Question 91: What FCC operating variables can be used to control the formation of acetone? What typical acetone concentrations are observed?
GIM (Technip Stone & Webster)
First of all, acetone is hard to detect by itself. It requires a special column in GC (gas chromatography) to pick up the polar species. Normal GC just picks up the regular hydrocarbons. We have seen acetone concentration in the C4 stream, butane and butylene (or BB, to be specific) as high as 800 ppm. In the same unit, we also measured average acetone concentration of 300 ppm over the course of the same month with values as low as 50 ppm. So, what are these sources of acetone? Oxygenates are byproducts of entrained oxygen in the regenerator and hydrocarbons in the reactor. Entrained oxygen from the regenerator to the reaction zone provides an opportunity for acetone formation in the reactor. Excess oxygen in the regenerator standpipe increases with higher catalyst circulation rate. High catalyst circulation rate entrains more air from the regenerator because the entrainments are among the catalyst particles.
Now, what are some of the potential ways to reduce this acetone formation? A few solutions for preventing acid formations are as follow:
1. Replace the instrument air in the reaction taps from air to nitrogen.
2. Tweak the operating variables may lead to some unnecessary increase in catalyst circulation rates such lowering the ROT (reactor outlet temperature), raise feed preheat, or use a higher activity and lower catalyst cooler duty, if you have them. Many of these will decrease the cat circulation rate and, therefore, the formation of the acetone.
3. Properly design the C3/C4 contaminant removal bed to help remove this acetone as well. Keep in mind that there may be other sources of oxygenates that had been introduced into the FCC system, such as external oxygenates or oxygenates that are being recycled, as well as some of the oxygenate-containing sludge in pipings.
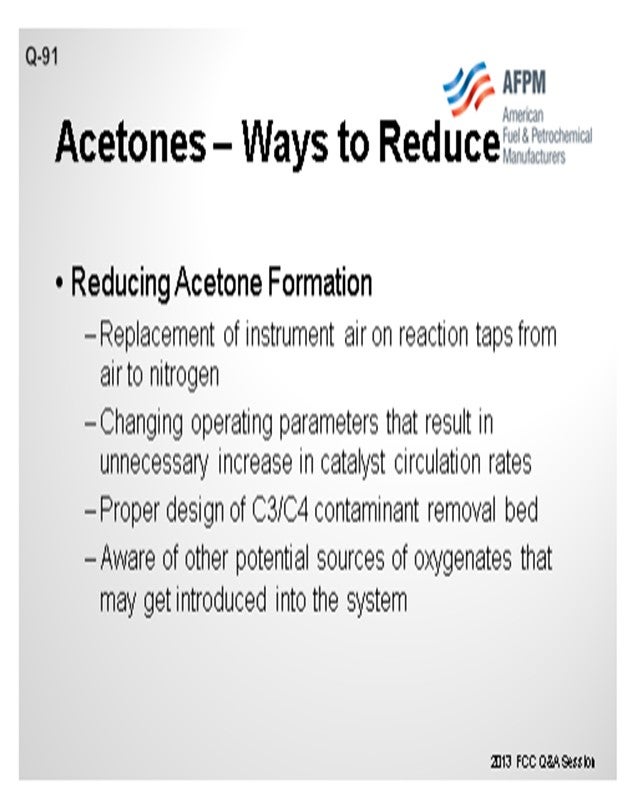
BULL (Valero Energy Corporation)
We have seen levels of 50 to 200 ppm acetone in the BB stream in our refineries. Now for refiners in general, a move from 50 to 200 ppm is normally not that large; but if you are selling the stream as a chemical feedstock, the difference between the 50 and the 200 ppm can be significant on the downstream plants. That is definitely a consideration. Another concern about acetone in the feed to the alkylation unit is that it does result in higher acid consumption and can increase the ASO (acid-soluble oils) formation; but in low levels, this can normally be managed.
MICHAEL WARDINSKY (Phillips 66)
This question came up in 2007 when I was on the panel, and I remember answering it. You might want to consider making sure you have a good washwater rate going to your main frac overhead system because acetone should partition out to the sour water system when contacted with washwater.
MARTIN EVANS (Johnson Matthey INTERCAT, Inc.)
A question for Steve: You mentioned the use of contaminant removal beds to remove acetone. What type of beds are you suggesting?
GIM (Technip Stone & Webster)
We are talking about the activated alumina adsorbent bed.
STEVE GIM (Technip Stone & Webster)
Measuring Acetone: First, acetone is hard to detect by itself. It requires a special column in GC to pick up the polar species such as acetone, other oxygenates, and ECL. Normal GC just picks up regular hydrocarbons. We have seen acetone concentration in the C4 stream (butanes/butylenes or BB) as high as 800 ppm, but the same unit also measured acetone concentration averaged 300 ppm in daily measurements over the course of the same month, with values as low as 50ppm.
Source of Acetone: Oxygenates are byproducts of entrained oxygen and hydrocarbons. Entrained oxygen from regenerator to the reaction zone provides an opportunity for acetone formation in the reactor. O2 in the regenerated catalyst standpipe increases with higher catalyst circulation rate; higher catalyst circulation entrains more air from the regenerator because most of the entrainments are among the catalyst particles.
Reducing Acetone Formation: Some of the solutions for acetone are:
(1) replacement of instrument air on reaction taps from air to nitrogen.
(2) tweaking of operating variables that may result in an unnecessary increase in catalyst circulation rates such as lower ROT, higher feed pre-heat, higher catalyst activity, and lower catalyst duty; and,
(3) properly designing C3/C4 contaminant removal bed (such as activated alumina adsorbents).
It is also important be keep aware of potential other sources [of?] oxygenates that get introduced to the system including external oxygenates, oxygenates that are being recycled, and oxygenate containing sludge in pipings.
JEFFREY BULL (Valero Energy Corporation)
Ketone formation in the FCC is heavily dependent on the amount of air entrained from the regenerator into the reactor through the regenerated catalyst. As catalyst circulation is increased, more air is entrained and the formation of ketones will increase; so any operating variable that raises catalyst circulation can contribute to the formation of acetone. Specifically, reactor temperature, catalyst formulation, and stripping steam all have a strong correlation to catalyst circulation. Valero does not have much data on concentrations of acetone in the LPG product, but we have seen it in the 50 to 200 ppm range. We had a recent experience with not being able to sell some of our LPG product due to high acetone numbers. For refiners, the change in acetone formation from 50 to 200 ppm usually will have no effect on product quality. However, if the LPG is being sold as a chemical feedstock, this shift in concentration can adversely affect the downstream chemical plant. Acetone in the feed to the alkylation unit does result in higher acid consumption and increased acid soluble oil (ASO) formation; but in low levels, this can be managed. I will also refer you to the 2007 NPRA FCC Q&A response to Question 14 for further information on this topic.
JACK WILCOX (Albemarle Corporation)
Oxygen entrained in the circulating catalyst resulting from excessive instrument and standpipe aeration using air as a source, as well as excessive excess combustion air for catalyst regeneration, can provide the oxygen necessary for the generation of acetone. Instrument tap and standpipe aeration air rates should be properly controlled by utilizing appropriately sized restriction orifices in these locations. If possible, the aeration media should be changed to sweet fuel gas or nitrogen. Excess flue gas oxygen levels should be optimized to maintain the desired level of carbon on regenerated catalyst and carbon monoxide in the flue gas. Acetone is formed from the reaction between propylene and benzene plus oxygen. Avoid, if possible, charging extraneous streams to the vapor recovery unit containing cumene which reacts with oxygen to form acetone. High FCC reactor temperature will produce more propylene and benzene, the combination of which can react to produce cumene. The use of ZSM-5 additive will obviously produce higher levels of propylene as well. Units operating at elevated cracking temperatures to maximize light olefin will see acetone levels in the debutanizer overhead C3 + C4 stream as high as 1500 ppm. Acetone levels in the range of about 100 to about 1200 ppm have been observed in the C4 fraction.