Question 74: How effective are the following decoke methods in a delayed coker furnace: online spalling, mechanical pigging, and steam air decoking?
HERLEVICH (Marathon Petroleum Corporation)
The way the panel decided to answer this question was for me to give an overview of the different methods and a few of the pros and cons. Then one of the other panelists will present his actual experience. The mechanical method employs metal studded pigs which are pushed in water. You typically have multiple runs in several directions because of the changing sizes of the heater tubes. Water quality and pressure indicate the cleanliness of the tubes. The whole process is typically accomplished in 18 to 24 hours. One advantage is that this process removes all of the coke.

The disadvantages of the mechanical method are it requires a heater shutdown and specialty contractor, and there is a significant amount of operator and maintenance involvement.

The next method is steam/air decoking. Here the coke is spalled with a high steam rate at elevated temperatures, and then air is introduced to burn the residual coke. You accomplish this method in 24 to 48 hours; so, it takes a little bit longer than the other way. The advantages are that it removes all of the coke again and the firebox does remain hot.

Then there are several disadvantages. The steam/air method requires a heater shutdown. There are environmental permitting issues for the emissions generated from the coke combustion. There is also the potential for tube damage. If you get a really hot spot, the metallurgy may be affected. It is hindered by any inorganic foulants, and you will have residual foulant in the tubes. Any residual will be problematic in the next cycle. This method requires significant operator and maintenance effort, as well as a fair amount of technical oversight. We station engineers on shift monitoring the combustion.

One additional point does not show on the slides is that we have had issues with combustion products around nearby structures. Care must be taken because there are often people working in the vicinity and the combustion sources are at relatively low elevations. So, there are safety issues that need to be mitigated. I can remember one experience where people working in a column nearby had to stop their work after the continuous air monitoring system indicated problems. Here combustion products were naturally drafting into the open distillation column. Please be mindful of these hazards.
The last method we have is online spalling. This is more popular in our plants. We keep the heater running and then thermally shock the tubes by varying the steam and firing rates. Typically, you would have a multi-pass furnace configuration so that one of the sections is online spalling while the other sections remain charging the unit. The advantages are that the overall coker operates in parallel; the method has the shortest overall time from start to finish; there is no waste generated; and, the operators can completely execute the procedure. Our engineers are used to determining when it is time to spall, but the operators execute the procedure quite well.

The disadvantage of the online method is that it achieves the lowest end-of-run temperatures. Unlike the mechanical methods, heater tubes are not being physically swept; so there could be some residual materials. The online method requires more frequent spalling intervals for that very reason. You can get tube and u-bend erosion because of the solids that are flaking off and then flying along at very high velocity as they pass through all downstream tubes and into the online drum. There is also a potential for tube plugging if a large chunk flakes off.
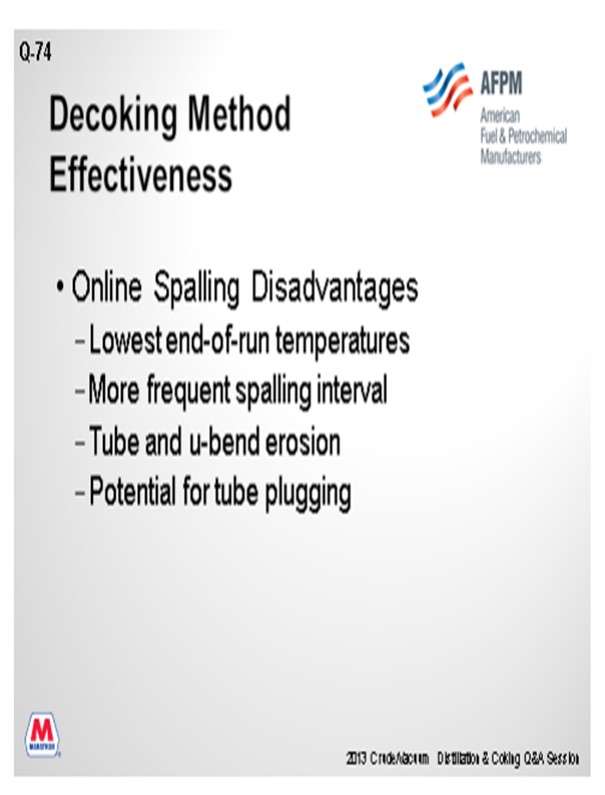
PRIBNOW (CITGO Petroleum Corporation)
At CITGO, we actually perform all of those methods. We also do an offline spalling method, which is a modified steam-only decoke. If we want to measure effectiveness, we look at performance effectiveness. We also look at the cost in dollars for the company effectiveness.
Performance effectiveness: When we look at our startup run’s tube skin temperatures, mechanical pigging wins. Mechanical pigging scrapes that tube to bare metal. Tubes are like new again. Steam air decokes are the second most effective, but inorganics are left on the tube wall, which can be seed sites for coking. The third most effective technique is online or offline spalling. This is just from a cleanliness and effectiveness perspective.
Depending on your heater design, you may or may not be able to do some of these different methods. It depends if your heater has U-bends as to whether or not you can perform mechanical pigging. The bottom line is that the economics of each coker should be evaluated based on your oil-to-oil duration, how well the decoke can be executed, and which is the most cost-effective method. For example, at CITGO, we have four cokers, and each heater method is different. One heater utilizes mechanical pigging; one likes to steam air decoke; one, online spalls; and, one, offline spalls. It is not that we cannot decide; it’s about the economics. I think it is more about what is right for your coker. You can do an economic evaluation and evaluate your tube life; because with mechanical pigging, there is some potential of scoring tubes and shortening your tube life. Just evaluate that, and then go with what you feel is best, economically, for your company.
One comment on steam air decokes: You must have good instrumentation. There is a lot of risk with heating up tubes using this method. If there is not adequate instrumentation, accurate monitoring, or experienced engineers watching the decoke, you can do damage. We have brought in IR (infrared) scanning companies and monitor the steam air decokes with an IR gun throughout the whole process. That helps us watch the burn go through the tubes and push to make sure the operators are not slacking off and prolonging the outage. So, I think that extra monitoring helps prevent damage and minimizes downtime.
We have two identical heaters. We performed a mechanical decoke and a steam air decoke side-by-side. We sent a camera in the tubes and could see inorganics and coke were left on the inside diameter of the steam air decoke. This material can potentially be seeds to coking. That is the reason why we, at Lemont, feel a mechanical decoke is more effective than a steam air decoke for our heaters. We observed a 10% improvement in mechanical decoke run-length compared to the steam air decoke on that run.
Lastly, we have employed smart pigging. We have utilized smart pigs which can tell how much coke is left in the heater tubes. Inspectors will use smart pigs to measure the tube wall thickness. One concern with mechanically pigging is tube wall thickness. Earlier we talked about seeing coking in different places in your heaters or higher coking rates than normal due to tight oils. Yes, we have observed this also, which is why we used the smart pig. We saw that we had more coking in the convection section and had to go back and decoke further. Smart pigging is more expensive, but it is one way to tell how much coke you have left in your tubes.
SRIVATSAN (Foster Wheeler USA Corporation)
I want to highlight just one point. In terms of maintaining feed throughput, online spalling is probably the most effective technique as you remove only one pass at a time. Also, the duration to spall a pass is generally shorter than that of the other decoking methods. Over the years, we have modified our online spalling procedure. It is extremely effective in restoring clean tube metal temperatures on our proprietary double-fired furnace. As illustrated by the results shown on this slide, we start the online spall when the skins reach about 1200°F to 1250°F; and then after you complete the spalling procedures, the clean tube metal temperatures are about 900°F to 950°F.
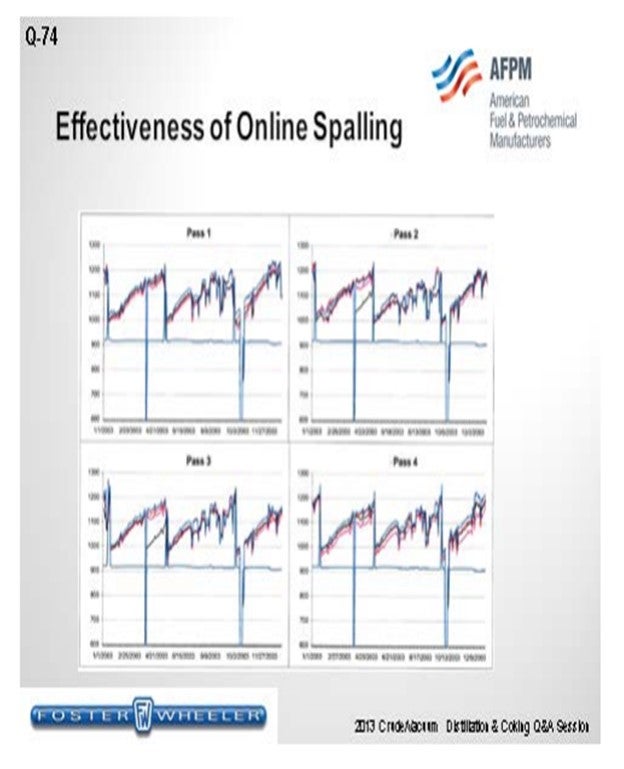
If you have a single-fired heater, it is possible to see the ratchet effect after every spall; that is, after every subsequent spall, you will not be able to get to the same tube metal temperature as the previous spall. You will eventually have to shut down and do a steam-air decoking or pigging. Since there is a more uniform heat flux in a double-fired heater, we have observed that we are able to hit the clean tube metal temperature each time. We know of refiners who just do an online spalling and shut the heater only during turnarounds.
JOHN BASING (CVR Energy, Inc.)
Are there any type of heaters or experiences that would justify definitely not trying the online spalling? Have you used it as a stopgap in between piggings?
EBERHARD LUCKE (CH2M Hill)
My experience as an operator is from working with a coker heater that was two-pass in one box. In that case, it was really difficult to separate the two passes and then do online spalling. We did manage to get it done, but efficiency was quite limited because we could only separate the radiation part. The convection section still stays. It was combined and generally stays in service, even with one pass online. So it is best if you have a bigger unit or two separate heaters. If you have just one big heater with two passes, online spalling is probably not the best way to go.
HECTOR GAMBOA-ARIZPE (CITGO Petroleum Corporation)
Is there an upper limit on the amount of water you would use during an online spall so that the coke morphology is adversely affected where you run a safety risk of not being able to cut it too hard; or worse, if it gets too soft on you and changes in oil properties?
SRIVATSAN (Foster Wheeler USA Corporation)
We have an elaborate procedure during which the water rates are varied during the spalling. I can put you in touch with our Operations folks who do this regularly.
HECTOR GAMBOA-ARIZPE (CITGO Petroleum Corporation)
I mean at Corpus Christi, we prefer to do the online spall. We do maybe three online spalls and then the steamer decoke, roughly in that frequency. I am just curious if there is an upper limit not to exceed; because if you do the procedure, there will definitely be a problem.
SRIVATSAN (Foster Wheeler USA Corporation)
I am not aware.
SRINI SRIVATSAN (Foster Wheeler USA Corporation)
These comments are primarily based on Foster Wheeler units having Foster Wheeler-designed delayed coking heaters. Please also refer to the 2005 Q&A and Technology Forum P&P presentation on “Fired Heater Design and Decoking Techniques” for more information on this topic.
Online spalling is the best selection for maintaining coker throughput as it only removes one pass from process operations at a time for spalling. The duration for spalling a pass and the whole heater is generally shorter than other decoking methods as the heater does not need to be shutdown. However, the effectiveness of spalling is dependent on the type of heater (single- or double-fired) and the spalling procedure used. Single-fired coker heater can have limitations on the recovery to clean tube metal temperature (TMT) due to less uniform heat flux as a result of burner firing from one side only. We have seen a ratchet effect in single-fired heaters where the after-spalled ‘clean TMT’ gradually rises on each spall until the time between spalls requires another type of decoke operation. Double-fired coker heaters with more uniform firing achieves a ‘near-new’ TMT almost every spall. As mentioned before, the spalling procedure/operation is the key to the effective spall. Foster Wheeler has evolved the spalling operation such that some DCUs run essentially without shutdown for five years plus between turnarounds using only spalling operations. The following plot shows the effectiveness of online spalling on a proprietary Foster Wheeler double-fired heater.
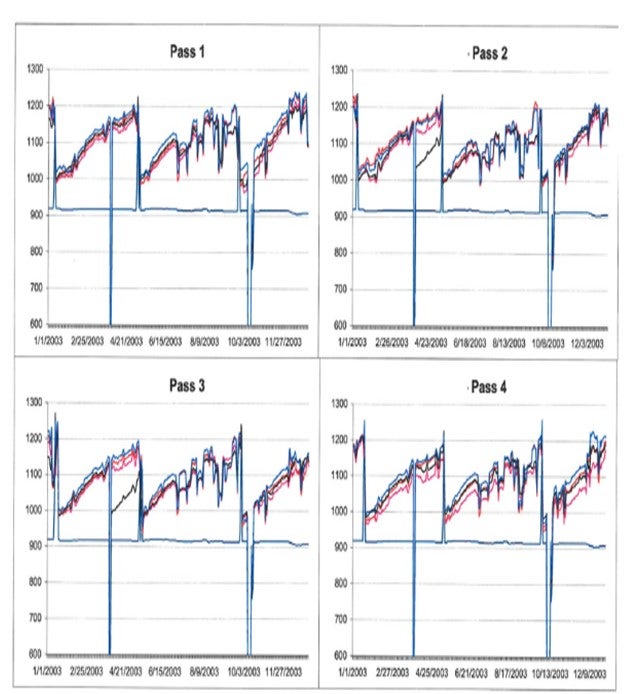
EBERHARD LUCKE (CH2M Hill)
The original heater decoking method – steam air decoking – requires the operators to follow a very strict procedure to achieve a highly effective decoking. This decoking method has been proven in removing organic material like coke/hydrocarbon. In the past years, the processing of heavy oils derived from tar sands and similar sources brought inorganic materials into the refinery systems which found their way into the coker heaters. Those materials cannot efficiently be removed with steam air decoking. For that reason, many operators switched to the mechanical decoking method: the pigging of the heater tubes. The latest heater designs and procedures allow for very quick and efficient heater pigging. The only area of concern could be deformation of heater tubes over time (more oval than round) and areas/pockets of coke laydown that are not cleaned properly. However, use of smart pigs and documentation of heater tube conditions and deformation will mitigate most of these concerns.
The other concern I have heard is that of scratching the internal surface of the tubes, leaving an area that is more prone to fast fouling and coking and potentially thermal deformation. Online spalling is a method of decoking heater tubes while part of the unit stays in operation. There are various procedures for online spalling that can be applied depending on the unit/heater configuration. It is a very good tool to increase the heater runtime between pigging/decoking shutdowns, but it will never replace the need for steam air decoking or pigging. In most cases, online spalling can only be applied to the radiation section of the heater, not to the convection section (especially when the heater has a combined convection section for two radiant sections). Spalling also never removes all the scaling and coke laydown in the tubes; so the more often spalling is applied, the less efficient the procedure. In some cases it was reported that since the coke layer was in the heater for a longer period of time, pigging was more difficult and took longer. So in summary: Mechanical pigging seems to be the most efficient method, in most cases. Online spalling may be used to increase the time between pigging shutdowns.