Question 86: What are the advantages and disadvantages of pre-blending FCC additives with FCC catalyst? What is the experience with incorporating FCC additive functionality into the catalyst particles?
KOEBEL (Grace Catalysts Technologies)
Certainly, the obvious advantage of pre-blending additives with your base catalyst is improving your logistics and not handling totes. Another advantage is in not needing an additive loader that you have to maintain. Additionally, pre-blending avoids the possibility of human error in the additive injection process. There are significant drawbacks to doing this as well.

Certainly, if you will be pre-blending additives, the best instance will be when you are using an additive at a constant rate every day. Because if you get into a situation of increasing catalyst additions, you may be over-adding the additives unintentionally and could even get into a bind where you have over-added promoter or ZSM-5.

There are applications for pre-blending additives. Sometimes refiner’s consent decrees call for them to add 10% SOx additive on a daily basis. That was a great example of an application where pre-blending SOx additive worked out very, very well. But certainly, working with your catalyst and additive suppliers will help you come up with what is best for your particular situation.
As far as incorporating additive functionality into the catalyst particles, this is an area where Grace has had a lot of success. In nickel trapping, it is particularly important to have that type of additive functionality. In the catalyst part of this, nickel is not mobile in FCC conditions in the catalyst section; so, you need to trap the nickel where it lands on the FCC catalyst. We have also had good success with our interoperable vanadium trap, which is rare earth based. That trap is depicted in the lower left-hand corner of the slide. The hotspots you see in the picture on the left represent where you find concentrated lanthanum on the surface of the catalyst particle. On the right is the concentrated vanadium. You can see that the two overlap and the vanadium trap is working. We find that having the vanadium trap widely dispersed throughout the catalyst inventory works very well.

We do also have gasoline sulfur reduction technology. That is an additive Grace sells. We do have our SuRCA® family line of FCC catalysts which incorporates that functionality into the catalysts as well. That is one area where people generally tend to use it on a day-in and day-out basis at the same concentration. And where people are long-term gasoline sulfur reduction technology users, we tend to incorporate that functionality into the catalyst.
Finally, Grace recently developed our newly achieved catalyst platform for tight oil and unconventional feeds. One of the comments we sometimes get from refiners is that octane and alkylation of feed stock shortages become an issue. So, in response, we developed the dual zeolite catalyst that will incorporate some isomerization zeolite into the catalyst particle. We find that we can get maximum octane and butylenes for the alkylation unit without the traditional increase in propylene that you would see when using a traditional ZSM-5-based zeolite additive. We have had good success with this product in development, and we are expecting the first commercial trial of it coming really soon.
BULL (Valero Energy Corporation)
As far as pre-blending additives, to reiterate what Jeff said, I will say that if it one being used every day, then add a base amount with the catalyst. What we have done, even when pre-blending, is to always have a loader because we never know more additive might need to be used. Situations do occur that necessitate totally changing the supply chain, taking the additive out of the pre-blend, and then adding it at a different ratio. The only caveat I will add is that even if you are pre-blending, just maintain the facilities so that you will be able to put in the additive.
The second half of the question asks about incorporating FCC additive functionality. We have had extremely positive experiences with trials at various sites, and we are currently using this variety of catalyst at several of them. With reference to metals trapping, we have incorporated that type of additive into the base catalyst for many years; but more recently, we have begun using more of the C4/butylene maximization kinds of additives incorporated into our base catalysts. Again, we have had multiple trials. I cannot really get into all the details of it, but it has been a very big success.

MARTIN EVANS (Johnson Matthey INTERCAT, Inc.)
My experience has been that in North America, most refiners generally tend to keep their additives separate from their fresh catalysts, adding them separately through their own addition systems, as Jeff advocated. I think that pays off. My own experience in this area, from when I was an FCC engineer in the U.K., really taught me that lesson very severely. We had just started using ZSM-5 additives. Because the refinery did not want to pay to put in the addition system, they decided to pre-blend. That worked great until our downstream LPG (liquefied petroleum gas) processing unit broke down. Then at that point, we were left with more LPG than we could handle, and the cost to us – in terms of lost profitability from having to turn down the FCC operation to keep the LPG under control – was a hell of a lot more than it would ever have cost us to put in an addition system. That really taught us a lesson about short-term economics. You think you are gaining something in the short-term by not putting in a loader, but it is a false economy. You definitely end up paying for it long-term.
ROBERT “BOB” LUDOLPH [Shell Global Solutions (US) Inc.]
For your awareness, if you are considering the use of, or have been using, e-cat, pay particular attention to the chemical properties. The presence of certain additives in the e-cat can be indicated like platinum for combustion promoter, phosphorus for ZSM-5, and copper for NOx reduction. Also be aware that the additive activity may be in excess of your need, and you many need to create other operating issues. For example, NOx emissions can take an unexpected step up if the pre-blended combustion promoter activity is too high.
KEN BRUNO (Albemarle Corporation)
Indeed, Best Practices for additive addition are highly influenced by the additive type and any kind of refinery-specific factors. Albemarle offers a full line of not only additive products, but also integrated products with integrated technologies. Again, please consult the Answer Book for a description and our recommendation for when, where, and how to use all these products.
ALEXIS SHACKLEFORD (BASF Corporation)
With regard to the second half of that question about experience with incorporating additive functionality in the catalyst particle, BASF uses a separate particle vanadium trap. It allows the refiner to have additional catalyst flexibility when the vanadium trap is not incorporated with the active catalyst particles.
BART de GRAAF (Johnson Matthey INTERCAT, Inc.)
In the case of metal excursion, we find that it is beneficial to have the possibility of adding additives to mitigate deleterious metal effects. Various base catalysts can contain a built-in metal trap, and there are various additives available which trap metals. When using an additive, you can react quickly to metal excursions when you use, for example, a different type feed. There are advantages of trapping metals on a separate particle instead of keeping them in close proximity to the base catalyst particles containing Y-sieve.
JEFFREY BULL (Valero Energy Corporation)
Pre-blending additives that are used every day for operational controls (combustion promoter), for regulatory/environmental controls (SOx reduction additive), or for yield selectivity changes (ZSM-5) at a base amount is advantageous, because it reduces the complexity of getting those additives in the unit. I would always recommend having facilities be able to add an individual additive in addition to the pre-blended amount in the case of an upset or for a “quick boost”. We have very positive experience with incorporating FCC additive functionality in the catalyst particle. I am not able to relate specific details; but overall, we have had favorable experiences with this type of catalyst. We have completed trials with positive results and are looking to expand to other units.
JEFF KOEBEL (Grace Catalysts Technologies)
Grace has extensive experience with pre-blending and incorporation of FCC additive functionality into the catalyst particle. Specifically in this discussion, we will focus on:
JEFF KOEBEL (Grace Catalysts Technologies)
Grace has extensive experience with pre-blending and incorporation of FCC additive functionality into the catalyst particle. Specifically in this discussion, we will focus on:
• SOx reduction,
• LPG olefins maximization,
• CO promoter,
• Metals traps, and
• Gasoline sulfur reduction.
Pre-blending of separate additives is advantageous when they are used at a fairly constant rate on a continuous basis. This pre-blending eliminates operator action, minimizes the possibility of over- or under-dosing according to plan, reduces the need for additional additive loader equipment, and eliminates the need to handle totes. If the need for the additive is consistent but the usage rate is variable, it is possible to pre-blend additive functionality into the catalyst at a minimum concentration and then supplement with additional dosing as required. A potential scenario for this would be if a refiner is regularly adding a SOx-reducing additive. One may consider pre-blending the minimum amount and supplement with additional dosing via totes to maintain the desired SOx emission level. Finally, purchasing your FCC base catalyst and additives from a single source provides for single-point accountability for your FCC catalyst and additive needs.
If the additive is only used on a spot basis, or if the fresh catalyst addition strategy changes, it is certainly possible to over-add or under-add an additive in a pre-blend setup. Some potential operational concerns are prematurely hitting production limits with ZSM-5 or elevated NOx emissions from overdosing combustion promoter. Either scenario can be managed. We recommend working with your vendor’s technical service representative to optimize your logistics.
Grace has extensive experience with incorporating additive functionality directly into the FCC catalyst particle. We have been extremely successfully in incorporating both nickel and vanadium metals trapping into the catalyst system. In the matter of trapping nickel, it is important to trap the contaminant nickel in the FCC catalyst particle because nickel is not mobile in the catalyst section and needs to be trapped where it is initially cracked on to the catalyst. To do this, Grace utilizes a proprietary alumina that absorbs the nickel into the catalyst particle forming a stable nickel aluminate that is no longer active for dehydrogenation reactions. Grace has been highly successfully in utilizing this technique. Currently, more than 65% of our worldwide customers are taking advantage of this technology.
For vanadium trapping, incorporating a trap on the catalyst system can provide widely dispersed trapping capability to more effectively reduce the negative impacts of the contaminant. Grace’s IVT-4 is an integral rare earth-based vanadium trap that converts contaminant vanadium into an inert rare earth vanadate, greatly reducing zeolite deactivation and coke and gas production. Grace is currently using IVT-4 in 60%+ of our worldwide catalyst formulations.
Gasoline sulfur reduction is another technology that can be readily incorporated into the FCC catalyst particle. Grace’s SURCA® catalyst can be used to reduce gasoline sulfur by 25 to 35% on full-range gasoline. Refiners can utilize this technology to potentially extend FCC feed hydrotreater catalyst life, reduce naphtha hydrotreater severity to preserve octane, or run a higher FCC feed sulfur during FCC feed hydrotreater outages. Typically, these applications require the technology consistently over an extended period, so incorporating this technology into the catalyst formulation is appropriate.
Finally, Grace has recently developed a new catalyst platform for unconventional feeds called ACHIEVE™. A common challenge reported by refiners operating on unconventional feeds, such as shale or tight oil, is a loss of gasoline pool octane, often caused by reduced volume of alkylation feedstock. ACHIEVE™ catalyst can be formulated with multiple zeolites to deliver an optimal balance of LPG-to-gasoline yield and an optimum level of butylenes to keep the alky unit full and maintain refinery pool octane. Incorporation of isomerization activity into the catalyst particle itself results in a more desirable yield pattern than would be realized by use of a traditional octane-boosting FCC additive. An example of the yield shifts possible with this technology is found in Table 1. At constant conversion, ACHIEVE™ delivers higher gasoline octane and higher LPG olefins, with preferentially more butylenes over propylene, providing more total octane barrels for the refinery.
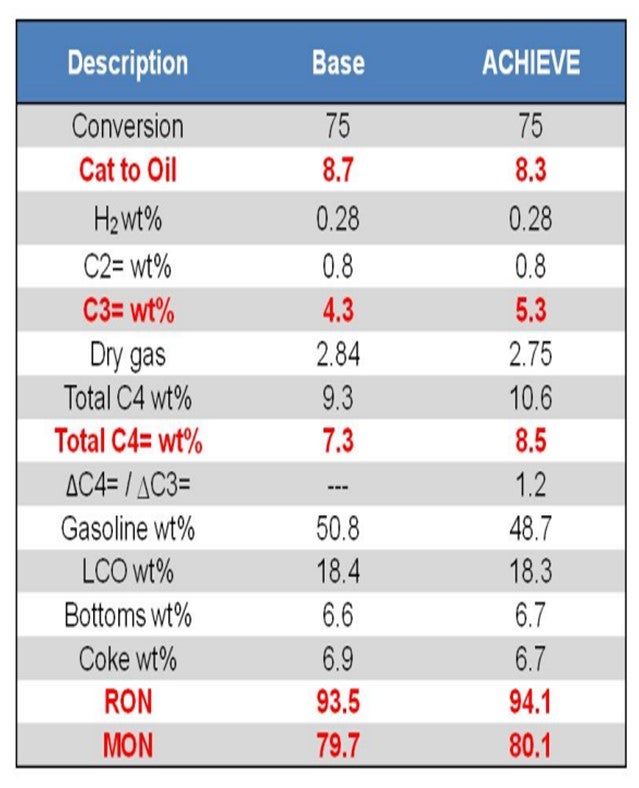
RYAN NICKELL, CAREL POUWELS, and KEN BRUNO (Albemarle Corporation)
Best Practices for additive addition are highly influenced by additive type and refinery specific factors. For environmental applications like SOx control, excursions must be avoided. Separate addition offers flexibility and can also be tailored for feed quality and trouble situations. Pre-blending is utilized in limited cases where a refiner prefers to avoid operating and maintaining a second loader. In these cases, the refiner may also have less strict emissions requirements.
For after-burn control, many refiners prefer to have a separate additive that can be quickly added during emergency situations. If a problem is chronic, pre-blending is a viable and preferable option. Furthermore, chronic problems are well managed by technologies like Albemarle’s InsituPro™ whereby the additive is incorporated into the catalyst particle. In such cases, the active metal is deposited on every single catalyst particle, and optimal distribution in inventory is obtained.
Metal traps capture nickel and vanadium that degrade catalyst performance. The Best Practice with metal traps is direct incorporation into the catalyst. Vanadium species attack zeolite in the regenerator, and incorporation of the metal trap into the attack zone typically works best. Albemarle’s SMR technology incorporates vanadium capture and nickel control directly in the catalyst. Pre-blending is an excellent option when using bottoms upgrading additives like Albemarle’s BCMT™ technology or olefins-octane additives like DuraZOOM™.
Pre-blending simplifies logistics at the refinery and avoids the maintenance and overhead associated with operation of a second loader. Many refiners pleased with BCMT™ performance have ultimately transitioned to a full catalyst solution like UPGRADER™ for maximum bottoms cracking.
While the use of separate additives often offers flexibility to the refiner, in some cases this can lead to suboptimal performance. One salient example is the refiner who believes he can have best of both worlds and simply change between max gasoline and high or max propylene mode by the use of additives. When operating in a high or maximum propylene mode the use of a separate additive, combined with the max gasoline catalyst, will lead to suboptimal propylene yields due to activity dilution and inefficient chemistry. A true max propylene catalyst, like Albemarle’s AFX™, makes use of a proprietary zeolite technology (ADZT-150) with high activity and low hydrogen transfer structured to produce unsurpassed propylene, which never would have been achieved by the aforementioned combination of catalyst and separate additive.
Lastly, for refiners seeking maximum butylenes with minimal gasoline loss, together with octane improvement, Albemarle’s ACTION® catalyst, with its specialized zeolite technology (ADZT-100), is preferred. The use of this specialized zeolite technology optimizes the chemistry and maximizes performance compared with the use of a base catalyst and separate additive.