Question 97: What equipment do you employ to help eliminate ESP hopper and downcomer plugging with catalyst fines? What additional operating practices are used? What type of level detectors are in use on the ESP hoppers and/or catalyst storage silos? Are there any new level detection technologies that could be applied, perhaps from coke drum measurement detectors?
PIMENTEL (CITGO Petroleum Corporation)
Our main problem with the ESP is fines accumulation in both the ESP hoppers and the transfer line from the hoppers to the fine's storage bin. We have incorporated some design improvements that have helped us minimize, but not completely eliminate, the main problems of condensation in the system and plugging. So, we added a second vibrator or rapper on the opposite side of the hopper, and we run them on alternate cycles of one minute each. The second improvement was to increase insulation of the hopper to a point where we now have it completely encapsulated. We have steam tracing as well. We believe there is still room for improvement.
At this time, we know that we can minimize the run of the piping from the hopper to a storage bin. We are also aware that there is a possibility of actually installing the fines storage directly below the ESP to basically eliminate the problem of plugging the transfer line.
Part of the question asked about our experience with level detectors. We do not have any. We mostly use an infrared gun if we suspect a high level in the hopper.
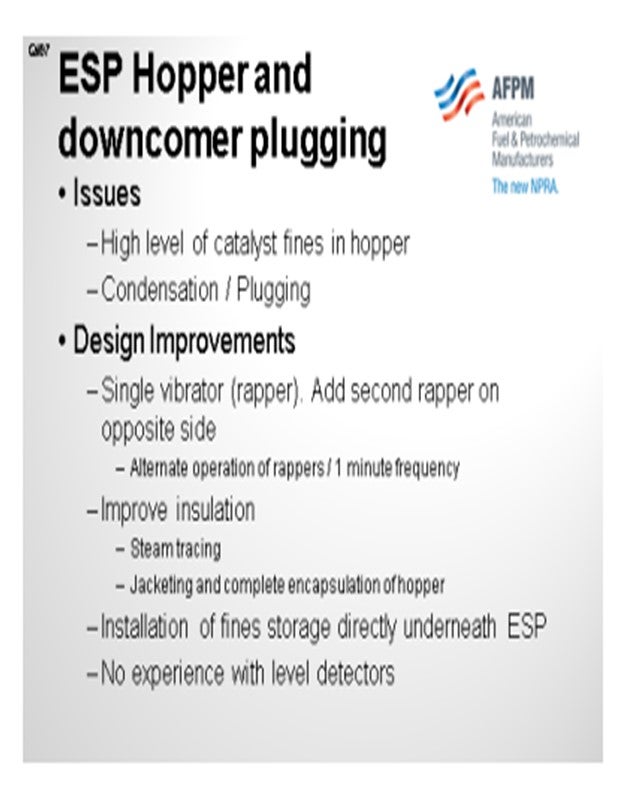
BROOKS (BP Refining)
BP uses an industry consultant to help us guide our operation on most of our ESPs. This industry consultant has a multitude of experience in ESPs over many years. Because of that, we have similar systems on most of our ESPs and in our ESP hopper systems. We have found that when we target keeping our hoppers warm, we help prevent some of the issues from condensation. Almost all of our hoppers that operate well have electric-traced hoppers to prevent condensation and keep the hoppers warm.
We also focus on trying to keep our hoppers as empty as possible since overfilling causes outages of the TRs (transformer rectifiers). Because of this, some of our sites have a system that continuously empties the hoppers. I do not know a great deal about it, but I am aware that they do this to prevent catalyst fines levels from building up in the hoppers. We have other hoppers that gauge their typical fines generation and develop a schedule of manually emptying their hoppers based on the fines make they expect.
From a level gauge perspective, we use nuclear level gauges on the majority of our units. Again, the same ESP consultant recommends this as the best technology for hopper level indication, and that is why we have employed them at the majority of our sites. A lot of our sites that do not employ these are up against limits for radiation sources on their site, so they are unable to use nuclear level gauges on their ESP hoppers. Those sites have resorted to high-level switches and regular manual dumping of their hoppers. However, these switches can be rather unreliable.
We have also seen issues with the nuclear level gauges. We will sometimes have ledges of catalyst that are sitting over the level gauge making it look like you have a level of catalyst. In those cases, we will back-check our TR operation to determine if we actually have a level or if it is a false indication. We will typically make sure to empty our hoppers more frequently if we feel we have a bad reading on the gauge.
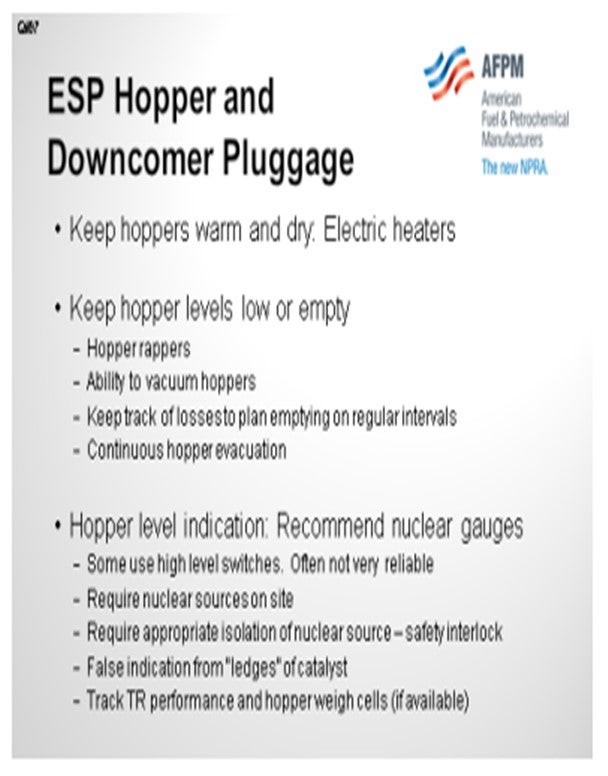
SCHOEPE (Phillips 66)
In our system, ESPs use most of the features that were already mentioned. We make sure that our hoppers are well-insulated and heated and that vibrators are used to keep the hoppers from plugging. Fines are typically dumped on a timed interval, but not so much on level control. However, some of the units do have a gamma ray-type of indicator that can generate a high-level alarm.
PIMENTEL (CITGO Petroleum Corporation)
Our ESP hoppers are equipped with automatic rappers, which create enough vibration to prevent catalyst accumulation. We use a single vibrator on each hopper; hoppers have steam tracing and insulation. We initially had insulation jacketing and then beefed this up with a second layer of insulation that completely encapsulated each hopper. We have also added additional steam tracing on some hoppers. These moves helped to reduce, but not eliminate, the downcomer plugging problem. We think that a second vibrator on each hopper opposite the first hopper would help. We have also increased the vibration frequency in steps so that each hopper vibrator now vibrates once every minute. We have experienced plugging in the transfer line from the hoppers to the catalyst fines storage at times, due to condensation. A good design practice is to minimize the length of the transfer line to the fines storage, or store the fines directly underneath the ESP. We do not have any level detectors in the hoppers (use of I.R. camera when high level is suspected).
BROOKS (BP Refining)
BP uses an industry consultant with a multitude of ESP experience to help guide our ESP operations and optimization efforts. As such, many of our ESPs employ similar systems to manage fines handling. Our hoppers are typically equipped with electric heaters to maintain temperatures. We have found that keeping hoppers warm is one of the biggest keys to prevent pluggage. Warm hoppers prevent liquid condensation from causing fines clumping and sticking to walls. Most ESPs employ hopper rappers and have an ability to vacuum out hoppers if necessary.
Our sites typically work to keep the hoppers as empty as possible to prevent overfilling and outages of the TRs. Some sites have continuously empting hoppers. Others have gauged their typical fines makes and have regularly scheduled times to manually empty hoppers.
The ESP consultant we use recommends nuclear level gauges as a best technology for the hopper levels, thus these are employed at the majority of our sites. These gauges tend to work well; however, the following are key concerns around using nuclear gauges:
• Gauges require nuclear sources onsite. Some of our sites have had to remove these due to restrictions in the amount of nuclear material onsite. These sites have typically resorted to high level switches and regular manual dumping of hoppers. However, these high-level point readings are often not very reliable.
• It is important to note that the nuclear sources need to be appropriately isolated when work is done in the ESP. It is recommended to include this isolation as a safety interlock.
• Some sites have seen “ledges” of catalyst causing false level indication in the hoppers. This phenomenon is not exclusive to the use of nuclear level gauges. Our sites typically handle this by using tracking TR performance and hopper weigh cells if available to determine if hopper levels are actually too high or if the reading is false. If the reading is false, sites will typically resort to manual emptying of hoppers to maintain levels.
As with any type of indication, there can always be issues associated with these level gauges. However, we feel that the nuclear gauges are the best level indication technology available for this service.
SCHOEPE (Phillips 66)
Electrostatic precipitator hoppers are well insulated and use small heaters and vibrators to prevent plugging. Fines are typically dumped on a regular interval, but gamma ray type level indicators are used which can trigger a high-level alarm.