Question 66: In order to meet the pending MARPOL/IMO (International Convention for the Prevention of Pollution from Ships/International Maritime Organization) 0.5% sulfur fuel oil standards in 2020, what options do you have available to implement within FCC units to improve slurry quality, adjust yield, or find alternate dispositions, both within the overall facility and as a saleable product?
BHARGAVA (KBC Advanced Technologies, Inc.)
In the absence of configurational studies in changing crude, the options you have for reducing sulfur and fuel oil are very limited. The IMO standards of 0.5 wt% will make slurry a discounted product because the slurry sulfur will most likely be molten into 0.5%. Further, because of the ash content, you will need to have a bigger discount and you may not even be able to put the slurry back into fuel oil anymore.
So, what are the potential solutions within the FCC boundary? One way to solve the problem is to reduce slurry yields to, hopefully, get to a net-zero slurry product, which is impossible. However, you do want to reduce the slurry. One of the places where you can find a home for slurry is the coker unit. If you have an FCC and a coker and you put the slurry back into a coker, you will create an infinite recycling of the unconverted products. The only way that will work is if you have a partial slurry recycle or if you have a coker and a hydrotreater in between the coker gasoil and the FCC. This arrangement will help you break the cycle because it will reduce the amount of slurry you make and also reduce the PNA buildup.
If you do not have a coker, the cheaper option is to recycle the slurry into the FCC riser and destroy slurry that way. You will still end up having a net product which will be of very poor quality. The last option is to do catalyst reformulation with a pore-sized active matrix or additives to reduce your slurry make on a once-through basis.
The only dispositions for slurry are very limited. One is carbon-black feedstock. The spec on carbon-black feedstock is 4 wt% on sulfur. You should be able to make that feedstock. The only word of caution is that the ash content there is tight: 0.5 wt%; so, you might have to upgrade your filtration facilities to meet the ash limit. The other place people have now started putting slurry is road asphalt. Those are the only two options.
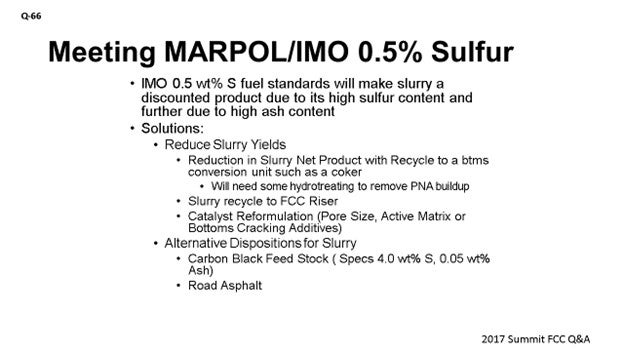
FOOTE (CHS Inc.)
The trend on the right side of the slide shows feed sulfur versus clarified sulfur for one of our operating units. To meet the IMO standard, the trend suggests that we need to get down to about 0.1 wt% feed sulfur to meet the 0.5 wt% in the slurry. You also need to meet the IMO standard for ash content, and this can be challenging. Often, if we could somehow control how our cyclones work, we probably would not be here. So, that is not really the handle we have outside of just the general sound design of the cyclones. But if you have two run-down tanks, consider running down to one tank, letting it settle, and then running down to the other tank. In this way, you would be utilizing two tanks for settling out the ash, which will make your loaded slurry a little better.
If reducing sulfur is not an option, consider recycling slurry. In the riser, the slurry in the coker yields 30 wt% coke on feed versus slurry recycled to the riser, which makes about 15 wt% coke on feed. So, I think that the FCC yield slate would be better with slurry recycling than when putting slurry in the coker.
Bottoms cracking additive is a high-value proposition which is low-risk. There are not very many drawbacks to it. If it pays out big by uplifting the difference between the cost of slurry and the additive, especially after the IMO standard comes out, then uplifting to LCO is huge. So, if you think it might work, try it. Also, denitrification performance on gasoil hydrotreater or cat feed hydrotreater catalyst is important. Nitrogen has a worst conversion effect than sulfur.
Next, look at crude purchases to ensure that your LP (linear program) is calibrated to reflect the effect of gas, oil, and nitrogen on cat yields. Make sure you are debiting those crudes that have high nitrogen in them.
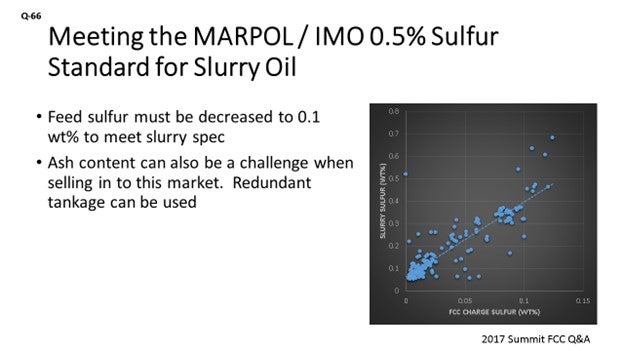
ROBERTSON (AFPM)
Mel Larson is going to do a further in-depth analysis of this tomorrow when he addresses the challenges and opportunities of the IMOs 2020 Marine Fuel Standard tomorrow in the Fostering Profitability P&P.
PHILLIP NICCUM (KP Engineering, LP)
I would like to reference the paper I wrote with two coauthors from KP Engineering and presented at this year’s Annual Meeting. The topic of the paper was vacuum distillation column for upgrading slurry oil from the FCC unit by removing light cycle and heavy cycle to reduce the net slurry or yield. As you know, vacuum conditions are required to keep the temperatures down to a level that will not terminally degrade the oils. That is why the vacuum tower is required.
SANJY BHARGAVA (KBC Advanced Technologies)
In October 2016, the International Maritime Organization (IMO) decided to implement the strict level of stack emissions equivalent to burning 0.5% sulfur residue bunker fuel from 2020 rather than 2025. The FCC bottoms (decant oil or slurry bottoms), along with cycle oils, are often blended into internal and external fuel oils. With the lower sulfur regulation, high sulfur FCC bottoms will be a discounted stream based on sulfur content; and then further, on catalyst content.
Without addressing a wholesale crude change and extensive configuration rationalization, the slurry yield – and thus, bulk sulfur contribution – can be mitigated by optimizing the FCC operating conditions and catalyst properties to reduce slurry yields. FCC operating conditions optimization would include recycling slurry to the riser up to a point. A better option is recycling slurry to a bottom's conversion unit, such as a coker with coker VGO hydrotreating, to avoid PNAs to build up in the recycle (even to extinction). Catalyst options would include the use of a bottoms cracking additive or reformulating the catalyst with active matrix and different pore size.
The sulfur reduction in slurry is a more expensive proposition. Some of the potential routes being considered are low-sulfur crudes, which would result in lower-sulfur VGO being processed in the FCC, resulting in lower-sulfur slurry. The other option would be to build VGO hydrotreaters and run them at higher severity with lower VGO sulfur targets. Higher hydrotreater severity (pressure) would have an additional benefit of higher conversion in the FCC, thereby lowering slurry yield. Another option is to consider a small vacuum unit that would “lift” recoverable cycle oil, which would leave a very heavy but less volume of catalyst-laden oil. The handling of the residual stream will be difficult and could challenge the use of the last option.
One outlet for high sulfur slurry is carbon-black feedstock (CBFS) if the slurry has high aromaticity. CBFS has a higher S specification of 4.0 wt%. You will need some filtration to bring the ash content to less than 0.05 wt%. FCC bottoms have also been used in road asphalt successfully.
DARIN FOOTE (CHS Inc.)
In order to meet the 2020 MARPOL/IMO 0.5% sulfur standard, feed sulfur must be reduced. Figure 1 is a scatter plot of feed sulfur versus slurry sulfur. The data is taken over several years from one of our units that processes highly hydrotreated feedstock. The results suggest that the target feed sulfur, in order to meet the IMO standard, is approximately 0.1 wt% feed sulfur.
Ash can also be a hurdle in selling into this market. Cyclone performance is not an operating variable that we can typically control. However, if you have two slurry tanks accepting rundown, you can use the offline tank to settle out any catalyst and improve slurry ash content in the product sold.
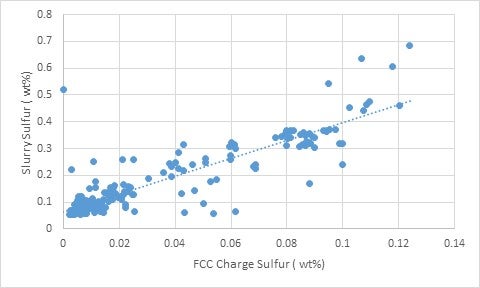
Figure 1. Slurry Sulfur versus Feed Sulfur
(100% Hydrotreated Feed with 70/30% VGO/HCGO Hydrotreater Feedstock)
If reducing feed sulfur is not an option, then likely reducing slurry make is the best option to reduce exposure to high-sulfur residual markets. The following are a few options to consider with potential limits.
PARAMETER |
POTENTIAL LIMIT |
Increase catalyst/oil. |
Dry gas limit, regen temperature, catalyst circulation limit |
Add a bottoms cracking additive. |
None |
Slurry recycle |
Regen temperature, air limits, riser velocity |
Slurry charge to the coker |
Cycling up PNAs in the HCGO, GOHT, FCC complex |
Consider denitrification performance when selecting your next GOHT catalyst load. Reduction of feed nitrogen directly impacts conversion more than feed sulfur. |
GOHT limits: H2 consumption, Rx volume |