Question 92: Describe the turnaround scope of work for the combustion air blower. Does it differ for units with turbo expanders? Do you work on the air blower every turnaround? Is this work performed by a general turnaround contractor or by the manufacturer? How often does this work become critical path?
SCHOEPE (Phillips 66)
Most sites replace the internals of the expander during every turnaround. The stator veins are thoroughly inspected and replaced on as-needed basis.
In terms of the main air blower, it depends. Some sites replace all of the internals every turnaround, while other sites are managing to push the air blower overhaul to every two turnaround cycles.
Work is usually done by a qualified contractor or OEM (original equipment manufacturing) consultant. Usually, one of those people is onsite to supervise the overhaul work. It is critical to have a full set of spares onsite before you start your turnaround so that this type of work does not become critical path. Typically, critical path is set by the work that is being done in your catalyst section.
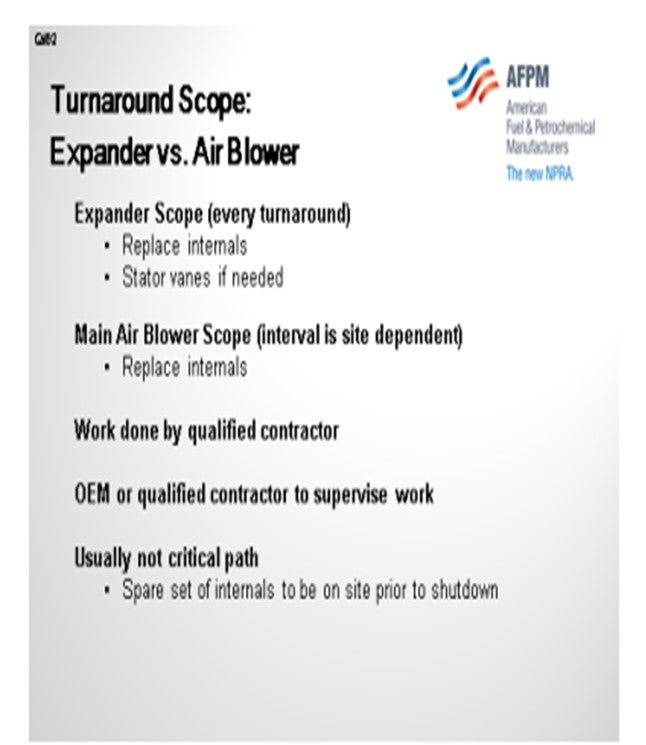
PIMENTEL (CITGO Petroleum Corporation)
I agree with Christian. In our experience, the air blower work is never on the critical path of the turnaround. In one of our refineries, we do complete overhauls every third cycle. By that time, we have already have lost our 10% efficiency in the air blower. This type of work is performed in a specialized shop outside of the refinery; and then again, it is hardly ever part of the critical path. In another refinery, we have multiple air blowers and interconnecting airlines between the FCCs, so the turnaround work is mostly limited to instrumentation, correction, changing vibration probes, testing trips, and cleaning the lube oil system. This work is performed by general turnaround contractors and, again, is not part of the critical path.
BROOKS (BP Refining)
Our response is similar to Sergio’s and Christian’s in that we have some units which overhaul this equipment every turnaround. Some pull the blower, send it out to fix everything, and replace the rotors. We have many other sites that only do it every other turnaround. We do not really have a lot that do it every third turnaround, but we do have quite a few that perform a full overhaul every other turnaround. On the off years when we are not doing a full overhaul, we will conduct similar types of inspections and basic repairs around the lube oil system. The bearing inspections, turbine and motor inspections, and testing of your safety system are essentially exactly what Sergio said. Basically, most of the work we do is driven by each site’s individual experience with their air blowers. So if their air blower has particularly poor reliability, they will tend to do more work on it. Others that have fairly reliable or redundant air blowers do not do a full overhaul every time. But for us, it rarely becomes critical path.
SCHOEPE (Phillips 66)
Expander Turnaround: All Phillips 66 units replace the internals during each turnaround. The stator vanes are being inspected and are replaced if needed.
Main Air Blower Turnaround: Depending on the reliability of the equipment, some sites service the main air blower every turnaround while others are able to service the blower every second turnaround. When serviced, the internals are replaced with spares.
If expander and main air blower are serviced, it is typical that one qualified contractor does this work. Supervision of this work is usually done by the original equipment manufacturer or a qualified third-party contractor.
To prevent this work form becoming critical path, a full set of equipment internals is usually available prior to shutdown. The critical path is usually set by the work scope in the catalyst section and not by rotating equipment maintenance.
PIMENTEL (CITGO Petroleum Corporation)
We do complete air blower overhauls every second or third turnaround, but we have found that significant capacity losses of 7% to 10%, depending on total years of operation in the blower run, occur by doing overhauls every third turnaround. This is true for an axial compressor on one FCC and a centrifugal compressor on another FCC. Work is performed in the shop of a specialized rotating equipment vendor. The presence of an expander on one of our FCCs does not alter the scope of work for the air blower.
In another refinery, we have multiple air blowers in every FCC; in addition, there is a combustion air header interconnecting all the units. Therefore, the turnaround scope for the air blowers is limited to small corrections such as changing vibration or temperature probes, cables, cleaning the lube oil system and testing trips and throttle valves. This type of job is done by the general turnaround contractors and is never part of the turnaround critical path.
BROOKS (BP Refining)
All our sites do some work on the main air blower during turnaround outages. The scope of work is slightly different per site. Some sites will do a full air blower overhaul on every turnaround because they have had significant reliability issues. Other sites focus on a list of basic repairs and inspections for each turnaround with full overhauls planned every other turnaround (typically eight- to 10-year cycles). This work scope typically includes:
• Lube oil system maintenance and flushing,
• Bearing inspections,
• Turbine and motor inspections, and
• Throttle valve trip and testing.
The scope of work on the main air blower at our sites is typically driven by each sites’ main reliability issues with the air blower. For us, this work rarely becomes critical path.