCHOEPE (Phillips 66)
I do not have much to add. Halle highlighted all of the points. Phillips 66 has a few installations where we inject ammonia into the ESP. Collection efficiencies were increased by 25% to 50%. It is critical to have good ammonia injection quilts which inject ammonia across the entire duct. Typically, we have not seen any issues with ammonium salt deposition anywhere in the downstream equipment.
MARTIN EVANS (Johnson Matthey Intercat)
To give a contrary comment, I heard a few people talk about the importance of dispersion. We recently had one refiner start ammonia injection and have trouble with the quill. When the quill was removed and the ammonia was injected straight into the nozzle, he got a similar reduction in opacity as he had been getting with the quill. So go figure. It is always the same with the FCC. You can prove something on one unit and then prove the exact opposite in another unit. Another point I want to make is that we have seen that opacity can increase when refiners go to low SOx emissions, typically below 50 ppm and certainly below 20 ppm. This occurs, if you are not using ammonia, because the SO2 (sulfur dioxide) actually acts in the same way as does the ammonia to decrease the resistivity of the catalyst and improve the efficiency of the ESPs. So, when you take out the SO2, you have to replace it with ammonia. Otherwise, you will lose ESP efficiency when you get down to very low SOx levels.
PIMENTEL (CITGO Petroleum Corporation)
We have extensive experience using ammonia in the FCC flue gas line to improve the performance of the ESP. NH3 is a very effective way to improve the conductivity of the flue gas at the levels as low as 10 ppm. In our experience the use of ammonia helped to reduce the flue gas opacity from an average of 15% to less than 5%. Ammonia is injected directly in the flue gas line downstream of the waste heat boiler (at about 500°F) from cylinders or directly from an ammonia storage tank located outside of the unit battery limits. The only operational issue with this system was plugging the regulators with ice, which was solved by steam tracing upstream of the regulator/orifice plate. We do not have experience injecting steam in the flue gas line to improve the operation of the ESP.
BROOKS (BP Refining)
BP does not have a great deal of experience using steam to improve ESP operations. We have one site that uses steam in the ESP during start-up to improve efficiency before the ESP is hot enough to add NH3 injection. This is to prevent possible salt formation that can result from adding NH3 into a cold ESP. The majority of our units use ammonia (NH3) injection successfully to improve ESP collection efficiencies. The purpose of using steam or NH3 injection upstream of the ESP is to condition the particulates by decreasing their resistivity. Decreasing particulate resistivity makes them easier to attract to the walls of the ESP, thus leading to higher collection efficiencies.
As mentioned above, BP uses an industry consultant with a multitude of ESP experience to help guide our ESP operations and optimization efforts. The majority of our NH3 injection systems are similar and follow the consultant’s guidelines, which typically include heaters for vaporization and metering injection pumps. Some sites have basic injection nozzles in the ducts while others have full injection grids. The key considerations for this injection system are around ensuring the injection point provides good dispersion in the flue gas duct and that they NH3 is sufficiently vaporized. Un-vaporized NH3 injection can cause issues with particles remaining on the collecting plates and falling off in chunks or hopper pluggage caused by sticky fines which leads to difficulty evacuating hoppers.
BP has also done a series of NH3 step-tests to optimize NH3 injection. These tests are simple adjustments to NH3 flow rates that are compared to improvements in stack opacity for each step as can be seen in the example graph below. During these tests we have seen that the reduction in opacity with increasing amounts of NH3 injection lines typically lines out at some point, as can be seen in the graph below.
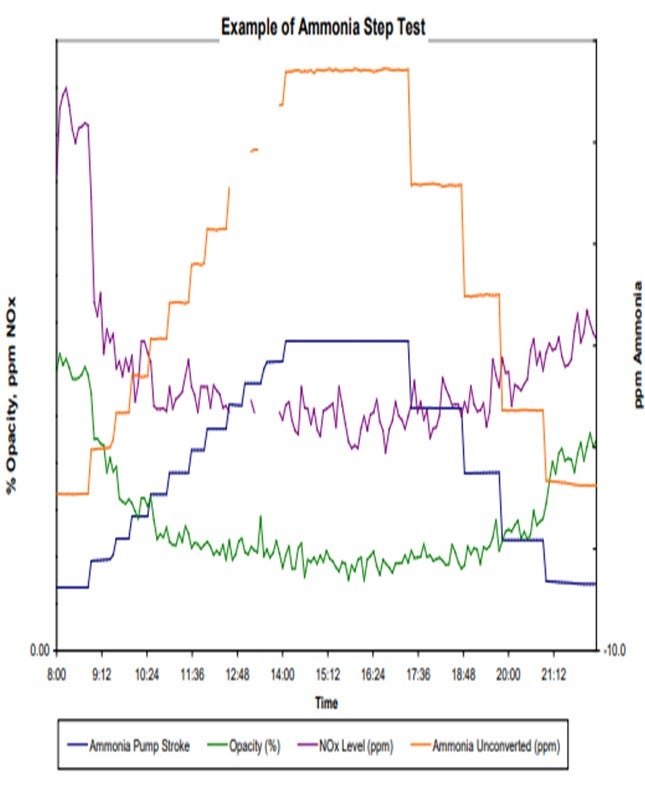
Our experience with NH3 injection has generally been very good at sites with good injection systems. In addition to improvements in opacity with NH3 injections, BP has also seen some reduction in NOx at some of our sites. Generally, we have seen sites with higher base NOx levels see reductions in NOx with NH3 injections and others with lower base NOx levels may not see any change in NOx emissions with NH3 injection.
SCHOEPE (Phillips 66)
Ammonia has been used effectively in a number of refineries to increase electrostatic precipitator (ESP) collection efficiency. Ammonia decreases the resistivity of the catalyst which makes it easier for a catalyst particle to accept a charge. Depending on the ESP design aqueous ammonia injection can increased the ESP collection efficiency by 25% to 50%. A successful installation requires good distribution of the aqueous ammonia. Injection quilts need to be designed to distribute the ammonia equally across the area of the flue gas duct upstream of the ESP and resist catalyst erosion. Deposition of ammonium salts is typically not an issue.