Question 80: We are considering severe hydrotreating of our FCC feed. What yield shifts or unusual operating problems might we expect? What can be done to address these issues?
SCHOEPE (Phillips 66)
Processing Hydrotreated Feed: First of all, let’s define what ‘severely’ hydrotreated feed means. One unit in our system hydrotreats the feed down to 50 ppm sulfur and 50 ppm nitrogen, so you can see that processing that type of feedstock has tremendous yield benefits. You can expect conversions of 90% and higher. In some cases, you can recycle this slurry to extinction. However, there were a lot of issues. Some were anticipated, and some were not.
Operational Issues: The most obvious issue everyone expected was the regenerator temperature. Because of the low amount of coke precursors in the feed, it is very hard to keep your regenerator temperature high enough for efficient coke combustion. Our units have tried several options. In the extreme cases, we have used torch oil. One unit used the direct-fired air heater for some period of time. Sometimes stripping steam was reduced in order to increase regenerator temperature. Of course, slurry recycle is used first. All of these steps were done to increase the regenerator temperature. If you start processing hydrotreated feed, the gas make will increase. Your wet gas compressor and absorber train have to be designed for that change.
Reliability Issues: Two units experienced alkaline carbonate stress corrosion cracking after they switched feed. As a result, Phillips 66 developed an ROL that monitors the ratio of sulfur to nitrogen in FCC feed. I put that ratio in the Answer Book also. Additionally, the slurry system has to be designed for a higher catalyst concentration and lower flow. If you have a unit that is accustomed to much higher slurry yields, then the ash content can easily double. During my tech service times, I had a unit that ran in distillate mode and then switched to 100% hydrocracker bottoms. Their slurry pumps that used to last for years now eroded within a matter of months. So, the slurry system has to be reevaluated.
The catalyst losses on the reactor are basically the same. But because your slurry yield is so much lower, the ash content in slurry is increasing.
Another issue is the reliability of the flue gas system. If you do recycle slurry to extinction, the only way for the catalyst to get out of the system is through the flue gas section. Therefore, all of that equipment has to be designed to handle the additional dust load.
Environmental Concerns: On the environmental side, we actually ran into unanticipated issues. I already spoke about increased particulate emissions. Stack opacity can also increase because the SO2 almost disappears. The reason is that the SO2 decreases the resistivity of the catalyst particles; therefore, it is more difficult for the particle to accept a charge if SO2 is missing. On at least one unit, after switching to hydrotreated feed, we had to install an ammonia injection system to compensate for that effect.

CO Combustion: This slide was presented by Bill Hennings in a previous NPRA meeting. It shows the relationship between CO and NOx (nitrogen oxide) of one unit after the switch to hydrotreated feed. All of a sudden, their CO emissions went way up 3,000 ppm while their CO limit was 500 ppm. It did not matter how much excess O2 was used. They operated with 3% to 6% excess oxygen, and it was still not possible to reduce the CO.
When the production plan called for processing a little heavier feed, which included more contamination, they noticed that as the NOx came up, the CO decreased. Once they discovered that relationship, they tried to purposely increase the NOx in flue gas in order to stay below 500 ppm. They settled for an ammonia injection system at the main air blower outlet. Another unit which processes the same kind of feed did not have this strange behavior. We, therefore, think that the aforementioned can be related to inadequate air distribution.

WILLIAMS (KBR)
My colleague has already highlighted the impacts on the unit’s heat balance. As far as yield shifts go, with more improved crackable feedstock and a higher cat/oil ratio, one should expect an increase in conversion, which ultimately should yield a higher gasoline and LPG yield for the unit with corresponding reductions in light cycle oil, slurry, and coke at a cost of reactor outlet temperature. The LCO and slurry yields will crack into the gasoline/LPG range. The impact of coke yield will result from the improved feed quality, higher hydrogen content in the feed, reductions in metals content, and Conradson carbon residue content. One should also expect to the see the gasoline octane decline to some extent because the aromatic content in the naphtha is reduced as the aromatic content in the feed stream is saturated.
Operational problems for a full combustion regenerator include lower temperature operations which will impair the regenerator performance and can lead to poor combustion kinetics. These lower temperatures often result in higher afterburn conditions and higher carbon on regenerated catalyst. From a hydraulics standpoint, elevated catalyst circulation will be observed, resulting in lower catalyst slide valve differential pressures and elevated stripper flux rates.
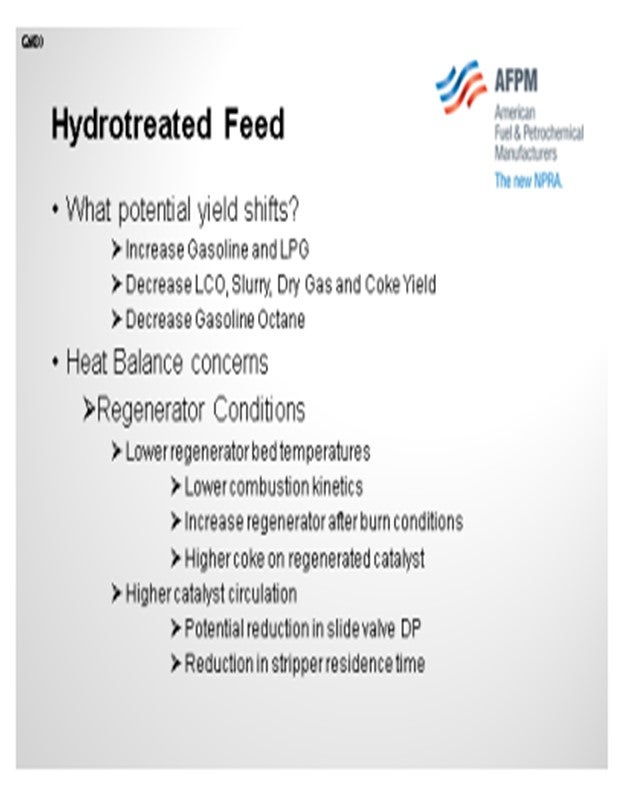
As far as potential process solutions, the most favorable option is to increase catalyst activity. This can be done in multiple ways, such as increasing the catalyst makeup rate, changing the catalyst ingredient itself to increase the catalyst surface area, or even adjusting the rare earth content to help stabilize the unit. Another option is to increase the unit feed rate, but you should be mindful of the downstream processing units to ensure that they can handle the increased capacity to the unit.
If you do have a feed furnace, increasing the feed preheat temperature can generate some flexibility for the unit itself. In this case, a typical rule of thumb is to increase the preheat temperature by 15°F to 20°F. This change would typically generate about a 1°F increase in regenerator temperature. Another option is to recycle slurry oil to the riser itself. Before you do this, we recommend that you communicate with your feed nozzle licenser to ensure that the maximum solutes concentration to those feed nozzles is not violated.
If the FCC was formally processing resid to the unit and you have cat coolers, then you have the flexibility of turning them down to reduce the duty in order to regain the regenerated temperature itself. Because of the potential catalyst deactivation, KBR does not recommend long-term conventional torch oil operations or decreasing the stripping steam rate in order to restore the regenerator bed temperature.
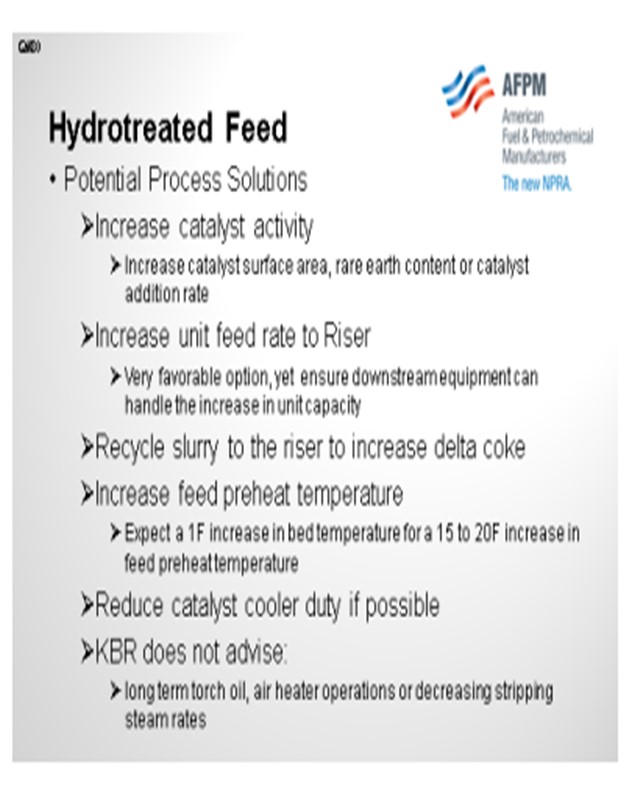
LALL (UOP, A Honeywell Company)
Technology offered by UOP for delta coke-challenged operations is RxCat™, which decouples the traditional heat balance by recycling a slipstream of spent catalyst back to the reactor riser and permits variable amounts of recycled spent catalyst to achieve the minimum regenerator operating temperature. RxCat has been utilized in UOP’s new unit designs and revamp applications for low delta coke operations.
AVERY (Albemarle Corporation)
Most of my answers have already been covered by the previous panelist. I do want to say that when you have a lower delta coke on the catalyst side, you need to increase your activity. In other words, if you increase rare earth, then you should increase delta coke and hydrogen transfer.
We are fortunate to be a leader in hydrotreating and FCC catalysts. On the slide is an example showing a time when we used hydrotreating severity to make a higher activity FCC pretreater (hydrotreating) catalyst and changed the operating conditions on the hydrotreater. This slide shows an example of how when we increased hydrotreater severity, the gravity went from 25 to 27 and the sulfur went from 0.5 to 0.1. There are also other various effects to the feed. You can also see that we kept the catalyst effects the same except for the metals on the equilibrium catalyst, which is going to go down due to the higher severity hydrotreating.
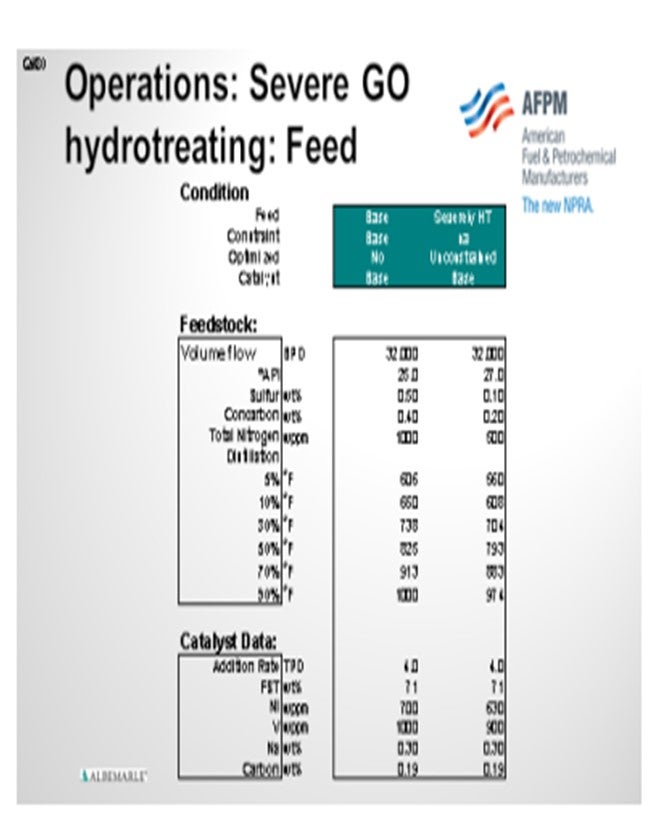
The next slide shows you some typical yields. We have five different cases. The first column shows the base case where the regenerator temperature is 1276ºF with a conversion of 77ºC. By going to this more severely hydrotreated feed, the lower delta coke represented in the region goes down to 1233ºF and the cat/oil ratio goes from 6.1 LV% (liquid volume percent) to 7.2 LV%. You can also see an increase in the gasoline yield.
What happens when you go to these higher severity feeds is that you will hit some other kind of constraint. In the second column, you see that you are not hitting any constraint. One of the most common constraints for FCC units is catalyst circulation rate, which is the first added category. Wet gas compressor constraint is also common, as is minimum regenerator temperature. So in this case, we used the kinetic model to put in the constraints for catalyst circulation rate, wet gas compressor, or regenerator temperature. So based on the location of your constraint, your economics – which are represented on the very top on the gross margins – can vary quite a bit.
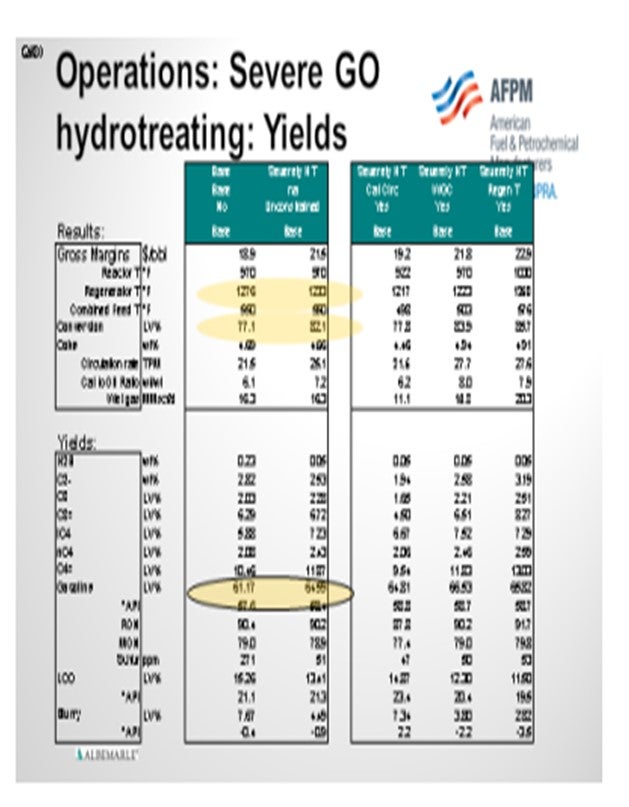
JACK OLESEN (Praxair, Inc.)
I believe that this topic was covered at the 2012 AFPM CAT conference. There was some discussion about torch oil and cutting back on stripping steam. Betsy Mettee answers this question well in the Answer Book. At Praxair, we have experience with refiners who have decided to cut back on their air blower rate, add oxygen to minimize the amount of nitrogen going through the regenerator, and reduce cooling due to that nitrogen in the air.
KEVIN PROOPS (Solomon Associates)
Christian, regarding your severe operation, am I correct in understanding that the main reason you were operating that severely is because the light cycle oil product has to make diesel ULSD (ultra-low sulfur diesel) specs?
SCHOEPE (Phillips 66)
Yes, that is true.
KEVIN PROOPS (Solomon Associates)
Thank you. I also want to point out that if you have an LCO sulfur constraint, there are hydrotreating technologies that allow you to make diesel sulfur without having to go quite so severe on cat feed sulfur. While Rik Miller was at Unocal, he wrote an excellent paper describing the situation when you severely hydrotreat feed and can actually end up making coke out of hydrogen you pumped in. So that may not be an optimum case.
On the plus side, our data shows that units which are severely hydrotreated (0.1 wt% sulfur or better) tend to see forgiveness of the hardware that is not optimal. For example, in units with sloped risers or units with feed nozzles that are not state-of-the-art, because you tend to run hotter feed, some of these hardware deficiencies are masked. The hydrotreated feeds tend to look better, across the board, just because these hardware issues become less relevant.
SCHOEPE (Phillips 66)
Processing severely hydrotreated feed (sulfur less than 50 ppm, nitrogen less than 50 ppm) in the FCC has significant yield benefits. The FCC conversion can be increased to over 90% and in some cases slurry can be recycled to extinction. Such a change in feedstock, however, can cause operational, reliability and environmental issues.
Operational Issues:
Due to the very low amount of coke precursors in hydrotreated feed, the regenerator temperature can decrease to such a degree, that coke is not burned efficiently off the catalyst in the regenerator. The low regenerator temperature will also increase the catalyst circulation rate which decreases the regenerator catalyst residence time and which further contributes to poor catalyst regeneration.
To increase coke yield in order to increase the regenerator temperature, the catalyst had to be reformulated for higher delta coke. Our FCC units have recycled slurry, used the start-up air heaters on occasion and/or torch oil or reduced stripping steam to keep the regenerator temperature high enough for adequate catalyst regeneration.
Processing hydrotreated feed increase the unit conversion, but it also increases the gas make from the FCC. The wet gas compressor and the absorber system have to be designed to process the increased gas load.
Reliability Issues:
Carbonate Stress Corrosion Cracking (ACSCC): Some sites have experienced significant amounts of Alkaline Carbonate Stress Corrosion Cracking (ACSCC) after switching to hydrotreated feed. This type of cracking can occur in piping and vessels in areas with residual stress. In most cases, the feed nitrogen to feed sulfur ratio is greater than 100 [N ppm / (wt% S *100)], the PH in the main fractionator and high pressure receiver water boot is above 8.5 pH and if the carbonate (CO3=) concentration is larger than 400 ppm. As a result of this type of cracking, new stress relieving guidelines were developed and the feed sulfur to feed nitrogen ratio is monitored on all Phillips 66 units as part of the Reliability Operating Limits (ROL).
Slurry System Reliability: Units designed for much larger slurry yield can see the catalyst content (ash content) in the slurry increase after switching to hydrotreated feed. The catalyst content in slurry increases because the reactor side catalyst losses remain constant while the slurry yield is much lower. The equipment in the slurry circuit has to be designed to handle the higher catalyst in slurry content.
Flue gas section reliability: If slurry is recycled to extinction, all catalyst fines leave the FCC through the regenerator with the flue gas. The catalyst fines collection system in the flue gas section has to be designed for the increased dust load.
Environmental Issues:
Particulate Emission: Units with electrostatic precipitators (ESP) can see an increase in stack opacity and particulate emissions as the SO2 content in flue gas decreases. The lack of SO2 in flue gas makes it more difficult to charge a catalyst particle. Some units have compensated for this effect by installing ammonia injection at the inlet of the ESP.
CO combustion: If the nitrogen in feed is reduced to such a degree that little or no NOX is made, the CO content in flue gas might increase. The data below shows the relationship between NOX and CO content in flue gas from one Phillips 66 unit. This data was previously published by Bill Henning during the August NPRA meeting in 2008. In order to keep the flue gas CO emission below 500 ppm, this particular FCC now injects ammonia into the air blower discharge in order to generate some NOX. Another unit that was processing the same feedstock did not have these CO emission issues. It is believed that better catalyst/air distribution might explain the different response to this feedstock change.
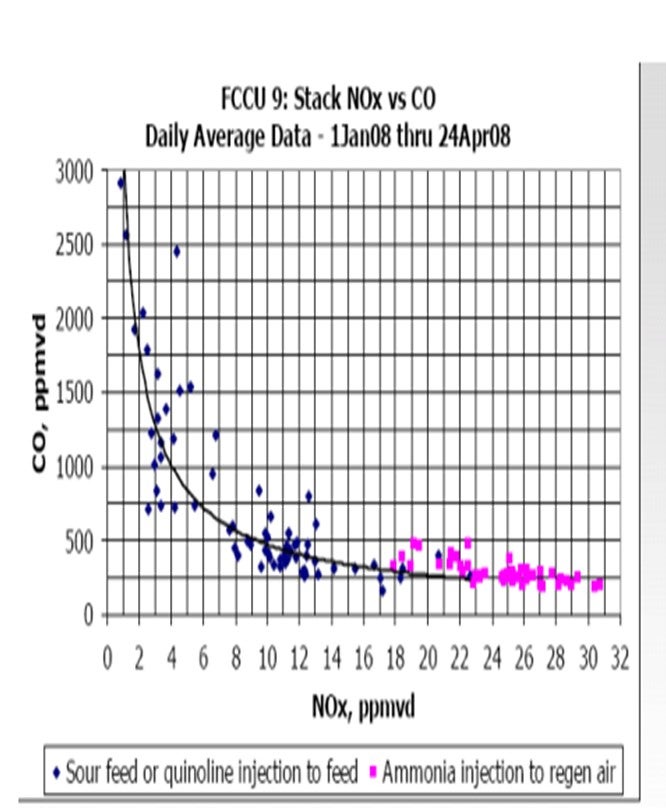
AVERY (Albemarle Corporation)
More and more refiners are hydrotreating (HT), or more severely hydrotreating, their FCC feed to meet fuel sulfur specifications. Hydrotreating the feed yields higher conversion, improved gasoline selectivity, lower octane, and lower delta coke.
Due to the lower delta coke, catalyst circulation rate limits can be reached. When this occurs, the refiner will need to increase the delta coke through higher catalyst activity, increase rare earth (delta coke increase), increase reactor pressure, increase slurry recycle, reduce stripping steam, or utilize torch oil. Reducing stripping steam and, in particular, using torch oil, should be avoided if possible. These methods introduce high hydrogen content combustibles that lead to localized exotherms. These effects will be covered on Question 81 in the Operations section.
Albemarle is a leading supplier in FCC and hydrotreating catalysts. These combined strengths give us the experience and opportunities to demonstrate the effects of changing FCC feed through increased hydrotreating severity. To demonstrate the effects, we have run a test case where the HT severity was increased by changing to a more active FCC pretreat catalyst and operating at higher temperatures over a shorter run length.
WILLIAMS (KBR)
Severe hydrotreating FCC feed [VGO (vacuum gas oil) feed with high Watson K-factor and low Conradson carbon content] will largely affect the FCCU heat balance by lowering delta coke, thus reducing regenerator temperature while increasing the catalyst to oil ratio for a constant Reactor Temperature.
As far as yield shifts go, a more crackable feedstock and higher cat-to-oil ratio will result in higher unit conversion with increases in gasoline and LPG and corresponding reductions in dry gas, LCO, slurry, and coke. Gasoline octane will be lower due to the reduction of aromatic content in the naphtha as more aromatic compounds in the feedstock are saturated. LCO and slurry yield will decrease as more will crack into gasoline and LPG range materials. The impact on coke yield is a result of better feed quality: higher hydrogen content, lower nitrogen, metals, Conradson carbon, etc.
Excessive high cat-to-oil ratios can create unit issues as catalyst circulations are increased at lower regenerator temperatures. For full combustion regenerators, low temperature operations will impair the regenerator performance which can lead to poorer combustion kinetics often resulting in higher afterburn, higher catalyst circulation and higher carbon on regenerated catalyst. One should determine whether adequate stripper residence time and catalyst slide valve differential pressure can be maintained at the increased catalyst circulation rates.
To address these issues, refiners have incorporated several options to increase regenerator temperatures while processing hydrotreated FCC feed. Often the best approach to addressing the low delta coke issue is to increase the catalyst activity. Several options to increasing catalyst activity include increasing catalyst surface area, rare earth content or catalyst addition rate. As e-catalyst activity increases, the amount of coke generated per pass through the riser increases and therefore increases regenerator bed temperature.
Another option is to recycle slurry oil to the riser. Most refiners elect to inject slurry recycle with the feed to the riser while others elect to inject the slurry in a separate nozzle. One should be mindful of the process issues when considering injecting slurry and feed the same nozzles. For long-term reliable operations, feed nozzles are design for a maximum solids handling. Proper feed nozzle design is essential for robust operations when processing streams with high solids content. In addition, on rare occasions, injecting slurry within the same nozzle can allows asphaltenes to drop out of solution and potentially plug the nozzle. KBR designs for injection the slurry mixed with the fresh feedstock. Finally, slurry recycle often increases dry gas make, so one should evaluate downstream systems to ensure the increase capacity can be handled. Increasing unit feed rates and/or feed preheat temperature are other options, if the unit has the flexibility.
Increasing the unit feed rate is favorable option if downstream processes can handle increase capacity. As far as feed temperatures, one should expect about a 1ºF increase in regenerator bed temperature for every 15ºF to 20ºF increase in feed temperature to the riser.
FCC units processing residue and equipped with catalyst coolers will be able to maintain regenerator temperature by adjusting catalyst cooling. Because of the potential catalyst deactivation, KBR does not recommend long-term torch oil usage using traditional torch oil nozzles or decreasing stripping steam rates to increase regenerator temperatures.
LALL (UOP, A Honeywell Company)
Hydrotreating of the FCC feeds has become more popular and widespread as refiners choose to remove more of the sulfur-containing contaminants in the feed to avoid post treating of the FCC products. Severe hydrotreating of the FCC feed promotes hydrogen saturation of the feed molecules, as well as removal of much of the sulfur, nitrogen and metal contaminants. FCC feed crackability is improved, yielding increased liquid volume conversions (approaching 90%) of valuable transportation fuels (gasoline and lighter) and reduced dry gas yields. One of the main challenges in processing severely hydrotreated feeds is the resulting low delta coke operation and low regenerator temperatures. We have observed regenerator temperatures dropping to 1220°F (660°C) and lower the regenerator can become limiting in achieving satisfactory coke combustion kinetics to the extent excessive afterburning leads to regenerator internals’ temperature reaching design limits. Maintaining the unit within “acceptable” heat balance range therefore becomes a major consideration. A number of operational adjustments can be undertaken to offset low regenerator temperatures including increased reactor temperature, increased unit catalyst activity, suboptimum stripping steam rates, and recycle of heavy cycle oil and/or slurry streams. Considerations to increasing the cutpoint/endpoint of the FCC feed should also be given as should elimination of 650°F- boiling range material (light gas oil) in the feed.
Some refiners have resorted to using continuous firing of the air heater or torch oil. Further options include a fired feed heater. The economics of fired feed heater versus continuous operation of the air heater should be evaluated on a case-by-case basis. An alternative technology offered by UOP is its RxCat™ technology, which decouples the traditional heat balance by recycling a slip stream of spent catalyst back to the reactor riser and permits variable fraction of spent catalyst recycle to achieve the desired minimum regenerator operating temperature. UOP utilizes RxCat™ technology in its new unit designs and revamp applications for low delta coke operations.
A risk of carbonate stress corrosion cracking (CSCC) exists in certain areas of FCC units running heavily hydrotreated feeds having sulfur levels below 1,000 wppm (weight parts per million) or 0.1 wt% (weight percent). This leads to more basic sour water in the 9 pH to 10 pH range due to a higher ratio of feed nitrogen-to-sulfur than exhibited by non-hydrotreated or less severe or mild hydrotreated feeds. UOP specifies “special” post-weld heat treatment (PWHT) requirement for units with feed sulfur ≤ 0.1 wt%. Application of “special” PWHT includes all of the wet gas compressor system in hydrocarbon sour water services (piping and equipment) from the top half of the main column through the absorbers and stripper in the gas concentration unit.
ROSANN SCHILLER (Grace Catalysts Technologies)
Severe hydrotreating of the FCC feed offers a mix of benefits and challenges for the typical FCC operator. Benefits can include dramatically lower sulfur content in products, lower flue gas SOx (sulfur oxide) or NOx, and improved yields; however, the price for these benefits is often a dramatically lower coking tendency of the feedstock. Many units which operate with severely hydrotreated feed struggle to make enough coke to maintain heat balance within unit circulation constraints. In addition, one may see slurry yield decrease to minimum acceptable levels, increased bottoms circuit fouling due to the lower volumes, heat removal limits in the gas concentration units due to higher volumes of light and wet gases, and lower overall product olefinicities. To counteract that challenge, several operating changes are possible.
These include:
• Use of Higher Activity FCC Catalyst: For units which will run severely hydrotreated feed for long periods of time, reformulation to a higher activity FCC catalyst is often the most cost-effective means of increasing the e-cat activity and bringing the unit into heat balance.
• HCO (heavy cycle oil) Recycle: HCO can be recycled to the reactor to aid in additional coking and to reduce the heat requirement on the reactor side. This strategy causes an economic penalty when the unit is operating at maximum fresh feed rates, as fresh feed will need to be backed out.
• Use of Regenerator Torch Oil: Torch oil is often used in the regenerator to add additional heat. However, the severe hydrothermal environment, coupled with the high velocities near the injection point(s) creates a very challenging environment for FCC catalyst particle integrity. In addition, many refineries use LCO material as torch oil, which is a substantial hidden cost.
• Use of Fired Air Heater: Some units will activate the fired air heater to reduce the heat requirement in the regenerator. In some cases, this air heater does not offer a great deal of flexibility in its duty, so its use can “swing” the unit from very low regenerator temperatures to much higher regenerator temperatures.
• Reduction in Stripping Steam: Some refiners elect to reduce stripping steam, sending some unstripped hydrocarbon with the catalyst into the regenerator. While this is a viable source of heat on the regenerator side, it results in a net loss of total liquid volume, and unit profitability can suffer. Additionally, the hydrogen-rich unstripped hydrocarbons burn rapidly creating local hot spots which can deactivate the catalyst.
• Higher FCC Catalyst Addition Rates: For units that process severely hydrotreated feeds intermittently, catalyst reformulation may not be practical. However, a short-term increase to the FCC catalyst addition rate can increase the equilibrium activity and bring regenerator temperatures up, which will allow the unit to maintain heat balance.
Each of these methods should be evaluated for both its feasibility in a given refinery and for its economic impact to the plant. It is often the case that higher catalyst addition rates, or a high activity catalyst reformulation, are the most economically favorable option.
MARK ANDERSON (ThioSolv, LLC)
One change to expect is that the production of ammonia to the sour water will increase substantially. Each ton of ammonia in the sour water increases the load on the Claus by four times it weights in H2S. Claus capacity is not measured by the rate of sulfur captured; the equipment is sized for the gas flow, not the sulfur rate, and H2S in sour water produces as much tail gas flow as about three times as much H2S alone. To deal with the added load on SRU, consider diverting the sour water stripper gas to a SWAATS (sour water ammonia to ammonium thiosulfate) process to convert it to ammonium thiosulfate fertilizer, freeing up Claus capacity for the incremental H2S produced from the VGO hydrotreate.