Question 70: What are the key areas to target when contemplating crude unit modifications to enable effective tight oil processing? In addition to these modifications, what other problem areas become evident once the actual processing begins?
HERLEVICH (Marathon Petroleum Corporation)
We run tight oil in six of our seven plants, and it is mixed in the basket of the other 10 to 20 crudes normally processed. Tight oils are not the predominant crude in most places, so we have not needed many modifications. In two instances, we did have tray fouling from drilling mud; so, we installed low fouling trays.
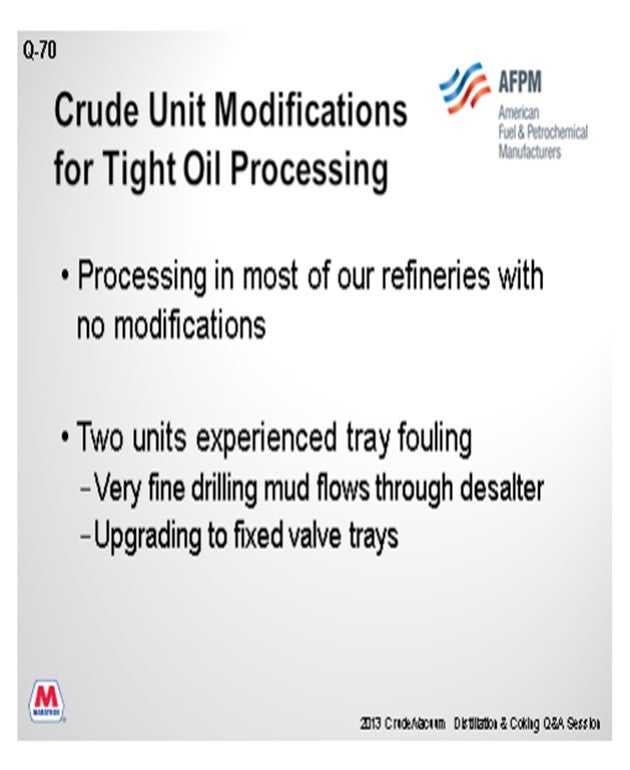
We have projects underway to increase the amount of tight oil received at two plants. The general theme is to install equipment to knock out water, a new pre-splitter, and heat exchange. One of the configurations will employ a pre-splitter for just the tight oils. We will take the overhead into the naphtha circuit and the bottoms to the desalter. One refinery also requires a gas plant expansion to process the incremental light ends.
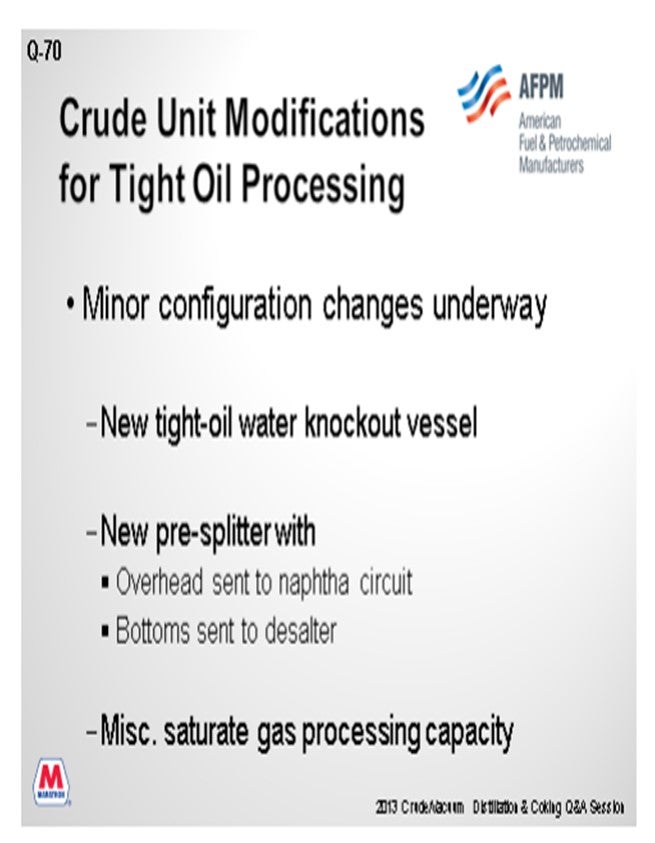
The next two slides were prepared with a larger question in mind: What happens directionally on all the units in the refinery when processing tight oils? I will not go over these slides right now because there is quite a bit of detail on them. The second slide is just the other half of the plant.
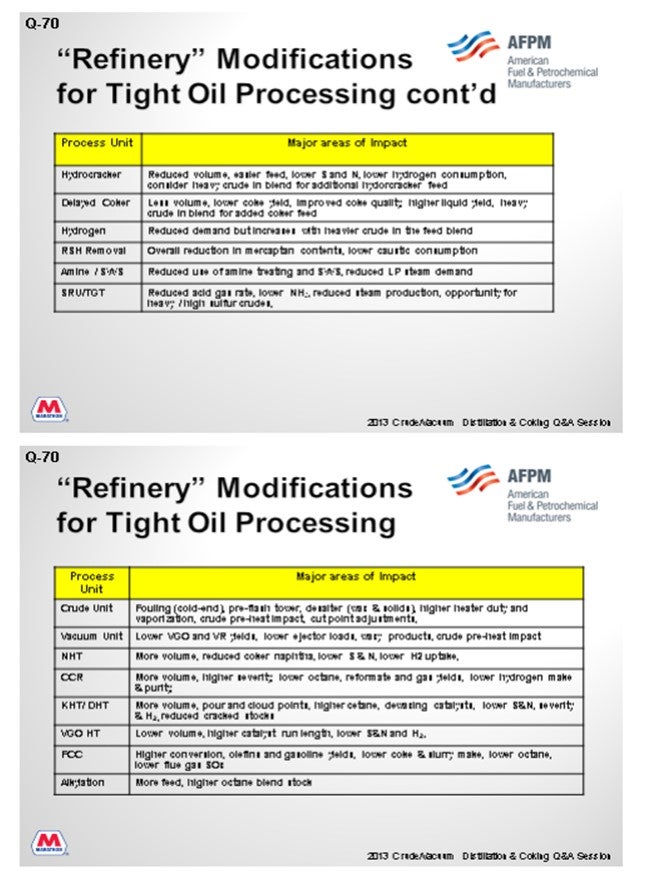
HODGES (Athlon Solutions)
Needless to say, there have been some interesting challenges discovered over the past several years of the running and processing of tight oils. I would like to offer another plug for the P&P sessions later on. Please check your program. There are two P&Ps that specifically address tight oil, and there will be a lot more information presented.
The biggest challenges really have to do with the unique composition of each of these tight oil's formation and the huge variation within a given field from cargo to the next. Often, tight oils are very paraffinic and have significant naphtha yields and very little resid production. If your normal slate is heavy blends, then your light ends processing ability might be inadequate to handle the higher naphtha yields.
Additionally, you might be forced to process blends of tight oils and heavy crude just to keep your coker running. Blending various crudes to meet the distillation profile, though, can often create compatibility issues with forced asphaltene precipitation. Some refiners, as was discussed earlier, have segregated crudes and tankage, added asphaltene inhibitors to the raw crude, and installed pre-flash drums or towers to reduce the light ends content in the hot pre-heat train. Less paraffins in the hot train, like C5 and lighter will induce asphaltene precipitation in the hot train.
Wax precipitation in the cold train has been observed as well. Wax inhibitors fed to the crude tankage or to the transportation of the crude can be used to address very severe issues. It is a good practice to use a simulation program to predict crude incompatibility and wax issues and then adjust your blends, if possible, prior to relying on chemical additives.
Since the gathering and distribution system for tight oils is still in its infancy, there is a significant amount of variation in the crudes that reach the market via trucks and railcars. I discussed this a few questions back as well. This often brings about huge variability in each of the trucks or railcars, depending upon which ranch it was produced on, and this fact demands that you develop a well-considered sampling testing and segregation plan. These shipments often require higher usages of H2S scavengers, which could create issues with tower fouling and increased COD (chemical oxygen demand) in the wastewater plant.
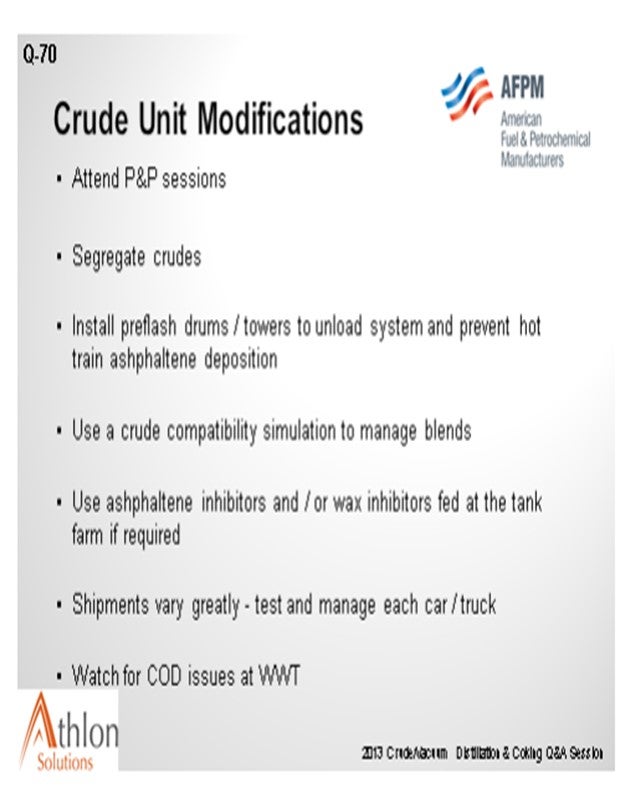
SRINI SRIVATSAN (Foster Wheeler USA Corporation)
A good overview of problems when processing shale oil was presented by C. Sandu and B. Wright of Baker Hughes in the July 2013 issue of Hydrocarbon Processing. Some of the problems include:
• Corrosion in crude units due to addition of amine-based products in upstream production;
• Problems due to incompatibility of asphaltenic crudes and paraffinic shale oils affecting all areas from tank farm to CDU. Concerns are in tankage, crude pre-heat, desalter operation (dark brine with potential high COD), heater fouling in both VDU and DCU, and exchanger fouling in both the cold and hot trains;
• Problems due to high solids loading affecting desalter operation; and,
• The quality of the finished products.
GREG SAVAGE (Nalco Champion Energy Services)
Refiners processing high levels of tight oil, 75% and greater, often are outside of design as tight oil contains very little gas and residual oil content. As a result, several refiners have experienced major shifts in the heat balance and velocity profiles on the pre-heat train. Evaluation of changes in crude cuts and the impact to pre-heat and furnace fouling is recommended for refiners considering processing high levels of tight oil. Changes in pre-heat configuration, blending with crudes in compatible ratios, and the use of antifoulant chemicals have reduced fouling rates for several refineries.
In general, the higher the desalter operating temperature, the lower the crude viscosity will be and the faster the coalescence of water droplets, which results in improved dehydration and desalting. However, some tight oils contain high levels of light ends, which can limit the desalter operating temperature due to pressure constraints. Refiners increasing the amount of tight oil processed are recommended to evaluate the impact on desalter operating temperature and performance.
As light tight oils may contain high levels of inorganic solids, a mud-wash study and solids handling evaluation is recommended when processing tight oil. Oily brine has been reported by refiners processing tight oil due to solids and low interfacial tension (likely due to surfactants in the crude). Refineries processing tight oil are recommended to review brine handling operations and develop strategies for reducing oil undercarry like the use of reverse emulsion breakers.