Question 92: What experience is there with cracking whole crudes in the FCC? What are the considerations for new crude sources?
KOEBEL (Grace Catalysts Technologies)
This is a question that comes up relatively frequently and is an area where Grace has done extensive R&D work and publication. I will summarize a longer answer that appears in the Answer Book. So please refer to that response, as well as to some of the publications Grace has in the trade magazines. In order to be able to help customers with the thought of running whole tight oil to the riser, we ran a sample of Bakken crude straight to our Davison circulating riser pilot plant over a moderate Z/M catalyst. Our data for the feed sample is shown on the slide and compared to a published assay of Bakken. We felt it was relatively representative of a typical Bakken crude.
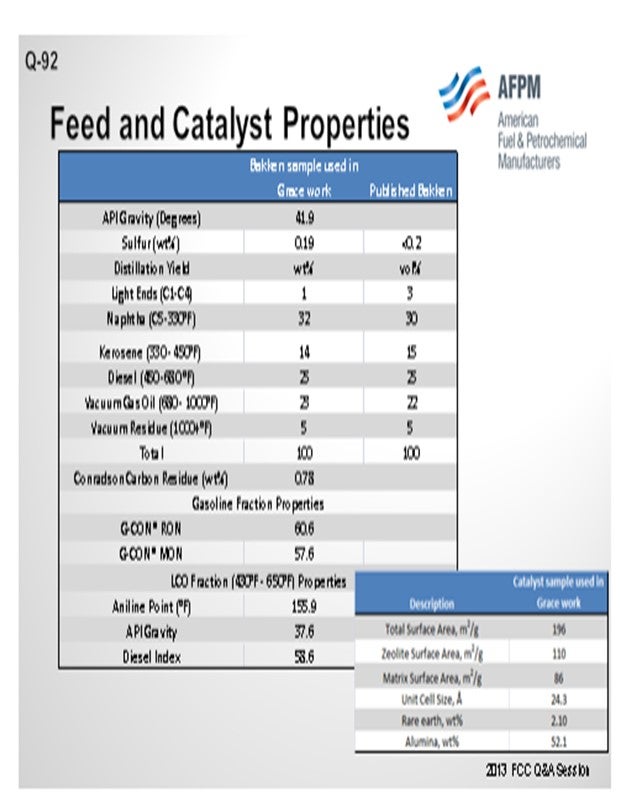
To summarize, the data behaved much as you would expect. There was a fair amount of 650°F minus in the feedstock, so it made significant amount of gasoline. You can see that the cracking yield was on the order of 65% gasoline. A lot of that was the gasoline inherent in the crude initially; it had just come along for the ride. There was not much conversion of those molecules that were present in the feed. As a result, the overall FCC gasoline octane is moderately low. The feed actually did convert very well, although it made very low coke and low bottoms yield.
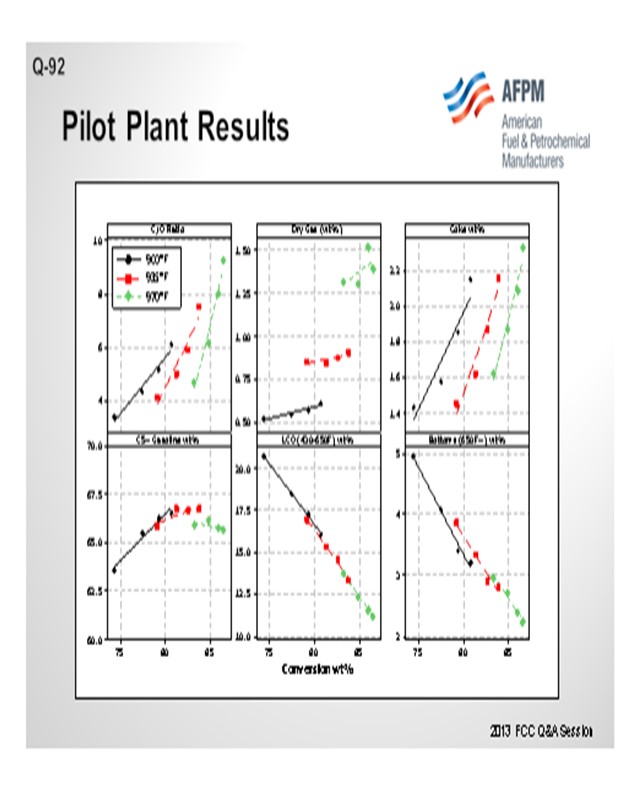
These are the specifics of the FCC gasoline from those products. You can see that the RON is much lower than 80, even significantly lower than you would typically give an FCC naphtha. It did have the normal response to reactor temperature that you would expect with an increasing RON as a function of reactor temperature. But still, the overall magnitude of the octane was very, very low.
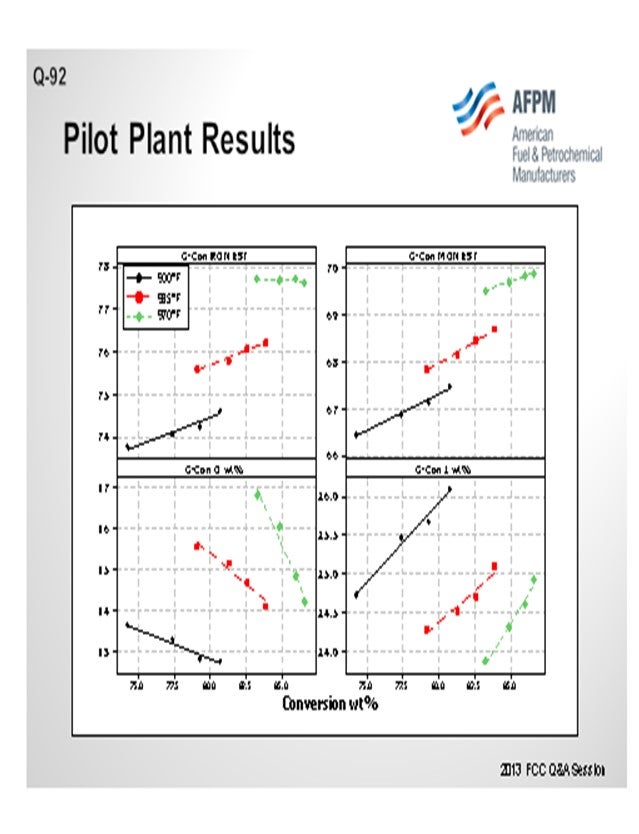
On the other hand, the light cycle oil was a much better quality than you would get from a typical FCC light cycle oil. This, again, is partially due to the material that was inherent in the feed. But overall, the quality of the LCO was not really a function of reactor temperature. It was more a function of conversion level and how much of the material in the LCO you were cracking up the tower while leaving the paraffinic molecules in the LCO. The diesel index was on the order of 35 to 45; whereas with a typical FCC light cycle oil, the diesel index was usually in the single digits. So, the quality of the light cycle oil you get from processing shale oil with the riser is much better than what you normally get with FCC light cycle oil.
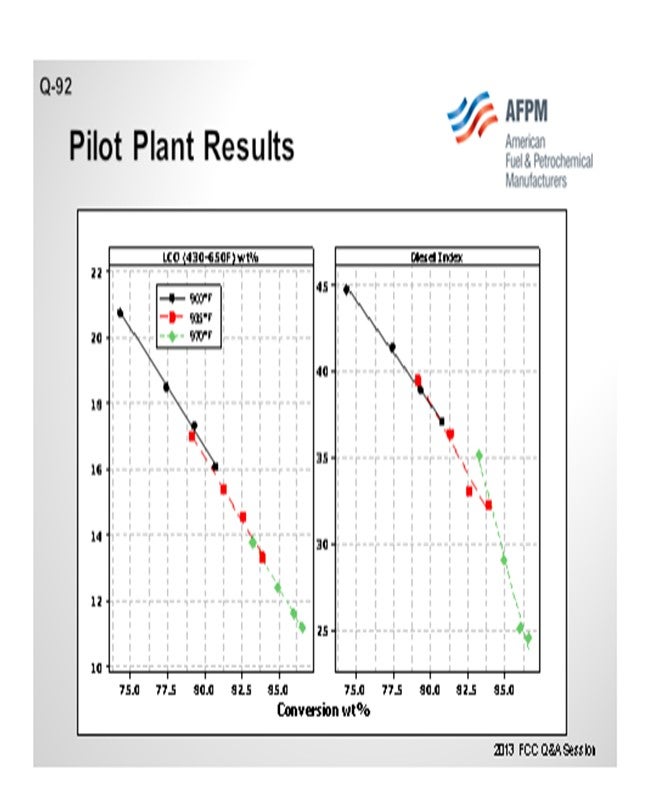
The question also asked about some of the other considerations for doing this. One of the considerations is that, with the variability of the tight oil quality, from time to time you may get unusual contaminant metals in the FCC feed. This slide shows one example of a unit that was routinely running Bakken crude to the riser. Over the course of a 10-day period, a spike of sodium hit the unit hard. This spike cost them about 10 points in activity on their circulating inventory. Often, the refinery is not set up to desalt the FCC feed directly. So, if you have a raw crude coming to the riser, you may see this happen, either with sodium or other contaminant metals.
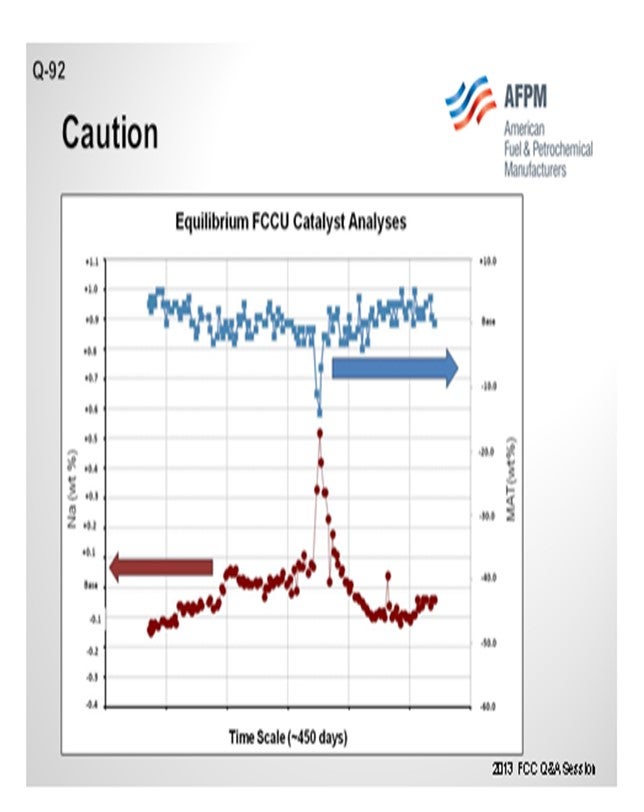
BULL (Valero Energy Corporation)
At Valero, we process desalted pre-flash crude in several of our FCC units. We desalt the crude or remove as many of the contaminants as possible. We also may pre-flash the crude to take off the light gas and naphtha, which is shown in the drawing on the slide. We run it through a desalter to try and take out contaminants. It then goes into the pre-flash tower to take off any light gas and some of the light naphtha, and then take the bottoms of that to the FCC unit. We have done this at several refineries. The pre-flash crude is then sent directly to the FCC feed drawing process in the unit.
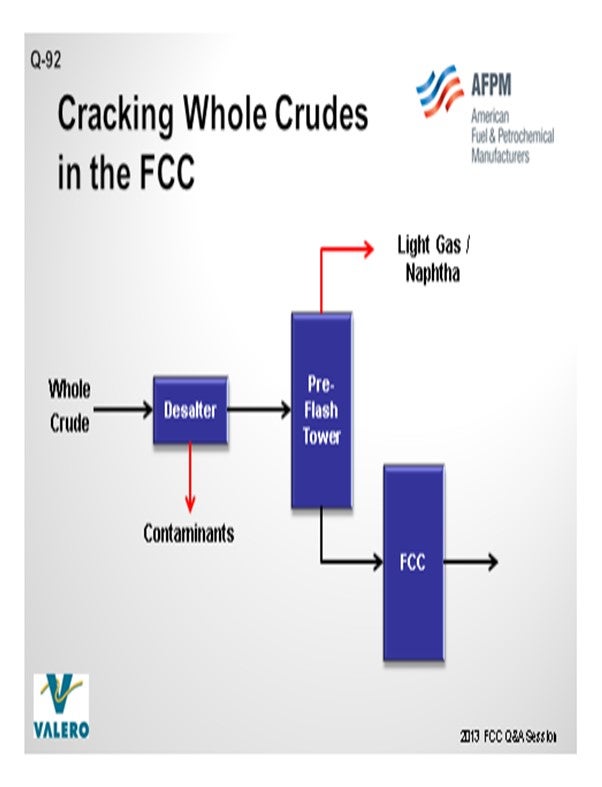
In general, the naphtha boiling range material goes straight through, and then we can see a proportional increase in the gasoline FCC naphtha range. The naphtha also has a cat cooling effect without the cat cooler, so you must take that into account when processing crude directly to the FCC. Some of the diesel boiling range material passes through, but we do see some of the heavier components of the diesel crack. The remaining portion of the pre-flash crude is your typical FCC feed at that point. So, the net effects are a reduction in overall liquid yield on the unit and the shift in selectivity to more naphtha and diesel range material.
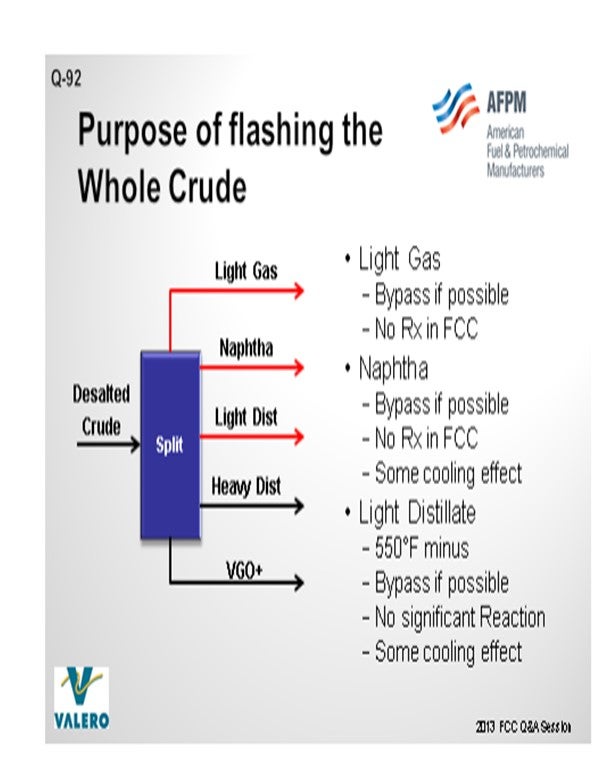
Two primary considerations for investigating new crude sources for processing directly in the FCC are the contaminant levels that Jeff referred to earlier, as well as the effect of the light material and the impact that will have on your delta coke and heat balance.
SOLLY ISMAIL (BASF Corporation)
All of these tight oils are very low in aromatics components. They typically have shorter length hydrocarbons which, when mixed with vacuum resid, can create salting out or compatibility issues. One way to address the compatibility issues is to extend the analysis and include the peripheral unit; i.e., the furfural unit in a lube plant. We know that in a furfural unit the paraffins are being separated from the naphthenes and aromatics. These paraffins are then sent for dewaxing to make base stock for lube oil while the extract, which is rich in aromatics, and some naphthenes become an orphan stream of the refinery. In this case, I am assuming that refinery does not make grease with the extract. Because this furfural extract stream is rich in aromatics, it is difficult to crack and makes lots of coke, which has always been a problem. Therefore, FCC operators are reluctant to accept furfural extract for processing in their units.
Nevertheless, refineries do process lube extracts (in low concentrations) in the FCC and would generally like to process more or higher levels in their feed to the FCC.
As just mentioned, because of the high tendency for furfural extract to make coke in the regen, refiners have been having a tough time blending it away in the FCC feed. However, when a refiner is processing large amounts of tight oils, the situation is completely different. In the scenario when tight oils are being processed, the regenerators have the problem of running at low dense bed temperatures. I think when processing high concentrations of tight oils in the FCC unit, increasing the levels of furfural extract with tight oils might be a blessing. Not only will the furfural extract provide an increase in the level of coke in the FCC regen, but it should help improve the compatibility issues as this stream contains large hydrocarbon molecules that can keep the vacuum resid in the solution.
JEFFREY BULL (Valero Energy Corporation)
At Valero, we have processed desalted pre-flashed crude in several of our FCC units. We desalt the crude to remove as many contaminants as possible, and we pre-flash the crude to take off the light gas and light naphtha. The pre-flashed crude is then sent directly to the FCC feed drum and processed in the unit. In general, the naphtha boiling range material goes straight through the FCC and, in effect, blends with the traditional FCC-derived naphtha. The naphtha also has a “cat cooling” effect without the cat cooler. Some of the diesel boiling range material cracks and some of the naphtha material passes through the FCC reactor. The remaining portion of the pre-flashed crude is typical FCC feed. The net effect is a reduction in overall liquid volume yield and a shift in selectivity to more naphtha and diesel range material. The two primary considerations for looking at new crude sources for processing directly in the FCC are contaminant levels (metals, sodium, calcium, etc.) and the amount of light material that essentially takes a free ride through the FCC and has a significant impact on the heat balance.
JEFF KOEBEL (Grace Catalysts Technologies)
The introduction of novel drilling technologies has resulted in large amounts of oil from shale becoming available in North America. While fluid catalytic cracking is typically done to reduce the molecular weight of the heavy fractions of crude oil (such as vacuum gas oil and atmospheric tower bottoms), in some cases refiners are charging whole shale oil as a fraction of their FCC feed.5 Also, whole crude oil has been charged to FCC units when gas oil feed is not available due to maintenance on other units in the refinery6 and to produce a low-sulfur synthetic crude7 .
As a model case for understanding the cracking of whole crude oil in the FCC and the effect of process conditions on yields, a straight-run shale oil was processed in the Grace DCR™ pilot plant at three riser outlet temperatures: 970°F, 935°F, and 900°F. The whole crude oil was a light sweet Bakken crude with a degrees API gravity of 42. The properties of the crude were similar to those given in a publically published assay8 . Table 1 presents a comparison of the properties of the whole crude used by Grace and the publically available assay data. Additionally, the straight-run Bakken sample was distilled into a 430°F minus gasoline cut and a 430°F to 650°F LCO cut. The properties of these cuts were measured. Gasoline from the straight-run Bakken was highly paraffinic and had low octane numbers [a G-Con® RON software of 61 and MON (motor octane number) of 58]. The LCO fraction had an aniline point of 156°F and an API gravity of 37.6, resulting in a diesel index of 59.9.
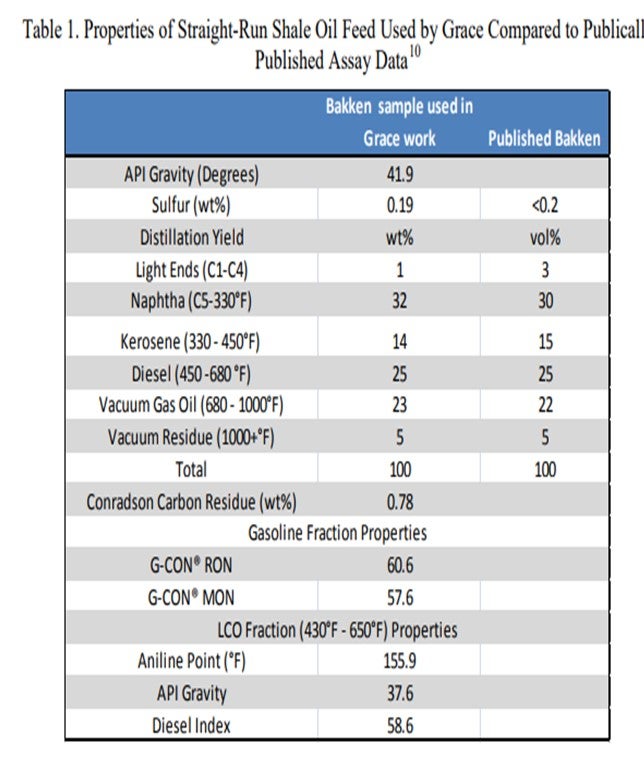
The catalyst used in the experiments was a high matrix FCC catalyst, deactivated metalsfree using a CPS (cyclic propylene steaming)-type protocol. The properties of the deactivated catalyst are given in Table 2. For the three different reactor outlet temperatures, plots of the catalyst-to-oil (C/O) ratio, dry gas, gasoline, LCO, bottoms, and coke yields versus conversion are shown in Figure 1. As expected, lowering reactor temperature increases the amount of LCO produced. As seen in the graphs, cracking straight-run shale oil produces little coke and bottoms. At the same conversion level, lowering reactor temperature results in slightly more gasoline yield (due to increased C/O), which is consistent with prior Grace work.
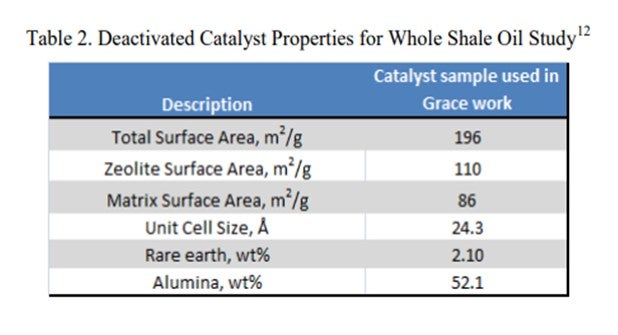
Plots of gasoline olefins, isoparaffins and RON and MON estimated via G-Con software are shown in Figure 2. Cracking straight-run Bakken shale oil produces a low-quality gasoline with research octane less than 80 and motor octane less than 70.
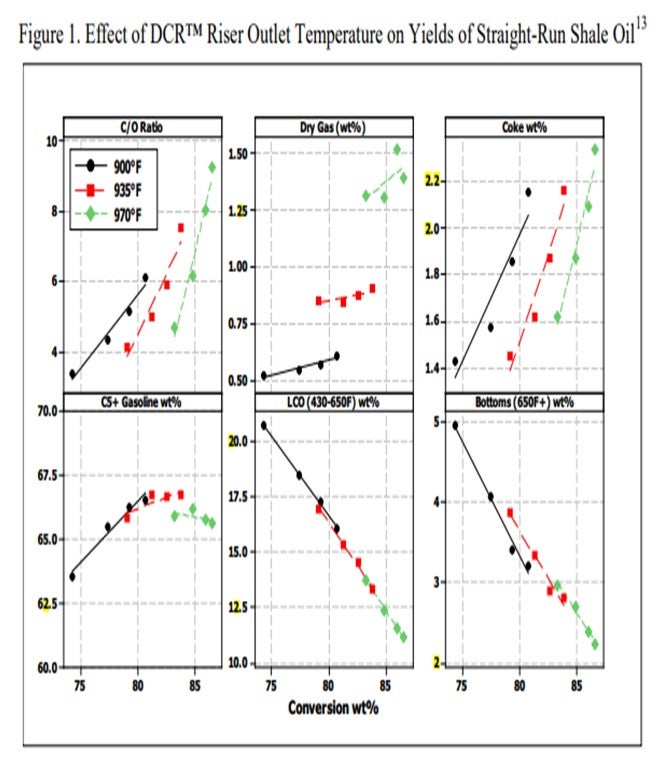
At constant conversion, increasing reactor temperature results in more gasoline olefins and higher research octane number. Diesel quality is of great interest to refiners. Syncrude produced in the DCR™ runs was distilled to recover the 430°F to 650°F LCO fraction. Aniline point and API gravity of the LCO were then measured to allow calculation of the diesel index, a measure of LCO quality [Diesel Index = (aniline point x API Gravity)/100]. Figure 3 presents data for LCO yield and LCO quality as a function of conversion. As seen in the data, increasing conversion lowers LCO quality as a result of increased cracking of the LCO range paraffins to lighter hydrocarbons. Similar to prior Grace work14, LCO quality follows LCO yield and did not appear to be influenced by reactor temperature at constant conversion. Diesel index values of the LCO produced by cracking whole shale oil were significantly higher than values obtained with typical VGO feeds.
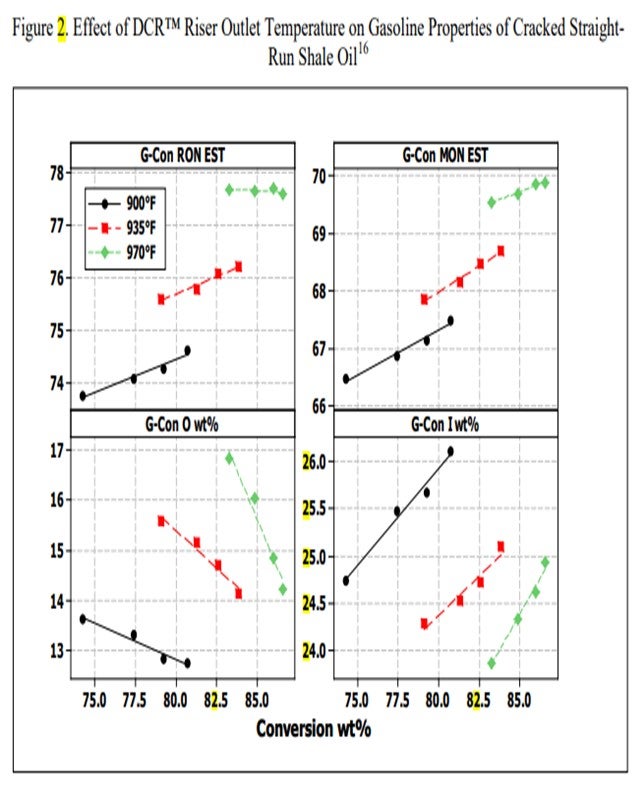
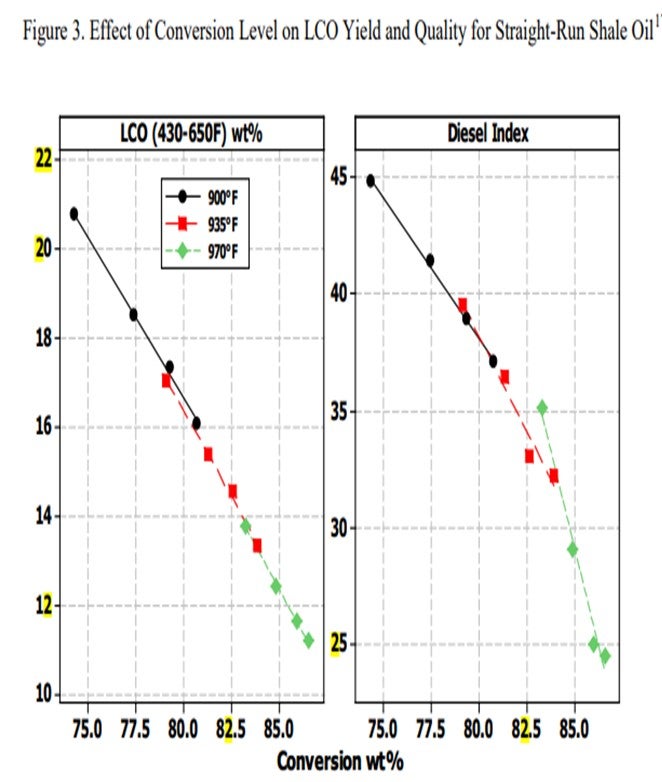
As seen in the results from this study, widely varying ratios of products and product quality can be obtained by changing process conditions. Information from pilot studies such as this one helps refiners to determine the optimum processing setup to maximize yields of desired products. The ability of the DCR to produce sufficient liquid product for properties testing assisted greatly in the measurement of LCO quality.
In addition to yields and operating conditions, contaminants and the impact they have on circulating catalyst inventory should be taken into consideration. A catalyst flushing strategy may be required to ensure that contaminants stay at reasonable levels in circulating inventory. For example, one refiner experienced high levels of sodium on e-cat while processing high amounts of whole crude. The sodium more than doubled and catalyst activity dropped more than 10 numbers, both of which impacted unit performance (Figure 3). The unit utilized purchased e-cat to help flush the sodium from circulating inventory.
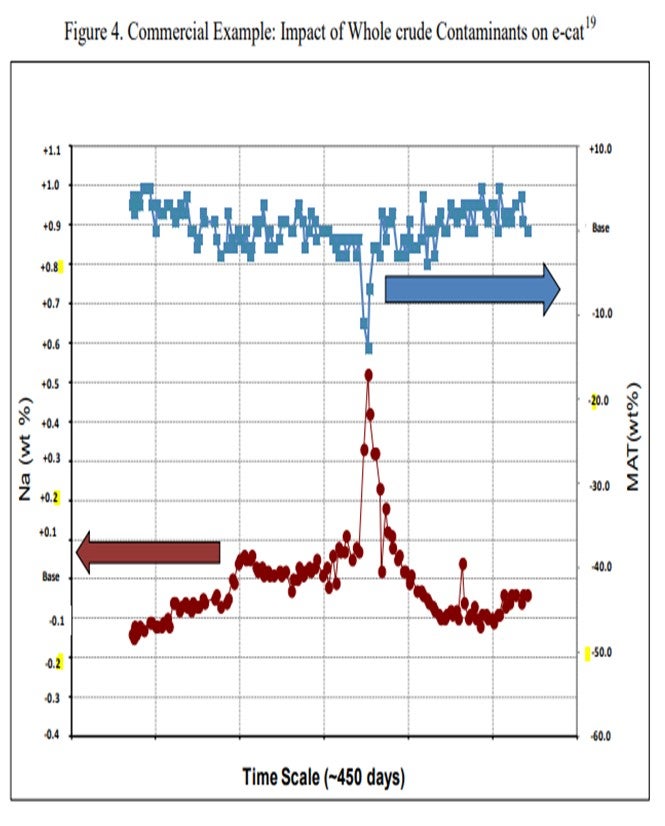
PAUL FEARNSIDE (Nalco Champion Energy Services)
The largest concern will be with the main fractionator performance. Issues with direct cracking of undesalted crudes revolve around the increased chloride loading and the resultant increase potential for ammonium chloride salting. Care must be taken to insure the upper section delta P does not increase to the point that daily operations are curtailed. Intermittent slumping of the tower while water-washing and the use of salt dispersant chemistries have worked well.
CHRIS CLAESEN (Nalco Champion Energy Services)
The increased metals content in the feed can lead to increased catalyst deactivation, coke formation, and hydrogen generation which can significantly reduce the FCC profitability. While the metals content should be kept as low as possible by pre-treatment in the tank farm and desalters, the effect of Ni and V can be significantly reduced with the use of a metal passivator program that is injected in the FCC feed.