Question 71: Is there any test method for performance evaluation of silicon-based antifoam agent used in coker?
DION (GE Water & Process Technologies)
Don mentioned the ASTM test procedure. It may also be beneficial to conduct elemental silicon loading. Silicone is a known molecule: dimethylpolysiloxane. The amount of elemental silicon introduced into the drum over a period of time can be tracked and compared with silicon in the distillate. Generally, the biggest step change to silicon loading is improving the chemical feed system. At the beginning of the drum cycle, little to no defoamer is required. Near the end of the drum cycle, copious amounts of defoamer may be required to prevent a foamover. Using a variable speed motor or solenoid valve on the feed system, with control at the board room, can reduce overfeeding the silicone, hence reducing downstream silicon poisoning concerns.
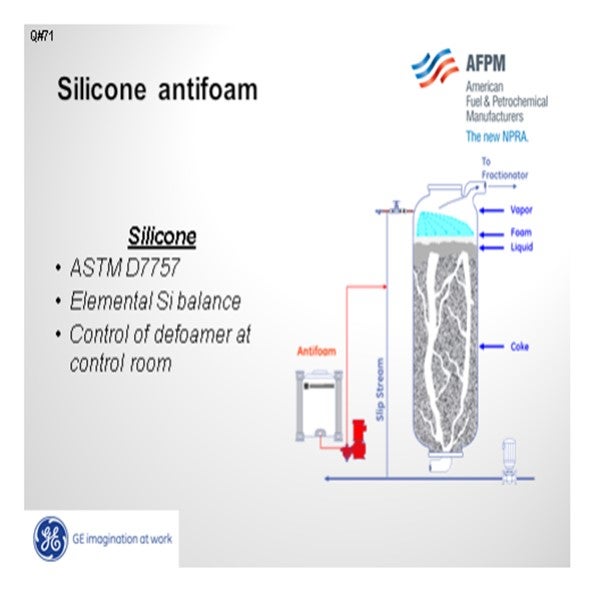
TRAN (Houston Refining, LP)
To test for silicon content in the coker naphtha streams, we use the ASTM D7757: the Standard Test Method for Silicon in Gasoline and Related Products by Monochromatic Wavelength Dispersive X-ray Fluorescence Spectrometry. Our main KPI (key performance indicator) is the amount of silicon loading on the downstream coker naphtha HDS (hydrodesulfurization) catalyst bed.
We track daily and monthly antifoam usages and compare them to industry low antifoam users. Typically, we are in the range of 1.2 to 1.5 gallons per thousand barrels of fresh feed versus 0.8 gallons per thousand barrels of fresh feed.
The coke drum foaming tendencies can vary greatly with resid feed qualities. For the resid feed with high foaming tendencies, our antifoam usage can increase by three to five times the normal antifoam usage. In these cases, we perform temperature ramp at the end of the coking cycle to stabilize the foam front and adjust unit charge rates and cycle time to achieve higher drum outages.
DION (GE Water & Process Technologies)
The standard for determining silicon content in gasoline and other products is ASTM D7757: the Test Method for Silicon in Gasoline and Related Products by Monochromatic Wavelength Dispersive X-ray Fluorescence Spectrometry. ASTM D7757 determines total silicon by monochromatic, wavelength-dispersive X-ray fluorescence spectrometry in naphthas, gasoline, RFG, ethanol and ethanol fuel blends, and toluene at concentrations of 3 mg/kg to 100 mg/kg.
In addition to measuring elemental silicon concentrations in fuels, the user of silicone antifoam can readily calculate the elemental silicon loading per drum cycle. GE Water & Process Technologies has a long history of providing state-of-the art silicone antifoam products, application procedures, automation packages, and onsite technical assistance.
LEE (BP Products North America)
We are not so sure about a test method per se, but one can look at the effectiveness of an antifoam agent if the drum is equipped with some form on continuous level monitoring. Monitoring silicon pounds per 1,000 bbl (barrel) of unit feed is a good practice to give a relative idea of dosing rates. One can also sample different product streams at various times while injecting silicon to try to give an idea of how much silicon the different fractionator products might have. With a continuous level indication or enough of the neutron backscatter points on the upper section of the coke drum, the decrease in foam layer when antifoam is added is really the only metric for showing that the antifoam is working.
ROGER METZLER (Baker Hughes)
Yes, silicon content analyses of the cracked liquid products can be measured by a variety of techniques. However, some of the Si fragments are volatile. Therefore, test methodology needs to allow for measurement of both volatile and nonvolatile Si. Baker Hughes analytical techniques measure both volatile and nonvolatile Si components in coker distillate liquid product streams. Baker Hughes FOAMSTOP™ Low Catalyst Impact delayed coker antifoam/defoamer can reduce Si contamination in these coker distillate liquid product streams. BASHAM (Marathon Petroleum Corporation) The glass coker apparatus at the University of Tulsa Coker Joint Industry Project (JIP) lab is used to measure antifoam effectiveness. The time it takes for foam to rise to a given level is measured after injecting a known quantity of antifoam. The longer it takes for the foam to rise, the better the antifoam performance