Question 95: What is the recommended Best Practice regarding the design of catalyst loading and unloading lines with respect to metallurgy, size, run lengths, bends/Ts, cleanout connections, etc.?
WILLIAMS (KBR)
KBR’s Best Practice is to fabricate the main catalyst loading and unloading lines with carbon steel. To protect the carbon steel lines against elevated regenerator temperatures, KBR recommends that Operations personnel only de-inventory the converter after the catalyst has been cooled below 650°F. The main catalyst loading and unloading lines are sized for an approximate vapor velocity of about 40 fps, and an inventory loading target of about 68 hours.
We also equipped the unit with a smaller 321H stainless steel line utilized to unload hot catalyst during normal operation for regenerator inventory or level control. For optimum loading, KBR targets shorter carrier length links with the least turns possible. Impact Ts or blinding Ts are used for the turns to protect the piping elbows from erosion. These Ts are properly spaced at least five to 10 diameters apart to minimize line pressure drops. Finally, we also equipped the line with one-inch blow-out connections, which are placed every 50 feet, to blast the unloading piping in the event the line becomes blocked.
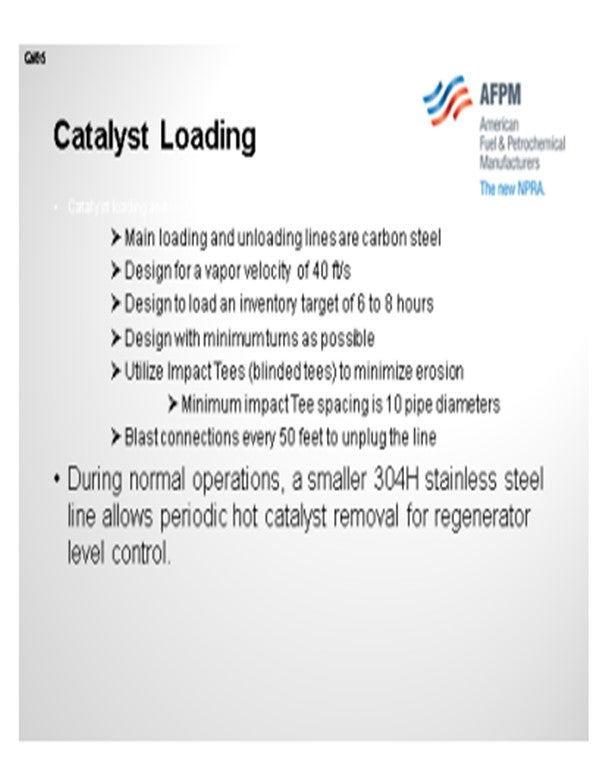
LALL (UOP, A Honeywell Company)
In general, I am in agreement with the comments made by KBR. We differ in that UOP’s standard piping metallurgy for handling hot catalyst from the regenerator is low chrome. As part of that system, we have a finned, low chrome piping section of approximately 100 feet provided downstream to enhance the heat transfer, which permits hot catalyst removal. We then switch to killed carbon steel for the piping to the hopper. Several skin thermocouples are installed along the piping system to assist in the monitoring of the catalyst withdrawal rate.
PIMENTEL (CITGO Petroleum Corporation)
I have nothing to add on the piping design. I want to say that it is important to have significant pressure in your plant air system over the internal regenerator pressure in order to avoid any backflow. You should also design your system to accommodate for the consumption peaks typically associated with the loading or unloading catalyst trucks. Inadequate air supply will result in hot catalyst backflow to the air pipes.
AVERY (Albemarle Corporation)
Catalyst loading and unloading lines are generally fabricated from carbon steel. Some refineries have used or added finned piping to portions of these lines if the catalyst withdrawal system is continuous or almost continuous. Aeration taps are typically installed every 22 feet to maintain sufficient carrying air to transport the catalyst. It is essential that the carrying air be dry. Most systems employ long radius bends to make turns, but several have used Ts at the transition for horizontal to vertical.
Cleanout connections are located at strategic points along the system. T cleanouts are needed to clear catalyst from portions of the piping, particularly the vertical sections, if aeration is lost. Otherwise, carrying air will is lost, thereby allowing the catalyst to settle. As the catalyst reaches the internal angle of friction, it is virtually impossible to blow the catalyst out of the line. Run lengths will depend on the location of the catalyst hoppers relative to the regenerator.
KEVIN PROOPS (Solomon Associates)
I want to comment on Jesse’s response. I am familiar with a regenerator with a 300 series stainless steel withdrawal nozzle which cracked due to polythionic stress corrosion cracking. It then fell off the regenerator and caused an unplanned shutdown.
AVERY (Albemarle Corporation)
We have not experienced any of that. To my knowledge, our systems have been very reliable, but it is great that you added that to the conversation.
ROBERT KURTAS (Hess Corporation)
In the continuous withdrawal system, what type of valves do you use that do not erode away?
SCHOEPE (Phillips 66)
At our refinery, we have actually experimented with a new type of valve. I am not supposed to be specific, but it is a boiler valve. There is a different manufacturer in Houston who also fabricates a very reliable ball valve. Some of these ball valves eliminate the air purges. Most of the erosion I have seen has really been caused because operators forgot to turn off the aeration to the stem seat and stem. We had huge problems with that until we changed operating practices to allow you to turn off your catalyst aeration air whenever you are not using your unloading line.
MARTIN EVANS (Johnson Matthey Intercat)
We have quite a lot of experience putting addition systems into newly built FCC units and helping people design their catalyst addition lines. I agree with everything that the panelists have said and want to add a few thoughts.
In a lot of newly built FCCs, we have seen the E&C (Engineering and Construction) contractors requiring Schedule 160 pipe and 300-pound flanges on catalyst addition lines. To me, that is total overkill. We have been using Schedule 80 pipe with 150-pound flanges for over 20 years, and we still have systems out there that are working perfectly fine.
One of the biggest problems I have notice with catalyst withdrawal piping is that most catalyst withdrawal lines are designed to allow the regenerator to be de-inventoried for a shutdown, but they are not designed for continuous withdrawal on the run. So what usually happens is that you have a 6-inch or an 8-inch line. You try to withdraw small amounts of catalyst every few days down that line, but it is just not designed for that service.
With our new catalyst withdrawal system, we are using a 1.5-inch diameter withdrawal line, which sounds incredibly small. But actually, you can get over 30 tons a day down that line in continuous withdrawal mode. So, you do not need a very big pipe if you are doing continuous catalyst withdrawal.
WILLIAMS (KBR)
KBR’s Best Practice is to fabricate the main catalyst loading and unloading lines with carbon steel. To protect the carbon steel lines against the elevated regenerator temperatures, KBR recommends operations personnel only de-inventory the converter after the catalyst has cooled below 650°F. The main catalyst loading and unloading lines are sized for an approximate vapor velocity of 40 fps and an inventory loading target of six to eight hours. A smaller 321H stainless steel line is utilized to unload hot catalyst during normal operations for regenerator inventory (level) control.
For optimum loading, KBR targets shorter carrier lines lengths with the least turns possible. Impact Ts (blinded Ts) are used for turns to protect piping elbows from erosion and are properly spaced at least 10 pipe diameters apart to minimize line pressure drops. Finally, one inch blowout connections are placed every 50 feet to blast the unloading piping in the event the line becomes plugged.
PIMENTEL (CITGO Petroleum Corporation)
In addition to the design aspects of the catalyst lines, it is important to ensure good supply of air to prevent catalyst back-flow. Our standard is to provide a minimum of 20 psi of pressure over the internal unit pressure (standpipe or regenerator), and design the system to support other activities that could potentially affect the local plant air pressure; such as loading or unloading catalyst from the unit hoppers to trucks.
AVERY (Albemarle Corporation)
Catalyst loading/unloading lines are typically fabricated from carbon steel. Some refiners have added finned piping to portions of these lines if the catalyst withdrawal system is continuous or almost continuous. Aeration taps are installed every 20 to 30 feet to maintain sufficient carrying air to transport the catalyst. It is essential that the carrying air be dry. Most systems employ long radius bends to make turns, but several have used Ts at the transition from horizontal to vertical. Cleanout connections are located at strategic points along the system. T cleanouts are needed to clear catalyst from the portions of the piping, particularly the vertical sections, if aeration is lost, or carrying air is lost and catalyst is allowed to settle. As catalyst reaches the internal angle of friction, it is virtually impossible to blow the settled catalyst out of the line. Run lengths will depend on the location of catalyst hoppers relative to the regenerator.
LALL (UOP, A Honeywell Company)
The following criteria are used by UOP for design of the catalyst bulk loading (filling) line to the regenerator and unloading line for complete de-inventory:
a) Catalyst loading and withdrawal lines are normally sized to a catalyst flux criterion based on less than 75 lb/ft2 -s (pounds per square foot per second) and a velocity of 30 fps to 40 fps.
b) Blast connections are located every 40 feet of catalyst pipe run.
c) The piping metallurgy for handling hot-catalyst from the regenerator is 1¼ Cr – ½ Mo (molybdenum) Class 300#.
d) Killed carbon steel class 300-pound rating is specified for piping section that operates below 400°C.
e) Double block valves located close to regenerator shell in each main withdrawal line. The one installed at regenerator nozzle shall be only operated in the fully open or fully closed position. The second valve can be used to “control” the catalyst transfer rate (note regulating the hopper pressure to limit the catalyst withdrawal rates greater enhances the longevity of the valve in this case).
f) All gate valves have plant air purge connections at the bonnet and seat to prevent ingress of catalyst and allow full opening/closure of the valve.
g) A finned piping section [approximately 25 m (meters) to 30 m] is provided downstream of normal catalyst withdrawal. A bulk unloading/loading branch connection is installed to enhance heat transfer and assist in reducing catalyst temperature from dense bed condition.
h) Several skin thermocouples are installed along the piping system to assist in monitoring the catalyst withdrawal rate.
Catalyst lines to and from catalyst storage hoppers and vacuum cleaning header shall be designed to meet the following requirements:
a) Changes in direction shall be made with pipe bends or Ts, as specified on the P&IDs. When long radius bends are specified, pipe bends shall have a radius between 9 and 18 (preferred) diameters of pipe (long radius elbows in the catalyst withdrawal line and catalyst filling and withdrawal line running to the hoppers are no longer specified by UOP and have been replaced with blind or hard Ts as these prove to be more durable).
b) Grind smooth the welds inside of pipes for butt-welded piping system. The slag and debris can obstruct catalyst flow.
UOP’s designs also incorporate a continuous catalyst withdrawal system for high catalyst users. Continuous catalyst withdrawal, in combination with continuous catalyst makeup, allows the catalyst inventory to be minimized and better catalyst activity maintenance. A continuous plant air purge used to maintain the catalyst fluidized also promotes higher heat transfer. An automatic valve (Everlasting, mogas, or equivalent) operates in an on/off mode to modulate the catalyst transfer from the regenerator to the catalyst hopper. The time intervals in the open and closed position is determined from actual operation experience based on mass of catalyst to be transferred, available pressure driving force, regenerator temperature, heat transfer rate with installed piping, and the return temperature to the spent or equilibrium hopper.