Question 84: What measures can be taken to reduce the residence time in the FCC main fractionator to offset slurry circuit fouling? What basis is used to determine the residence time in the main fractionator bottoms?
BROOKS (BP Refining)
I would like to start with a little background on bottoms coke to present some clarity on the basis for my answer to this question. Bottoms coke sources could come from multiple places. But to address the question with respect to residence time, our impression was that we are mostly looking at the thermal cracking and decomposition reactions in the main fractionator bottoms as opposed to asphaltene precipitation or reactor transfer line coke generation and carryover.
BP has done a bit of internal research based on a 1988 paper by TOTAL that was presented in an AKZO catalyst seminar. We looked at the pool residence time, pool temperature, and asphaltene content. Based on that paper, we took those three pieces and combined them with some internal data to regress an equation. We then backed out a coking point temperature (based on about 0.45 wt% coke) as our coke formation point. We ended up with a coking point temperature, and that is what BP targets when we watch our main fractionator for bottoms coking. We do not focus as much on the residence time as we do on this coking point temperature. We have noticed that in this equation, when you look at the different variables of temperature, feed paraffinicity, and residence time, feed paraffinicity and temperature have much greater effects in our equation than residence time, which is why we focus on coke point temperature.
For most of our units, we use the same coke point temperature equation and track a certain temperature for the main fractionator bottoms pool. We will try to keep it about 10°F to 30°F below the calculated coke point temperature. That will then be one of our KPIs, or monitoring points, for our bottoms to help prevent coking in that circuit. Basically, to help control this, we focus on removing heat through the pumparound system. Also, 10 of our 11 BPoperated FCCs have an internal slurry quench system, which includes a slurry pumparound distribution ring near the top of the pool and a stripping steam ring near the bottom of the pool to provide extra agitation. Both of those rings will provide cooling and help us maintain the main fractionator bottoms’ pool temperature below the coking point temperature that I mentioned earlier.
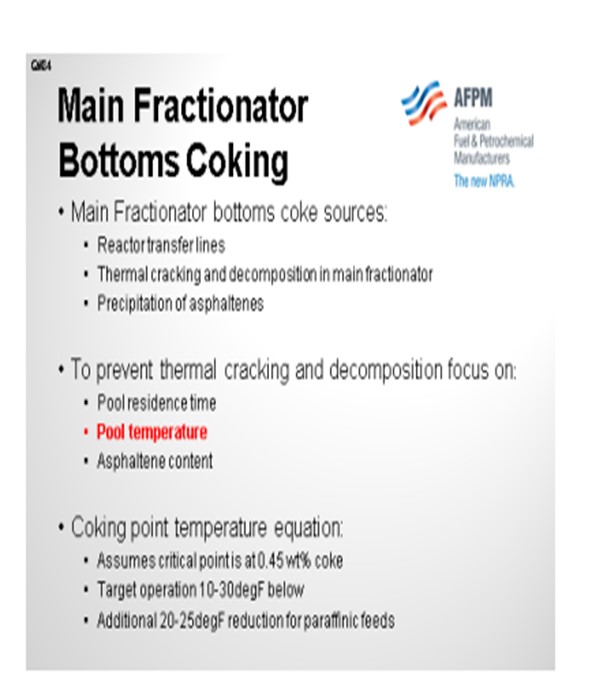
To go back and address the question, though, since it was not really about temperature, BP calculates our residence times based on the main fractionator bottoms’ head volume, and then we divide it by the DCO product flow rate out of the unit. By that definition, BP’s residence times for most of our units are in the hour to hour and a half range. We feel that this is a fairly good proxy for the residence time in the circuit without having to go develop detailed calculations around the volume in the piping or in the exchangers.
If you are considering reducing the residence time, then it is conceivable for you to do this by dropping the liquid level in your main fractionator bottoms, which would then lower the residence time in your main fractionator. And if you are doing any major modifications, you can adjust the volume of the main fractionator head, although that is typically not cost-effective.
When looking at residence time as opposed to temperature, consider that as you drop the time in this pool, you will have a greater chance of building up coke into the bottom of the pool, which will result in extra clogging problems in the main fractionator bottoms circuit. You should always consider your pumparound rates and the minimum pump NPSH (net positive suction head) on your bottoms pumparound circuit. Lowering your residence time could reduce the amount of the NPSH available. But typically, BP focuses more on the temperature and less on the residence time.
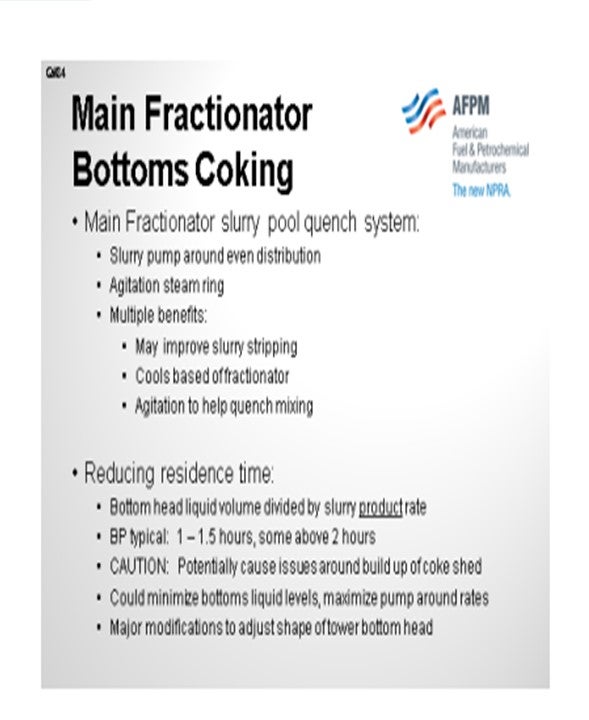
PIMENTEL (CITGO Petroleum Corporation)
I have a little to add to what Halle said. CITGO’s basis for residence time calculation is the total volume from the normal fractionator operating level all the way to the inlet passes of the slurry feed heat exchanger divided by both the slurry and recycle. The sum of these two flows represents what is being purged out of the system. Again, there are not many options to reduce residence time without sacrificing the cycle oil yield than operating at your lowest possible fractionator level.
As for temperature control, we do find significant temperature variances between different points in the fractionator bottoms compartment after injecting the quench oil. So, I would recommend that you monitor temperature not only by the temperature of the product leaving the fractionator, but you should also take some readings around the bottoms to find the significant temperature variances.
WILLIAMS (KBR)
KBR designs for a one-minute holdup between the maximum and minimum levels based on the total slurry draw-off rate. Operating the tower at a lower level will reduce residence time within the column.
AVERY (Albemarle Corporation)
I agree with the comments made by Halle, Sergio, and Jesse. My detailed answer is in the Answer Book.
NAVEEN DIMRI (Reliance Industries Limited)
What is the typical CSO (clarified slurry oil) asphaltene content? Is there any limit for the fouling control?
BROOKS (BP Refining)
The equation we use does not include the asphaltene level specifically. The feed quality parameter is around the feed paraffinicity, which is obviously not really the asphaltene. We have that built in to account for feed quality. I have seen some other general references for the industry around feed quality. A lot of people will look at their minimum bottoms temperature and then subtract 20ºF or 25ºF off of that as an extra cushion around feed quality differences, if they have particularly nasty feed.
PIMENTEL (CITGO Petroleum Corporation)
We do not measure asphaltenes, but we do control the API. We have found that when we operate below -3 API or -4 API, the coking tendency increases significantly. So, we have set that as a limit for a minimum API of your slurry oil.
NAVEEN DIMRI (Reliance Industries Limited)
At BP, what is the asphaltene content you normally create?
BILL WILSON (BP Products North America Inc.)
Just to clarify, in this coking calculation, we actually looked at the paraffinicity of the feed. So that is the parameter. Normally, we do not actually measure the asphaltenes in the slurry or, in fact, even in the feed.
BROOKS (BP Refining)
Coke in the main fractionator bottoms section can originate from multiple sources. The key typical sources are coke formed in the reactor transfer lines, thermal cracking and decomposition in the main fractionator, and precipitation of asphaltenes. High catalyst fines in the bottoms can act as nucleation sites for the asphaltene precipitation and thus result in higher bottoms coke formation. Catalyst and coke entrainment can be considered as determined by factors outside the main fractionator. Thus, when focusing on controlling main fractionator bottoms coking, we focus on the key factors influencing thermal cracking and asphaltene precipitation: bottoms pool residence time, pool temperature, and asphaltene content. To avoid coking in the main fractionator bottoms section, we typically do not focus on the residence time as much as we focus on maintaining lower temperatures.
BP has done a significant amount of work internally around the factors that influence main fractionator bottoms coking. Based on a 1988 paper by Total at an AKZO catalyst seminar, the thermal decomposition of DCO is directly related to both residence time and pool temperature. BP used data from this study and additional internal data to regress a relationship between weight percent coke formation in the bottoms, residence time, and pool temperature. Additional studies followed which indicated that FCC feed paraffinicity also has a significant effect on these main fractionator coking reactions. Thus this factor was also added to our regression equation. For our purposes, BP assumes the critical coking point in the main fractionator bottoms at 0.45 wt% coke. The regression equation is solved for temperature at the 0.45 wt% coke level. This temperature is our “coking temperature.” The BP units regularly track the coking point temperature and work to maintain main fractionator pool temperatures 10°F to 30°F below this coking point temperature to prevent main fractionator bottoms coking. Typically, refiners have addressed this by specifying a maximum allowable bottoms temperature which is reduced by 20°F to 25°F for highly paraffinic feeds.
A holistic look at this equation suggests that the effects of temperature and feed paraffinicity on bottoms coking is much greater than the effect of residence time. Typically our main controls around temperature are to install slurry pool quench systems and focus on heat removal in the pump around circuit. Ten of our eleven FCCUs in the BP system have slurry pool quench systems to maintain low pool temperatures. These quench systems typically include a distribution system to deliver cooled slurry pumparound into the base liquid as evenly as possible. This stream should be submerged in the liquid, near the top of the pool. The system also typically includes a steam distributor near the base of the slurry pool to cool the bottom of the pool and aid in mixing the cooled slurry into the pool. This steam ring can have multiple benefits including:
- improving the stripping of the DCO and thus may also improve the DCO flashpoint,
- cooling the slurry in the base of the fractionator and thus reducing coking tendency, and
- providing agitation to help mix the quench and liquid in the fractionator base.
To focus on the base question around residence times, BP calculates the residence time by calculating the main fractionator bottom head volume based on liquid levels as the pool volume and dividing this by the slurry product rate. BP’s typical residence times are between one and 1.5 hours for this system. Some of our units run with residence times over two hours due to large main fractionator bottoms volumes and minimum bottoms make operations.
It is important to note that reducing the main fractionator bottoms volume in an effort to reduce residence time can have the potential to cause issues around build-up of coke shed from the transfer line. Without major equipment modifications, a site could conceivably reduce residence time by minimizing bottoms liquid levels and maximizing the bottoms pump around rates consistent with the bottoms heat removal required to maintain the desired fractionator heat balance. If major modifications or revamps are made to the tower (including a full tower replacement), and a goal is to reduce the residence time in the bottoms pool, modifications can be made to the shape of the bottom head of the fractionator. Changing the shape to a cone or other lower volume head will reduce the residence time. This is typically not a cost-effective modification in most situations which is why we focus on maintaining lower slurry pool temperatures (as mentioned before). If residence time is reduced, it is also important to review the pumps and revamp as necessary for lower NPSH required due to lower liquid head volumes.
PIMENTEL (CITGO Petroleum Corporation)
The basis for the residence time calculation are: the slurry oil flow (as produced from the unit plus flow recycled to riser) and the volume of the main fractionator bottoms compartment from the normal operating level plus the volume of the piping from the bottom of the tower to the inlet of the first set of heat exchangers. There are not many options to reduce residence time other than lower the main column bottoms level. We have found that maintaining a continuous flow of cold slurry quench into the bottom head of the main column reduces coke formation and subsequent plugging of the slurry pump screens or pumparound exchangers. This practice minimizes hot spots in the slurry liquid in the bottom of the tower where coke can form even if the bottom outlet temperature is at target (690°F max). If the bottom temperature drops below our target when the quench flow is at minimum, we reduce slurry pumparound duty at the steam generator. We have experienced slurry exchanger fouling due to the presence of excessive PNAs (polynuclear aromatics) and find that this often correlates with very low slurry API. This can be mitigated somewhat by sacrificing LCO recovery and dropping LCO into slurry.
AVERY (Albemarle Corporation)
Including the composition of the main column bottoms oil and the liquid temperature, an important variable impacting coking in the main column bottoms circuit is the hydrocarbon residence time in the bottom of the fractionator. Excessive time and temperature can lead to coke formation. The oil residence time can be determined from the volume of oil in the bottom of the tower and the bottoms flow rate leaving the tower. The residence time should be minimized by maintaining a minimum bottoms liquid level and maximizing the bottoms pumparound rate consistent with the bottoms heat removal requirement necessary to maintain the desired fractionator heat balance.
SUBHASH SINGHAL (Kuwait National Petroleum Company)
Lower fractionation, bottoms level, and optimum temperature (less than 365°C) are a few considerations to avoid slurry circuit fouling.