Question 94: What methods do you use to determine the condition or remaining life of and regenerator cyclones?
GIM (Technip Stone & Webster)
Proper design of cyclones and cyclone support systems will extend the life of cyclones with proper maintenance. But like the tires on your car, it will need to be replaced towards its end-of-life. Just like checking for remaining treads on your tire, one common way to check the remaining life of your cyclone is to measure and log the thickness of your cyclones for each turnaround from their first installations to last turnaround dates. We can use that thickness in various locations on the cyclones and trend them to predict, before the next turnaround, whether a cyclone will need to possibly be replaced or even how much repair may be required on the next shutdown.
In general, cyclone systems are designed for at least 20 years of life. There are two components that determine the life of cyclones: the condition of the metal and the condition of the refractory. Obviously, steady-state operations with limited upsets and excursions will extend cyclone life. Any excursions beyond the original design temperature will obviously decrease the life of the cyclones.
The adoption of the so-called Life Fraction Approach will determine the allowable stress, which considers the normal operating range of temperatures over which cyclones are operated during the course of a year. Excursions beyond the design temperature reduce the allowable stress used for the design of cyclones. The use of this Life Fraction Approach for determining the allowable stress for design of cyclones will allow operators to analyze the life of the cyclone’s metallurgy by comparing its assumed annual temperature profile versus actual operations at temperatures below the designed temperature, as to life of cyclones. Obviously, operation at temperature above design temperature will reduce the life of cyclones.
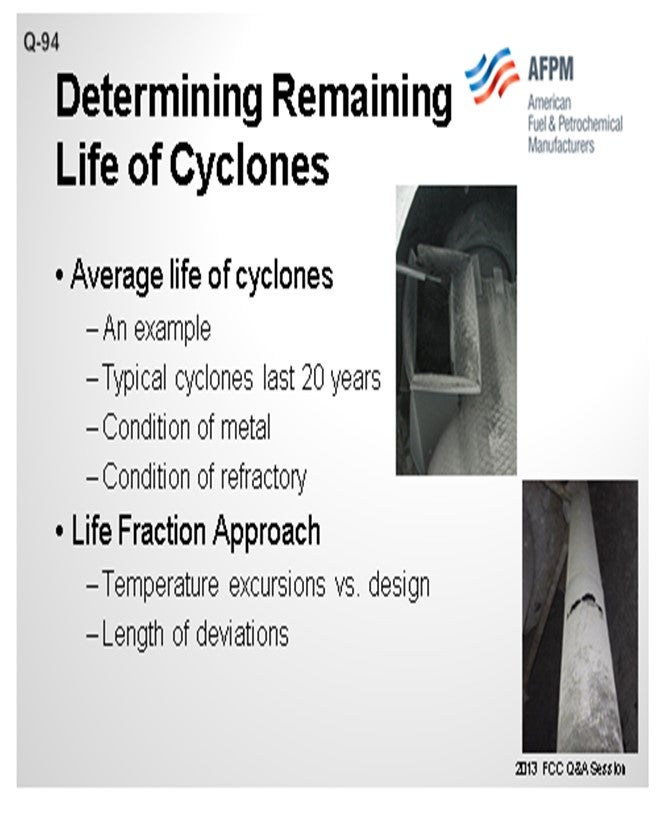
INKIM (PETROTRIN)
The inspection methods we use to determine the condition or remaining life of cyclones are visual, hammer, dye-penetrant, and ultrasonic testing. The results of the inspection and the thicknesses of the cyclones are compared to the original thicknesses and past values. Based on the findings, repairs or renewals are done. If there is significant erosion or thinning of about 40 to 50%, we will recommend replacement.
In the past, we have determined remaining expected life based on creep calculations, as Steve had said. There was an incident in the past where, due to a change in feedstock, we had to operate at abnormally high temperatures above the design temperatures. We consulted the cyclone vendor to get a revised life expectancy. They considered the past operating temperature profile, the original design, and the abnormally high conditions we wanted to run in the creep calculations. Thus, we were able to determine if we needed to shut down before the plant turnaround or whether we could use the cyclones up to the scheduled turnaround.
KEVIN KUNZ [Shell Global Solutions (US) Inc.]
Shell uses much of what the panelists mentioned; and like them, our methods have evolved for evaluating and checking cyclone remaining life. Years ago, Shell used techniques similar to those described by Catherine Inkim of PETROTRIN – visual inspection and hammering for integrity – but not a lot more. Today, though, Shell does more inspection at midlife using liquid penetration, particularly around high-stressed welds. Shell will selectively collect samples for carburization, sulfidation embrittlement, creep, and corrosion behind the refractory. The discovery of cracks often leads to weldability checks and testing for sigma phase in the regenerator and/or carburization and/or sulfidation, and creep in the reactor side. Shell also checks for cyclone erosion but rarely replaces the cyclones for erosion problems unless the cyclones are at the end-of-life. Strict adherence to velocity constraints and the advent of vortex stabilizer technology has improved cyclone system life. Vortex stabilization has dramatically extended cyclone life and minimized its repair. The norm is 15 years with little refractory repair in the cyclone cone.
Unlined portions of diplegs are checked with a mixture of remotely operated cameras, as well as a combination of manual and automated ultrasonic thickness measurement.
Shell selectively uses FEA (finite element analysis) in areas where metal degradation (creep and/or corrosion) is limiting cyclone system life. This guides local repairs and reinforcements rather than when complete cyclone system replacement may not be warranted. In some cases, we assess potential creep damage using actual historical temperature data pulled from the Process Engineering department, including monthly averages and detailed data around upsets.
We have sample plates with combinations of erosion-resistant refractory and metallic anchor materials placed in a number of regenerators. Data from these sample plates will be used to predict, rather than react to, corrosion behind the refractory.
KRISH KRAHEN (Marathon Petroleum Corporation)
Can you comment on techniques used to assess a decrease in weldability of cyclones as they age, and it becomes harder to do crack repairs?
KEVIN KUNZ [Shell Global Solutions (US) Inc.]
We check primarily for sigma phase. Now, the exact test that our mechanical department uses is not a specific ASTM (American Society for Testing and Materials) method. And if sigma phase is present, there is a limit to the amount of sigma phase that can be seen in the cyclones before you begin to run into trouble with weldability repairs. Shell checks for sigma phase primarily by doing in situ liquid penetrant inspection. The amount of cracking is trended TA turnaround) to TA. Based on the trending of number of cracks and the difficulty of doing local repair welds, we remove samples to represent the mix of plate and weld processes used to make the cyclones. These are polished and etched to reveal the extent of sigma and any remaining unconverted ferrite.
LARSON (KBC Advanced Technologies, Inc.)
This situation is not just in the U.S., although this is primarily a U.S. group here. I have seen locations where they cycled the cat cracker a lot more than we might do in the U.S., sometimes bringing down a unit every two years as opposed to every four years. Those up-and-down heating cycles degrade the run length of the unit even though you might think that cyclone should operate well. Cycles of startup and shutdown have caused a real degradation in the performance of those units. You will begin to actually see the barrels start to change and not be quite so round. As you are going in, you should monitor not just the metallurgy itself, but also the barrel to make sure it maintains its shape; because that will become a problem in your ability to maintain catalyst performance, and you will start to see erosion. We know of a company in Japan right now that is working on its 45th cycle on its cyclone. They cyclones were replaced last over 20 years ago.
STEVE GIM (Technip Stone & Webster)
Proper design of cyclones system, including the support system, will extend the life of the cyclones as will proper maintenance; but like tires on your car, they do wear out and need to be replaced at the end of their life. One refinery maintenance manager used to measure and log the thickness of his reactor and regenerator cyclones on each turnaround, from their first installation through the latest turnaround. He also used to measure the refractory thicknesses at various locations on the cyclones. He then could trend refractory loss from turnaround to turnaround and predict, before the next turnaround, whether the cyclones needed to be replaced or even how much repair would be needed. As his FCC tended to run the same rate and essentially the same feeds all of the time, the cyclone degradation over time could be trended.
I would also like to thank our friends at Emtrol for providing some empirical data from their knowledgebase.
Average Life of Cyclones: The average life of regenerator cyclones is about 20 years, when eliminating those systems that have been destroyed in the first operating campaign due to upset conditions and those operated well below design conditions extending life well beyond the norm. In general, cyclone systems are designed for a 20-year life. There are two components that determine the life of the cyclones: the condition of the metal and the condition of the refractory, both of which begin to deteriorate after the initial startup. Steady-state operation, limiting upsets, excursions, and afterburn extend the life of the cyclones. Utilizing a standard approach for determining allowable stress from the ASME code for a given design temperature does not directly address upset conditions that can greatly reduce the life of a cyclone system. For example, a one-hour upset at 1800°F will reduce the life of the cyclones by many years, depending on the actual design temperature used for design (1400°F, 1450°F or 1500°F).
Life Fraction Approach: Adoption of a “Life Fraction” approach for determining the allowable stress, which considers the normal operating range of temperatures that the cyclones are operated over the course of a year, including excursion temperatures (1500°F, 1600°F and even 1800°F), normally reduces the allowable stress used for the design of the cyclones but provides for operation at upset temperatures for a predetermined period of time. Use of a “life fraction” approach for determining the allowable stress for design of the cyclones will allow the refiner to analyze the life of the cyclone metallurgy by comparing the assumed annual temperature profile to the actual operating temperatures. Operation of the cyclones at temperatures below the design temperature adds life to the cyclone system, while operation at temperatures above the design temperature reduces the life.
CATHERINE INKIM (PETROTRIN)
During turnaround, the cyclones are inspected for cracks, erosion and corrosion, and thinning. The inspection methods used are visual, hammer, dye penetrant, and ultrasonic testing. Welds are examined for cracks. The cyclone supports and body are checked internally and externally for breakages, erosion, gouging, holes and thicknesses, lining and hex mesh for erosion/corrosion, and valves for movement.
The results of the inspection of the thicknesses of the cyclones are compared to the past values, as well as the original thickness of the cyclone material. Depending on the past history or severity of the findings at the current inspection, certain parts of the cyclones (for example, diplegs) may be renewed, as well as repairs done to the Resco lining and hex mesh and weld buildups. Some degree of repairs is always anticipated. However, if there is significant erosion/thinning of the order of 40 to 50%, then recommendations are made for replacement.
In the past, due to changing feedstock quality and mechanical issues with the air grid, we were forced to operate the regenerator at higher temperatures than originally designed. At that time, the cyclone vendor was consulted to provide a revised life expectancy for the cyclones if we continued to operate at the new abnormal conditions. Based on the historical operating temperature and the higher new temperatures, they provided the remaining expected life based on creep calculations and thus determined if a shutdown was warranted before the planned turnaround. Similar analyses can be used to determine if a particular operating mode would be economical, even though it may mean replacement of cyclones sooner than original design life.