Question 61: When performing catalyst evaluations and considering catalyst resistance to attrition about particulate matter (PM) emission requirements, what new or advanced attrition testing methods are you using to predict the performance of the new catalyst system? Are there third parties who can conduct a standard testing regime to multiple catalyst systems?
FEDERSPIEL (W.R. Grace & Co.)
As I said earlier, the average age of FCC e-cat in a unit inventory is between 20 and 100 days. Clearly, there is a distribution of particles. Some are much newer; some are much older. So, it is not at all practical to mimic exactly what is going on in the FCC to judge how a catalyst might break apart. Therefore, we use an accelerated wear test as a proxy for measuring the probability of attrition on a catalyst. There are several different types of accelerated wear tests. There are cyclone tests, which are a more elaborate method because they do require a large quantity of catalyst. There is the air jet method. The primary mechanism for attrition there is particle-to-particle impact. And then, there is the jet cup method, which has both particle-to-particle and particle-to-wall effects.
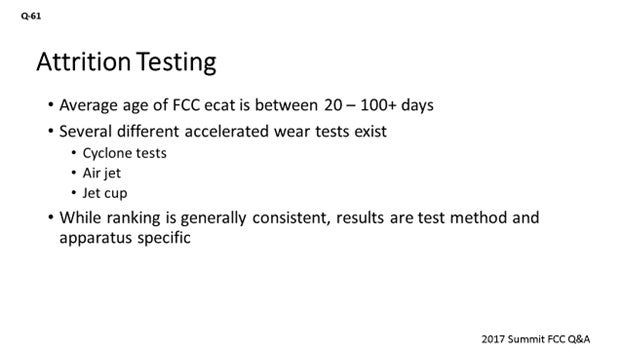
This next slide just shows the details about the most common attrition mechanism: abrasion. Using an accelerated wear test that simulates abrasion is a realistic method to pursue. The test procedure separates the elements that are uniformly distributed within the particle from those elements that are expected to be concentrated on the surface. The test method then compares the ratio between the fines and the e-cat for those elements. So, what we see is that elements which are concentrated on the surface are shown or overrepresented in the fines or they have a higher ratio in the fines. What that tells us is that the main attrition mechanism inside an FCC unit is driven by abrasion of catalyst particles. That makes sense, too, because fracturing has a higher energy requirement to fracture a particle than it does to abrade the surface.
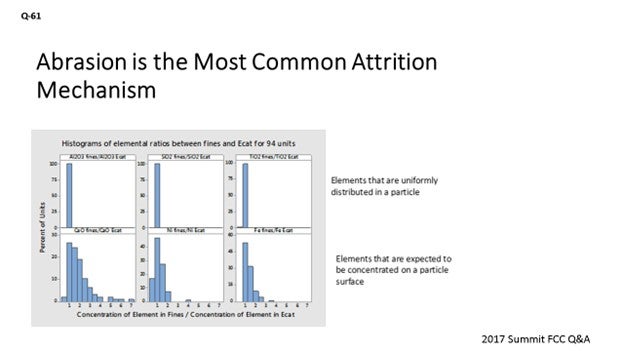
Now I will talk really quickly about the different mechanisms. The jet cup, the air cup, and the cyclones will have similar rankings, but they will not have the same number scale. You do need to find a single laboratory to compare them, because the method – and even the apparatus used in that same method – will have an impact on the result you get for the attrition testing.
DINKEL [Marathon Petroleum Corporation (MPC)]
In an earlier response, I mentioned that we have our own pilot plant, so we do our own jet cup analysis via the original Grace method to supplement our activities there. We utilize a pass/fail test, which is a good indication of whether or not we will have circulation issues within the pilot plant. We have also used that analysis to help with troubleshooting on some of our commercial units in the past.
The second bullet point mentions ASTM (American Society of Testing and Materials) Round Robin tests for comparing the variety of different test methods utilized in industry. Our central lab participated in the test, along with approximately 10 different suppliers and independent labs. We know what Grace uses from Mike’s response. BASF and Albemarle utilize different equipment and test methods than Grace and each other. PSRI (Particulate Solid Research Inc.) has also done testing on the jet cup. In their research, PSRI found some issues with attrition not being quite as reflective as they would have liked to have seen. As a result, PSRI developed their own test method, including equipment and procedures. The end goal is the analysis of all of this data from this ASTM study to see if ASTM can possibly come up with a standardized test.
The last part of the question is about independent labs for testing. I mentioned PSRI. As a member company, we have access to their attrition testing findings. PSRI also conducts contract research, so they are one option for independent testing. CPERI (Chemical Process & Energy Resources Institute) in Greece does independent testing. Cat Testing Labs in Savannah is another option that would allow you to evaluate catalysts from different suppliers and have an independent view of the test results.
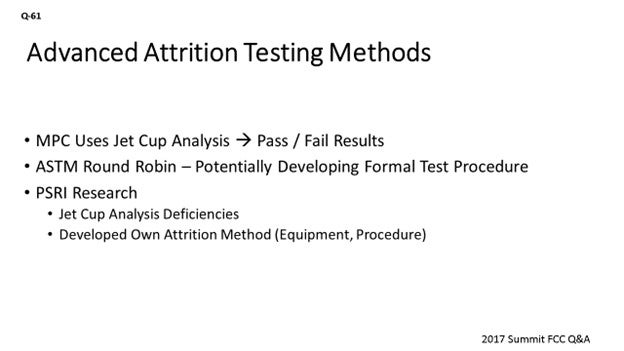
RIK MILLER (Phillips 66)
Phillips 66 operates a standard jet cup test to measure catalyst attrition. About 12 years ago, we became very interested in not just measuring the attrition indices of catalysts, but also measuring the particle size distribution of the attrited products. It was very important for us to know not just how much of a catalyst broke up, but also what it broke into, because flue gas particulate capture equipment varies in efficiency. So, we began to analyze the attrited products from the jet cup test to determine their particle size distribution, and we found significant differences from one catalyst to another. The catalysts might have the same attrition index but produce a very different attrited particle distribution. We found the results of this test to be very important as they were predictive of the performance of catalysts in our commercial units.
MICHAEL FEDERSPIEL (W.R. Grace & Co.)
A number of operating factors influence catalyst losses from the regenerator that can lead to particulate matter (PM) emissions. These factors include: the number of fines present in the freshly added catalyst, the number of fines generated in the unit, the amount of catalyst transport to the cyclones by entrainment, and the cyclone performance. Fines are the most important factor in catalyst losses, because the fines are most readily lost by the cyclones and the collection efficiency of cyclones drops as particle size drops. FCC catalyst fines (0-20 micron) can come from either fresh catalyst that is added to the unit or be generated via attrition while the catalyst circulates in the unit. Catalyst can experience attrition in the unit from either fracture (catalyst breaking into smaller fragments due to severe impact of the particle against a solid surface, severe impact against other particles, or impact from a jet of steam or air) or due to abrasion were rubbing against a solid surface or other particles erodes the particle at the outer surface and produces fines. Abrasion has a lower threshold energy than fracture18. While both fracture and abrasion occur in FCC units, abrasion is the dominant mechanism of fines generation in most FCC units. The evidence for this is that the fines for most units are enriched in surface contaminants such as calcium, iron, and nickel. If abrasion is the dominant mechanism, one would expect fines to be enriched in surface contaminants; while if fracture were the dominant mechanism, one would expect the fines composition to be the same as the bulk e-cat. Figure 1 presents data for 94 units where the concentration ratio of an element in fines versus e-cat is presented. As seen in the graph, there is no enrichment in fines in elements that are uniformly distributed in a particle (such as aluminum, silicon, and titanium), but there is strong enrichment of the fines of many units in the surface contaminants such as calcium, nickel and iron.
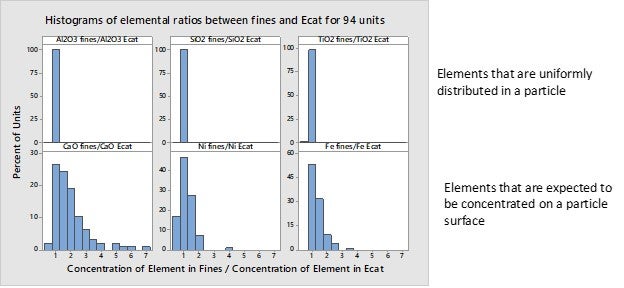
Figure 1. Abrasion is the most common mechanism, based on evidence that fines for most units are enriched in surface contaminants such as Ca, Fe, and Ni.
There are a variety of lab methods that have been used to simulate – in the lab – the particle attrition that occurs in a commercial unit. They all involve subjecting catalyst to more severe attrition than is experienced in a commercial unit. One sophisticated method involves passing the catalyst through a series of cyclones at high velocity19. These cyclone tests provide insight into attrition fundamentals, but the large amount of sample required, and the long testing times prevent their use for routine testing of catalysts for attrition. The most common test methods for routine catalyst testing are methods based on the air jet and the jet cup. In both methods, the catalyst is subjected to a high-velocity air stream, which results in fines generation. The number of fines generated is a measure of the attrition resistance of the catalyst. In the air jet method, most of the collisions are particle/particle; while in the jet cup method, both particle/particle and particle/wall collisions occur. Examples of attrition testing equipment based on the air jet method are ASTM D575720 and the designs of Forsythe and Hertwig21 and Gwyn22. Examples of attrition testing apparatus based on the jet cup method include the Davison Index (DI)23,24 and jet cup equipment developed by PSRI25 and other labs26. There are several jet cup designs reported in the literature. It is important to note that the dimensions, volume, and configuration of the jet cup all play a role in its performance and that some jet cups – described as “Davison-type” jet cups – are not the same as the jet cup used in the Davison Index test method practiced by Grace.
We are often asked how jet cup methods compare to the ASTM D5757 air jet method. Attrition resistance measured by ASTM D5757 (an air jet method) and by Grace’s DI test (a jet cup method) give comparable results in that lower values on each scale are more attrition resistant. It is not possible to directly correlate the scales of the two tests since they are different apparatus, but they tend to give values of the same order of magnitude. In round robin testing with an external lab, Grace found that those two methods gave the same ranking regarding catalyst attrition27. Similarly, a recent paper by Kukade, et. al.28 found that the performance ranking of catalysts did not vary between ASTM D5757, a cylindrical jet cup, and a conical jet cup. While the methods give similar rankings, it is important to remember that their scales differ; so, testing with the same method is necessary for an “apples-to-apples” comparison between catalysts.
For third-party testing of catalyst systems, we are aware of two organizations that conduct this testing: CPERI (Chemical Process & Energy Resources Institute) and PSRI (Particulate Solid Research Inc.)
BRYAN DINKEL [Marathon Petroleum Corporation (MPC)]
MPC uses a jet cup analysis to evaluate catalyst attrition. Testing follows the original Grace Davison procedure and generates a Davison Index (DI) value. MPC uses the jet cup analysis as a pass/fail test. Fresh catalyst samples possessing a DI value of less than 10 pass the test, while samples showing DI values greater than 20 fail. FCC e-cat (equilibrium catalyst) samples have DI values below 2, while fresh catalyst samples typically have DI values between 3 and 10. Samples that fail the attrition test are flagged for further testing. Commercially, we have encountered opacity problems when catalyst samples consistently fail the attrition test.
Each supplier has different equipment and/or conditions for testing, which makes it difficult to compare results from the different suppliers. ASTM D32.02 is developing a formal test procedure for the jet cup (WK34893), which may lead to a standard test.
As members of Particulate Solid Research Inc. (PSRI), we are aware of some of the deficiencies of the traditional jet cup test identified through their research efforts, which have included CFD modeling and high-speed video with a Plexiglas apparatus. PSRI used this information to develop its own testing equipment which can be used for membership testing or on a contract basis with individual companies. Additional information on this test equipment can be found in the article entitled “Jet Cup Attrition Test”29. In addition to PSRI, CPERI and Cat Testing Labs Inc. are other independent testing labs that can provide subjective testing when comparing catalyst options from multiple suppliers.
MELISSA CLOUGH (BASF Corporation)
There are many test methods available to evaluate attrition resistance, each with pros and cons. The best test method will meet the following criteria: It 1) is able to match the unit’s attrition profile, either predominantly abrasion or fracture, 2) is standardized and repeatable so that data are comparable, and 3) matches the FCCU’s overall material loss over the test period. The most common methods include the ASTM Air Jet, DI Jet Cup, and PSRI Conical Jet Cup. The Air Jet is the only ASTM-certified test method and thus represents the most standardized and repeatable test available. Air Jet also is predominantly abrasion (breakage into little particles from the surface of a catalyst particle) as opposed to fracture (e.g., breakage in half). An assessment of over a dozen refinery FCCU attrition mechanisms via population balance modeling indicates that the majority of attrition happening in the unit is via abrasion. Thus, Air Jet is both standardized and represents the majority of the attrition mechanism that can be seen in an FCCU. Air Jet can also mimic material loss of an FCCU over the test period. The DI Jet Cup method is predominantly fracture. Further, the mass loss is heavily hindered due to stagnation of material in the bottom of the cylindrical cup. Therefore, the majority of the catalyst is not being tested during the one-hour duration. The PSRI Conical Jet Cup improved on this by changing the shape of the holding vessel, which removes the stagnation problem. Third-parties available for this type of testing include PSRI in Chicago and CPERI in Greece.