Question 83: Can a slurry pump run at or below 1000 rpm (revolutions per minute)? If not, what is the lowest speed to minimize pump erosion?
RUSSEFF (CVR Energy, Inc.)
The short answer is “Yes”, but it would not be a good FCC answer if I did not say the words, “It depends.” The actual effective service life depends on your solids loading in your slurry system, in both typical and upset conditions. A good set of suction strainers and coke catchers in the entire level will certainly help you. I understand, from at least one of the major licensors, that there is typically a low limit of about 1200 rpm for new units. Can you run lower? Certainly, but there are also some considerations to contemplate.
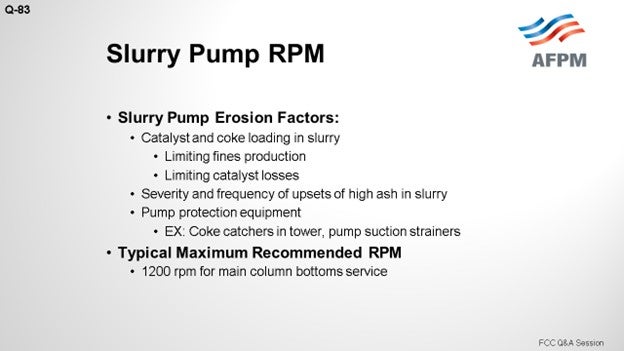
This slide shows a very old pump life curve from the old Lawrence literature, which I obtained when I was in my position. You can see “1200” annotated in red. You can also see that all of the curves start sloping up and that the coded pumps definitely have a distinct advantage. The CA6NM is uncoded, but it is also represented there without slurry contamination in its process.
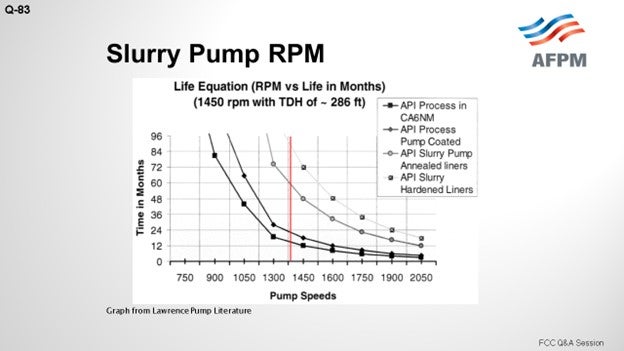
So, can you run lower? Yes. What is not shown up here is the type of contaminant; that is, what was the ash or the BS&W on the particular sample? It does not tell you the nature of the component. Although it is not shown on the slide, we would expect the shape of the curve to be the same. What is also not on the slide and which is part of the “it depends” part is the information about the location of your efficiency on the curve. You know, maybe that does not matter to you, but certainly what does matter are the minimum velocities through your exchangers. So those are some of the other variables to consider. Can you run lower? Certainly. Then you will see some great lifespan there, but it is a balancing act.
SINGH (Indian Oil Corporation Limited)
Slurry pumps are extremely critical for the performance of the MCB (main column bottom) circuit. While it is essential to maintain a certain minimum velocity in the slurry circuit, the speed of the slurry pump is typically governed by the desired capacity, head, and NPSH (net positive suction head). In all of our units, the slurry pumps typically operate between 1100 and 1400 rpm; and in most cases, these pumps are fully lined with 25% chromium (Cr). A word of caution while using fully lined pumps: They are very, very sensitive to thermal shocks. Our experience with these pumps has been extremely good, as far as erosion is concerned. Even under very bad conditions with very high BS&W due to occasional high catalyst carryover situations, these pumps have been able to perform well. But like I said, they are extremely sensitive to thermal shocks, so adequate precautions need to be taken. We have also had some bad experiences caused by thermal shocks to the pumps, which lead to sudden and total failure of the liner.
We have modified the warming up system of slurry pumps to enable heating at a very controlled rate (less than 50°C (82°F) per hour) by mixing hot and cold streams. This has eliminated the problem of thermal shock and substantially improved the reliability of these pumps. A maximum 50°C (82°F) per-hour rate is usually recommended for heating these pumps. One word of caution: It is not only the pump that has to be heated; the suction line or whatever is the stagnant material in the standby pump’s suction line also needs to be heated. Otherwise, whenever the standby pump is put to service, the pump will see an unexpected thermal shock.
ROBERTSON (AFPM)
Those were the responses from the panel. Any comments or questions from Kevin Proops? [Laughter]
KEVIN PROOPS (Koch Industries, Inc.)
I am not selling pumps either. [Laughter] I will put my Pete Andrews hat on here for just a second and talk about fundamentals. Pump rotation speed is important, but it is really the impeller tip speed that will cause erosion. If you slow the pump, you will need a bigger impeller for the same discharge pressure. The curve on Richard’s slide shows 286 feet of head, which is nominally a 100 psi differential. If you really want lower erosion, can you design a system that is more like 50 psi differential? You could put all the heat exchangers in parallel. I have seen that done before. You can avoid high pressure drop control valves in the circuit by diverting the pumparound return to the bottom of the tower to control heat removal, rather than throttling.
I have seen vertical steam generators that basically do not foul. These generators have the channels on the bottom with a vertical bundle. In any design, exchanger tube velocity is important and has been discussed in past sessions. Keep piping runs short. Minimize the pressure drop in the system, and you should be able to get there.
SANJIV SINGH [Indian Oil Corp Ltd. (IOCL)]
Slurry pumps are critical for the reliability of the MCB (main column bottom) system of an FCC unit. Desired velocity in the slurry exchangers also results in a high pressure drop, setting the operational requirement for the slurry pump. Impeller diameter or the speed need to be increased to match the hydraulic requirement of slurry circuit. The speed of the pump is mainly governed by operating parameters such as capacity, head, and NPSH. Adequate minimum tube velocity in the slurry circuit is absolutely essential to avoid excessive fouling in these exchangers. In the case of slurry pumps, a lower speed will mean less erosion but will require a bigger pump size. A higher head will require a higher speed. A speed limit of about 1500 rpm has been specified typically for FCCU units. Degradation of pump performance will increase the rate of exchanger fouling and limit MCB heat removal. To minimize pump erosion from catalyst and coke particles, an API fully lined pump is often required when operating with a higher pump head and operating speeds in the MCB circuit.
Apart from lowering speed, another way of reducing erosion is to specify a fully lined slurry pump with a 25% Cr iron liner. These pumps can be operated continuously for a considerably longer period compared to a normal API pump. In all of the recent projects, licensors specified fully lined slurry pumps and the same were used with satisfactory performance. Of course, speed was also limited, but physical pump availability at that speed has to be ascertained.
For most of our FCC/RFCC units in IOCL, slurry pump speeds are in the range of 1100 to 1400 rpm. Even for this operating range, fully lined pump internals are used (25% Cr). Though these pumps have demonstrated reasonable resistance to erosion, but these pumps remain extremely sensitive to thermal shocks. Recommended warming or heating up procedure for these pumps should be strictly followed. In our newer units, we have installed facility to heat up these pumps in a very controlled manner by mixing two streams of different temperatures and fine controlling the heating rate. Further reduction of pump speed below 1100 rpm is also possible considering acceptance of the bigger size of the pump model, as well as the availability of the PTR (performance track record).
Erosion is no doubt a function of speed: the higher the speed, higher the erosion, which will require more frequent overhauling.
CHRIS STEVES (Norton Engineering)
Slurry pumps are designed to operate at low speed to minimize corrosion but trade off hydraulic efficiency to do so. Pump manufacturers with long-term slurry experience can provide proven erosion-resistant metallurgy options (casing, liner, wear rings, etc.), which allow operation of slurry pumps at relatively high speeds (1200 rpm typical) yielding hydraulic efficiency and ultimately power reduction benefits versus low speed pumps.
ANDREW W. SLOLEY (CH2M HILL)
Refiners have reliably run API pumps continuously at speeds of 900 rpm and below. The lower speed is often compensated for by using a larger impeller. Slower pump speeds are applied in most cases to reduce suction-specific speed problems. However, slower speeds also reduce erosion, as well as reducing discharge pressure and pump efficiency.