Question 67: The industry continues to experience process safety incidents associated with FCC electrostatic precipitators. What are you doing to prevent these incidents?
REYNOLDS (Phillips 66)
Phillips 66 has six ESPs (electrostatic precipitators) in service. We have not been immune to serious incidents on our ESPs. In 1994, we had an ESP explosion, which led to a fatality. So, in order to minimize the likelihood of these kinds of incidents happening again, the company has a standard that all of the refineries are required to follow. It lays out how your safety system is supposed to be configured and which features it is supposed to have. The compliance of the standard is tracked at the corporate level, so all of the refiners have to report if they continue to meet the standard. We have one wet ESP that is downstream of the scrubber, and it must meet the compliance just like regular ESPs.
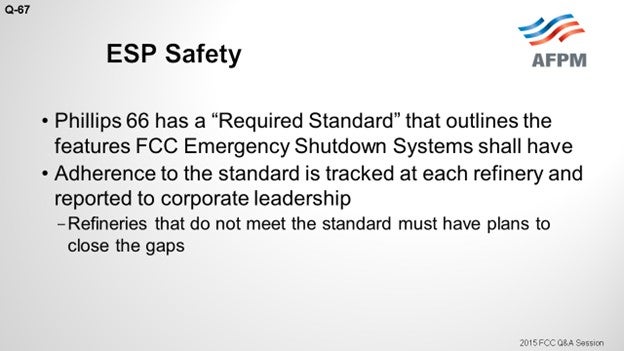
One of the features required by this standard is that the ESP shall shut down if the main FCC safety system engages or trips, regardless of the cause. There are several other features. If the inlet CO (carbon monoxide) level exceeds the prescribed limit in the standard, which says that it can be no greater than 5,000 ppm (parts per million) of CO, the safety system engages. Also, if the air preheater has a safety system on it which then trips, the ESP is required to trip along with it. The ESP must have its own separate shutdown button. The CO is used basically as a surrogate for other combustible material. CO is combustible itself; but if you are having poor combustion in your regenerator, you are likely to be generating CO as well. One of the more important features is that the ESP cannot have the capability to re-energize itself after it trips.
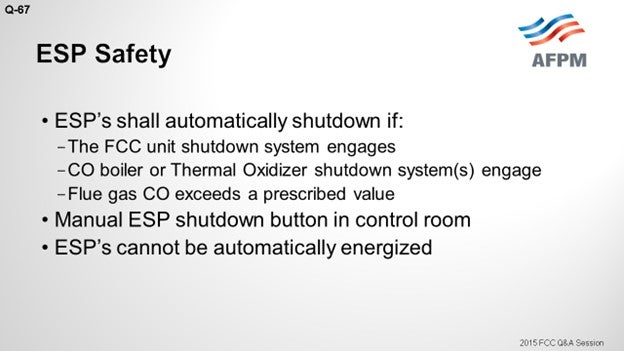
So the highest potential for operating on ESP and explosive composition in your flue gases during startups comes from the use of torch oil along with air preheaters, which can lead to poor combustion. Our recommended practice is to keep the ESP down during startup until the unit is stable. Stability is defined as feed in the unit, stable pressure balance, CO within limit, and nothing bypassed in the safety system. For certain locations, you may not be able to have the luxury of starting up without ESPs. So if you do that, the standard recommends that you have an air preheater safety system as well.
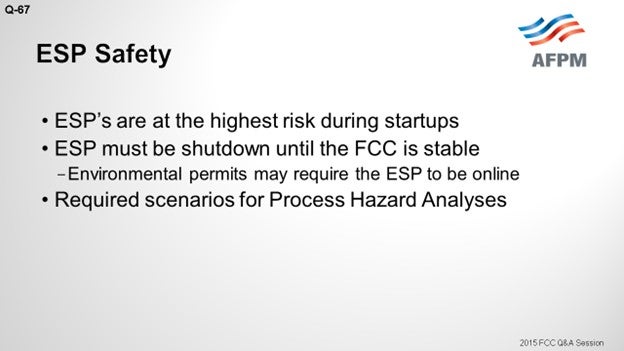
The standard includes some recommendations; for instance, minimizing the personnel around the ESP when you start up or shut down or if there is an upset. It also recommends utilizing the methane analyzer in conjunction with the CO analyzer. And for the sites that do start up with ESP online, having a methane analyzer – in addition to a CO analyzer – is strongly recommended. The standard includes some scenarios you must consider whenever you do a PHA (Process Hazard Analysis), such as the loss of combustion air or any kind of upset in the regenerator, upset in the stripper, low-riser outlet temperature, and pressure reversals. A lot of the information I used for today’s responses came from a presentation by Phillips 66’s own Mike Wardinsky at the 2009 AFPM Q&A Principles & Practices.
LARSEN [Marathon Petroleum Corporation (MPC)]
In Marathon, we have two units with ESPs on them. Our setup is very similar to what Mark described with Phillips. Any activation of the normal FCC SIS (Safety Instrumented System) will de-energize the ESP. On the slide, you can see some of the limits that we use. Our trip point for CO is 1500 ppm, which is a little more conservative. Also, we will trip the ESP if excess oxygen is less than 0.1%. So, either of those inputs will act to de-energize the ESP. For safety purposes, we only run our ESPs energized during stable normal operations, not during the times of hot standby or startup, etc.
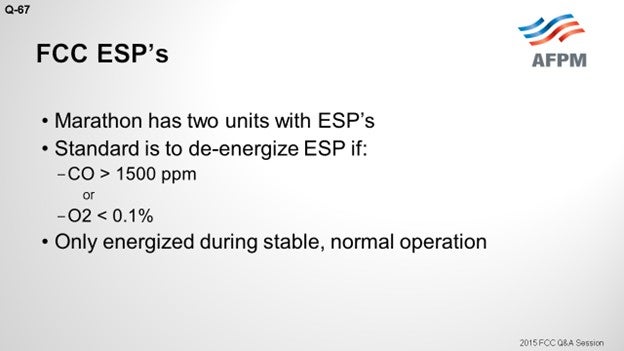
A lot of thought can go into the selection of the right number to use for de-energizing the ESP. An example is the chart on the next slide which includes some numbers, based on the molecules and some inflammability assumptions. This is an example, published by Thomas Lugar at GE1 in 1992, which shows you the magnitude and framework of the danger zone for CO in relation to ESP operation. So, with that, I will put in a plug for our Principles & Practices session tomorrow. I believe it has a topic on ESP safety as well, which will be discussed in more detail tomorrow morning.
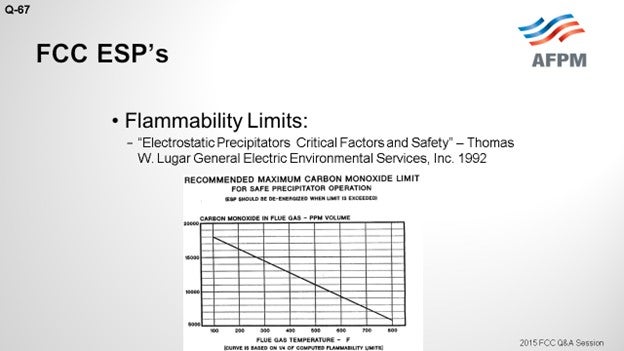
KEVIN PROOPS (Koch Industries, Inc.)
Mark and Nik, thank you for your comments. I had the misfortune of visiting the unit Mark mentioned about the week after that catastrophe happened. I want to add a couple of comments to what you described during the startup (when that explosion occurred). Natural gas backed in from the fractionator, through the reactor, and got all the way to the regenerator. I believe that there would not have been any significant CO at that time. Oxygen was high.
So panel members and the audience, if you are worried about ESPs on startup, recognize that they can be very abnormal to what you are used to seeing. I believe the incident investigation also found that the ESP had been in a de-energized state, but it still exploded. So, you have to watch out for potentially explosive mixtures of oxygen and methane at higher temperatures.
ROGER LANOUETTE (Monroe Energy, LLC)
I am curious about the shutdown system. Our analyzer people are telling us that there is interference with CO and methane in doing the analysis and calibration difficulties. Is there a specific analyzer that you have come across that is better for this kind of service? The second part of this question is: Is this an SIL (Safety Integrated level)-rated shutdown system?
UNIDENTIFIED SPEAKER
As far as the analyzer, I cannot speak to what works better in others. I do not think we have a standardized analyzer as far as I know. Do we?
LARSEN [Marathon Petroleum Company (MPC)]
My answers will be published in the final Answer Book. In them, I have detailed the specific analyzer we use. I know a lot of folks are going to the TDL (tunable diode laser) technology, which is a question later on. I think we will talk about response time in Question 76 in a little while, too. I can meet with you after the session to go over the specific analyzer we use with good success.
EMERSON FRY (Delek Refining, Ltd.)
Does anyone have any experience or insight as to whether or not this would be important to have in a partial-burn unit with a CO boiler on the backend? Is that at any greater or lesser risk than a full-burn unit?
J.W. BILL WILSON (BP Products North America Inc.)
Just to add another question about it, is there greater risk with an ESP and CO boiler or is the risk the same? It is at least the same. Okay. We actually managed to blow up an ESP that had a CO boiler on it, so the risk is there. So yes, I certainly think the standards will be the same on our units. I imagine other people who have standards will probably apply the same standards.
RIK MILLER (Phillips 66)
I will address two issues. One is the analyzer. As Nik said, the Phillips 66’s standard also calls for TDL analyzers because they are very fast-responding and very accurate and sensitive for CO. You can also get a TDL for methane. Some of our units have that as well.
As Kevin pointed out, the incident that Mark mentioned would not have been stopped by one of these analyzers. The explosive mixture was fuel gas, and the ESP was not energized at the time. What that site and about half of our other FCCs have done since then is install these overhead blinding devices between the reactor overhead and the main fractionator. Those are reusable devices that can seal off the reactor from the main fractionator so you avoid getting migration of fuel gas or other hydrocarbons during periods when you are down or starting up. Those are very effective, and we recommend them strongly in our system.
ROBERT (BOB) LUDOLPH [Shell Global Solutions (US), Inc.]
I would like to expand Question 67 to include the representatives of the electrostatic precipitator manufacturers who may be in the audience. What are the electrostatic precipitator manufacturers doing to help improve the safety and operation of their equipment, and, in turn, the overall safety of the refining facilities?
NEIL DAHLBERG (Hamon Research-Cottrell, Inc.)
Hamon Research Cottrell has supplied a large number of precipitators to refineries in the United States over the past 15 years. Many of these suggestions are implemented in our design, and we participate in a HAZOP (Hazard and Operability) study at the beginning of each design process. An additional level of protection would be to limit the power to the operating transformer rectifies at startup to stay below the threshold of sparking, which will eliminate a source of sparking in the precipitator and a potential source of ignition of combustible gases.
NIKOLAS LARSEN [Marathon Petroleum Company (MPC)]
The function of an ESP is to remove particles from gaseous streams by passing the gas between a pair of electrodes: a discharge electrode at high potential and an electrically grounded collecting electrode. Sparking in an ESP is an ignition source for a fire or explosion if enough combustibles and oxygen are available.
Specific to FCC units, the biggest concern is carbon monoxide (CO). CO is very unstable; and as such, it is difficult to measure and deliver the information fast enough in order for a manual process adjustment.
Marathon Petroleum Company (MPC) utilizes an extractive system in one FCC unit, and the analyzer is the ABB AO2000 platform with a Magnos 106/206 Paramagnetic Oxygen Analyzer and Uras 14/26 Non-Dispersive Infrared CO Analyzer. Our analyzer is mounted on the deck at the duct; so our sample line is very short, probably in the 10- to 20-foot range. Overall, we have been pleased with this setup.
Others in industry have had success with tunable diode laser analyzers (see Question 76). MPC automatically de-energizes an ESP at a conservative level of either excess O2 (<0.1%) or CO (>1500 ppm). Other actions that de-energize the ESP include activation of the SIS Feed Divert Sequence, control room ESD (emergency shutdown) button, and two field ESD buttons. There is no automatic re-energizing. MPC also does not energize an ESP during times of unstable FCC operation, such as startup or hot standby, when torch oil is being utilized.
The following additional resources are available for your review.
-
“Reducing the Risk of Fires and Explosions in FCC Electrostatic Precipitators”, Michael Wardinsky’s presentation at the 2009 AFPM Q&A Principles & Practices.
-
“Advances in Fluid Catalytic Cracking – Testing, Characterization, and Environmental Regulations”, edited by Mario L. Occelli; Chapter 18 (18.4.8) on ESP Safety by Jeffrey Sexton.
-
“Electrostatic Precipitators Critical Factors and Safety,” a paper by T. Lugar which also calculates safe limits for CO when operating an ESP (GE Environmental Systems, 1992).
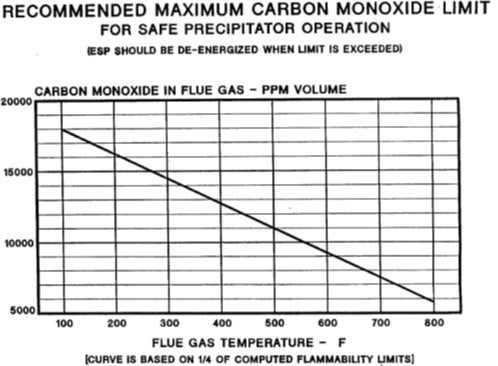
ALAN STAHL (CSI Engineering)
CSI Engineering evaluates the safety procedures and systems of our client refineries’ electrostatic precipitators (ESPs). Of particular importance is the precipitator emergency shutdown system that eliminates high voltage sparking as a source of ignition in the event of hazardous process conditions. Shutdown system designs vary in details of wiring, control inputs, and procedures for use. Some systems and practices prove to be inadequate. We apply our experience to advise our clients of what we consider the most effective features and procedures.
CHRIS STEVES (Norton Engineering)
Some of our clients have installed automatic shutdown systems for ESPs, which may be triggered by any of the following initiating factors:
-
High ESP inlet CO or methane concentration [as measured by tunable diode laser (TDL)],
-
FCC unit trip, or
-
CO boiler trip.
Some refiners will also keep the ESP de-energized during unstable phases of the startup, such as when first introducing torch oil to the regenerator. A thorough analysis of the unit configuration and potential causes of an ESP incident should be reviewed by a multifunctional team in the refinery so that the best solution can be implemented. Consultation with outside experts familiar with FCCU ESPs and previous industry incidents is normally useful.