Question 78: What procedures (maintenance and operational) are being used to minimize risk when swinging the blind between the reactor/main fractionator?
INKIM (PETROTRIN)
There are two scenarios to consider: shutdown and startup. I will address the shutdown scenario first.
For the shutdown scenario, catalyst is de-inventoried from the reactor and regenerator systems, and the main column and reactor are cooled down to 350°F. There are certain operational conditions that must be satisfied before the blind is installed. The reactor is gas-freed and being purged with steam. The vapor line blind flanges are soft-bolted and hot-bolted in preparation for the removal of the spacer and installation of the blind. The blind on the warm-up line is removed to allow the reactor to continue to purge and cool when the vapor line blind has been installed. The hydrocarbon level in the main column will be lowered to minimize risk of flashing and fire and to prevent any hydrocarbon vapors from coming in contact with Maintenance personnel. At this time, steam would be introduced via the try lines to provide a purge.
The pressure in the main column and the reactor will be reduced to a minimum, below 1 psi (pound per square inch), and the over-pressure valve would be placed in manual mode to lower the steam and gas from the main column to go towards the flare. The installation of the blind is a fresh air mask job, and all personnel involved would be required to wear the requisite PPE (personal protective equipment). The fire equipment would be available in the vicinity for the activity of installing the blind. The installation of the blind is done via a chain block operation. Once the blind has been installed, gaskets are placed on either side of the blind. Prior to their installation, gaskets are normally wrapped with a GRAFOIL™ material to keep them intact during the installation.
For the startup scenario, this is done after the regenerator has been dried out. The temperatures in the main column and the reactor would have been brought up: the main column to at least 250°F; the reactor to 300°F. At that time, again, the levels in the main column would be lowered to prevent any risk of flashing, fire, and any contact with Maintenance personnel. We would also reduce the reactor pressure down to around 1 psi. Similar safety precautions will apply as for shutdown; e.g., PPE, etc. Once the blind has been removed for startup, the spacer will be installed and flanges guaranteed; and then, we will continue with the normal startup process.
LARSON (KBC Advanced Technologies, Inc.)
In this particular situation, we considered that in general, some people may be changing this blind in what is called a hot operation. This was covered in an MPRA (Munich Personal RePEc Archive) 2010 Q&A Session. This procedure evaluates the benefits of using the blind in the open position all the time, which we have represented on the slide.
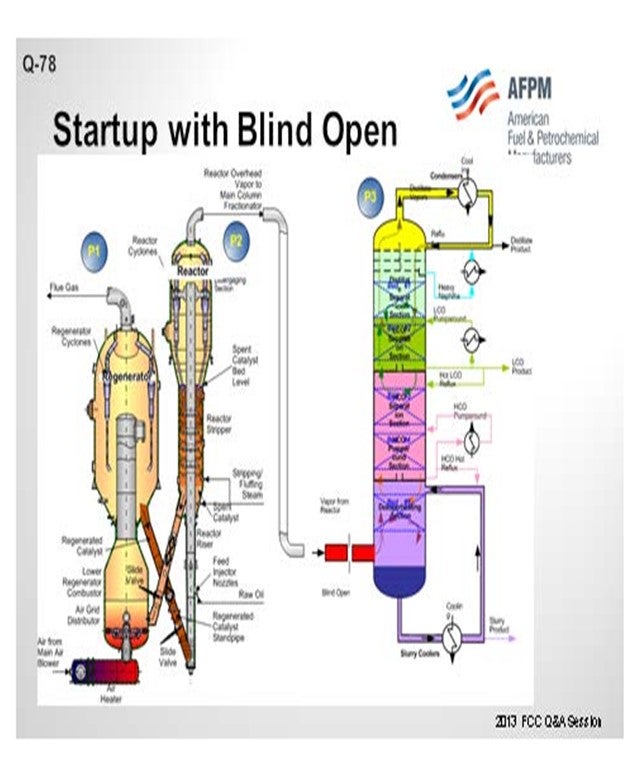
We suggest that when Maintenance turns over the system to Operations, the unit must be air-free. In general, you will have refractory work after turnaround, so you must dry out the system. The blind can be in the open position as you continue to dry out the circuit with the blind open and let that air go all the way through the fractionator to further dry out the system. There will be a point in time when you will you need to introduce steam to air-free the system. That additional water is not a problem.
Then, as you have the system “air-free,” the next step will be to establish a catalyst seal. By the way, I am not really trying to represent anyone’s cat cracker here as a commercial, but you will want to establish a catalyst seal in the stripper and in the regenerator to isolate those vessels. As soon as you have circulated catalyst to establish a catalyst seal, you can then continue to heat up the reactor regenerator with torch oil and circulating catalyst. With the blind open, you continue to put oil in the main column as you would normally do to heat up the fractionator. The key step in this is that when you are doing this process, you will want the pressure gradient such that the pressure in the fractionator is over the reactor, which is over the regenerator.
This pressure balance allows you, with the blind open, to have any vapor that may come through the system to move back towards the reactor. You are burning torch oil in the regenerator, so it is not a problem if a little hydrocarbon vapor would actually back into the system. Having done this myself, I know that we did not see any hydrocarbon vapor back into the system. This procedure works fine. When we started up the unit this way, we saved about 16 hours. If you read the some of the material in the 2010 transcript, you will see that there is anywhere between 16- and 48-hours’ worth of time savings as a result of leaving the blind open during a startup.
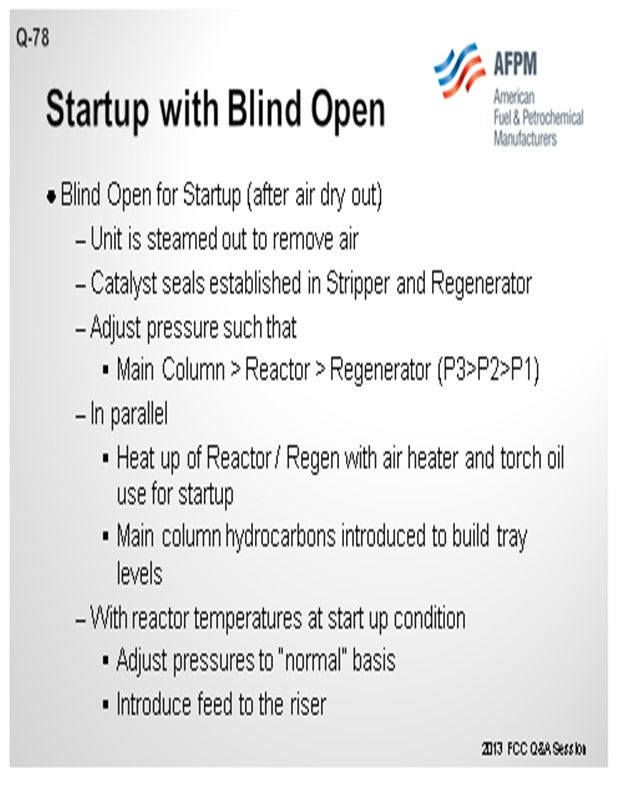
MICHAEL WARDINSKY (Phillips 66)
Phillips 66 operates 15 FCC units. Some of them follow an open blind startup procedure, and others have blind devices that are initially closed during startup. There are advantages and disadvantages to both approaches. I also want to point out that on the open blind procedure, you will really have to be careful if you are curing refractory on the converter side. If that hot flue gas gets over into the main fractionator (frac) bottoms where you have coke in bottom pumparound lines, you could start a fire down there and destroy those bottom pumparound lines. The other issue is that with the open blind procedure, we really advocate keeping the reactor pressure elevated above both the frac and regenerator (regen) sides; because if your blower trips during that process, the resulting pressure gradient will drive hydrocarbons down into the regenerator. At that point, you will have hydrocarbons in your regen flue gas line, which could lead to potential safety scenarios.
LARSON (KBC Advanced Technologies, Inc.)
The other point I want to make is that we learned about this practice when it was presented in 2010 as primarily a safety issue. At that time, a lot of people had installed delta valves or other devices in the circuit, so they were not exposed to flipping a blind and a hot service and potentially having an event. Unfortunately, I have seen a situation where this was done, and a flange fire occurred. Luckily, no one was hurt. So, I have firsthand knowledge of the value of doing this in a way that it is safe for personnel and reliable for Operations.
CHRIS GREEN (Marathon Petroleum Corporation)
When you are starting up with the blind in the open position, are there any risks around pyrophoric iron sulfide residue left in the packing if you have a packed fractionator? That would be worth discussing before you put steam through that system; essentially, when you still have warm air there.
LARSON (KBC Advanced Technologies, Inc.)
Yes, you should have that consideration. I should have prefaced my comment by saying that I considered this after a turnaround where you would have gone into the unit, done sufficient cleaning of critical pieces of hardware to eliminate the coke, and removed the coke from the packed section. We would probably recommend a slightly different procedure if you are going to have a blind opened without having the unit clean prior to this action. Absolutely, you have to consider the pyrophoric material and how you might manage it. The point is that I would still try to find mechanisms, either through a valve or with the blind opened, to where you do not expose personnel to poor safety situations.
J.W. “BILL” WILSON (BP Products North America Inc.)
You really do need to worry about that pyrophoric iron because there has been at least one fire of which I am aware where we literally burned down the main fractionator. It was pyrophoric iron and hot air that ignited.
CATHERINE INKIM (PETROTRIN)
There are two scenarios to consider: shutdown and startup. Let’s address the shutdown scenario first.
A. For the shutdown scenario, the vapor blind is inserted after the main column and reactor are cooled down (below 350°F) and the catalyst is de-inventoried from the reactor and regenerator systems. To insert the blind the following operational conditions must be satisfied:
1. Reactor is gas-freed and being purged with steam.
2. The main column is cooled, and the catalyst flushed from the system by circulating and flushing with gas oil.
3. The vapor line blind flanges are soft-bolted and hot-bolted in preparation for removal of the spacer and the installation of the vapor line blind.
4. The blind on the warmup line is removed as the warmup line to the flue gas stack is to be opened to allow the reactor to continue to purge and cool when the blind is installed.
5. The gas oil circulation is stopped and the level in the main column pumped away to a minimum. This is done to minimize the volume of hydrocarbon in the vessel and therefore minimize the risk of flashing and fire, as well as prevent any oil from coming in contact with maintenance personnel. Steam is then introduced to the column via the try lines to provide a purge.
6. Steam is opened on both sides of the vapor line blind to form a steam curtain, and the valve on the warmup line is cracked open.
7. Reactor pressure is reduced to a minimum (0.5 psi to 1 psi) by shutting down the MAB (main air blower), if in service, and reducing the steam flow to the reactor.
8. The main column pressure is reduced and maintained at less than 1 psi by reducing the gas makeup to the main column to a minimum and opening the overpressure valve to flare. At this time, the overpressure valve is operated on manual mode to ensure continued flow of gas and steam from the column to the flare system.
9. During the installation of the vapor line blind, the purge to the reactor instruments is changed from gas to air.
During normal operations, the blind is usually stored in close proximity to the vapor line flanges and is protected against weather elements to minimize corrosion. A chain block operation is used to insert the blind with new gaskets installed on both sides of the blind. Prior to the job being commenced, each gasket is wrapped with GRAFOIL® tape (graphite tape) to assist with keeping it intact during installation. Three gaskets are made available onsite in the event that one is damaged.
Contractors used for installing the blind are usually rotated so that there is more than one contractor with experience in the installation and removal of the blind. The blind installation is a fresh air mask operation as hydrocarbon vapor can be present and usually lasts less than 45 minutes with a crew of seven people. During the blind installation operation, all other maintenance activities in the vicinity are suspended and fire equipment – steam hoses and dry powder extinguishers – are made easily available. Insulation jackets are used to cover any hot lines that contractors may come into contact with during this operation.
B. At startup, the blind is usually removed following dryout of the regenerator. If the unit is new, hot air can be used to dry out the reactor prior to blind removal. If the startup is from a turnaround and there is coke present, preliminary reactor dryout is done with steam prior to the blind removal; however, the reactor dryout is completed when catalyst circulation is being established. To remove the blind, the following operational conditions must be satisfied:
1. The main column must be air-freed and inventoried with gas oil, circulation established, and circuits dried (i.e., all water removed). Temperatures must be warm enough to prevent steam condensation when the blind is removed. Efforts are made to achieve a main column overhead temperature of at least 250°F.
2. The reactor should be steaming to atmosphere via the warmup line with the reactor temperature being maintained above 300°F.
3. One hour prior to removing the blind, the purge to the reactor instruments should be changed from air to gas.
4. Once the required reactor and main column temperatures are attained, the MAB is shut down to allow for the reduction of the reactor pressure while maintaining a negative vessels differential pressure in preparation for blind removal.
5. Prior to the blind removal, the main column gas oil circulation is stopped and the level in the main column pumped away to a minimum. This is done to prevent any oil from coming in contact with maintenance personnel during blind removal. At this time, steam is introduced to the column via the try lines to provide a purge.
6. Reactor pressure is reduced to a minimum (0.5 to 1 psi) by reducing steam flows.
7. The main column pressure is reduced and maintained at less than 1 psi by adjusting the gas makeup to the main column and the overpressure valve to flare. At this time, the overpressure valve is operated on manual mode to ensure continued flow of gas and steam from the column to the flare system.
8. Steam is opened on both sides of the blind to form a steam curtain, and any accumulated condensate is bled from the vapor line via the bleed immediately upstream the blind.
Similar safety precautions and PPE are used as for blind installation. On removal of the blind, the spacer is installed in its place using two new gaskets. Once the flange is guaranteed, steam rates are increased and circulation of oil in the main column is reestablished. The warmup line valve is shut, its blind installed, and the reactor pressure increased in preparation for restarting the MAB.
MEL LARSON (KBC Advanced Technologies, Inc.)
The basics of this question suggest that the blind is being opened in a “hot” operation. This was partially covered in the AFPM 2010 NPRA Cat Cracker Seminar during the Operations/Technology and Reliability/Maintenance/Turnaround Q&A. The preferred option to minimize risk with improved personnel safety on startup is with the blind open.
Note that this procedure focuses on reduced personnel risk from opening the blind in a hot hydrocarbon system; thus, safety is priority No.1.
A general procedure is as follows:
1. When Maintenance turns over the system to Operation, the unit must be air freed. If refractory work was completed, there will be a defined stepwise heat up and hold sequence for the refractory repairs. Consider using the heat of the dryout procedure going all the way through the column (blind open) to further “dry out” the system.
2. After the refractory dryout is completed and the blind is in the open position, continue with the standard startup procedures to air-free the system.
3. Establishing catalyst seals in the reactor stripper and sufficient level in the regenerator are key steps in the process. With catalyst seals established, procedural changes can be utilized that adjust the pressure of the system to simultaneously heat up the reactor, regenerator, and main column with the blind in the open position.
4. Considering elevation difference of vessels and transfer lines, it is possible to prevent oxygen to the fractionation system by pressure adjustment. In general, consider a pressure profile such that main column pressure is greater than reactor pressure which is greater than regenerator pressure.
5. The unit heat-up process continues per the normal use of the air heater, torch oil, and catalyst circulation.
On the fractionator side, normal oil-in and heat-up can continue in parallel to the regenerator and reactor heat-up. This can be achieved as the pressure gradient is aimed toward the regenerator minimizing the possibility of oxygen into the fractionator. Once the systems have achieved the normal temperatures and feed to the riser is the next step, the unit the pressure profile can be adjusted to “typical” startup, followed by the introduction of feed in the normal manner. Companies indicate that between 24 to 48 hours of improvement in startup timing and lower risk to personnel from using an open-blind startup. There are a number of companies that have installed a valve in the reactor vapor with positive results. For more an in-depth discussion on valves, consider reviewing the transcript from 2010.
The blind or valving can be used as a means to isolate systems during maintenance. However, unit startups should avoid a closed blind with “hot” opening procedure in startup.