Question 62: What criteria are used to evaluate the performance of crude pre-heat train exchangers to support a decision to clean any portion?
PRIBNOW (CITGO Petroleum Corporation)
It is essential to keep crude pre-heat exchangers clean. Cleaning benefits are hard to justify if they negatively affect crude rate. The criteria we use are crude hydraulic throughput, heater firing limits, fuel gas savings, desalter temperature efficiency, or crude or vacuum tower heat balance if you have needs in that area to remove heat. Each of these criteria at CITGO is periodically monitored by the process engineer or unit engineer and unit personnel to determine if action needs to get taken. If the fouling factors increase, we will increase monitoring of that exchanger and begin to make plans to take it offline in the near future or next opportunity.
The most common methods we use at CITGO are rather simple: pressure surveys and U-factor or duty calculations. For the crude hydraulic restrictions in your pre-heat, perform pressure surveys. Find out what bundle has the greatest impact, or which will give the crudest throughput recovery, and then clean it. The exchangers should be ranked in order of greatest to least impact. Compare the design conditions with the start-of-run conditions. If bypasses around exchangers are utilized to increase crude throughput, downstream relief capacities must be checked, and heater inlet temperatures monitored.
Perform U-factor or duty calculations for heater firing limits, desalter temperature, and fuel gas savings. Rank the exchangers by the most fuel gas saved at the heater. If you are cleaning an exchanger at the beginning of the preheat train, recovery factors need to be considered. A 20°F increase at the exchanger will not gain 20°F at the heater inlet. Consider this when performing economic evaluations. For the crude or vacuum tower heat balance or heat removal issues, then target that section of the tower and clean those bundles.
Another method for determining which exchangers to clean is a rigorous model. I have seen a couple programs that model crude pre-heat trains. These programs model heat integration within your crude towers and are able to predict the inlet temperature of your heater. We do not currently utilize that at CITGO. We prefer the simple go-out-in-the-field-and-look method.A couple of points to keep in mind: When exchangers are taken offline and bypassed, understand how this will affect the crude or vacuum tower heat balance. If parameters are not set properly beforehand, the crude or vacuum tower may become upset, which may result in product quality or pressuring of the tower. We experienced one event when we almost had to abort a cleaning because taking the exchanger offline resulted in an increase in crude tower pressure. We learned from that event. Now, we make sure to predict the heat balance change and adjust tower crude rate or heater firing as necessary prior to taking a preheat exchanger offline to clean.
HERLEVICH (Marathon Petroleum Corporation)
Just to add onto the cleaning piece: At our refinery, we recently made a procedure for evaluating whether it is actually acceptable to take bundles offline or bypass equipment. This has not typically been an issue in the crude pre-heat train because they were designed with online cleaning in mind. However, our practice is to review anyway because we have found several instances where downstream equipment was not rated for the bypassing scenario MAWT (maximum allowable working temperature) or sometimes the blocked-in case MAWP (maximum allowable working pressure).
We monitor the heat exchanger performance at Marathon, in most plants, by using a simple spreadsheet-based model as well. We have standardized on a corporate-supported, macro-driven, performance monitoring spreadsheet that was developed in-house. We used these on all units in the refinery, both for heat exchange and for basic catalyst performance. We monitor the heat exchanger performance in terms of actual heat transfer coefficient (UA) compared to start-of-run clean conditions. We also track heat exchanger pressure drop through field measurement. Once again, we often employ our college co-op workforce for these activities. Next, a simple economic analysis is conducted to compare rate reductions versus fuel gas savings. Most of our plants also do a ready-to-run analysis, which that typically results in spring heat exchanger cleaning programs.
A couple of points to keep in mind: When exchangers are taken offline and bypassed, understand how this will affect the crude or vacuum tower heat balance. If parameters are not set properly beforehand, the crude or vacuum tower may become upset, which may result in product quality or pressuring of the tower. We experienced one event when we almost had to abort a cleaning because taking the exchanger offline resulted in an increase in crude tower pressure. We learned from that event. Now, we make sure to predict the heat balance change and adjust tower crude rate or heater firing as necessary prior to taking a preheat exchanger offline to clean.
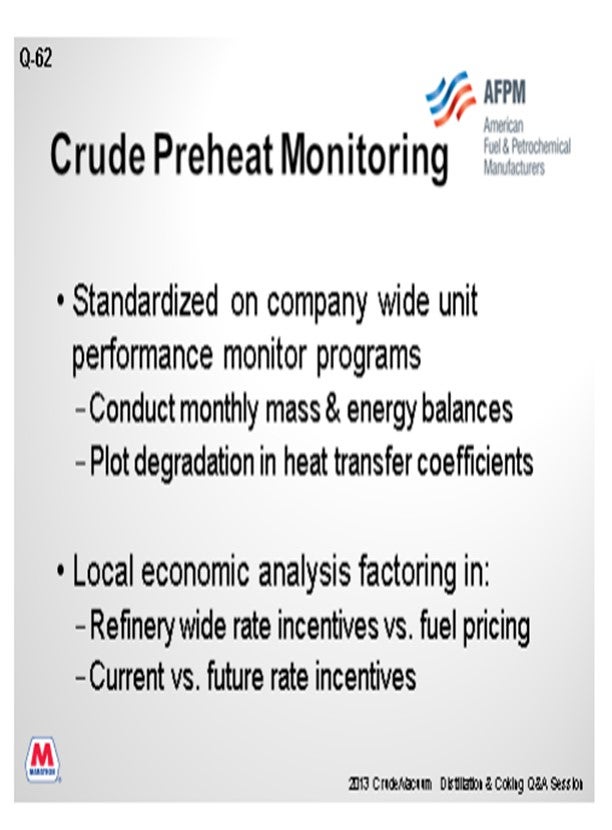
The next slide shows a graph from the performance monitor. This macro-driven, Excelbased software produces graphs that the tech service engineers include in their monthly reports. The results are analyzed to estimate fouling trends. You can see the UA and the duty for this particular set of exchangers in the graph.
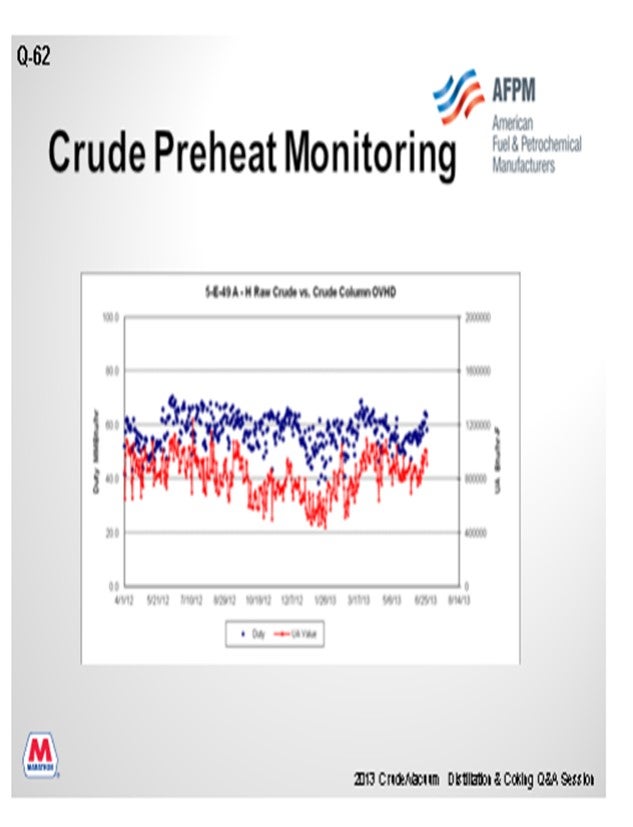
The last slide lists the typical configurations for our crude units. In our bigger refineries, we have complete dual trains on the heat exchange side. During the spring exchanger cleanings, we will reduce the rate on those crude units to clean one heat exchange train at a time. In the medium-sized crude units, we tend to take off the individual exchangers or smaller batteries of exchangers. Finally, we have one small refinery that idles the entire unit for heat exchanger cleaning. This process is often conducted in sympathy with work on other refinery other units.
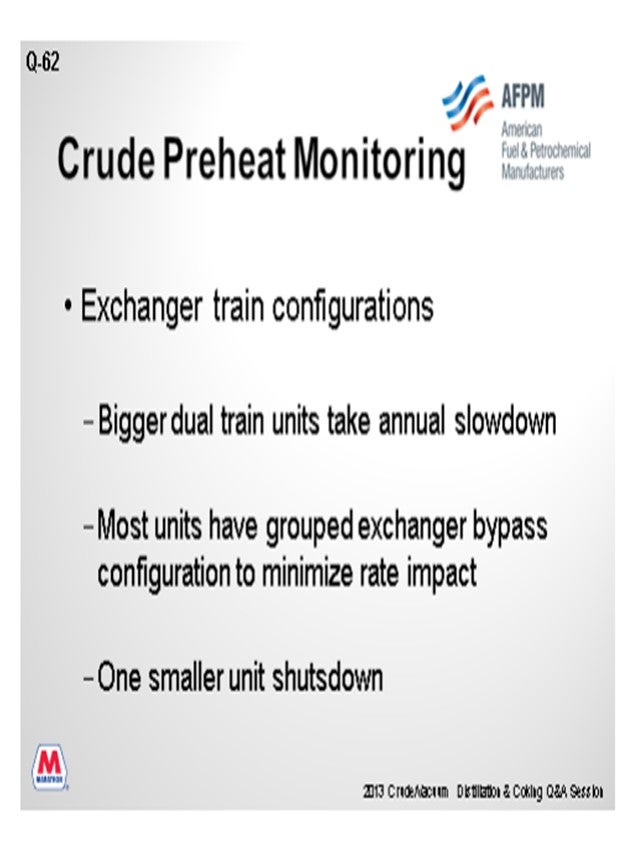
VICTOR TAILOR (Commonwealth Engineering & Construction)
The panel covered the entire pre-heat train potential problem well. I want to add that in a revamp case, you should consider the pressure drop through the heat exchanger when calculating the desalter charge pump to make sure that it has enough head, even at a slightly higher pressure drop. This pump needs to be very generously sized. In this way, you avoid reducing crude charge for a longer period of time.
TOM GERMANY (Calumet Specialty Products Partners, L.P.)
Has anyone on the panel used online thermal shocking of exchangers to clean in lieu of taking them off mechanically?
PRIBNOW (CITGO Petroleum Corporation)
Yes, we have heard of a couple of techniques in the cold pre-heat train.
SHENKLE (Flint Hills Resources, Ltd.)
We have not.
HERLEVICH (Marathon Petroleum Corporation)
No, I am not aware of our doing that.
HAROLD EGGERT (Athlon Solutions)
On units that are being monitored for crude pre-heat trains, we have noticed that when there is an upset, power failure, or shutdown, after the shutdown and startup, there is some significant heat gain recovery. It is, again, the thermal shock. The tube shrinks at a different rate than the fouling that is on there, resulting in some of the material breaking loose. I think some of that is being employed in a cold train, too.
HERLEVICH (Marathon Petroleum Corporation)
Just one more thought to add to that. We have seen times where we take down exchangers and prep them by conducting steamout and cleanup. Then where we have put them back online without any mechanical cleaning, they do still work much better. Once you discover that this process works, it may actually become routine. So take a look at that.
DENNIS HAYNES (Nalco Champion Energy Services)
The use of a heat exchanger rating program that can look at individual exchangers and how they relate to the overall system performance is the best method to rank the exchangers based on impact to the system due to fouling condition. Look at fouling rate, and then develop a cleaning schedule.
CHRIS CLAESEN (Nalco Champion Energy Services)
An intelligent way to look at this is by the determination of the total cost of operation (TCO) for each exchanger. The exchanger TCO consists of the additional fuel-burning cost required to generate the duty lost by fouling, cleaning costs (which are the additional furnace duty when offline), and fixed costs for chemicals, equipment, and manpower. More frequent cleaning reduces the additional fuel burning cost, but also increases the cost of cleaning. Clearly, there must be an optimum time to clean an exchanger, which will give the minimum cost, and this can be calculated. The exchanger network and individual exchanger fouling rate should be routinely calculated and tracked to maintain an optimum cleaning schedule using exchanger model software, such as NALCO’s Monitor™.
GARY HAWKINS (Emerson Process Management)
Emerson Process Management offers a heat exchanger health monitoring solution that calculates the duty on both the hot and cold sides (should be the same, alerts if too much deviation) and the current value of the heat exchanger coefficient. Changes in the heat exchanger coefficient are indicative of fouling. The rate of change of fouling is also calculated, and alerts can be generated to warn of potential crude instability leading to accelerated fouling of the exchangers.
PATRICK TRUESDALE (Emerson Process Management)
One problem facing refiners gathering all of the temperature measurements around each tube-and-shell bundle in the crude pre-heat train. Often, capped test thermowells are provided for periodic measurements taken manually. This option presents a refiner with the opportunity to take advantage of wireless temperature transmitters utilized to bring these missing temperature measurements into heat exchanger health monitoring solutions.