Question 87: The operation of a resid FCC can be challenging as more of its feed is hydrotreated to meet ULSG and ULSD specifications. What changes can be made to improve its operation?
LARSON (KBC Advanced Technologies, Inc.)
For the purpose of this answer, we will look at this as a resid cat cracker that would have a catalyst cooler or be in a two-stage operation. Any increase in feed hydrotreating which increases the portion of hydrotreated feed, or an increase in hydrotreating severity, will obviously improve the feed quality. The slide shows a representative material of a gas oil plus resid and then what it might look like on the basis of a hydrotreated feed. You will notice that by using Watson K or refractive indices, the quality of the feed improves quite substantially. We see that the Concarbon (Conradson carbon) is dropping quite significantly. In those cases, you will have a substantially different coke balance in the unit, and you will see the regenerator fall.
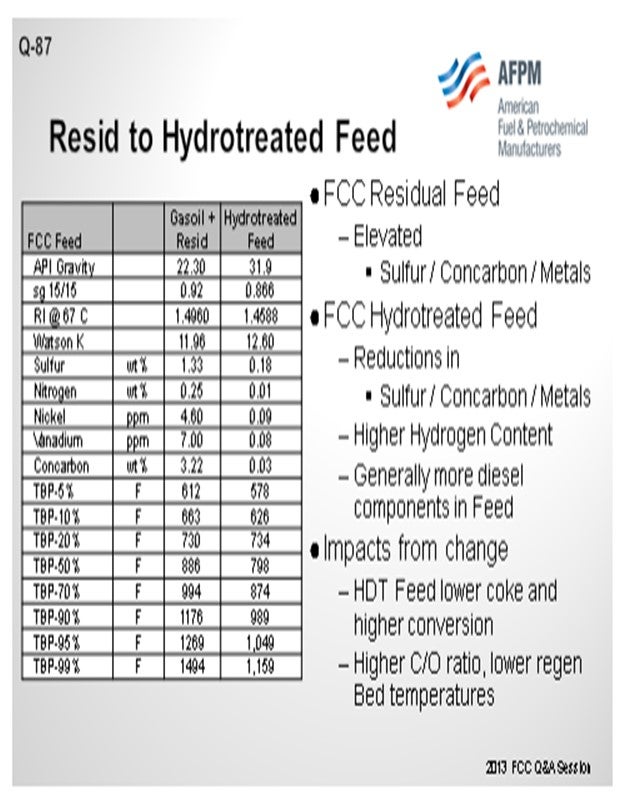
So, what are some of the conditions that you might evaluate to change the operation? One condition is that you will see a much higher cat-to-oil in the unit. Operationally, catalyst circulation itself will go up. The slide valve may need to be increased further. So, then what will be the counter-condition you will need to examine? Can you circulate the catalyst rate that is needed to operate? If you have a two-stage system and a cat cooler, can you keep the cat cooler in operation? Do you just turn it off completely?
Make sure you can get as much trapped diesel out of the unit as possible; because if you distill it in, even if it is only 10%, it will be acting like another cat cooler. With regard to catalyst change, we have a lot of catalyst vendors here. That may be one of the first product you examine in order to maintain the heat balance. You might also consider adding carbon. If you have hydrotreated feed, you can add carbon through the HCO recycle overflash, provided you can maintain the sulfur specifications on your products. You also need to consider the pressure balance to keep the unit operating within targeted range.
In a step change on the existing unit, if you are far enough away from turnaround, you might have to take actions that you would not do in an optimized situation, like reducing the actual steam to the feed nozzle to reduce mixing to allow the addition of carbon. Because it is a situation that exists now and has to be lived with it until the next shutdown, we have clients who have actually pulled steam out of the stripper and let hydrocarbon slip into the regenerator to keep up the profile, which allows them to run the unit. These are non-ideal situations and are done in lieu of mechanical adjustments so you can stay online. Before doing any of the above recommendations, you should consider first a catalyst change.
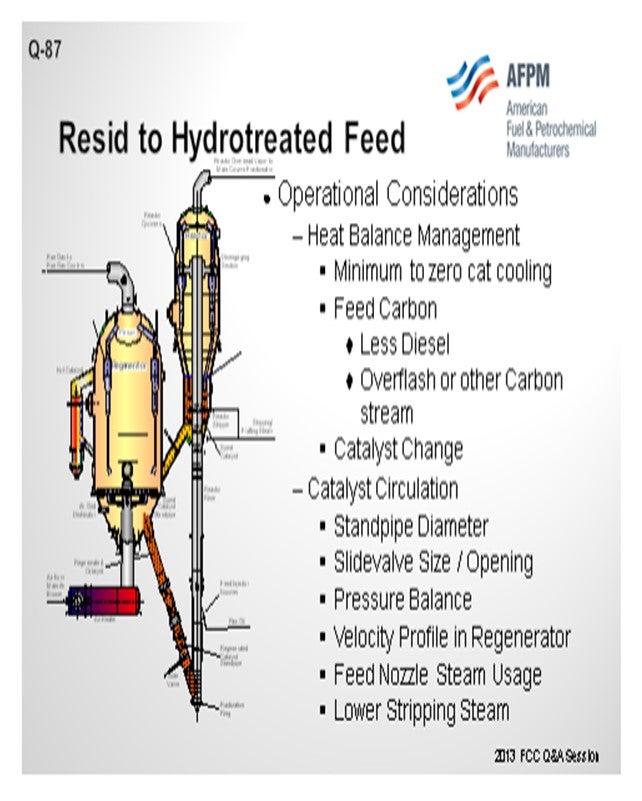
KOEBEL (Grace Catalysts Technologies)
I want to add one comment about hydrotreated resid. I made a quick query of Grace’s worldwide catalyst database and found some examples of people running hydrotreated resid or partially hydrotreated resid. There were still very, very high levels of metals: much higher than you would consider for a traditional hydrotreated feed operation. Certainly, from a catalyst standpoint, a unit running some hydrotreated resid and a portion of actual resid can still have very high metals; so, you need to make sure you are considering that as part of your solution on the catalyst side as well.
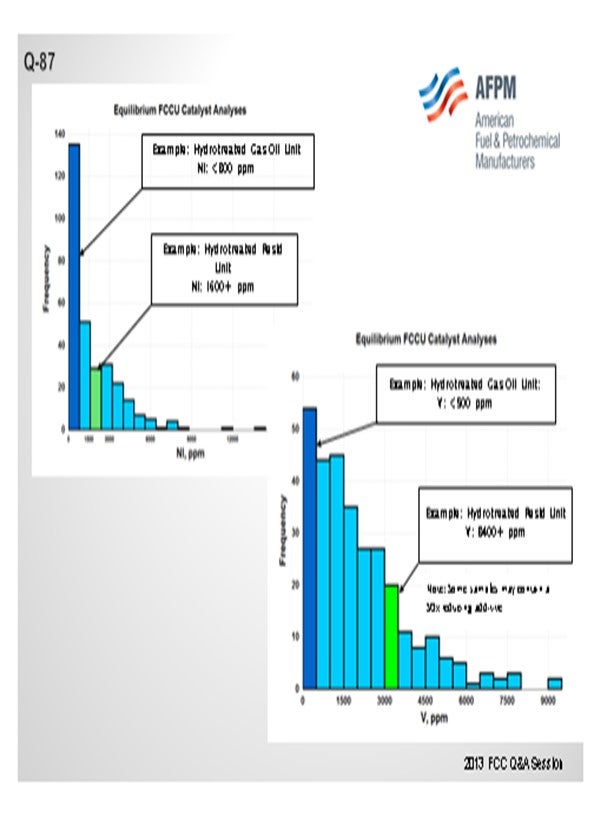
Another phenomenon we see regularly is that the unit running some hydrotreated feed and some resid has a dumbbell-type distribution – a lot of light feed but also some 1300°F plus material – so that type of feed will not behave as if it was blended properly. So, consider the overall distillation of the feed when selecting catalyst as well.
JEFF KOEBEL (Grace Catalysts Technologies)
One catalytic challenge related specifically to resid units that process hydrotreated feed is delivering the proper balance of catalyst activity, metals tolerance, and bottoms cracking. Hydrotreated resid, or a mix of resid and some sort of hydrotreated feed, can still contain a significant amount of contaminant metals. One example of a unit processing hydrotreated resid has in excess of 1600 ppm Ni and 3500 ppm V on e-cat, which is much higher than traditional hydrotreated gas oil operations (Figure 1 and Figure 2). With this level of metals contamination, it is important that the catalyst have proper metals tolerance, which one does not normally think of when considering a hydrotreated feed. Having the proper balance of zeolite and matrix activity is also critical to achieve an optimal level of bottoms conversion. In instances where the feed is a mixture of hydrotreated and untreated resid, the resulting feed blend will not behave at all like a feed with its blended API and K factor. Therefore, the capability to optimize the zeolite and matrix balance in the FCC catalyst becomes even more critical.
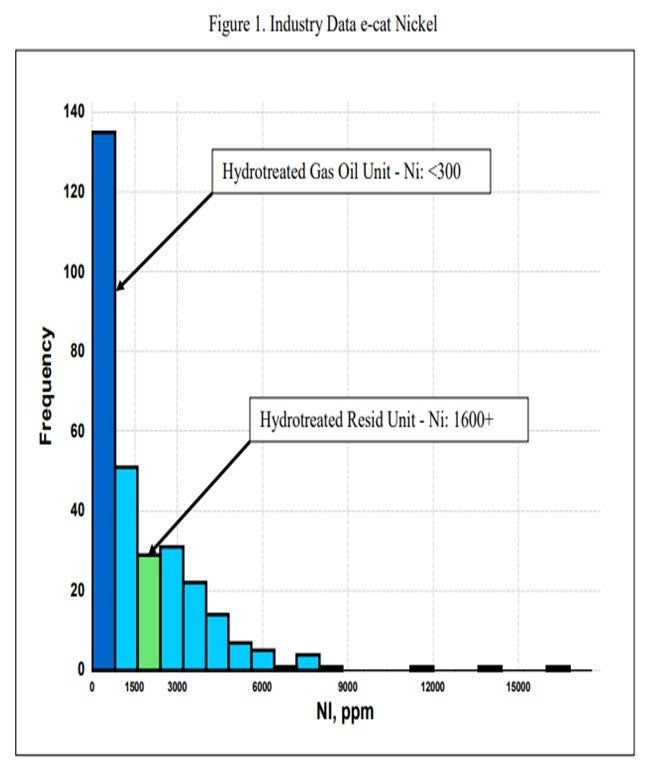
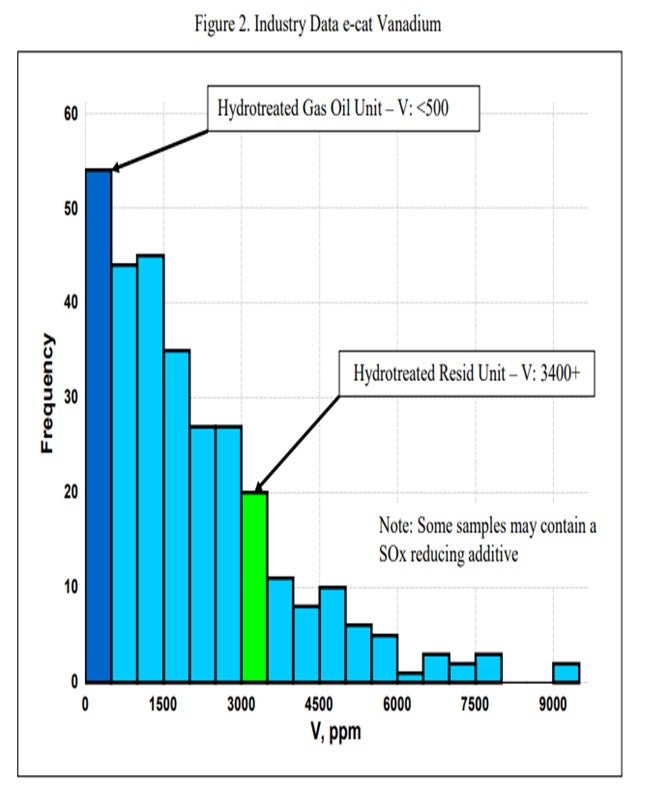
MEL LARSON (KBC Advanced Technologies, Inc.)
For the purposes of this answer, the designation of resid FCC will be defined by those units with either a catalyst cooler or a two-stage operation. Any increase in feed hydrotreating (either increased hydrotreater severity or an increased portion of the feed being hydrotreated) will improve the feed quality resulting in a lower regenerator temperature. Resid cat crackers, which are designed to burn large amounts of coke, often have problems maintaining sufficiently high regenerator temperature with treated feeds.
When the coking tendency of the feed drops or lowers dramatically, it is a good time to review the crude and vacuum unit operations and any post-hydrotreating fractionation to ensure that the diesel content of the FCC feed is reduced as much as possible since light boiling feed will reduce regenerator temperature. We have found several instances where a minor revamp of the vacuum unit allowed an increase in the vacuum gas oil cutpoint by up to 90°F (or more). This results in more and heavier charges to the FCC, which will increase regenerator temperature.
The normal considerations with lower regenerator temperatures are catalyst circulation issues and regenerator combustion profiles and carbon removal from the catalyst that are very different than the design basis. Therefore, the objective is how to maintain regenerator temperatures that keep the unit within reasonable operating parameters. Operational changes are defined as follows:
• Minimize heat removal via catalyst coolers or quench systems as much as possible. Longer term and depending upon the situation, eliminating regenerator heat removal system could be considered.
• With two-stage regeneration systems, minimize air rate and coke burning in the first stage and shift it to the second stage so a greater percentage of the coke is burned in the total combustion mode. For single-stage regenerators with cat coolers, move toward total combustion with minimum excess oxygen in the flue gas if the unit is in partial combustion.
• Consider a catalyst change. RFCC (resid FCC) units typically use catalyst with low coke selectivity to help minimize regenerator temperatures. Whenever a significant change in feed quality is anticipated, a catalyst evaluation should be conducted to assure that the best catalyst for the new operation is selected. Moving from a low coke-selective catalyst to a high coke-selective catalyst can add 30°C to 50°C to the regenerator temperature.
• Add slurry recycle to the riser.
• Lower stripping steam.
• Lower dispersion steam.
• And lastly, introducing torch oil (in the extreme case) can be considered. The addition of an external fuel source directly to the regenerator (torch oil) has a deleterious effect on the FCC catalyst.
Lower coke yield or lower regenerator temperatures can be an especially severe problem for units with two-stage regenerators. With some of these designs, some coke must be burned in partial combustion; so, there may well be insufficient heat available to run the unit on gas oil or severely hydrotreated resids. This really highlights the need to consider feed flexibility when designing new units as changes in relative crude prices, crude availability, or product specifications (especially sulfur content) can make resid cracking unattractive.
Despite the drawbacks of reducing stripping steam mentioned earlier, we have at least two clients who, after exhausting the other options, have found it economical to do this rather than continue to charge resid to the FCC. In one case, this was a temporary solution used until a catalyst reformulation could be put into effect. In the other, it is still used as a trim variable.
Hardware changes to consider accommodating higher catalyst flux rates would include, but not be limited to:
• Elimination of heat removal system on regenerator,
• Review of standpipe and slide valve sizing, and
• Expansion of capacity given that the air blower is less constrained.
Consider post-treat options that allow a more carbonatious feed.