Question 67: We have an atmospheric overhead system with inadequate waterwashing,and we experience fouling and corrosion issues in the bundle. What might be the pros and cons of making a bundle modification or installing direct water spray into the shell side of the atmospheric tower overhead condenser in terms of underdeposit corrosion and bundle life?
SHELTON (KBC Advanced Technologies, Inc.)
We would not recommend direct water sprays into the shell, regardless of whether this is the first overhead condenser, because direct sprays can cause many problems, including erosion. This is why vapor inlet nozzles have impingement plates in shell-and-tube heat exchangers. Solids may also precipitate, causing pressure drop problems and underdeposit corrosion. Typically, washwater is injected into the crude tower overhead line. I used quills so it would fit on the slide, but vendors supply sophisticated spray nozzles for good distribution. Mixing is important, but identifying the optimum injection point is critical. In this case, it is probably a crude overhead condenser; however, the entire overhead system should be modeled. Injection points vary for cold versus hot reflux systems. There can be combination air coolers, water trim coolers, or air-only coolers. Some overhead systems have banks of air coolers and then several water trim coolers in series. So, the optimum injection point must be determined by simulation.
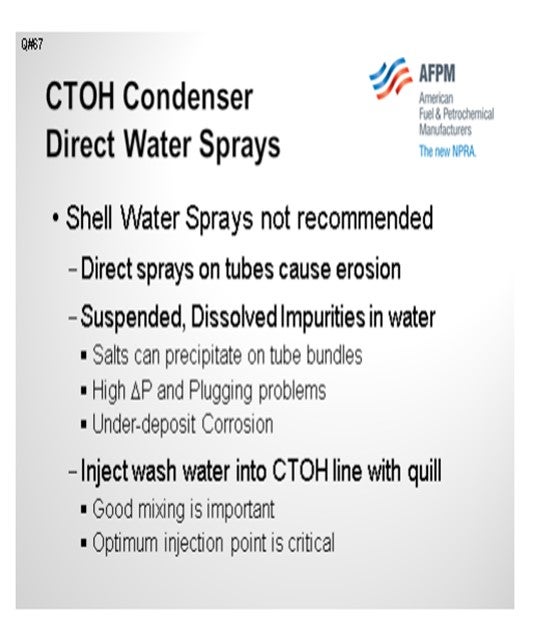
First, determine the water dew point, and be sure that the column overhead temperature is operating well above the water dew point. Calculate the water required to force saturation, and operate at 20% to 25% higher. To minimize corrosion, hydrogen chloride must be diluted with a large volume of washwater to elevate the pH of the water phase. Each operation must be analyzed by simulation. As I said, the first step is to determine the water dew point.
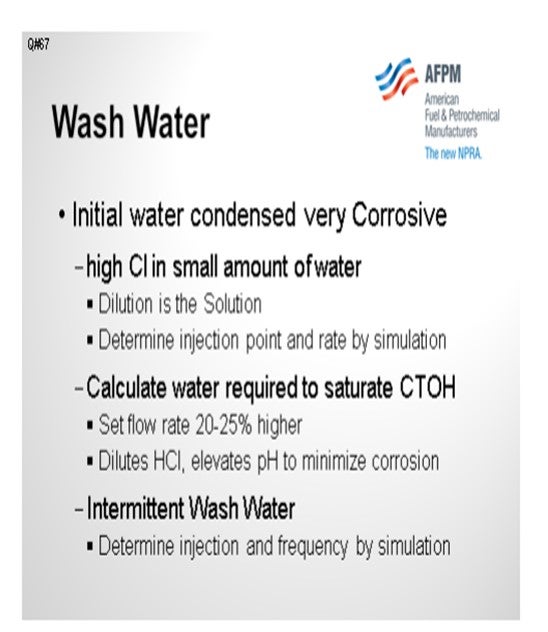
Maintaining the overhead temperature well above the water dew point is less challenging when maximizing gasoline with full-range naphtha overhead product. This becomes problematic when maximizing distillate, which lowers the overhead temperature. For distillate operations, there are potential dew point problem in the column; so, it is important to do the process engineering. We use several models. In one model, the crude column overhead vapor is sent to a three-phase separator with a cooler. A logical adjust operation varies the temperature of the cooler until the first drop of water condenses. That is the water dew point. The column and overhead line should be operated 15ºF to 25ºF above that temperature.
We set up a similar model to determine the target washwater rate for operation. Recycled washwater, plus the overhead streams, are fed to a three-phase separator with a cooler; so the temperature can be adjusted to simulate any point in the overhead system. Then with a logical adjust, the flow of water is increased until the first point of saturation or until the first pound of water condenses. We recommend operating with 20% to 25% additional washwater above the water saturation point.
It sounds fairly simple, but what dramatically affects the dew point is the equation of state model, be it Peng-Robinson, SRK (Soave-Redlich-Kwong), or a vapor pressure type.
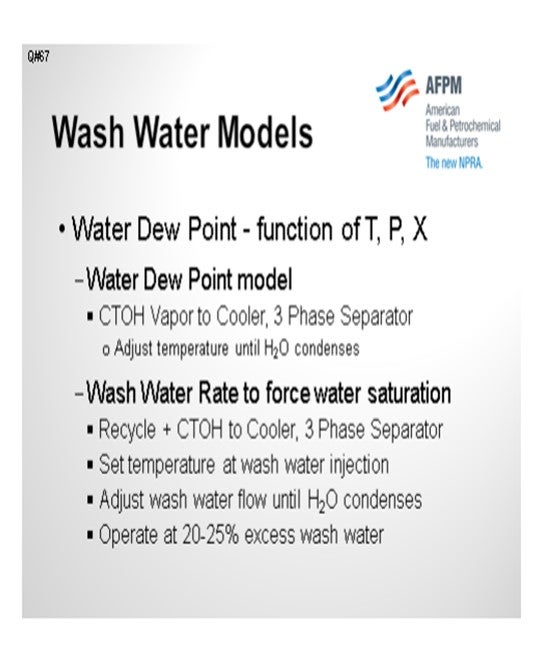
CLIFFORD (Motiva Enterprises LLC)
My response is very similar to Al’s. Going after waterwash improvements is really the key to preventing fouling and issues on the overhead condensers. Twenty-five percent of the injected water must remain in the liquid phase. You need to consider varying operating conditions and their effect on the required washwater rate. Variability in crudes and yield structures in your unit will change the conditions in the overhead system. Key factors in the proper design of your waterwash include injection point location, piping configuration, nozzle and quill design, and materials. As Harold mentioned, there is a P&P on waterwashers this afternoon.
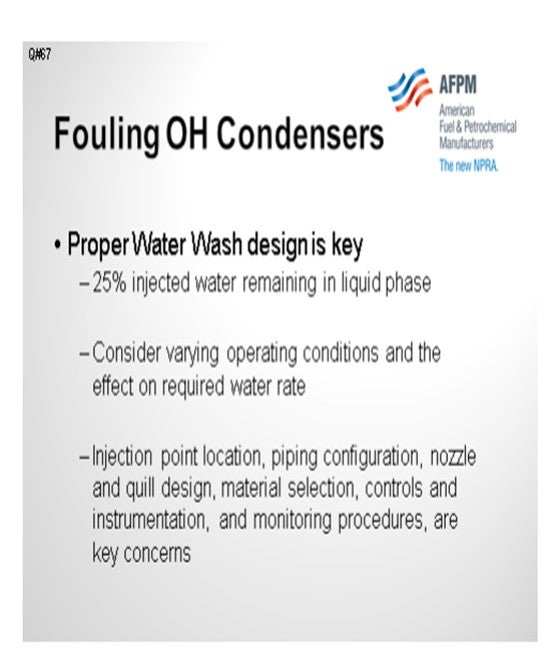
DION (GE Water & Process Technologies)
We recommend injecting the overhead waterwash in two places: into the overhead line and then individually into each leg of the overhead system. Use a very high efficiency nozzle to achieve atomization and good distribution of water droplets into the vapor phase. Then install a flow indicator, like a rotameter, on the waterwash to each of the overhead legs to ensure adequate water flow rate in each. It is extremely important to address the whole program – the waterwash, dew point, and salt point – because 90% of the corrosion occurs 10% of the time.
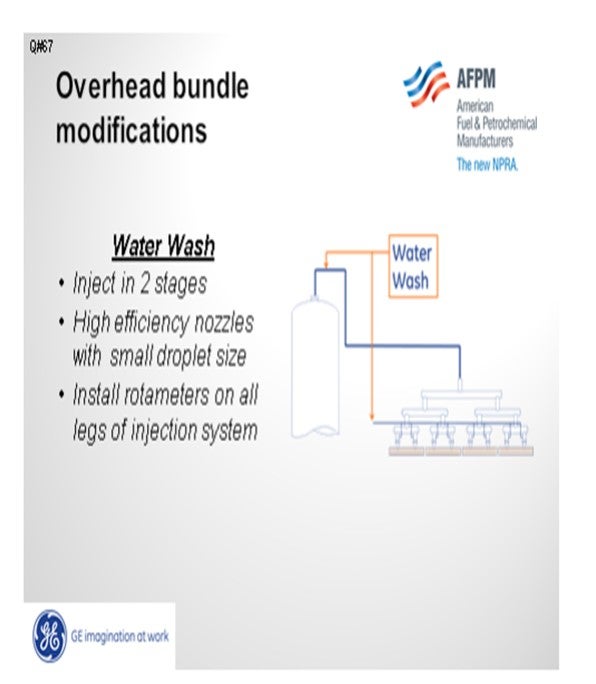
Regarding bundle modification, one refiner was limited on the amount of washwater he could use due to the size of his overhead. An impingement plate was removed and chevrons installed to direct the flow, and sacrificial tubes were utilized in the exchanger. That seems to have worked well because it channeled the corrosion to the sacrificial tubes while minimizing corrosion in other tubes.
RUSSELL STRONG (Champion Technologies)
First, I will also put in a promotion for this afternoon’s P&P because we are going to be talking about waterwashes. Here is a teaser: If you look at the high velocity in an overhead, it is certainly not at equilibrium at any point in the overhead line. So today, you will see computer flow simulations that show the immediate distribution effect of various waterwash spray nozzles in an overhead. We will also share thermography that shows the inefficiency of some waterwashes and why many of the waterwash rate calculations do not accomplish the end objectives. As far as the spray nozzles in the bundle are concerned, there is an option to put a nozzle into the bundle. There has been a successful case where there was a bundle on which you could not quite get water to the extremities. The top tubes were actually reconfigured by drilling through the tube sheet into those tubes where waterwash was then supplied. Holes were drilled into the tubes along the top and provided supplemental wash inside the bundle, which seems to have worked. Some people can get creative and come up with solutions that you would not have ordinarily imagined.
UNIDENTIFIED SPEAKER
So far, I think we have been addressing waterwash on a shell side. There have been some of these exchangers done with condensing on the tube side where waterwash was used on the tube side onto the tube sheet with the injection through the head of the exchanger onto the tube sheet. This put water down all of the tubes inside the exchanger. So, I think it is a little different from the previous discussion.
SHELTON (KBC Advanced Technologies, Inc.)
Direct injection of washwater through sprays installed in the shell of a shell-tube heat exchanger crude column overhead exchanger is not recommended for several reasons.
• Direct sprays on the tube bundle can cause erosion, which is why most designers specify impingement plates below the vapor inlet nozzles.
• Recycle washwater contains suspended and dissolved impurities such as salts which can precipitate on the tube bundles resulting in high pressure drop and plugging.
• Salt deposition on the outer surfaces of the tubes can result in underdeposit corrosion, tube leaks, unscheduled shutdowns and reduced tube bundle life.
Inadequate waterwashing causes localized corrosion, fouling and underdeposit corrosion. Adequate waterwashing in crude column and conversion unit fractionator overhead systems is so important that KBC has specific Best Practices for each service. Since an entire P&P session is devoted to Best Practices for crude unit overhead waterwashing, this response is an overview.
The initial water condensed in crude column overhead systems is very corrosive due to high concentrations of chloride ions in a small amount of water. Provision should be made for water injection at the point of initial condensation to minimize corrosion. KBC’s Best Practice is to calculate the washwater rate required to saturate the overhead stream and set the flow 20% to 25% higher. KBC grassroots crude unit designs are based on 25% excess washwater. This safety margin ensures that sufficient water is present at the point of initial water condensation to dilute the HCl and elevate the pH to minimize localized corrosion.
The water dew point is so important that it should be determined by rigorous simulation, not with a “rule of thumb”. Process simulators categorize water as a separate third phase. Accurate water dew point is a function of temperature, pressure and composition, including the water phase. Many physical properties are calculated on a dry basis. Thermodynamic models such as PR (Peng-Robinson) versus SRK (Soave-Redlich-Kwong), vapor pressure versus EOS (Equation of State) packages, and pseudo-component characterization produce different water dew points and flashpoints. KBC rigorously models the point of water saturation to determine the water dew point. Two simulations are required to calculate the water dew point and washwater rate required to force water saturation.
In a water dew point model, the overhead vapor feeds a cooler and three-phase separator with a Logical Operation to adjust the cooler outlet temperature until the first ounce of water condenses in the third-stage separator. This method provides an accurate water dew point to determine if the overhead temperature is operating with sufficient safety margin to avoid condensation in the column. Water dew points should also be checked at the inlets to each of the downstream services in the overhead system and the intermediate exchanger banks.
The next step is to develop a similar model with makeup, recycle washwater combining with the overhead vapor, feeding a cooler and three-phase separator. The cooler outlet is specified to match the operating temperature at the point of continuous washwater injection. A logical operator is used to adjust the washwater rate until the first ounce of water condenses in the third-stage separator. The model calculates the wash rate at the conditions for water saturation. For operating units, the washwater target flow rate should be set 20% to 25% above the theoretical rate required to saturate the stream.
The amount of water recirculation for saturation is a function of crude slate, column operating conditions and overhead product cutpoint. The theoretical rates required to saturate streams at the point of continuous water injection, as well as other points in the overhead system, should be calculated frequently to adjust washwater targets and identify requirements for intermittent waterwashing of upstream services in the overhead system.
The location of a continuous washwater injection is dependent on the design of the overhead condensing system because the water dew point depends on heat exchange configuration.
Hot Reflux Drum / Cold Product Drum (two separate vessels):
• Cold crude versus hot reflux exchangers should operate hot to avoid water condensation.
• The waterwash injection point is determined by the configuration of the cold product cooling. Some examples are listed below.
• For air coolers with water trim coolers, water injection is typically at the trim coolers.
• For air cooled condensers without water trim coolers, water injection is typically at the air cooler inlet nozzles.
• Water coolers only are multiple banks in series, and injection is typically between shells.
Combined Reflux and Product Drum with Cold Reflux:
• For 100% cold reflux with no top pumparound, the waterwash injection point varies for the following configurations:
- Crude overhead versus cold crude heat exchange,
- Air cooled condensers,
- Air coolers and water trim coolers, and
- Water condensers
• For 100% top pumparound heat removal with minimal cold reflux, the washwater injection point is determined by cold product cooling: air coolers with and without water trim coolers, or only water coolers.
Piping and injection points for intermittent waterwash should be provided for services that do not require continuous waterwashing. Some operators conduct intermittent waterwashing because of increased pressure drop in the overhead system. The frequency of intermittent waterwashing should also be based on the propensity of salt deposition determined by process simulations, fouling and ionic models.
CLIFFORD (Motiva Enterprises LLC)
Each option presents an opportunity to improve fouling and corrosion resistance. Bundle modifications as I understand it would be to improve the flow patterns at the point of fouling such that the fouling is not concentrated in one area. This would give the cooling in the bundle a chance to increase the amount of liquid water, and prevent further fouling and corrosion. This option is relies on fairly constant salt point/water points to achieve the desired performance improvements. If water dew point is shifted further downstream it may not achieve the desired level of success. Modifications which add additional nozzles to direct sprays to areas susceptible to fouling may increase the risk of damage to the bundles due to impingement of the spray onto the bundle. Pressure equipment engineering should also be consulted when adding nozzles to existing equipment.
Another option may be to improve the metallurgy such that it is more resistant to the corrosion mechanism and monitor differential pressure. It may be possible to bypass and waterwash exchangers for a short period to time to remove the deposited salts and restore performance, however this poses risks as it may move corrosion into downstream equipment not designed to handle this mode of operation.
A more robust solution would be to enhance the waterwash. This does not come without technical challenges which must also be addressed. Proper Injection point location, piping configuration, nozzle and quill design, material selection, controls and instrumentation, and monitoring procedures, are key concerns. Sufficient contact time must be provided to ensure that the HCl vapors are contacted by the liquid and neutralized. Spray pattern is important as ensuring a continuous aqueous phase along the pipe wall is important to prevent localized concentration cells from developing and causing accelerated corrosion. Impingement on downstream equipment should also be avoided as this may cause erosion/corrosion concerns. A rule of thumb is to maintain injection rates such that at least 25% remains liquid at the point of injection.
Alternate modes of operation including varying temperatures and mass rate should be considered to ensure that the system is robust enough, and monitoring should be in place to know when to adjust the rates. Finally, the impact of the increased water on downstream separations equipment should be considered, as well as the potential shift in duties to the downstream exchangers.
Injection of the water directly into or immediately upstream gives very little contact time, so the downstream bundle essentially functions as a static mixer forcing contact with the hydrochloric acid vapors and the aqueous phase. Because there is no guarantee that the neutralization amine will be immediately present where the HCl condenses, this bundles metallurgy should be carefully selected.
DION (GE Water & Process Technologies)
Waterwashing is used to provide a means of forcing the water dew point further upstream in the overhead system and to physically dilute and wash salts. This is accomplished by raising the amount of free liquid water in the system. This free water will then dilute corrosive species at the ICP and also wash away any neutralization salts formed at temperatures below the wash injection temperature or mixed exit temperature (MET). Water-washing of the overhead system is a beneficial and essential part of proper overhead maintenance. Modification of the bundle metallurgy to a higher corrosion-resistant material will increase the durability of the metal surface but will only delay failure and not prevent it. With the continued accumulation of precipitated salts, underdeposit corrosion potential is still present and fouling of the exchanger will continue to be an issue. In addition, the metallurgy involved in the bundle materials upgrade will be expensive and may not provide the bundle life and return on investment initially anticipated.
On the other hand, direct water spray into the overhead condenser delivers several benefits compared with a metallurgical upgrade. A properly designed waterwash will dilute acidic species at the initial condensation point (ICP) and physically remove the corrosive salts by washing them away from the metal surfaces. An adequate waterwash will also eliminate the need to upgrade the bundle metallurgy to a more expensive material. There are documented cases of bundles lasting 10 to 15 years due to the proper implementation of an overhead waterwash system. However, the overhead accumulator boot has to be large enough to accommodate the additional water volume and still provide acceptable separation of water from the hydrocarbon stream. Water carryover in the overhead reflux can introduce high levels of water-soluble amine back to the distillation column. This causes a large cycling effect that will dramatically increase salt points. Additionally, the water can cause wetting of forming or already existing salts. This in turn causes their characteristic corrosion rates to increase significantly.
A poor waterwash can be worse than no waterwash. Waterwash should be injected in two stages using high efficiency nozzles in a cocurrent configuration to provide a small droplet size with large surface area and dispersal pattern. This will impact both the wall wetting capability of the spray, as well as the vapor scrubbing efficiency. The first injection stage would be a single point injected into the overhead vapor line near the top of the column, while the second stage would be multiple points injected in parallel just prior to exchangers. In a well-controlled unit, the first-stage wash injection should provide just enough water to form 20% of total liquid water and primarily saturate the overhead vapor. The second injection stage then would inject the remainder of the total waters needed to achieve the washwater target. Enough water should be added to achieve at minimum 5% free water. While 5% is a minimum value, 10% to 15% waterwash can be even more effective. To ensure proper volumes and distribution of the washwater in the overhead system, it is critical to install rotameters on all legs of the injection system and maintain proper balance and monitoring of these flows on a routine basis. A GE client has also experimented with the mechanical changes to problem exchangers instead of installing washwater injection ports into the shell. The impingement plates on these exchangers were removed and replaced with chevrons welded just below the inlet to direct flow axially as the overhead stream entered the exchanger. To compensate for the increased impingement at the exchanger inlet created by these modifications, sacrificial tubes were installed wherever increased impingement resulted due to the mechanical changes (in this case, on the top of the bundle). The client reported that after making these modifications, the exchanger problems related to salt fouling were significantly reduced.
RANDY RECHTIEN (Baker Hughes)
Exchanger bundle modification and water injection (via multiple points) into the shell side of the exchangers have been implemented in the past; however, the success of these techniques has been limited. For those systems where a waterwash is already in place, more benefit can be realized by redesigning the waterwash so that it performs as required. Such modifications may include:
• Increased water flow rate,
• Installation of atomizing spray nozzles, and
• Relocation of wash injection points further upstream of condensers.
BASHAM (Marathon Petroleum Corporation)
We have never tried to put direct water spray on the shell side of a bundle. While the idea has merit, it requires multiple water injection nozzles and bundle modification to provide free area just below the nozzles so the water will spread out. Potential problems are water impingement leading to tube failure and reduction of condensing duty.
LEE (BP Products North America)
For corrosion mitigation, the tower should be completely dry or have adequate waterwash. As the crude tower normally has stripping steam in it, the overhead system is not able to be dry so the only option available is to have enough water that the water dew point is higher than the salt point so that water condenses first and is present in sufficient quantity to dilute the salts as they dissolve into the aqueous phase. Adequate waterwash also requires enough residence time to separate out the water from the hydrocarbon so that there is not water carryover into the hydrocarbon stream. Good contact and mixing are needed to adequately wash the inlet stream. Depending on the direct water spray configuration, there may be a compromise in this respect, but the suggested geometry is probably better than doing nothing.
DENNIS HAYNES (Nalco Energy Services)
If the modification allows for better dispersion of the washwater through the exchanger so that areas of less liquid traffic are contacted, it would be an improvement, and this has been done in rare cases in the industry; however, if the water flow rate is too low, the risk is that it may not be enough to wash salts out of the system resulting in elevated corrosion due to damp salts.
MARK ANDERSON (ThioSolv, LLC)
It is difficult to get adequate water distribution through the shell side of S&T (shell-and-tube) exchangers. There are a few measures which can help:
1) If the condensers are two-pass on the shell side, make sure the seals between upper and lower pass are intact. Leakage not only reduces the heat transfer, but it also allows the washwater to bypass large parts of the bundle, which allows heavy accumulation of solids in the unwashed spaces.
2) Provide a high washwater flow rate by recycling water from the reflux drum boot to. Distribute the washwater into the inlet of each condenser train with its own FI and globe or needle valve. The recycle water stream may be drawn from high in the boot because it does not matter if some hydrocarbon is entrained. That allows the vertical velocity in the lower part of the boor to remain low to minimize entrainment of hydrocarbon in the net sour water stream. Make sure the drum internals are designed to provide effective oil/water separation.
3) One can visualize that as the process stream passes around the side of each baffle in the exchanger, the liquid phases will not turn the corner as sharply as the gas phase. Deposits form on the downstream side of the baffle because of the water “shadow”. Water distribution can be improved by notching the circumference of the baffle plate to allow some liquid to leak past the closed side of the baffle. When fabricating a new bundle, specify that small holes be drilled through the baffle plate to allow liquid leakage into the liquid shadow.
4) Make sure that the type and amount of neutralizing and filming amines injected are not part of the problem rather than part of the solution.