Question 96: What are the typical causes of dipleg plugging/fouling? How can the plugging/fouling be avoided? What is the experience with clearing diplegs online?
KOEBEL (Grace Catalysts Technologies)
]I am going to take the question in a few parts. I will cover the reactor side first. In the reactor side, dipleg plugging will generally be due to coke formation that can be subdivided into two categories: the coke formation that occurs either internal to the cyclone or externally. On the gas outlet tube of the cyclone, you will see the stereotypical coke formation on the backside of the gas outlet tube, perhaps from incomplete feed vaporization. It could also be a result of running a very low conversion operation for some time and leaving crackable material still in the slurry. You end up with a sheet of coke that forms on the back of the gas outlet tubes. Then, during a thermal cycle, that sheet of coke will fall off to the bottom of the dipleg; and since it is bigger than the dipleg diameter, it blocks the flow of the dipleg.
Alternatively, you can get coke formation external to the disengager at the diplegs. In these cases, the coke formation could be due to inadequate purge steam or dome steam. The dipleg valve can become ensconced in coke, as you see in the photograph. Physically, it just will not move. Effectively, you end up with a plugged dipleg. So, the question asks: What are the successes with clearing these types of blockages online? Because these are just physical obstructions, there is little chance that you will be able to fix them with the unit online.
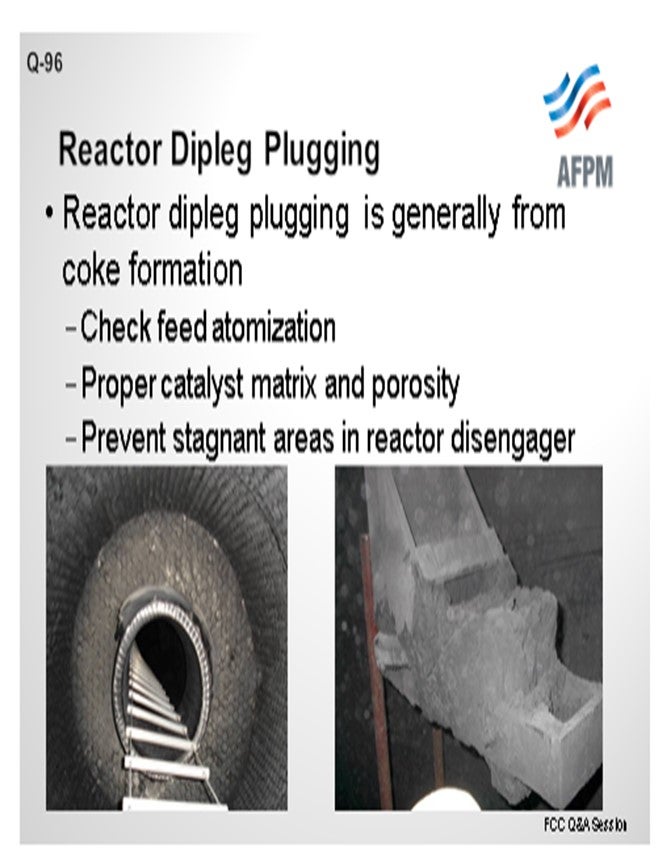
On the regenerator side, one common method of dipleg plugging is due to low melting point eutectics that you associate with iron and calcium contaminants in FCC catalyst. These contaminants tend to form a crust on the outside diameter of the catalyst particle. As the catalyst circulates through the unit, the fines chip off the outside and become extremely enriched in iron and calcium, which exaggerates the formation of eutectics. The formation of these eutectics is why iron, and calcium close off the porosity of the catalyst and become a problem with conversion. That same phenomena can cause the fines to melt locally, especially in high velocity areas where you can get some friction. Combine that with the temperatures in the regenerator, and you could develop a very solid cement-like deposit. I have seen it in the tops of cyclone diplegs, perhaps where the vortex extends down into the top of the dipleg. You get a disc of this sintered catalyst at the top of the dipleg. Again, those are very cement-like deposits, and they are hard to remove online.
The data on the slide is an example of an analysis of such a deposit. You can see that it has rare earth, as well as all of the other components you associate with FCC catalyst. Relative to the e-cat, the deposit is essentially double the contaminant level of iron and calcium. So, one way to avoid this type of deposit is just to keep iron and calcium under control to the maximum extent possible.
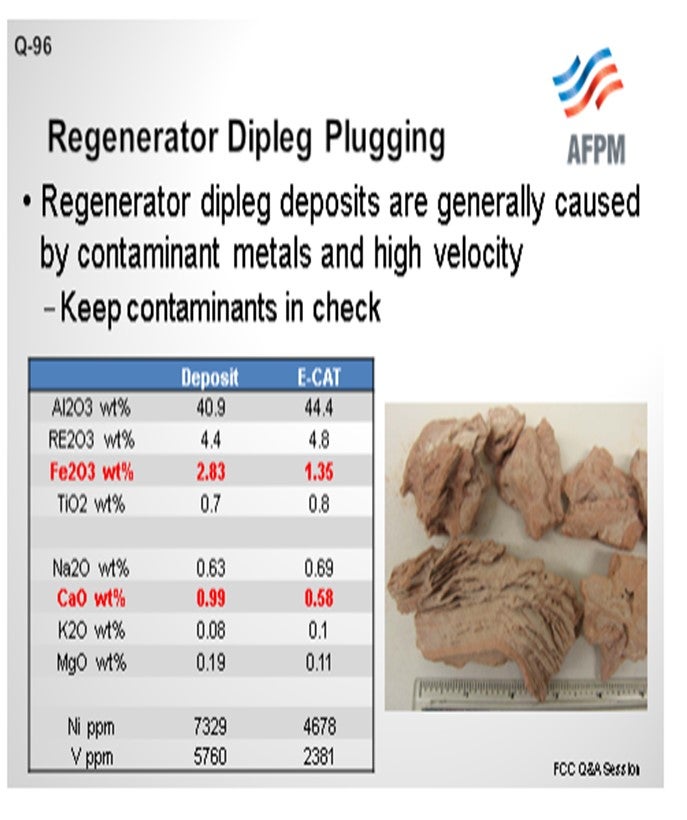
Finally, one of the other causes of dipleg pluggage is fluidization issues around diplegs, particularly submerged diplegs. If you have diplegs that are submerged in the catalyst bed – either in the reactor or the regenerator – and if you have fluidization issues, either you are losing catalyst, and your average particle size is getting high, or you have a damaged distributor or just poor distribution in general in the bed. You can get localized defluidization around the dipleg opening, which results in the effective blocking of the flow out of the dipleg. You then get catalyst carryover from that type of event. For this type of blockage, you will have some moderate degree of success clearing these online. One option is to lower the reactor or the regenerator level down to below the bottom of the dipleg opening, raise it back up, and then re-seal the dipleg in an attempt to reboot the fluidization of the bed. Some refiners have success doing pressure bump procedures to help with fluidization in these cases.
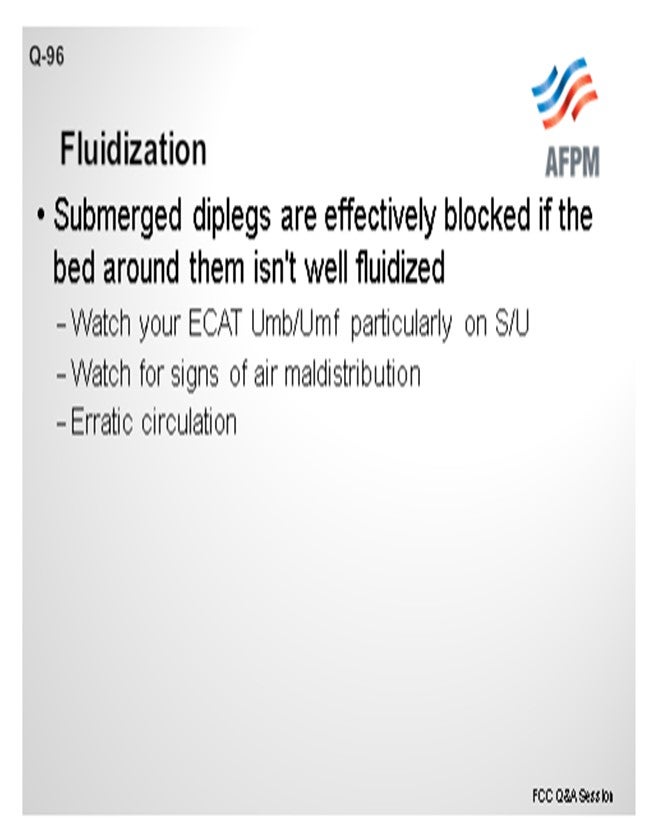
KEVIN KUNZ [Shell Global Solutions (US) Inc.]
Shell has had quite a bit of experience with occasional dipleg plugging from either coke formation or catalyst hang-up. I very much agree with a lot of what Jeff Koebel of Grace said. The coke formation in the reactor side is most often found to be caused by the lack of feed vaporization, particularly in resid cat crackers, and typically toward the end of the run when the feed nozzles begin to wear. To counteract that, obviously, good feed distribution and minimum droplet size are required to minimize the time required to vaporize the feed as much as possible. There are not too many FCCUs with cyclones external to the reactor, but Shell does have one. In this case, it is critical to make sure you have good, uniform heat to the diplegs. Checking for cold spots is a good practice.
As Jeff also pointed out, one of the challenges – online cleaning of a coked-up reactor dipleg – is tough to do. However, sometimes increasing riser temperature or decreasing the sour water use has helped improve the feed vaporization, particularly toward the end-of-run. On the regenerator side, catalyst hang-up can have multiple causes. Uncovering the dipleg termination devices or pressure bumps, and even cooldowns, have been successful at times.
Diplegs which contain obstructions that are operating with faulty termination systems are less likely to be successfully cleared online. Keep in mind that when planning and executing pressure bumps, the key is to do it very safely. You must consider everything that could go wrong and make sure that all of your proper safeguards are incorporated to prevent the plant or other unit shutdowns or upsets. This is very critical.
LEE WELLS (LyondellBasell Industries)
In the past, we have had issues with catalyst becoming defluidized in the reactor cyclone diplegs and plugging up the cyclones. Since we have improved our riser termination devices and lowered the catalyst flux in those diplegs, it has gotten even worse. But we have had success doing pressure bumps on the reactor side to free up that catalyst. The trick is recognizing that you are losing the catalyst before you carryover too much of it into your main fractionator.
MICHAEL WARDINSKY (Phillips 66)
One time we plugged up the diplegs in a third-stage separator due to what we believe was a combination of about three factors. The first was the existence of a lot of circulating fines in the inventory due to an attrition source that had developed during a startup. The second was relatively high concentrations of alkaline metals being present in the circulating inventory. We had been using a SOx reduction additive that contained a high level of magnesium. The third factor was that the unit experienced an exotherm due to a reversal scenario. The combination of those three factors led to the formation of a very hard ceramic like deposit in the TSS diplegs. I think we had to use a diamond-tipped drill bit to get them out.
JEFF KOEBEL (Grace Catalysts Technologies)
Dipleg deposits or blockages that lead to excessive catalyst losses happen as a result of a variety of causes. On the reactor side, dipleg plugging or blockages are often the result of coke formation. Coke can form on the internals of the cyclone gas outlet tubes, opposite from the gas inlet duct. This coke formation is generally stable and can build up to a thickness of several inches during normal operation. These sheets of coke can become dislodged during a thermal cycle and fall into the cyclone body where they come to rest at the top of the cyclone dipleg. This physical blockage restricts the flow out of the cyclone. The key to preventing these deposits is to prevent the coke formation in the first place. Make sure that feed is adequately atomized in the riser feed distributors because unvaporized feed can travel up to the top of the riser and lay down as coke in the cyclones. Additionally, a catalyst with adequate active alumina for bottoms cracking is critical to assure proper feed vaporization and pre-cracking, particularly when running a feed with any resid content.
Coke formation can also come in the form of generalized reactor coking throughout the reactor vessel. In this scenario, coke can form on dipleg outlet valves. This coking can restrict the proper movement of these valves, leading to catalyst losses.
Generally speaking, with either of these types of dipleg deposits caused by coke formation, there is little experience with successfully clearing the deposits with the unit operating.
On the regenerator side, dipleg deposits are often the result of the formation of low melting point eutectics. These eutectics occur when specific contaminant metals – such as Fe (iron), Ca (calcium), and Na (sodium) – are elevated. These deposits form a crust on the outside surface of the catalyst that can chip off during normal operation and cause the FCC catalyst fines in the inventory to be very highly enriched with these contaminants. When the fines are circulating in high velocity areas such as the bottom of a cyclone dustbowl, at the top of a cyclone dipleg, or perhaps orifice chamber plates, the combination of the heat from the regenerator and local friction heating is enough to cause the fines to melt and form hard deposits at the point of first contact with the internals. These deposits, when analyzed, will typically show Fe and Ca enrichment about two times the level of contamination in the circulating catalyst inventory. Table 1 is an example of a typical analysis of these deposits compared to e-cat. The deposits also often show that the zeolite is compromised, as if exposed to high temperatures which would not be present according to the unit data. These types of regenerators dipleg deposits are very hard and must often be physically chipped out of the cyclone. They cannot be cleared online.

Finally, fluidization issues can also cause dipleg blockages. During times of catalyst losses, the FCC catalyst inventory can get very coarse with inadequate fines content. Fluidization issues can develop in a dipleg or around the dipleg openings for submerged diplegs, even if the catalyst circulation is unaffected by the change in the catalyst fluidization characteristics. This can be a problem, particularly after a turnaround when the catalyst inventory is reloaded into the unit. There has been some success with clearing these problems during unit operation. Pressure bumps or draining of the vessel level below the dipleg discharge level are solutions that have been successful in some circumstances and should be attempted as a last resort measure only, as the risk for a significant catalyst loss event is high. These types of blockages are particularly frustrating because they will often disappear during a unit shutdown when the catalyst is deinventoried, leaving behind no evidence as to what caused the blockage in the first place.
CATHERINE INKIM (PETROTRIN)
Though we have not experienced dipleg plugging or fouling, dipleg plugging can be a result of coke, refractory, or catalyst plugging. Typically, the diplegs in the reactor can be plugged by spalled coke after a thermal cycle or by defluidized catalyst in both the reactor and regenerator diplegs. Pressure bumps may help the latter.
CHRIS STEVES (Norton Engineering)
In reactor diplegs, plugs are often caused by coke, catalyst, and refractory. With the decreasing 6 oil market, the push to convert more of the bottom of the barrel is increasing. FCCs share in this effort, and some have been referred to as catalytic cokers. The heavy resids and tars are difficult to atomize and convert. Even if the conversion looks good, these high molecular weight molecules slowly build in all parts of the reactor, especially in areas of low velocity or adjacent to exposed “cold” surfaces. Thermal cycles from startups and shutdowns will eventually spall coke from the reactor internals, and this coke can end up plugging cyclone outlets and diplegs. Prevention of coke buildup is the key to avoiding this type of issue. Maintaining high enough riser temperatures to ensure vaporization of the feeds being processed and ensuring that cold wall reactors are well insulated to prevent coke formation is essential. Anti-coking baffles have successfully been installed in some reactors to allow for a steam purge of low velocity areas (typically above cyclones) so that coke will not form in these areas.
Catalyst can also plug reactor diplegs. Experience has shown the plugging is most frequent on unit restarts and likely from wet catalyst. The catalyst is wet either from oil or from steam/condensate from the restart or shutdown. To prevent wet catalyst from plugging diplegs, use of superheated steam in the stripper during startup, as well as early circulation of hot catalyst from the regenerator to the reactor, can help prevent wet catalyst from plugging diplegs.
In regenerator cyclone diplegs, refractory and defluidized catalyst can lead to dipleg plugging. Proper refractory inspection and repair during unit shutdowns is essential to prevent refractory damage and potential dipleg plugging. Defluidized catalyst “plugging” of diplegs may also occur, especially if the air distributors are damaged and zones of defluidized catalyst exist in the regenerator dense bed.
If dipleg plugging is observed during operation of the FCC unit (as diagnosed by high losses and sampling of the catalyst fines for PSD analysis), some online techniques have been successfully executed. Changes in bed level (for units with submerged diplegs) may help in changing the pressure balance in the cyclone dipleg enough so that the plug is dislodged. Rapid pressure swings on the unit can also be used to dislodge a blockage. With external diplegs, diagnosis of plugged diplegs can be easier (looking for cold spots). The use of vibrators, external heat, or a hot gas injection can be used to clear the blockage.
ROBERT TORGERSON and SYDNEY GARRETT (Gayesco International)
It is possible for diplegs to foul during the startup process if the dipleg is too cold. The resulting condensation can cause the catalyst to bridge and impede catalyst circulation. We have many customers who now require the attachment of removable skin thermocouples to the diplegs to monitor that temperature during startup. Removable thermocouples allow for easy replacement, simplified dipleg maintenance, and easier installation as the attachment hardware can be installed by the dipleg/cyclone manufacture during initial fabrication.