Question 97: What operational or design changes can be employed to address heat balance issues – e.g., catalyst circulation limits, low regenerator temperatures –associated with processing tight oil-derived feeds?
LARSON (KBC Advanced Technologies, Inc.)
This answer will be very similar to what was already discussed about how to treat the resids. The example shown on the slide is a Maya blend, a typical tight oil, and then a tight oil with resid. Again, we are seeing significant reductions in sulfur and Conradson carbon metals and also a much higher hydrogen content. So just by comparison, let us look at this at constant reactor temperature. What we would expect to see is low coke, which will raise our cat oil and pull a lot more heat out of the regenerator. We will get much more liquid yield, which is what is reported by those who are running more and more tight oil in the system.
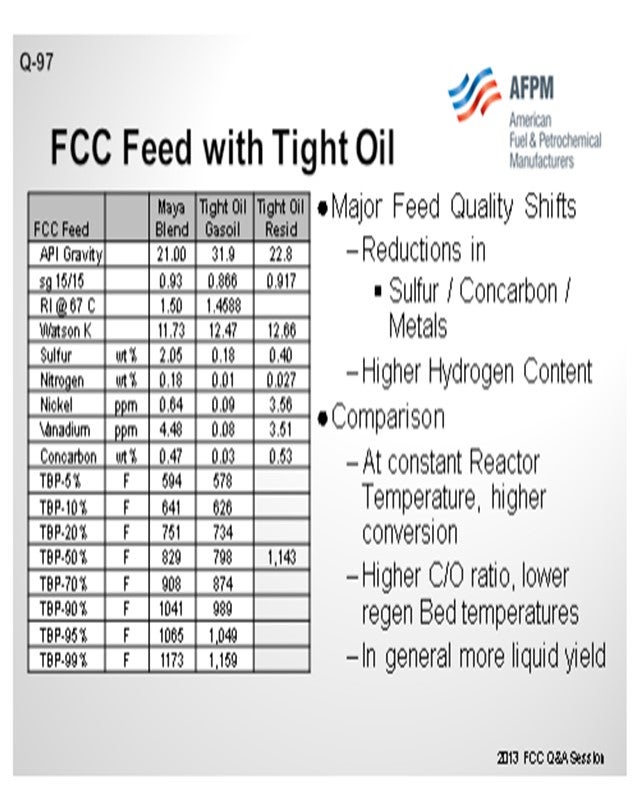
The question is: What can we do to operate these units? You are going to have some open capacity. So operationally, what can you do to hydraulically increase the feed to the unit? Given our economics is more feed, more feed, more feed, how far can we push the “more feed”? On the heat balance side, consider first getting all of the diesel out of the feed so you do not have an additional cooling effect with material going through that will not crack very well. Look at processes like deep cutting your VGO. How far are you going into the material? Are you going to 1000°F to 1050°F? Can you go to 1075°F? There are some people who have shut down the vacuum columns and are actually just running pure catalyst from the tight oil into the unit. And, we have already had a question on processing whole crude.
So, there are actions to consider. Again, look at catalyst change. We have been taking recycle out of the riser for years. We might put it back in now as a way to manage the coke balance. You should consider these questions: 1) What is your standpipe flux? and 2) What is the maximum catalyst flux rate that you can tolerate in your standpipe? You will not get to choke flow. You will get to a point where it will not flow any faster. Look at the slide valve opening. Most units have been designed with a slide valve that will run approximately 50 to 60% open under normal operation. Now with tight oil’s higher circulation rates, you might be looking at a slide valve that wants to operate at a much higher percentage opening. That may be your first point. It is not the pressure drop. It is the feeling of running at 80 or 90% open. Resize the slide valve. It may be a very easy modification to get you where you can run much higher cat to oil rates.
Make sure that you have the right pressure balance. Now that you may not have as much air demand, maybe you can change the pressure balance of the unit to raise coke make in the reactor and improve the ∆P across the system. You will have to be aware of additional catalyst erosion if you go to higher pressure drop on your slide valves. Look at the velocity profile in the regenerator itself. Make sure that you can push the unit or that the unit is down to where you can operate in a comfortable range. Again, I look at this as a perspective of something that occurs today and is not happening tomorrow, so what should we do? We might back some steam off the feed nozzles to make a little more additive coke. Perhaps we will lower the stripping steam again to manage it with more coke in the extreme conditions; and I do say ‘extreme.’ Adding torch oil to the regenerator would be an extreme if you are just trying to keep the unit on. We do not recommend that because it substantially chews up the catalyst. Keeping the unit on would be a last resort.
We have heard of people wanting to start the air heater in the bottom of the regenerator to add enough heat to the system. That would be a control issue. There are a lot of issues around the air heater with temperature profiles and the reliability of the air grid that the metallurgy would have to be checked out for a continuous long-term operation. But fundamentally, check your catalyst type. What are you using? What can you change in the catalyst system? What can you do to adjust your feed quality? You add carbon to the system. In the U.S., it has to be moving to a higher and higher percentage of tight oils because we are finding it; and by law, we have to process it. So this would be a new challenge. I think the catalyst manufacturers have done a great job, and they will continue to find ways to give us a catalyst that makes a little more coke and gives us the yields we want.
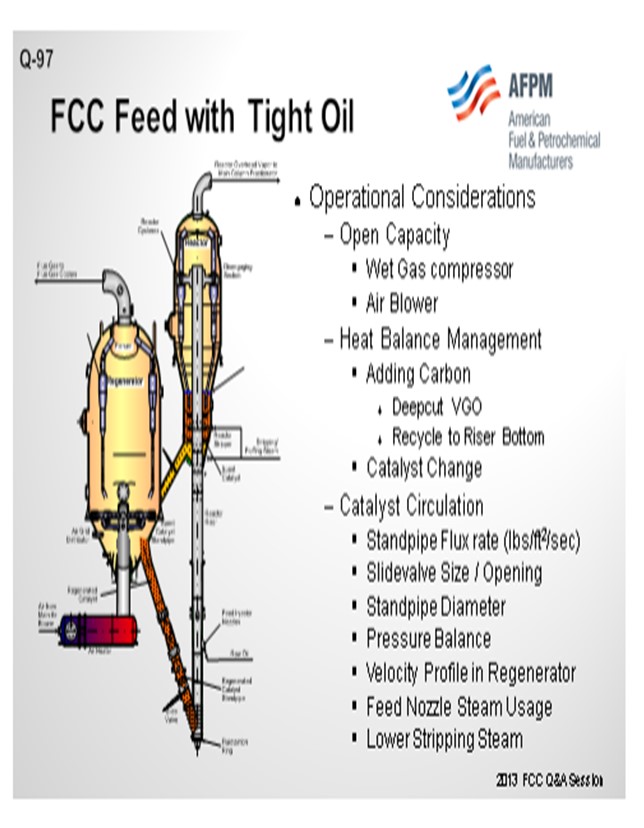
GIM (Technip Stone & Webster)
Many of the available crude oil analyses of the tight oil show that the coke precursors in both the gas oil and the resid portions are very low. Those FCCs that were designed for heavy sour crudes may have some detrimental heat balance issues on the converter side, as well as light ends constraints on the gas plant side. I am going to discuss what you can do in terms of both operational and hardware changes. I will not repeat the redundant points that Mel Larson described previously.
First is riser outlet temperature. The obvious solution is to raise the riser outlet temperature not only to heat up the system but also to gain back some of the octane loss resulting from processing paraffinic feeds. This may be problematic because your gas plant will probably already be overloaded with the lighter ends stemming from the processing of tight oil.
Using higher feed preheat, if you have room, will certainly alleviate the higher catalyst circulation rates expected from the low delta coke feeds, such as tight oil.
Step jumps in the conversion level from the improved feed qualities need to be counterbalanced. Raising the reactor vessel pressure will certainly help in terms of increasing the unit delta coke directionally. That would add to the delta coke because of the higher hydrocarbon partial pressure. It will also help alleviate the light ends circuit in the gas plant. Reduction in dispersion steam and the addition of torch oil were already discussed by Mel.
Hardware Changes: I know it is a big-ticket item, but certainly the fired feed preheater could be an option. Again, that is with the installed TIC cost and permitting issues. We spent a great deal of our resources on conducting pilot plant testing of recycle streams in terms of both HCO (Heavy Cycle Oil) and slurry. Being derived from very paraffinic feeds, these high-quality feeds do not have much HCO and slurry yields to begin with. The amount of recycle stream that is available to recycle back to the riser is not there. So that is the problem one.
Second is the coke precursor for these HCO and slurry streams. Even if you are able to recycle them, you will not get as much coke out of these recycle streams as you would have in your conventional FCC feed.
Problem number three: We found that the actual conversion level for these streams – converting it into something other than the cycle oils, dry gas, LPG, gasoline, or coke – was also low. It was quite nonreactive in that sense and is another issue of recycling these streams.
Enlargement of catalyst standpipes and port openings of slide valves may be necessary for catalyst circulation step-jumps, even after making all other operational and hardware changes.
Continuous usage of air heater may also be evaluated, but this may require redesigning the air distribution system to ensure that the increase in the exit tip velocities will not result in unsustainable catalyst attrition.
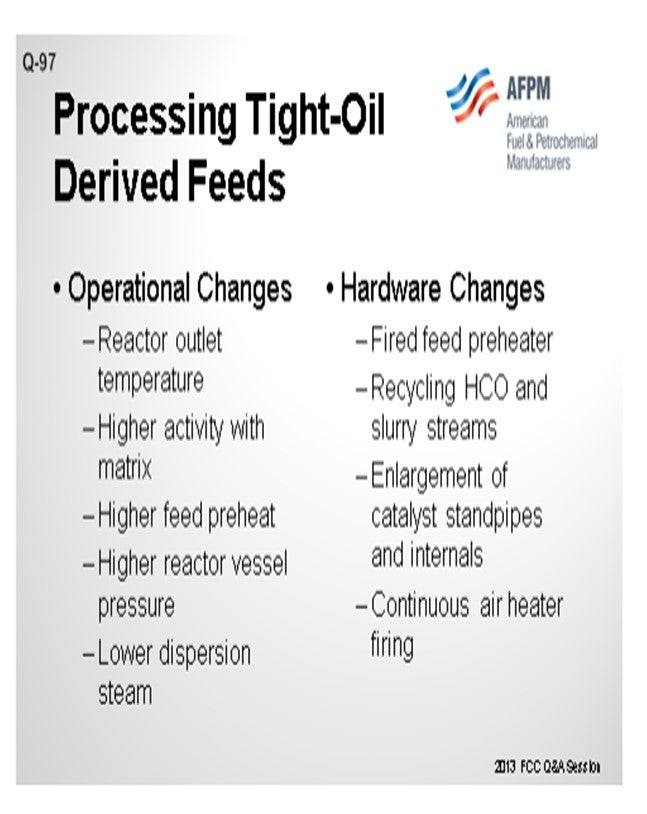
PAUL DIDDAMS (Johnson Matthey INTERCAT, Inc.)
One additional suggestion might be to consider oxygen enrichment and reducing your air rate to decrease the heat losses a little bit. Of course, you might also consider running a residue stream in directly with your feed.
KEN BRUNO (Albemarle Corporation)
The panel did an excellent job reviewing the operational and hardware changes. I want to point out that to help manage these changes, it is critical to use the right catalyst. To that end, Albemarle has developed a tight oil family of catalysts, in particular Upgrader T and Amber T. Again, please consult the Answer Book response for more information on the application of these products, as well as all of the commercial experience we have with those products.
LARSON (KBC Advanced Technologies, Inc.)
I want to highlight the need for you to have a good baseline of where you are currently operating. Jeff talked about unit monitoring earlier. When you know that you will be processing a higher percentage of tight oil, to the extent that you can either ratably, put it in or put some material in storage and regularly bring it into the unit. Controllable rates of tight oil will give you the chance to learn what the effects are as opposed to jumping out and saying, “We can handle 50%.” Get yourself a really good baseline in advance; so that when you do make changes, you will have a better educated starting point.
PARAG KANADE (Lummus Technology)
What do you think will be the major challenges in the fractionator and the VRU (vapor recovery unit) section? You mentioned that there will be excess capacity in the compressor and the overhead circuit; but at the same time, the debutanizer stripper bottoms will be loaded. All of these are very heat-integrated with the pumparounds on the reboilers. To utilize the compressor, I think the incentive will be to push more fill through the unit. However, you will also have problems in the stripper debutanizer in the downstream unit. So, my comment is that a small study will be helpful to determine the right throughput to your unit which will avoid the need for a major revamp.
LARSON (KBC Advanced Technologies, Inc.)
The answer is that on a hydraulic basis, you will have to find your pinch point. You would like to be able to analyze it with kinetic modeling and seeing where your pinch points may come up. Also, I appreciate the heat balance comment. I think some of our panelists have actually had experience with this issue. As you process more tight oils, you physically cannot run the riser top temperature; i.e., the heat going to the main column is less because you cannot tolerate 90% plus conversion in the unit. You have a different balance when you run more tight oil than we have been running in the last 20 years. So, there will be different pinch points.
MICHAEL WARDINSKY (Phillips 66)
I cringe every time I hear people talk about using torch oil to maintain regenerator temperature above some minimum for an extended period of time. Make sure you understand the environmental and process safety implications of trying to run long-term on torch oil. In addition, the catalyst will suffer accelerated attrition and activity loss. There are environmental concerns about firing torch oil. Any time you put torch oil in the regenerator, your CO emissions will go up. In some units, I think you will be challenged to stay under a 500-ppm limit. You also have process safety issues that deal with the consequences of the blower tripping. If there is no interlock on your torch oil supply system, you will be injecting a lot of fuel into your regenerator and could have a real problem. So, make sure you understand those consequences before you use torch oil outside of startup.
LARSON (KBC Advanced Technologies, Inc.)
Just as a follow-up, my comment on that was generally not regarding refineries in the U.S. We have people outside the U.S. who are, in fact, using torch oil and who do not have the same EPA and environmental constraints, or even some of the other safety issues you mentioned. I totally agree with what you are saying from our position here in the U.S. The window of operation is much tighter here than it is in other countries.
MEL LARSON (KBC Advanced Technologies, Inc.)
For the last 20 years, the industry has been driven by tighter gasoline and diesel sulfur specifications, as well as increased demands for propylene. The catalyst manufacturers and licensors have done a great job making improvements that focus on maximizing the profit from these operations.
Now with a greater percentage of tight oil in the refinery, what are the changes? The tight oil might be similar to a severely hydrotreated virgin gas oil FCC feed. The typical shift from typical WTI (West Texas Intermediate) to tight oil (not all tight oils are equal) will be as a result of:
• Increased hydrogen content;
• Lower contaminants, such as Conradson carbon, nitrogen, and sulfur; and/or,
• Low aromatic content.
As previously mentioned, the diesel content of the FCC feed should be reduced as much as possible since light boiling feed will reduce regenerator temperature. One point: Diesel quality from the tight oil has greater value as diesel than as FCC feed. Secondly, consider substantially increasing the HVGO/resid cutpoint or checking the quality of the overflash from the vacuum column as a potential feed to the unit.
As feed quality improves, the regenerator bed temperatures reduce, and catalyst circulation rates go up to a “limit”. There are a number of steps recommended to define the real limits in processing tight oils:
1. Define a base line of the circulation rate. This step is crucial for understanding the current or anticipated changes with tight oil. The base line should be consistent with typical or routine operation. Included in this step would be a single-gauge pressure survey to aid in system definition and base line.
2. Identify the limiting issue, i.e., the flux in the standpipe, the residence time in the stripper or regenerator, the slide valve (SV) position(s), or ΔP across the SV. From a flux rate perspective, there are a number of units operating successfully at mass flux rates in the standpipe well over 300 lbs/sec/ft2 (pounds per second per square foot). Historically, FCCs used to operate successfully with lower regenerator bed temperatures in the range of 1200°F to 1250°F and residual carbon on catalyst at levels of as high as 0.30 wt%.
Operational considerations are similar to those discussed previously:
• Consider different feed sources to add carbon, such as vacuum overflash and a Slip-Strip™ of vacuum residua.
• Change the pressure balance.
– Move from partial to total CO combustion in the bed, not just in the regenerator proper. Add (more) promoter to the regenerator.
• Change the catalyst.
• Recycle a cycle oil to add carbon.
• Increase reactor temperature.
• Use air heater continuously.
• Add external heat oil direct into the regenerator.
Hardware changes to consider for accommodating higher catalyst flux rates would include, but not be limited to, the size of the standpipe and slide valve and capacity expansion, given that the air blower is less constrained.
STEVE GIM (Technip Stone & Webster)
Cracking of paraffinic FCC feed derived from tight oil crude behaves similarly to severely hydrotreated feeds or cat feeds from other sweet crudes like West Texas Intermediate. As many of the available crude assays show, these crudes do not have many coke precursors in the gas oil or even in resid fractions. FCCs designed for sour heavy feeds may face heat balance constraints in the converter (reactor/regenerator) and light ends circuit constraints in the gas plant. Sometimes, too much of a good thing can be a bad thing.
Operational Changes
Higher reactor outlet temperature may be necessary not only to heat up the overall system, but also to make up the gasoline octane loss stemming from the paraffinic feed. This may not be easy, however, given the fact that the lighter feed would be already taxing for the light products circuit in the gas plant. Higher catalyst activity accompanied by more matrix content will help increase the catalytic coke.
Talking about catalyst, for partial-burn units, the addition rate of CO promoter can be increased to preferentially raise the regenerator bed temperature.
Higher feed pre-heat (if there is room in the pre-heat train) can help alleviate the expected increase in the catalyst circulation rate and also counterbalance the step jump-in conversion due to improvement in the feedstock qualities and higher operating severity I just described.
Raising the reactor pressure will directionally increase the delta coke due to the higher hydrocarbon partial pressure. It will also help alleviate the increased burden in the lighter ends of the recovery section.
I do not like this idea as much, but lowering feed dispersion can help increase the delta coke. There will be some debits in selectivity.
I also do not like the idea of injecting torch oil into regenerator, but that is always an option.
There is a possibility of a compatibility issue of highly paraffinic tight oil and asphaltenes. It could form two phases and may have to be injected separately into the riser.
Hardware Changes
A big-ticket item, in terms of cost and permitting issue, is to install a fire feed pre-heater to counteract the lower system-wide Btu (British thermal unit) posed by the lighter fresh feed.
Recycling HCO and slurry streams (preferably upper section, otherwise they will be entrained to regenerator) into stripper may also be an option. We have done some pilot tests of these recycles from light feeds. There are a few not-so-obvious issues. Issue 1: Quantities of these recycle streams are lower than those from heavy feeds since conversion levels are expected to be higher. Issue 2: Coke precursor level is low for even for these bottoms. Issue 3: Conversion level (i.e., converting into something other than the cycle oils such dry gas, LPG, or gasoline) is low. Depending on the starting point of delta coke for the operation without the recycles, only recycling the heaviest cut may be a delta coke additive.
Enlargement of catalyst standpipes and port openings of slide valves may be necessary if catalyst circulation step-jumps even after making all other operational and hardware changes.
Continuous usage of air heater may also be evaluated, but this may require redesigning the air distribution system to ensure that the increase in the exit tip velocities will not result in unsustainable catalyst attrition.
RAUL ARRIAGA and KEN BRUNO (Albemarle Corporation)
Tight oil (TO)-derived feeds, in general, show high API gravity and a high amount of paraffins compared to traditional VGOs being processed in FCCUs. On the other hand, TOs tend to come with higher amounts of some metals, particularly iron and calcium. This combination of properties makes TOs more crackable than traditional VGOs due to their molecular distribution, but it also results in a lower contribution towards delta coke, lower regenerator temperature, and increased catalyst circulation provided the iron and calcium are low. On the other hand, if the metals (usually iron and/or calcium) are high, TOs are conducive to increased deactivation rates, especially pore mouth blocking, which tends to increase catalyst mass transfer limitations and FCCU slurry yields. The increased slurry production can push a refiner to reduce feed rate in order to stay within limits, resulting in economic losses. To overcome mass transfer limitations and optimize delta coke, high accessibility catalysts such as AMBER™ and UPGRADER™ have been developed and proven successful for tight oil applications.
Based on the above, operational changes that can be employed to address heat balance issues include increasing activity via higher catalyst addition rates and HCO or slurry recycling. Another option is the processing of bi-modal types of feed; meaning that as a refiner increases the amount of TOs in the feed, the refiner could compensate for the TOs by lowering the API gravity of the rest of the material in the blend. However, care needs to be taken regarding the compatibility of the different components or asphaltene precipitation may occur.
It is not recommended to reduce stripping residence time as valuable product is burned in the regenerator. It is also not recommended to use torch oil to increase regenerator bed temperature due to the possibility of drastically higher catalyst deactivation rates and lower e-cat activity, which would create a negative contribution to delta coke and likely result in increased catalyst addition.