Question 81: Is there experience with continuous torch oil and/or air preheater firing; and if so, for what reasons? What are the demonstrated effects from doing either of these processes?
SCHOEPE (Phillips 66)
We do not have much experience with continuous torch oil firing. We do have one unit that fires torch oil if the bed temperature drops below 1250ºF. However, that unit is not set up for slurry recycle. So, on most units, we prefer slurry recycle over an operation with torch oil. In one case, after an extended use of the inline air heater, a Phillips 66 unit actually caused mechanical damage after switching to hydrotreated feed.
Torch Oil: When using torch oil, your emissions and catalyst fines generation will increase. You might have noticed that during and after start-up, as it always takes a few days for the fines to work themselves out of the system.
Continuous Air Heater Operation: The equipment is typically not designed for continuous operation. However, if it is decided to use it as such, it would not be difficult to design the air heater for this operation.
Other Considerations in Our Tech Network: We discussed the case when one unit was starting up and the air blower tripped, but the torch oil was left on. You can imagine that the restart ended up being very exciting when the torch oil lit up during the restart. If you intend to operate that way, an automatic shut-off on the lower air flow should probably be considered as part of the SIS.
'
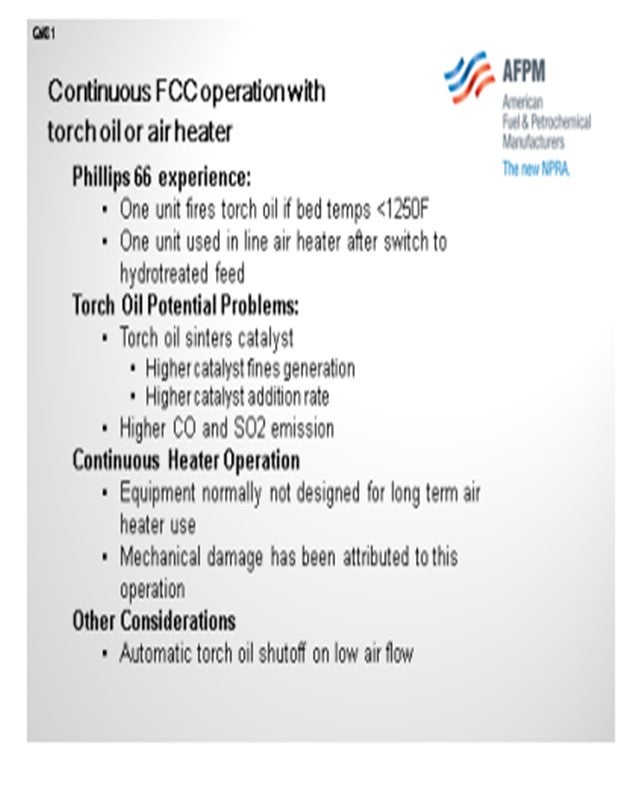
LALL (UOP, A Honeywell Company)
Use of continuous torch oil and/or air preheater firing can occur in numerous instances, such as abnormal circumstances following unit upsets, safe park holding modes, or during operations when addressing low delta coke operation with very low Conradson carbon residue feeds or hydrotreater feeds. In addition to high air grid exit velocities, when increasing the risk of erosion and catalyst attrition through continuous air heater firing, the air heater flame pattern should be monitored and controlled by adjusting the air splitting damper to prevent damage to the internal refractory lining.
If heater firing is to be considered on a continuous basis, then the air grid should be designed for jet velocities below 200 fps during operation, with and without the air heater at all times. As Christian already described, the continuous torch oil firing is not good because excessive heat release can sinter catalyst. If it is necessary to use torch oil, care should be taken to properly atomize the oil. A high concentration of oil in one spot can result in hot localized temperatures being undetected by the regenerator temperature indicator. More even distribution of torch oil in the regenerator would be desirable by using more torch oil nozzles.
WILLIAMS (KBR)
KBR recommends limiting conventional air heater and torch oil firing as extended periods will only accelerate catalyst deactivation and catalyst attrition. However, on rare occasions, we have witnessed a client who has elected to utilize torch oil for an extended period as a primary approach to address problems with the upstream units where the FCCU feed become lighter and also to maintain heat balance for that period of time. In another case, the client elected to hold the regenerator temperature for extended periods while addressing the processing issues in the VRU (vapor recovery unit).
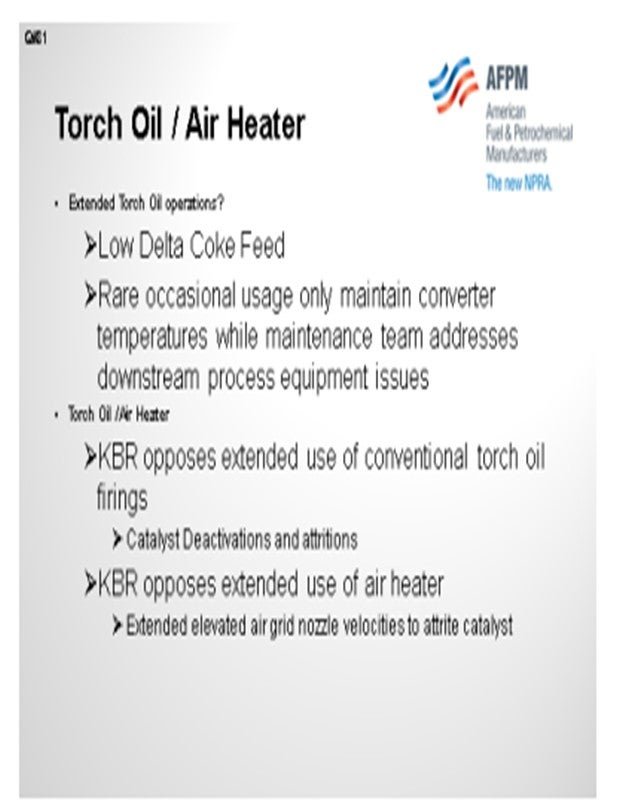
A traditional alternative approach when the feed becomes lighter is that the plant personnel, instead of going with torch oil, may elect to increase the endpoint on the feed by making adjustments at the VDU (vacuum distillation unit). Recycling slurry would be another option to do this. Slightly reducing the hydrotreating severity to increase the coke make precursors may help restore the temperature in the regenerator itself.
KBR has a non-traditional alternative for mitigating the catalyst damage associated with conventional torch oil. We have developed a system for distributing liquid fuel in the regenerator. This system was initially commercialized for our KBR SUPERFLEX™ process. It also can be utilized for severe hydrotreating operations. Since its inception, KBR has adopted this technology for use in conventional FCC units with particular list return configurations. So, before you consider this, we have to evaluate your configuration to see if these configurations will be applicable for you.
In addition to the system for liquid fuels, a system for firing the regenerator with fuel gas, which is alternately lower-cost fuel, has also been commercialized. So, for this situation of severe hydrotreating, this approach of additional fuel gas firing in the regenerator is a non-traditional alternative a refiner could consider.
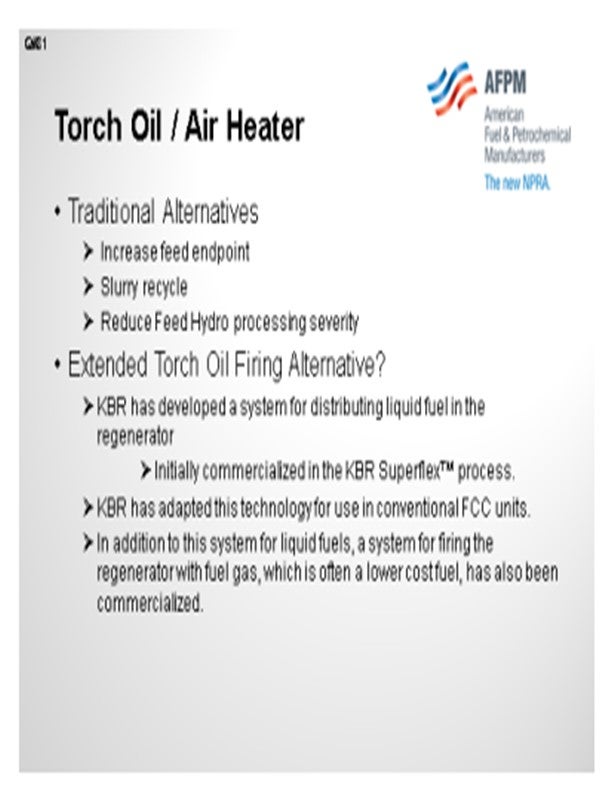
PIMENTEL (CITGO Petroleum Corporation)
We have some experience with continuous torch oil operation for about three to seven days. Christian already covered most of the reasons, so I will only add a few more. First, a very light FCC feed was coming from a crude oil unit at start-up. That unit was slopping the distillates to the FCC tank rather than to the slop oil system. Another reason could be very inactive FCC catalyst coming from an extended start-up operation and/or from a standby operation due to fractionator emergency work. Then again, torch oil should be your last resort. Alternatives were already covered: increase vacuum cutpoint, increase severity in the unit, recycle slurry, or even detune your stripper or feed nozzles.
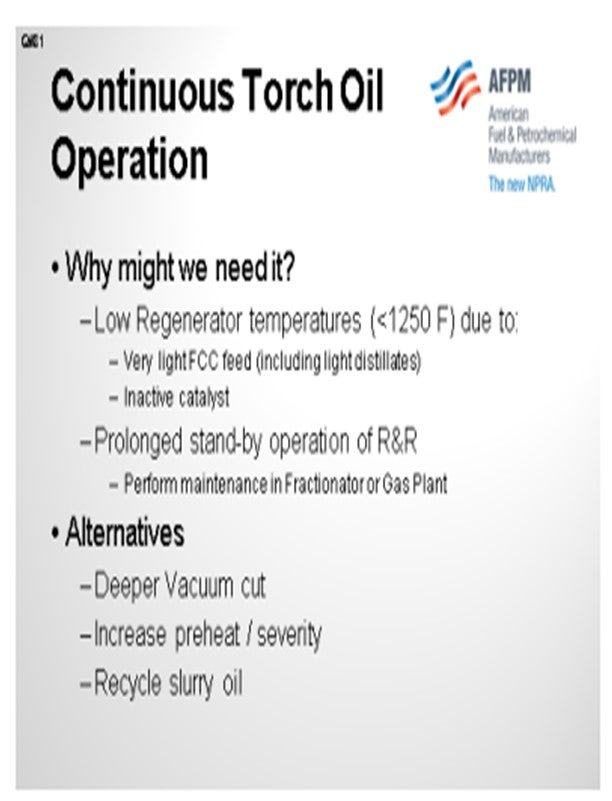
Consequences have also already been covered. Again, continuous torch oil firing increases the catalyst attrition and deactivation due to localized hot zones around any of your torch oil nozzles, as well as causes incremental fines generation due to increased exit velocity from the air grid nozzles.
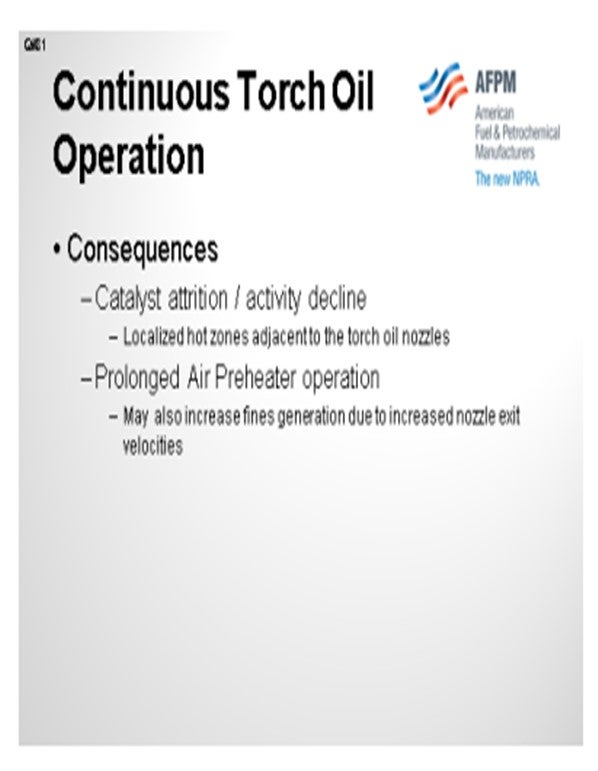
AVERY (Albemarle Corporation)
I agree with the comments already discussed and have just two more points. We have seen some refiners using torch oil not just for days, but for months on end. So it has happened, and it does happen right now. Also, speaking as a catalyst supplier, if you want to keep doing it, it is fine with me.
LALL (UOP, A Honeywell Company)
This situation can arise in numerous circumstances. It can arise during unit upsets or safe park holding modes, in low delta coke operations associated with clean (low Conradson carbon) and hydrotreated feeds, with refinery crude slate changes or crude and/or vacuum distillation operating changes. Some refiners have resorted to using continuous firing of the air heater or torch oil. In addition to higher air grid jet exit velocities increasing the risk of distributor jet erosion and catalyst attrition, the air heater flame pattern must be monitored and controlled by adjusting the air splitting damper to ensure no damage to the air heater internal refractory lining occurs. There have been many recorded instances of hot spots and refractory damage occurring to the air heater internal refractory lining during start-ups. If air heater firing is to be considered on a continuous basis, the air grid should be designed for jet exit velocities below 200 fps during operation with and without the air heater.
Continuous torch oil is generally not desirable because the excessive heat release can sinter catalyst, resulting deactivation. When it is necessary to use torch oil, care should be taken to properly atomize the oil. A high concentration of oil in one spot can result in hotter localized temperatures undetected by the regenerator temperature indicators. A more even distribution of torch oil into the regenerator catalyst is therefore desirable. We have seen operations where torch oil was fired continuously over a seven-day period to maintain a regenerator in “warm” condition (regenerator dense bed temperatures of 1,025°F to 1,100°F) while the unit was in a safe hold position without any noticeable impact to catalyst activity.
SCHOEPE (Phillips 66)
Phillips 66 has very little experience with continuous torch oil firing. One unit fires torch oil when the feed gets so light that the regenerator temperature drops below 1250°F.
Operation with torch oil sinters catalyst and generates catalyst fines. Many units see higher amounts of catalyst fines during the first few days after start-up. It also increases CO and NOx in flue gas. Poorly designed torch oil systems can cause mechanical damage.
Most sites do not tie the torch oil into their safety instrumented system. If a unit fires torch oil continuously, then consider a torch oil trip on low airflow. For example, if the main air blower trips, the catalyst could become oil soaked and cause damage if the oil ignites during unit restart.
One Phillips 66 FCC unit experienced damage in the spent catalyst/air distributor after firing the air preheater continuously for several months. The air heater needed to keep the regenerator temperature high enough after this unit had switched to hydrotreated feed.
PIMENTEL (CITGO Petroleum Corporation)
We have limited experience with continuous torch oil operation (for one to three days maximum) for several reasons. First, very light FCC combined feed from crude start-up operations slopping to FCC feed tanks or very inactive FCC catalyst due to extended start-up operations leads to a relatively low regenerator temperature (<1250°F). Another reason for operating on torch oil is prolonged standby operation of the reactor/regenerator section to perform maintenance activities in the workup section; for example, the fractionator or WGC. The use of torch oil should still be the last resort to keep the regenerator hot. Preferred options are include increasing FCC preheat/severity and making the feed heavier by achieving a deeper cut in the vacuum unit or recycling slurry oil to the riser. The effect of extended torch oil operation is accelerated catalyst activity decline due to the localized hot zones adjacent to the torch oil nozzles. Prolonged air preheater firing may also increase fines generation due to increased nozzle exit velocities.
AVERY (Albemarle Corporation)
Yes, there are some units practicing continuous torch oil and/or continuous firing of the direct-fired air heaters (DFAH). This practice has been used in an attempt to compensate for very low delta coke operations in order to keep the regenerator hot enough to maintain control of the catalyst circulation. Neither practice is desirable, especially long term. Other means of increasing delta coke, such as complete CO combustion, adding a heavy feed component, or utilizing a less coke selective catalyst should be investigated. Burning torch oil does not typically heat the catalyst bed uniformly, leading to thermal gradients in the dense phase and increased catalyst deactivation. If the dense phase level is not carefully controlled, significant afterburn can occur, as well as damage to cyclone diplegs. Continuous firing of the DFAH is probably worse, as there are certainly safety concerns with flameouts, overfiring, and more. Potential damage due to thermal stress to the combustion air distributor is also possible, especially when the distributor temperature cycles. Also, increased catalyst deactivation can occur due to non-uniform heating.
WILLIAMS (KBR)
Continuous torch oil firing, though normally only used during start-up, has been practiced. On rare occasions, Operations has elected to maintain converter temperatures with torch oil firing for several days while Maintenance teams address downstream equipment issues. During upstream operational upsets where the feed delta coke is reduced, Operations may also elect to introduce torch oil to maintain unit heat balance. KBR recommends limiting conventional torch oil firing as extended periods only accelerate catalyst attrition and deactivation. To mitigate the catalyst damage associated with conventional torch oil firing, KBR has developed a system for distributing liquid fuel in the regenerator which was initially commercialized in the KBR SUPERFLEX™ process. Since its inception, KBR has adapted this technology for use in conventional FCC units. A patent pending version is also available for use in conventional FCC operations. In addition to this system for liquid fuels, a system for firing the regenerator with fuel gas, which is often a lower cost fuel, has also been commercialized. Continuous air heater firing has been utilized for continuous support of the heat balance, but this practice can have an adverse impact on the velocities through the regenerator air distributors which can lead to catalyst attrition, as well as the practical issues associated with monitoring the heater firing.
ROSANN SCHILLER (Grace Catalysts Technologies)
The use of “dry circulation” is a common event in many refineries. Often upstream or downstream problems in a refinery can cause the FCC to pull feed, and during these times, many units elect to continue “hot” catalyst circulation to avoid a complete thermal cycle on the FCC. Typically, these events are short-lived (up to about one week). During this time, refiners may add fresh, or more typically, equilibrium catalyst to the unit to maintain catalyst bed levels. Using torch oil creates a severe hydrothermal environment, with temperatures at the nozzle tips often eclipsing metallurgical recommendations, and velocities well over 100 fps.
These nozzle tips are often buried in the dense bed of the regenerator, causing areas of severe stress on the catalyst particles. Attrition and catalyst deactivation are the outcomes of this activity.
The use of torch oil or fired air heating while feeding oil is less common. In units that process severely hydrotreated feedstocks, operators often use torch oil to create additional heat in the regenerator to maintain the heat balance. This operating strategy often comes at a high cost, as many refineries use LCO material for torch oil. A more economically attractive option is to add higher amounts of FCC catalyst and to pursue a reformulation to higher fresh FCC catalyst activity.
We have noted one refinery that, after a turnaround, started up on a substantially lighter feed. This unit started up using the fired air heater and did not turn it off, as the new feed made substantially less coke than the pre-turnaround feed. Catalyst addition rates were increased, and eventually, the unit reformulated to a higher activity catalyst. This reformulation, along with other moves in the operation, allowed them to discontinue the use of the fired air heater.
Another refinery with a similar short term “lightening” of the feedstock elected to fire torch oil to maintain heat in the regenerator. This unit continued this practice until they shut down for a planned turnaround. We observed increased fines generation, and complete destruction of the torch oil nozzle tip. After their turnaround, the refiner reformulated to a more active catalyst to remove their dependence on torch oil to keep the regenerator hot