Question 91: What FCC turnaround intervals are refiners achieving for units that do not take mini turnarounds? Do longer intervals mean lower reliability between turnarounds?
BROOKS (BP Refining)
Most of BP’s units are now transitioning from about a four-year turnaround cycle to a five-year. We have some units already running five years between turnaround cycles without necessarily showing evidence of higher wear and tear. We do not typically need to perform any mini-turnarounds or swoop-downs unless there are some extraordinary circumstances where we know equipment is broken and have to go in for repairs. Our unit reliability has been very high, so that is not really a concern for us when switching from a four-year to a five-year cycle.
We have done some internal Availability Improvement Studies and identified turnaround duration as a significant focus. Some of our turnarounds get a little long. It does not seem to correlate directly with our units that have longer time between turnarounds though, so I would not necessarily relate those together. We have quite a few units that are 100% hydrotreated feed, and a number of others that run untreated gas oil and resid. Both of those types of units have been able to do five-year runs. We have not seen any correlation between feed types and any issues with longer runs.
Right now, we actually have one unit that is planned for a five-year turnaround run. This unit is pushing its turnaround out another six to 12 months by doing a very, very small swoop-down or mini-turnarounds to make very minor corrections. The units have not had any other significant operational or reliability issues. Obviously, as you increase the length between turnaround cycles, you do have an increased risk of unplanned outages and slowdowns, especially near the end-of-run. A typical area of concern when you push your turnaround cycle out is having a very large turnaround scope. As I mentioned, worn cyclones causing catalyst loss increases, gas plant reboilers and exchanger fouling, feed nozzle erosion, flue gas system fines deposition, air grid erosion, and transfer line coking are among numerous items that can become concerns when pushing towards longer runs between turnarounds. So, there are obviously risks for pushing your turnaround cycles out. We have looked at some of them, and we feel comfortable moving most of our units to a five-year cycle.
There is an additional consideration that might affect you. Some of our units have mandated inspections on certain pieces of equipment based on local regulations and may require a shorter turnaround cycle. Thus, some might have to do mini-turnarounds or swoop-downs to meet those requirements, or they may have to plan for shorter turnaround cycles.
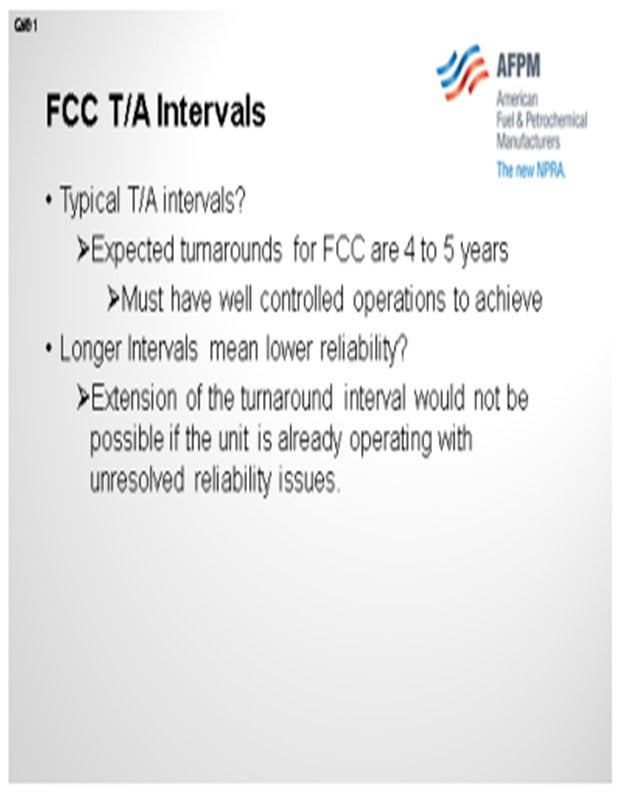
LALL (UOP, A Honeywell Company)
In our experience, most FCCs are achieving four- to five-year runs. There are a number of factors that determine the onstream reliability of the FCC. To say that longer run life equates to less reliability and more unplanned shutdowns is not an automatic conclusion. The key to maintaining onstream reliability is that the important components of the reactor regenerator are controlled during operations, as should be the operating variables during the course of the run.
A health check philosophy is used to identify all of the reactor regenerator’s critical components. A priority table identifies the key design parameters and compares those values to actual operating values seen in service. For items identified as running above design limit, repairs are expected. A plan is then devised such that those high priority items are seen first during the inspection discovery phase. There is then a plan for either a quick repair, a repair with modifications, or complete replacement with upgraded or improved technology.
The other aspect of the health check is the monitoring of erosion, particularly for cyclones. The amount of cyclone or erosion observed is directly proportional to the velocity at which they are operated. Therefore, it is fairly easy to predict the level of expected erosion by reviewing the operating history. While the health check is a great tool for predicting problems, the mini shutdown is a great opportunity for verifying those predictions, as well as discovering any new potential problems.
While the mini-turnaround generally does not allow for any major repairs, it does allow the units to continue operating until proper adjustments and repairs can be made. In general, the mini-turnaround does not improve reliability, but it does give the refiner a chance to redo some quick fixes that were made, perhaps unexpectedly, during the last turnaround. The mini-turnaround also provides a great gauge to establish the amounts of expected repairs.
WILLIAMS (KBR)
At KBR, we also agree that a typical, normal FCC turnaround is around four to five years. But in order to achieve this interval, we believe that it requires well controlled operations. To support what my colleagues stated earlier, to achieve longer turnaround cycles requires operating within the recommended design parameters as far as feed rates, properties, and temperatures, as well as catalyst circulation rates and superficial velocities, to just name a few.
VILAS LONAKADI (Foster Wheeler USA Corporation)
I think Jesse mentioned remaining within the design parameters. Those of you who are having five years, and even beyond five years, are you really operating at design or are you below the design? On what percentage of units can you still achieve five years and longer?
BROOKS (BP Refining)
It depends on which unit we are looking at in our system. We have some units that are running below their design capacities, but we also have some running at or above their design capacities on most days. As Jesse mentioned, these units will target superficial velocities in the regenerators to make sure their cyclones can make run-length. They will focus more on their KPIs if they are pushing their run-length and running near their design limits. We do have some units that make it longer because they run a little bit further below their design limits due to other constraints, not because we do not want to run feed.
BROOKS (BP Refining)
BP is trying to transition most of its units from four-year to five-year cycles. Our five-year turnaround cycle units do not tend to see higher “wear and tear” than our shorter cycle units and “mini-turnarounds” have not been necessary except in special/unusual damage cases. Our unit reliability is typically high. Internal availability improvement studies have identified turnaround duration as a significant focus area for the future, but this does not appear to correlate directly to our units with longer time between turnarounds. While our units running 100% hydrotreated feed typically run on five-year cycles, we have multiple units running resid who also successfully operate on a five-year turnaround cycle plan. One of our units recently planned for a five-year turnaround cycle and is pushing their maintenance turnaround out another six to 12 months by doing a brief “swoop-down” for minor repairs. Thus, allowing them to take advantage of favorable market conditions forecasted. With this swoop-down, the unit will meet a six-year cycle on this run.
A previously owned BP unit ran a seven-year cycle with no mini-turnarounds in the middle. While this was certainly impressive, notes suggest that the final turnaround scope after this run was extremely large and required significantly more manpower than typical turnarounds.
Increasing the time between turnarounds can certainly increase the risk of unplanned outages and slowdowns, especially near end of run. Typical areas for concern when considering longer turnaround cycles include: large turnaround scope, cyclone wear and resulting increases in catalyst losses, gas plant reboiler and exchanger fouling, feed nozzle erosion, fines deposition in the flue gas system, air grid erosion, and transfer line coking. Some site equipment can also be affected by mandated inspections that may fall within a longer turnaround cycle window (less than five-year cycle).
WILLIAMS (KBR)
A normal FCC turnaround interval is approximately five years and requires a well-controlled operation to achieve this interval. The unit needs to be operated within its design parameters (feed rate, feed properties, temperatures, pressures, catalyst circulation and superficial vapor velocities among others) to avoid afterburning and thermal damage to cyclones and excessive erosion of the air distributor and other key internal equipment. Extension of the turnaround interval would not be possible if the unit is already operating with unresolved reliability issues.
LALL (UOP, A Honeywell Company)
There are a number of factors that determine the onstream reliability of the FCC; to say that longer run life equates to less reliability (i.e., unplanned shutdowns) is not an automatic conclusion.
The key to maintaining onstream reliability is that the key components of the reactor-regenerator are monitored during operation, as well as controlled as should be the operating variables during the course of the run.
The health check philosophy is an engineering-based tool used to identify all of the critical components of the reactor-regenerator by a priority table that identifies the key design parameters for the given equipment and compares those values to the actual operating values seen during operation. These variables are typically capacity (flux/volume), flow (velocity), temperature and pressure. For those items identified as running "above" design limit, repairs are expected, and a plan is devised such that those "high priority" items are seen first during the inspection discovery phase of the turnaround and there is a plan for either a quick repair (replacement in-kind), alternate repair with modifications, or complete replacement with upgraded or improved technology. The more items that are identified and pinpointed during this health check process, the more planning can go into the turnaround to minimize unknowns during the turnaround. Several refineries have adopted a policy of planned replacement during shutdowns, so that in-situ repairs are avoided. Ideally, these refineries localize and rotate the majority of maintenance for a given unit so that they do not overload the manpower requirements for any one turnaround. For example, the refiner would do reactor work (and cyclones) for the unit one turnaround, with regenerator work (and cyclones) the following turnaround, and with work on the flue gas in the subsequent turnaround.
The other aspect of the health check is the maintenance of erosion - particularly for cyclones. The amount of cyclone erosion observed is directly proportional to the velocity at which they are operated. Therefore, it is fairly easy to predict the level of expected erosion by reviewing the operating history and estimating the level of expected erosion. The same holds true for standpipes and risers. The key is to map the known critical areas and determine the severity of service it has experienced between campaigns (run-lengths) to gauge the level of expected repairs. The health check is also a good tool for judging the impact of "pushing" the unit beyond design limits, or running the unit with a severe/contaminated feed. Additionally, the effect of excessive turndown can also be predicted and planned for. The success of the turnaround planning is the coupling of the current process conditions with the known mechanical problem areas and developing a plan to eliminate the root cause of any problem, avoiding re-occurring maintenance and inspection headaches.
The onstream health check mainly comprises conducting thorough and comprehensive thermographic reading of the entire unit to identify and isolate areas of refractory problems. This primarily relates to the cold wall vessels and standpipes. For hot wall standpipes and vessels, onstream thickness readings are used to establish erosion tendencies and potential corrosion area.
While the health check is a great tool for predicting problems, the mini shutdown is a great opportunity to verify those predictions, as well as discover any new potential problems. While the “mini-turnaround” (or “pit-stop”) generally does not allow any major repairs, it does allow the unit to continue to operate until the proper adjustments and repairs can take place. In general, the mini turnaround does not improve reliability, it just gives the refiner a chance to "re-do" some quick fixes that were made (unexpectedly) during the last turnaround and gives the refiner a great gauge to establish the number of expected repairs. Having the unit well mapped with a priority assigned to critical areas for inspection is key during the mini turnaround. Generally, the complete unit is not available during this time, so the inspection areas must be prioritized and planned such that the critical areas are inspected. In general, it is always good practice to have a "hit list" ready for potential inspection in the event the unit comes down for any reason during an unplanned outage (major power failure, refinery fire, feed outage, etc.). One of the most difficult predictions to make is the remaining life of equipment, so any opportunities to reduce time between turnarounds helps in the planning phase. For example, if it is known that cyclones are eroding, it is easier to judge if they can last two years until a mini-shutdown, versus having to determine if they can last four or five years until the next planned outage.
SUBHASH SINGHAL (Kuwait National Petroleum Company)
Typically, three years between turnarounds without mini shutdown is achievable. Many refiners achieve four years with mini-turnaround. If a refiner intends to achieve four years between turnaround without mini-turnaround in between, he may have reliability issues. There has been enhanced focus on improved maintenance and inspection during turnaround for better reliability.
KEVIN PROOPS (Solomon Associates LLC)
We examined worldwide FCC turnaround data from 2008 to 2010, collected in our 2010 Fuels Study. New study entrants without enough historical availability data were eliminated, leaving 162 turnarounds. We saw turnaround intervals from two to almost nine years, with a median of 4.5 years. Extending interval will increase duration, as shown in Figure 8. The best performers achieve fewer than seven annualized days down, regardless of interval. For these best performers, interval does not significantly impact the turnaround contribution to availability in our metrics. Feedstock impacts turnaround interval: RFCC units with feed above 3 wt % Conradson carbon are achieving two- to 5.5-year intervals.
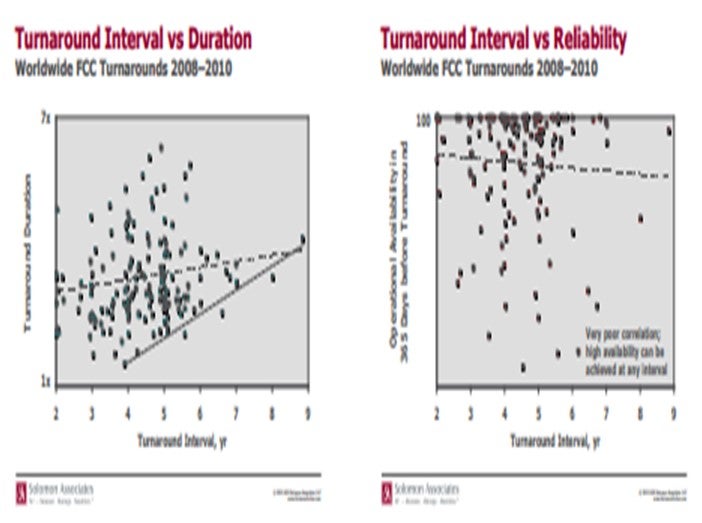
HARVEY MCQUISTON (Technip Stone & Webster)
Technip Stone & Webster provided design for a major FCC revamp in a 33-day revamp turnaround. Large increases in gasoline yield obtained at the expense of slurry were seen after the modifications. After six and a half years, the cat cracker completed a very profitable run with minimal problems and was brought down for a regularly scheduled maintenance turnaround in which minor refractory repairs were performed. Upon completion of the maintenance turnaround the unit was once again producing the same yield structure seen after the unit revamp. Another very successful run is anticipated. Please refer to the paper AM-11-37 given at the 2011 Annual Meeting.