Question 65: Our vacuum column wash bed has lasted seven years in service and now needs to be replaced due to excessive coking and pressure drop. What is the typical life expectancy of the wash grid and packing? What is the panel's experience for the use of wash oil to the vacuum column wash section bed in gpm/ft2 (gallons per minute per square foot) with structured packing and/or grids in the bed? What is the recommended maximum slop wax draw temperature? Should a limit be set on this temperatu
SHELTON (KBC Advanced Technologies, Inc.)
This topic was discussed extensively in the previous Q&A, so my response will focus on wash bed replacement after seven years due to excessive coking and pressure drop. The typical life expectancy of a wash bed has to be qualified. It is dependent on cutpoint, design of the column, internals, operation, and severity.
A wet operation with stripping steam requires lower coil outlet, severity, and flash zone temperature to achieve the same cutpoint compared to a dry operation. I will not address lube oil wash beds, which last considerably longer than a fuels operation. Obviously, a bed with 100% grid lasts longer than a deep-cut design with structured packing.
Since the run length is seven years, it is assumed this is combination packing over grid and a deep-cut design. For a heavy crude operation, six-year runs are typical. If it is a severe operation, then even with a well-designed wash zone with good overflash and adequate slop oil there are still some sections of the packing that have to be replaced during turnaround. With some asphaltic crudes, refiners are satisfied if they make a run without any incidents. So I would say that a seven-year service life is better than average in a severe operation.
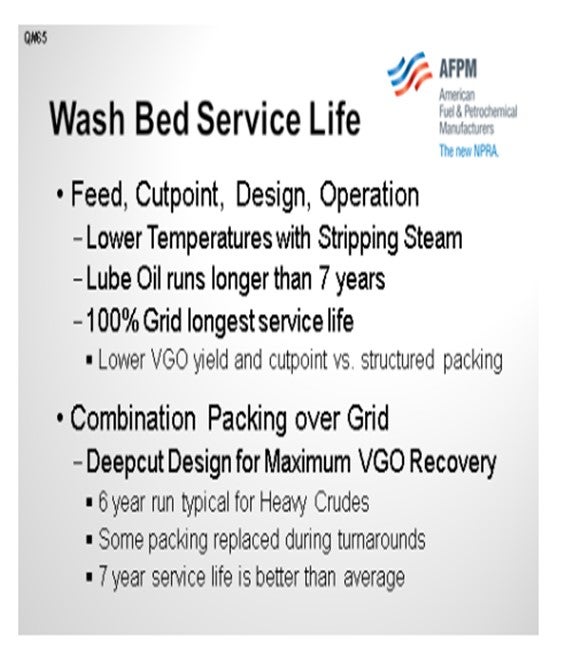
Regarding the specific wash oil flux rate, we try to avoid rules of thumb. Every operation is different and has to be modeled. In this kind of severe operation, the depletion ratio could vary from 4:1 to 6:1 and is a function of bed height and wash rate conditions. In a severe operation or deep-cut operation, we typically see 80% of the wash oil vaporized in the beds. KBC targets the overflash or the slop oil at the bottom of the bed, and the required wash oil rate at the top of the bed to produce that overflash target is variable.
It was interesting when we were talking amongst the panel. I would have thought this would have been the standard. Recent Q&A answers quote flux rates, but it was surprising that standard conditions or flowing conditions were never specified. At the low end, the cold versus hot flux rate varies by 35%.
Typical overflash flux rates range from 0.1 gpm/ft2 to 0.2 gpm/ft2 at 60°F, and 0.1 gpm/ft2 at 60°F is about 0.15 gpm/ft2 at operating temperature. In our designs, we target 0.20 gpm/ft2 overflash at 60°F at the bottom of the bed. The wash oil rate at the top of the bed is whatever is required to attain 0.20 gpm/ft2 at 60°F overflash at the bottom of the bed. Wash oil rate is a function of flash zone temperature and pressure. Hopefully, if you work on an operating unit, it has a slop oil meter. Then the wash oil rate should be adjusted to maintain the target overflash at the bottom of the bed. This is how we model an existing operation that does not have a slop oil meter. Frequently, the wash oil to the top of the bed is measured but not the slop oil or overflash.
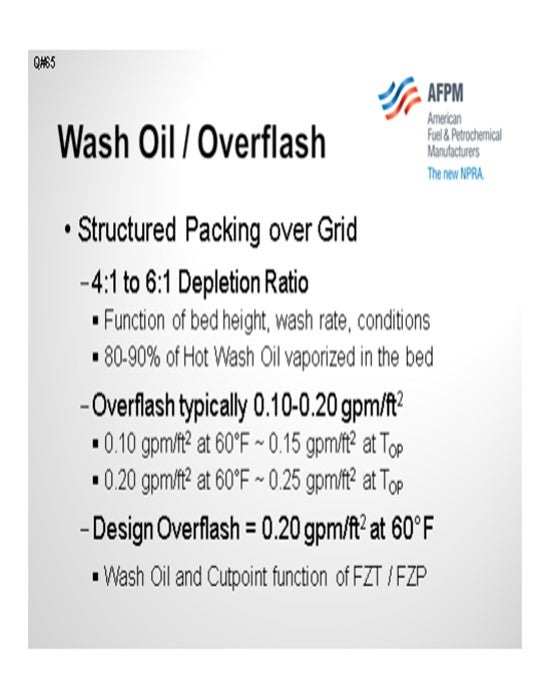
For an optimization or a grassroots design, we develop a fully-integrated model of the vacuum heater with our VIS-SIMTM model, including the transfer line and the wash zone in the column. The overflash in the column model and the heater outlet temperature are specified.
Petro-SIMTM accurately predicts the depletion ratio based on theoretical stages, and the wash oil rate at the top of the bed is variable. The answer to the target wash oil rate is whatever is required to produce the desired overflash at the bottom of the bed and which will ensure that the wash bed will operate trouble-free for a run-length.
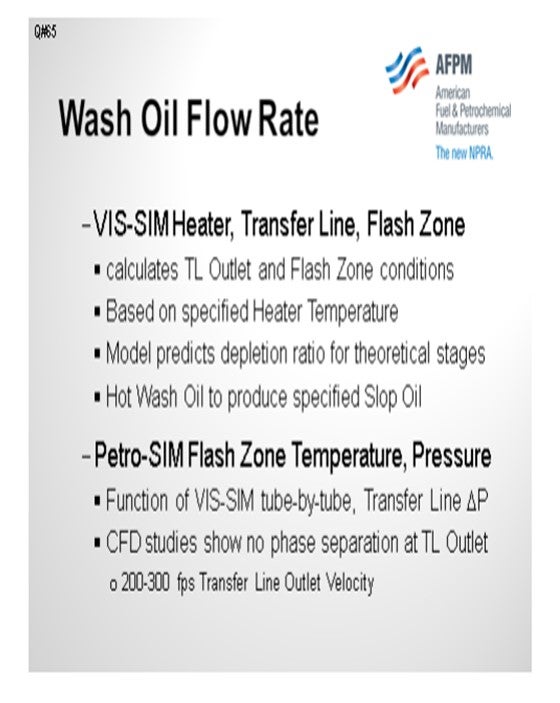
Discussions about wash oil should include inlet distributors because this is critical. In our grassroots designs, we specify spray distributors with 200% to 300% coverage; so, in any one spray pattern, even if one or two spray nozzles fail, there is still coverage in that zone. Some vendors use tough distributors, but we have designed 47-foot ID (inside diameter) vacuum columns. It is difficult to install a level gravity flow distribution system in a very large diameter column. Furthermore, in a deep-cut severe operation, we would be concerned about coke solids plugging the gravity troughs. With any distribution system, proper metallurgy is very important with a good filtration system to remove solids from the wash oil.
The final question was about the recommended maximum slop wax draw temperature. The slop oil temperature should be cooler than the flash zone, which confirms that the wash oil has penetrated the bed and will not coke. As far as a maximum temperature, Kevin thought this might have to do with pump seals.
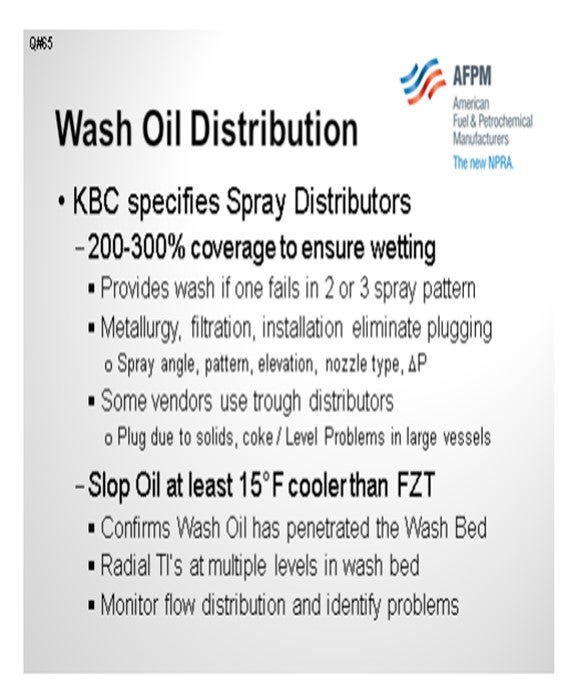
BASHAM (Marathon Petroleum Corporation)
In our experience, if the wash bed temperatures get up over 770°F or so, the coking tendency will go up. We have had beds in mild service that have lasted over 10 years. We have had beds in severe services that have only lasted a couple of years. As Al was saying, it really depends on the severity of the service. In regard to the maximum slop wax draw temperature, one of the considerations needs to be the slop wax pump seal integrity. We try to keep the slop wax pump temperature below 700°F. We do that with vacuum tower bottoms quench that is cooled and put back to the pump suction.
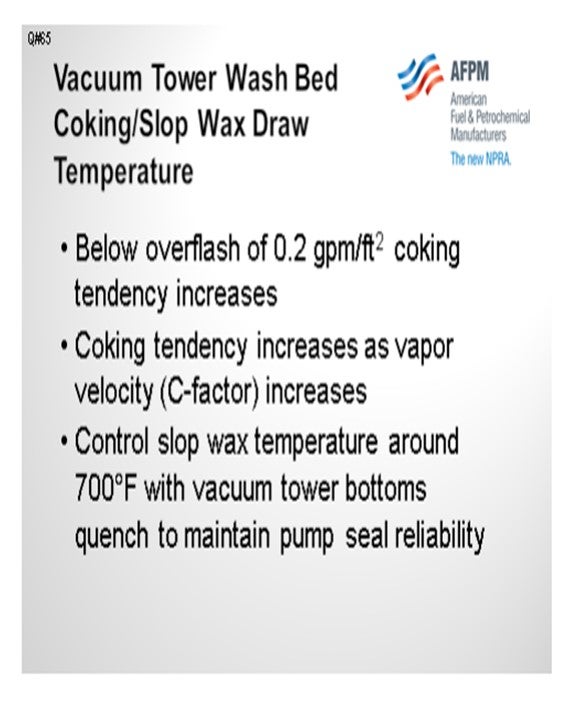
CLAY MARBRY (Roddey Engineering)
Does anyone on the panel or in the audience have any experience with recycling spent wash oil from the vacuum tower, not back to slop but to the vacuum heater inlet?
SHELTON (KBC Advanced Technologies, Inc.)
We have modeled slop oil recycle or overflash to the vacuum charge heater several times. It does not accomplish anything, except in a lube oil operation, because lube slop wax is very light and paraffinic. But in a deep-cut fuels operation, 75% to 80% of the slop oil is resid. Vacuum charge heater excess duty is better utilized by increasing feed rate or increasing heater outlet and flash zone temperatures to lift more gas oil product.
LEE (BP North America)
I will add that in our experience, we recycle the slop wax to the furnace inlet on several of our units, maybe 40% of them. However, we do find that if you are at a furnace outlet temperature limit, the slop wax recycling will cost you more duty; however, it will give you more lift. You do get a cutpoint gain, but you have to judge your unit limit.
CORY NOYES (Marathon Petroleum Company)
How do you typically set the wash rate typically? Is it done once and verified with lab results, or is anyone trying to automate that wash rate effectively based on the energy balance around the slop wax tray?
SHELTON (KBC Advanced Technologies, Inc.)
As mentioned, our models specify the overflash at the bottom of the bed, which includes the column energy balance and produces the wash rate at the top of the bed. We optimize the packing versus grid and bed height, which affects the depletion ratio. However, with some grid at the bottom of the bed, it is difficult to attain two theoretical stages because the packing height becomes excessive. In theory, we target two theoretical stages for good, deep-cut separation. In our grassroots designs, we specify radial thermowells at three levels in the wash bed. Unfortunately, after detailed design and cost cutting, very few of our units have wash bed radial temperature indicators at multiple levels. We prefer to monitor what happens in the wash zone, but there are only a few units with radial temperature indicators. We would like to see the wash zone operation optimized by monitoring temperature gradients, overflash, and HVGO yield and quality. But again, we target sufficient wash at the bottom of the bed to prevent coking.
SHELTON (KBC Advanced Technologies, Inc.)
Wash zones with 100% grid will last longer than wash beds with combination grid at the bottom and structured packing on top of the grid. For the same operating conditions, the grid will not produce the VGO recovery or the cutpoint that can be achieved with structured packing. Deep-cut designs for maximum VGO recovery are typically combination beds. There is no typical service life for vacuum column wash beds, and KBC is not aware of any vendors that provide guarantees. Crude type, severity of the operation and column design affect run lengths. The same cutpoint can be achieved at a lower transfer line temperature in a wet design with a bottoms stripper compared to a dry operation with no bottoms steam. Lube oil operations typically operate at low cutpoint with high quality, paraffinic feeds and will not be included in this discussion. Lube oil run lengths would be longer than seven years.
In fuels refineries, wash zones operate well for the normal four- to six-year run between scheduled turnarounds. For heavy crudes with high asphaltenes in deep-cut operation some sections of packing typically require replacement during turnarounds. If the question has been posed by a refinery operating under these severe conditions, a seven-year service life is better than average, particularly when processing heavy crudes at high flash zone temperatures associated with deep-cut operations.
Wash beds with structured packing over grid have wash oil depletion ratios of 5:1 to 6:1, depending on bed heights and operating conditions. Approximately 80% to 90% of the hot wash oil flow to the top of the bed will be vaporized in the bed. Targets for minimum wash oil penetration through the bed or overflash (slop oil) at the bottom of the bed are often quoted as 0.10 gpm/ft2 to 0.20 gpm/ft2 . It is important to specify if the flux rate is calculated at flowing or standard conditions. The 0.10 gpm/ft2 overflash flux rate is usually at 60°F, which is equivalent to 0.15 gpm/ft2 at operating temperature. KBC designs for 0.20 gpm/ft2 at 60°F standard conditions. Petro-SIM™ oil characterization produces the corresponding wash oil rate at the top of the bed without adjustment or design factors.
Accurate flash zone conditions are difficult to obtain for operating units. For prediction cases and vacuum unit design, KBC employs integrated VIS-SIM models of the fired heaters, transfer line and vacuum column to calculate transfer line outlet and flash zone conditions. For a specified heater outlet temperature, Petro-SIM™ accurately predicts the depletion ratio based on theoretical stages and the amount of wash oil required at the top of the bed to produce the target overflash or slop oil at the bottom and minimize coking. CFD studies show that phase separation does not occur at transfer line outlet velocities of 200 fps to 300 fps in properly designed piping configurations. Predicted flash zone temperature and pressure are a function of accurate model results for heater tube-by-tube and transfer line pressure drop profiles.
Wash Oil Coverage and Distribution: KBC specifies spray distributors designed for 200% to 300% coverage to ensure full wetting of the wash bed. Some vendors concur, and others specify trough distributors due to concerns about potential entrainment of atomized wash oil. In our experience, entrainment is more dependent on vapor velocity, the design of the flash zone inlet distributor, and the wash zone spray distributors (spray angle, pattern, elevation above the bed, nozzle type, and pressure drop). Trough distributors in the wash zone can plug due to solids and coke. Uneven level of gravity flow distributors in large diameter vessels can result in inadequate coverage of the wash bed. KBC designs spray distributors so that wash bed coverage is maintained if one of the double or triple coverage spray nozzles fails in any single spray pattern. Proper wash oil system design, metallurgy, filtration and installation can eliminate spray nozzle plugging. Although usually omitted during final design, KBC process designs specify radial temperature indicators at multiple levels in the wash bed to provide indication of flow distribution through the bed and identify problem areas.
Recommended Maximum Slop Wax Draw Temperature: The slop oil liquid temperature should be approximately 15°F cooler than the Flash Zone temperature to confirm that the lighter wash oil (HVGO) has penetrated the Wash Bed and mixed with the overflash (slop oil).
A limit should not be set on this temperature; it should be cooler than the flash zone.
BASHAM (Marathon Petroleum Corporation)
This depends on severity of the operation. As temperatures increase above 770°F, then life expectancy drops. Also, as C-factor increases, life expectancy drops. As overflash drops below 0.2 gpm/ft2 , then life expectancy drops. We have beds that have been in service for over 10 years in mild service. We have had beds in severe service that last only a couple of years. In regard to the maximum slop wax draw temperature, a primary consideration is slop wax pump reliability. To maintain pump seal integrity we recommend a maximum temperature of 700°F, which is achieved with vacuum tower bottoms quench.
LEE (BP Products North America)
We have had a grid wash bed last 20 years in Alaskan North slope service. When it was finally removed due to suspected performance issue, it was found to be in pristine condition and the bed could have gone at least another five years. We do not think a temperature limit per se is necessary, but more of maintaining an appropriate minimum bed wetting rate for the conditions and feedstock.
DENNIS HAYNES (Nalco Energy Services)
The use of KOH (potassium hydroxide) is limited compared to the more abundant use of NaOH, so there is comparatively fewer field data for KOH. It should react similar to NaOH regarding the ability to reduce chlorides for atmospheric overheads. One reason that some refiners are evaluating it is in order to reduce sodium content going to downstream conversion units, such as coker. The use will reduce sodium going downstream where there is concern in keeping this specification in greater control; however, potassium is also known to have properties (such as hydrocarbon dehydrogenation) that may increase coking. Potassium is assumed to have less detrimental properties than sodium but is not a total solution to downstream concerns.
ANDREW SLOLEY (CH2M HILL) Wash bed coking tends to be a catastrophic problem. Either the unit cokes or it does not. Many plants have achieved 20-year, or longer, service life without having a coked bed. Bed coking is caused by excessive liquid residence time at high temperatures. Keeping liquid flowing over the bed keeps the residence time down. The accepted minimum liquid rate on the bed is 0.15 gpm per square foot at the lowest liquid loading point. This will be at the bottom of the bed. Plant data has shown this liquid rate is the same for both grid and reasonably open structured packing. This value assumes good distribution of both the liquid and the vapor to the wash bed.
In operation, the plant meters or controls the liquid to the top of the bed. Liquid dryout ratios across the bed may vary from 5:1 to as high as 15:1. If the bed dryout ratio is higher than expected, the bottom of the bed will coke. This dryout ratio depends upon the pressure drop across the bed, fractionation efficiency of the bed, transfer line performance, crude composition, and cutpoint of the unit.
Very little evidence of coking will be seen for the first 10 to 14 months. After that point most units will see a noticeable pressure drop rise across the bed. However, once formed, further coking is inevitable.
A few plants chose to deliberately run with excessively low liquid rates. The objective of these plants is to tradeoff a long period with higher liquid yields (due to lower wash oil rates) versus a short period of time with lower yields due to pressure drop. The economics of this operation seem doubtful for a typical facility. The temperature difference between the slop wax collector liquid and the flash zone is more important than the absolute temperature of the flash zone. The more liquid that leaves the wash bed, the lower the slop wax temperature compared to the flash zone temperature.
The temperature difference sufficient to prevent coking will vary with the unit. The temperature difference resulting from sufficient liquid will go up if the vapor and liquid distribution to the wash bed gets worse. To maintain a minimum liquid rate at all points of the bottom of the bed, more total liquid is required.
Careful design and installation of the liquid distributor and slop wax collector tray is amply justified. So are effective control systems to monitor bed performance.