Question 64: How do you select the proper metallurgy for crude overhead (OVHD) to increase reliability?
HERLEVICH (Marathon Petroleum Corporation)
Our belief is that a proper design includes a good waterwash system and less expensive metallurgy. Our tower tops are typically carbon steel with Monel overlay. Our top trays are typically Monel. Our overhead circuits are often water-washed carbon steel with a good chemical corrosion inhibitor and monitoring program. Corrosion monitoring facilities are also important to ensure performance.
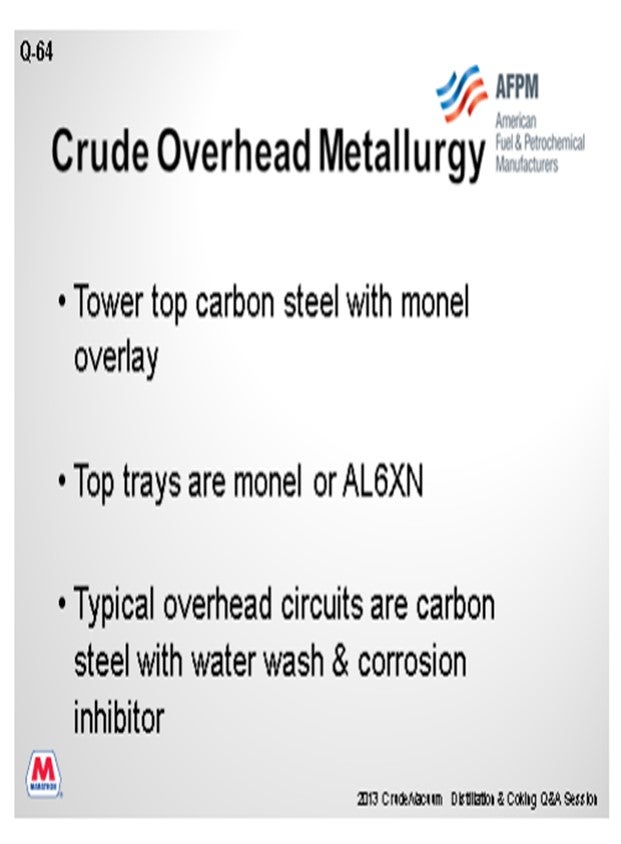
Two of our crude units have titanium metallurgy, as they exchange against the colder raw crude. A couple of our units use Hastelloy or Duplex. The decision is based on a simple lifecycle economic analysis. Of course, the last bullet on the slide suggests that when doing the design and evaluation, you really need get the metallurgists and corrosion engineers involved. There are many articles in the literature that cover this analysis.
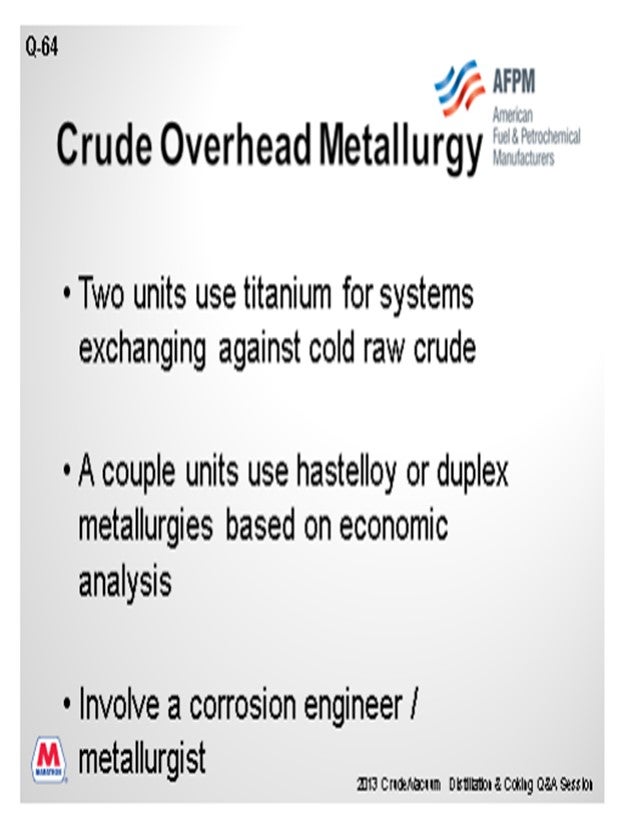
SHENKLE (Flint Hills Resources, Ltd.)
We reiterate that the metallurgy is only one part of the system that should be considered. Design considerations are based on the following:
• Feed: sulfur (S), H2S content, and total nitrogen, both ammonia and tramp amines.
• Desalter operation: efficient solids and salt removal and pH.
• Crude tower design: whether you have a single-drum or two-drum system with hot drum/cold drum operation and exchanger design
To further emphasize: The washwater system, sufficient washwater rates, and accurate DPs (differential pressures) for proper nozzle operation on washwater systems are all important when considering overhead corrosion. We further suggest that it is critical to establish an operating envelope with parameters that can be monitored and action to be taken when you are outside the appropriate operating envelope. We also utilize an ionic model to help us understand salt deposition temperatures. Additionally, we assess velocities and look at actual deposition temperatures for ammonia, tramp amine, and neutralizer amine. In our opinion, with a good monitoring program of the overhead system, carbon steel is sufficient in most applications.
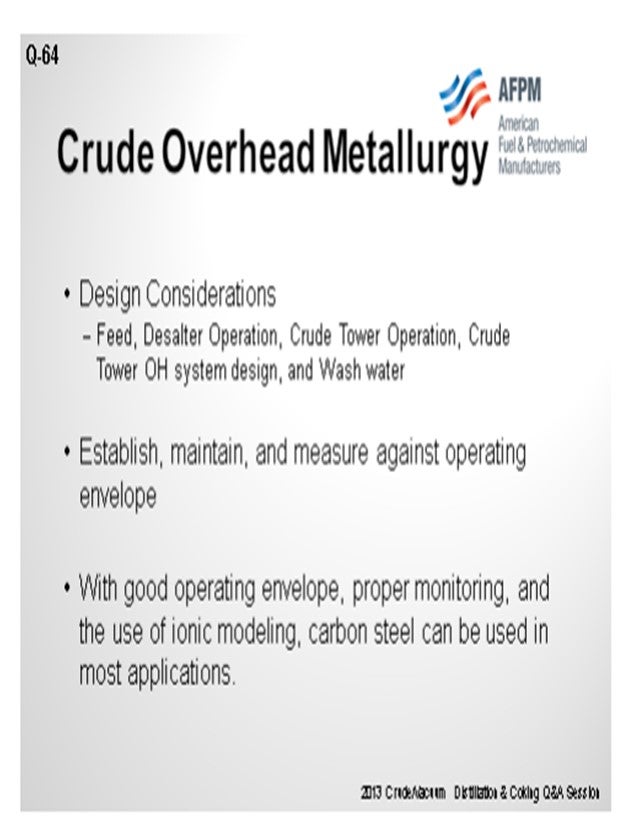
BOB SHENKLE (Flint Hills Resources, LP)
Metallurgy is only one part of the of the OVHD system that should be considered when process/mechanical reliability improvements are needed. Before metallurgy changes are made, a clear window of operation has to be established and operational guidelines must be adhered to. If the normal operation moves outside the window of operation, changes to the process must be made to bring the unit back into the window. At FHR, we use key process reliability parameters to monitor what we consider critical parameters.
To establish the required parameters, the crude unit is reviewed from upstream of the desalters through the OVHD system. Product piping metallurgy should be assessed as well. Some parameters for consideration:
1. Feed: S level, H2S content, solids content, total N (nitrogen) content [NH3 (ammonia) and amines], BS&W, TAN (total acid number)
2. Desalter Operation: washwater pH, salt out, temperature, mud-washing, solids out, N content out
3. Crude Tower Operation: pressure, temperature, flows, gas velocities, reflux return temperatures, pump around temperatures
4. Crude Tower OVHD System Design: single-drum or two-drum system, exchanger design/type (air fin, vertical, horizontal)
5. Washwater: required amount, quality, quantity, spray nozzles designed with the correct pressure drop, pump discharge pressure, location of injection of washwater
At FHR, we believe the best way to achieve reliability expectations is to incorporate a detailed Ionic Model for the overhead system and understand salt deposition temperatures. Our belief is that metallurgy to combat operating at some salt deposition temperatures can have mixed results. With a good operating envelope, proper monitoring and ionic modeling carbon steel can be used in most applications to meet mechanical reliability expectations.
DENNIS HAYNES (Nalco Champion Energy Services)
For the specific system, corrosion mechanisms and rates must be clarified, and then a review should be made of the available metallurgical, operational, and other corrosion control options (waterwash design, inhibitor application strategy, etc.). The review should include information on acceptable equipment life and risk minimization to assist with the selection of the appropriate metallurgies for the overhead environment under review.