Question 68: After the operating temperature of the crude column overhead has been raised, corrosion rates in trim coolers’ inlets have increased greatly. Ultrasonic thickness (UT) measurement has indicated some increase in local thinning, but not to the degree of actual damage. What are new trends for monitoring corrosion in distillation columns and overhead condensing systems?
CLIFFORD (Motiva Enterprises LLC)
When we talked about this on the panel, we had some very interesting discussions. Generally speaking, increasing temperatures tends to help with most overhead corrosion issues as it moves you away from salt and dew point consideration. What we think is going on here is that if you increase the temperature, you may shift your dew point downstream of where you are designed to handle it. So it is important to understand your overhead conditions as much as we have been talking about on several of the previous questions. I am not going to go over too many details; but again, understanding waterwash modeling and ionic equilibrium modeling is important, as well as understanding where the corrosion may occur. But again, the localized conditions make it very difficult to predict the exact location and corrosion rate.
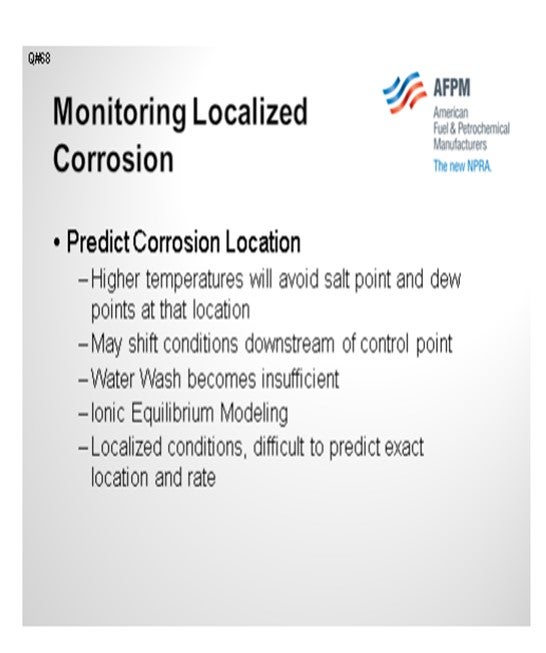
I have relied on some of my Pressure Equipment Integrity folks for some of these answers, and I apologize for my terminology. Using spot ultrasonic thickness (UT) measurement is a very difficult technique on which to rely for the indication of localized issues. There are some advanced NDE (nondestructive examination) techniques that can be used, such as radiographic testing, electromagnetic acoustic transducers, and guided wave testing. There are also various inspection companies that offer their own techniques. These methods can be used to take a larger sample size than the local spot UT reading, which can give you a picture of what is going on inside the entire pipe section.
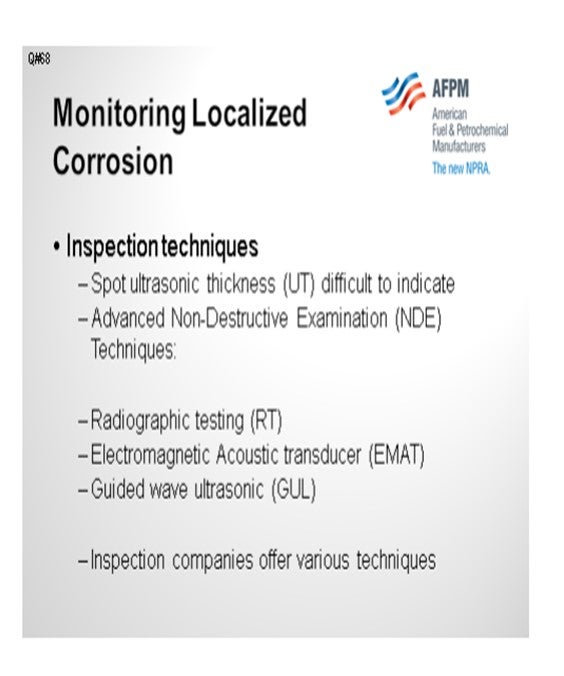
There are companies that offer online monitoring, which consists of field-mounted UT measurements that eliminate the variability of coming back six months later and getting the exact spot that you tested ultrasonically before. Hydrogen permeation plates, for example, detect the byproducts of corrosion, but all of these online programs are installed at fixed locations. They will not detect if the conditions upstream or downstream have changed and have thus moved the localized corrosion to an area outside of where you are monitoring. So, it is important to understand your overhead corrosion program and stay within your safe operating windows.
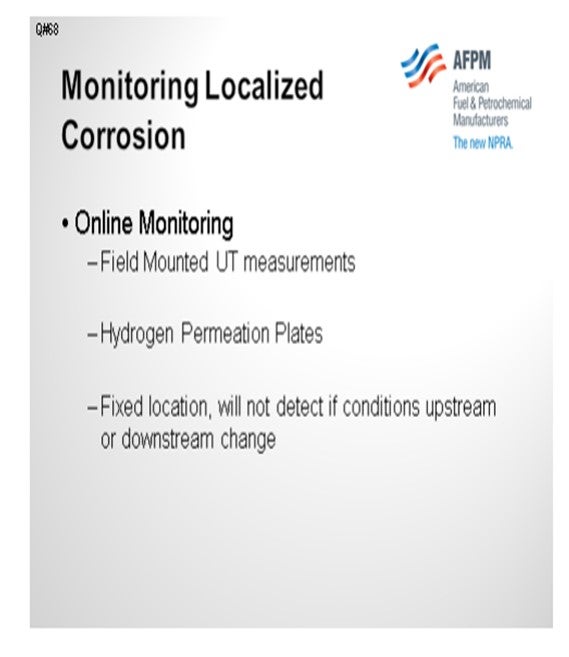
LEE (BP North America)
Online continuous chloride analyzers are now available in CDU overhead water service. We touched on it earlier. We have a couple of installations at BP refineries. This device provides a good view of the blips and excursions in the operating timeline where much of the corrosion damage can occur in a relatively short period of time. It also provides a means of being informed on operator adjustments and neutralizer addition that may occur between shifts and which might otherwise not be apparent when a spot reading is taken only every two or three days. Additionally, some of our sites have had good experience with the permanently mounted UT probes. We use the Permasense® wireless probes, like those that Steve mentioned. Readings can be taken as frequently as you want. Accuracy can be good, although sometimes we have had problems with the probes showing apparent growth and thickness.
DION (GE Water & Process Technologies)
GE developed a nonintrusive UT device through their Sensing & Inspection Technologies division. It is called GE Rightrax*. It is chain-mounted on the pipe with a temperature ceiling of 662°F around a pipe diameter of up to 42 inches. It can be strapped onto a pipe and relocated as desired.
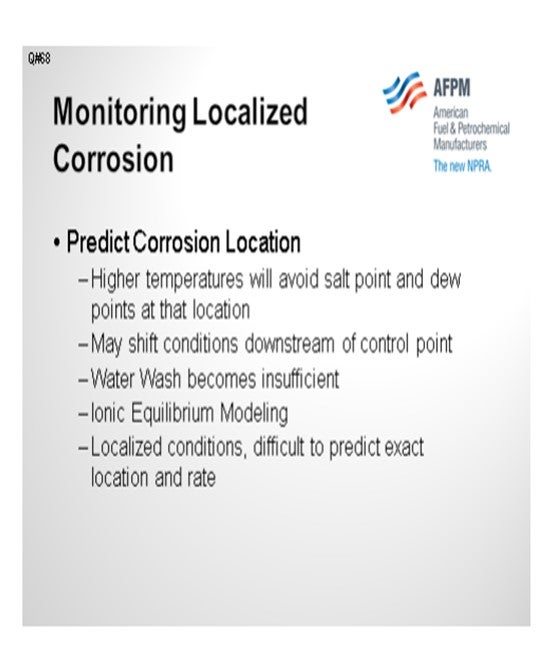
CLIFFORD (Motiva Enterprises LLC)
There are two aspects to this answer. The first is around predicting where corrosion may occur, and then the actual inspection techniques used to look for it. In general, maintaining high temperatures in atmospheric tower overheads is the preferred method for preventing corrosion because maintaining temperatures well above salt points and dew points is important. However, this question appears to be related to corrosion which is occurring downstream of the primary condensers, past where dew points or salt points are expected to occur. As will be discussed further in question 2003, it is possible to predict salt point and water dew point. With respect to that question, the concern is around the increase of the salt point relative to operating conditions and corrosion control. That phenomenon will result in fouling and corrosion at higher temperatures than anticipated. Those same techniques can be used to determine the effect on water dew points and waterwashes by increasing temperatures and/or process flow rates in those areas. In columns that have overhead waterwashes, increasing temperatures and/or rates, may result in an insufficient amount of liquid water remaining at the point of injection. This will result in localized conditions of high corrosivity as the injected water phase may evaporate leaving wet corrosive salts in its place. In cases where waterwash is not used, the increased temperature and material may shift the water dew point downstream of the design location. This will result in localized conditions until a sufficient amount of water is condensed. These localized conditions are very difficult to predict and spot ultrasonic thickness may not accurately represent the actual corrosion of the overhead system. Alternate methods which may provide more information than a spot UT include radiographic testing (RT), electromagnetic acoustic transducer (EMAT), or guided wave ultrasonic technology (GUL) to look for localized thinned areas. Many inspection companies and vendors will offer similar services.
If you do find a localized thinned area, there are methods to monitor these areas online. One technology allows for field mounting of UT thickness monitoring devices. In this fashion the variability of field UT measurements can be minimized. Another technique which can be employed involves hydrogen permeation plates. These plates detect the presence of hydrogen which is a byproduct of the corrosion reaction. While not a measurement of metal loss, it can measure if corrosion is occurring and based on conditions and rates, the rate of corrosion can be estimated.
DION (GE Water & Process Technologies)
Multiphase piping systems such as crude overhead systems often experience localized flow-enhanced corrosion/erosion effects and it is necessary to monitor these rates at critical locations (e.g., water drop out zones, slugging areas, bends and other positions that cause turbulence within the pipe). However, obtaining quality corrosion data in these areas frequently enough to adequately predict equipment failure can be difficult and/or costly (e.g., manpower, scaffolding, etc.). The ability to quickly and easily gather piping thickness data remotely allows for greater understanding of the system’s corrosion dynamics and better prediction of equipment failure timing. Traditionally, monitoring of corrosion and erosion or any other material loss process involves manually scanning pipe work, vessels and pipelines with an ultrasonic probe by a skilled operator. Additionally, high costs may be incurred due to the necessity of removing insulation, erecting scaffolding, shutting down equipment, and other complicated logistics to allow access to the area of interest. Several manufacturers supply nonintrusive online UT measurement systems that provide high-quality thickness data without the need to interrupt equipment integrity. The GE Sensing & Inspection Technologies division has developed an online UT measurement device called Rightrax* HT that can detect piping metal losses through a nonintrusive monitoring system that provides a direct measurement of localized material loss. The UT sensors are held in place on the pipe exterior using a chain-mounting coupling which requires no welding or penetration of the pipe and measures the actual wall thickness with sound waves instead of correlating voltage differences, as in traditional corrosion probe technology. The result is a repeatable wall thickness measurement, with measurement accuracy of 0.1 mils on piping up to 42-inches in diameter and temperatures up to 662°F. Additionally, the unique mounting technology of the Rightrax* system allows for the adjustment or movement of the monitoring system when necessary to accurately monitor corrosion activity as needed.
The selection of the appropriate location and orientation of the monitoring sensor is critical to the success of the monitoring process. The advantage over portable handheld devices is remote monitoring. Once these online UT systems are correctly installed at the appropriate location, there is no need to revisit the site and, subsequently, eliminates the need to send operators into hazardous environments or remote locations to measure wall thickness.
LEE (BP Products North America)
Online continuous chloride analyzers are now available in CDU overhead water service. We have a couple of installations at BP refineries. This device provides a good view of blips and excursions in the operating timeline, where much of the corrosion damage can occur in a relatively short time period. It also provides a means of being informed on operator adjustments in neutralizer addition that may occur between shifts, and which are not otherwise apparent when only a spot reading is taken every day or few days.
Additionally, some of our sites have had good experience with the permanently mounted Permasense® UT probes. These are the wireless probes and Permasense is the vendor. Readings can be taken as frequently as wanted. Accuracy can be good, although sometimes we have problems with the probes showing apparent growth in thickness.
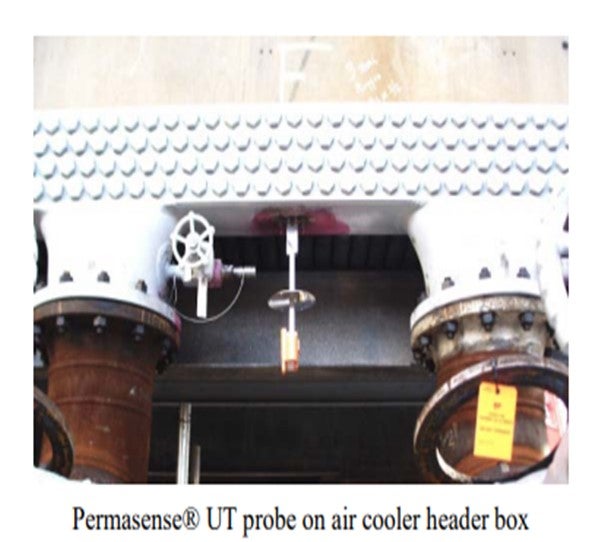
RANDY RECHTIEN (Baker Hughes)
To properly monitor corrosion in tower overhead systems, multiple techniques should be employed. Relying on a single method is insufficient to provide a complete picture of overall corrosion risk. In addition to traditional metal loss techniques (e.g., UT and ER probes), the use of hydrogen permeation measurement has proven successful in monitoring corrosion activity, particularly in localized areas.
Frequent analyses of overhead drum waters must also be performed to capture variations in contaminant levels. Recent improvements in online analytical equipment allow for nearly “real-time” feedback on variations in pH, chloride and iron levels in the drum water. The measured values from these analyzers can then be used to frequently and properly adjust treatment additives to improve corrosion control. Combining the output from these techniques with Baker Hughes’ TOPGUARD™ Corrosion Monitor ensures that corrosion control programs are performing as desired.
DENNIS HAYNES (Nalco Energy Services)
A new piece of equipment used for looking at overhead systems has been designed by Nalco that combines other components with an automatic analysis for iron content in overhead condensate analysis to be able to evaluate changing trends in overhead systems. A company called Permasense® also has developed an online UT device for measuring corrosion and evaluating rate changes for process equipment.