Question 61: What are the advantages and disadvantages of preflash/pre-topping columns in crude units in terms of operational flexibility to process different API crudes? Please comment on overall energy efficiency and reliability (corrosion).
ALLRED (Suncor Energy, Inc.)
At our refinery in Commerce City, we have three separate crude units. One crude unit has a classic preflash drum with the vapor going to the flash zone in the atmospheric tower, which is very typical, as shown on the drawing.
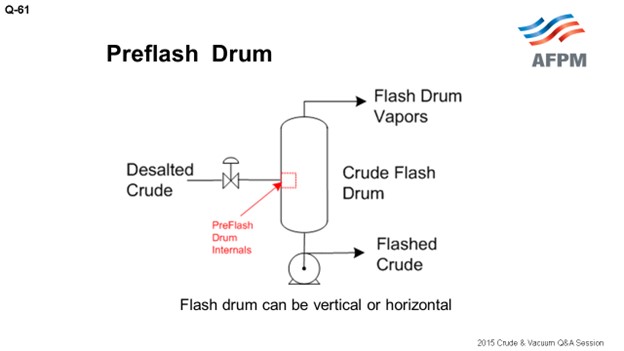
Another one of our crude units has a preflash tower with its own independent reflux system. The advantage here is not shown on this drawing, but you can have a side-draw of light liquid products.
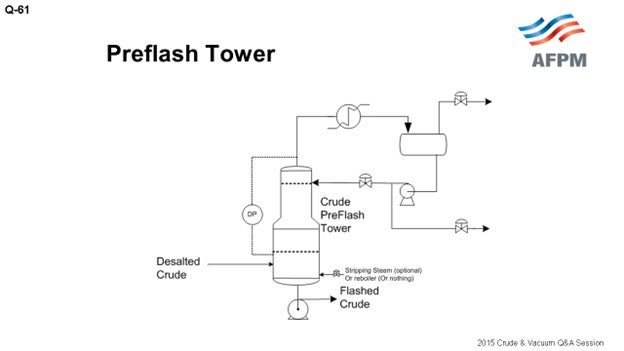
Our third unit has a very convoluted arrangement. I am not going to show any drawings of it. It is an old unit that has evolved in a very unique way, but it has what we could call a preflash tower. It has a single overhead reflux that is combined with the atmospheric tower. The atmospheric tower overhead vapor comes back into the middle of this preflash drum. You would never design a unit like this today, but it is an older unit that evolved that way.
Preflash drums are useful for removing the vapor from the feed to the atmospheric tower, but there is a lot of debate about its purpose. Many people believe that this is done for energy purposes, but I think those who really study this come to the realization that it is not for energy. You are doing it for hydraulic reasons. You are trying to get the vapor out of the piping without having larger furnace tubes and piping hydraulically going to the atmospheric tower.
In theory, the optimal location to send the vapor is the spot on the atmospheric tower that most closely matches what that vapor looks like. But in practice, that can lead to a lot of problems because foaming is the biggest problem in preflash systems. It is not really a matter of “if” it is occurring; but rather, to what degree it is occurring. Have you designed your systems adequately to make sure you are not getting a lot of foaming that then hits your tower? If so, then the reason people send preflash vapors to the flash zone is so that the black products, which end up in that vapor, will not contaminate your lighter side-draws. Some people put in vortex clusters to knock out the foam. I have no experience with them, but I understand they can be effective.
The advantage, as I mentioned before, of having a preflash column is that you can have your own overhead reflux vapor recovery system. You can then take some liquid drawn off the side of that tower and recover some product. If it is adequately sized, you can still manage your issues with foaming and sulfur. There is a really good, detailed discussion on foaming and preflash systems, drums, and columns in Question 62 of the 2012 AFPM Q&A.
Another option is a hybrid that uses liquid from the atmospheric tower reflux to the preflash column. I am not very familiar with this option, but I read about it in the recent Petroleum Technology Quarterly. The article claims that energy efficiency is much improved in this arrangement from a typical preflash column.10 The claim seems plausible. Technically, the bottom line for corrosion, operability, and flexibility is that you just need to understand that the size your crude range needs to be in order to adequately allow for the flexibility you need.
PRICE (Fluor Corporation)
I echo everything Bruce already said, and I want to add a couple points. Sometimes you can debottleneck a unit by 10 or 20% with a light crude by adding a preflash tower. It can be energy-efficient; but equally important, as Bruce noted it, it debottlenecks the flashed crude preheat train and the heater.
However, a preflash tower is not always energy-efficient; but sometimes, it does end up that way! The energy savings associated with the addition of a preflash tower depends on the location of the heat transfer surface area, what cutpoints you are after, and which piping and controls you have to work with. One of the other benefits we see with a preflash tower is that by removing the light paraffins (and by light, I am talking about C5 and lighter), you can significantly reduce the asphaltene precipitation and fouling in the downstream exchangers.
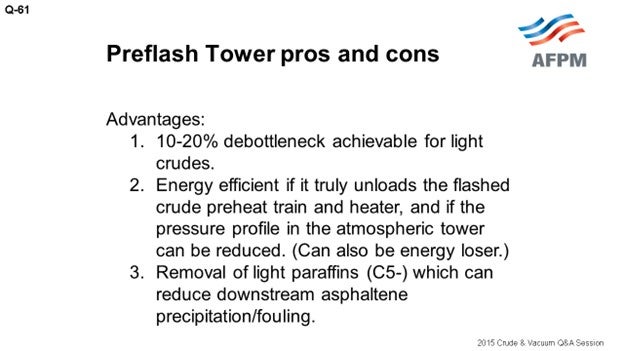
When you do add in a preflash tower as a revamp, consider the fact that you will significantly change the vapor traffic in the atmospheric tower unless you compensate somehow by either increasing your stripping steam, lowering your pressure, or having a higher heater outlet temperature. The light gases being taken out in the preflash tower actually do have a stripping effect and will increase your diesel yield. This stripping effect is sometimes small, but you do actually need to check and make sure you understand the impact.
The other consideration is that the water dew point in the preflash and atmospheric tower will change based on the crudes you are running. This is very important. Watch your overhead temperatures to ensure that you have adequate margin above the water dew point in all operating scenarios.
The last comment is that if you have a highly variable crude slate with a significant crude gravity range, it will add some complexity to the design. Designing for a crude slate with a wide range of gravities is doable (safely and reliably), but you do need to understand the parameters up front.
As Bruce said, if you just have a flash drum, you really need to be bold to route the flashed vapor somewhere other than the atmospheric tower flash zone. Routing the vapor directly to the atmospheric tower flash zone will debottleneck your flashed crude preheat exchangers; however, the flashed vapor has a tail (heavy end distillation) due to the single-stage nature of this drum.
With respect to the risk of foamovers, they happen. A properly sized drum will help mitigate them, as will the use of some sort of cyclones or vortex internals. Equally important is that whatever you have must be instrumented well, so you will know what to watch to maintain an upper hand and manage any foaming problem when it happens. You need to have instrumentation to watch your pressure, levels, and flow rate in the flashed crude. You will see, depending on the instrumentation in your unit, the indications come up (hopefully) before the foaming hits the main fractionator.
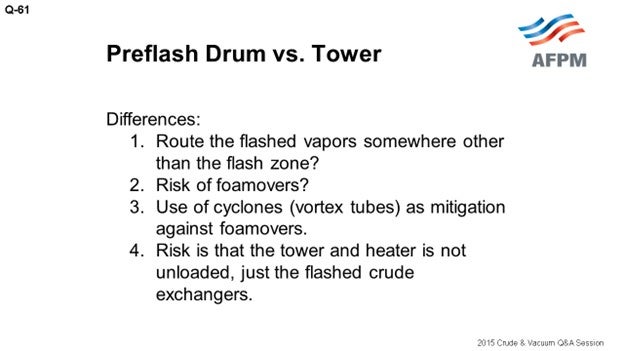
NAGASHYAM APPALLA (Reliance Industries Ltd.)
What is the Best Practice for monitoring the foaming incidence in the flash drum?
ALLRED (Suncor Energy, Inc.)
It is important to monitor the color on your products on the side drawer of the preflash tower because that is where you will see it first.
PRICE (Fluor Corporation)
We encourage people to watch for instability in their flashed crude flow rate, in the level, and in the pressure, as well as watching your pump for cavitation. We feel like that is where you will see it first.
CELSO PAJARO (Sulzer Chemtech USA, Inc.)
Just to clarify, if the preflash has a level glass gauge, you should see the foam there. The second point is that we have designed vortex tubes for preflash columns and preflash drums, and they work well. On our website, we have a video showing how it works. You can see how the foam is reduced between having nothing and just adding the foam-breaking element.
HAROLD EGGERT (Athlon Solutions)
You can also install a TI (temperature indicator) on the vapor out of that flash drum and watch the temperature. The temperature will change as you see increased foaming. The second part of this question is a commercial for this afternoon’s Principles & Practices session. There will be a session discussing Best Practices for caustic injection, and there are some interesting phenomena around the foaming in a flash drum, depending on where you put in the caustic for chloride suppression. So I encourage everyone to come to the P&P session this afternoon.
ANDREW SLOLEY (CH2M Hill)
If you are going to have a nuclear-level device in one place in a refinery, it would be on the preflash drum or tower bottoms. Some type of radiation instrument for online density and level measurement will greatly improve performance. There are other ways to monitor the foam level. But in these situations, by the time you notice it using other methods, the foaming event has already occurred. This is one place to spend money to make sure that if a foaming event happens, you will be able to react to it in real-time to prevent foam from entering the crude column.
LUIS GORDO (Amec Foster Wheeler)
Increasing diluted bitumen, synthetic crudes, and tight oil crude components in the feed increases the amount of light material that must be processed through the refinery (higher API feed). Depending on how the crude diet changes, the increase in light materials can be significant. This is often one of the limits to leveraging the typically discounted pricing of domestic tight oil.
Many refiners find that their ability to blend light tight oils into their feedstocks is restricted by the higher content of light materials [LPG (liquefied petroleum gas) and naphtha] in the crude. Preflash towers offer the advantage of debottlenecking crude preheat trains and atmospheric tower overhead sections in order to enable higher volumes of crude to be processed. Typically, preflash towers should be located after the desalter in order to mitigate corrosion/fouling. This spot is also convenient as a crude booster pump is almost always required at this location. Foaming is a concern for the design and operation of preflash towers/drums. Superficial liquid velocity must be kept below a certain threshold. Specific internals, such as vortex clusters that separate liquid and vapor by means of centrifugal force, can be considered. If the preflash tower is equipped with distillation trays/top reflux, there is a reduction in crude preheat temperature that must be offset by the crude heater.
In addition, if there is a plan to process heavy crudes also, then preflash towers need to be evaluated for the same due to lower light end loads. If this flexibility is required, then a preflash drum may be a better choice.
Economics that come into play are:
-
Increased Profit through incremental unit throughput,
-
Operating Expense of preflash tower condenser and pumps versus furnace firing cost, and
-
Capital Expense including modification of hot preheat train, crude tower overhead, and possibly furnace tubes versus new preflash tower, condenser, overhead drum, and pumps.
ANDREW SLOLEY (CH2M HILL)
Preflash drums and towers are a relatively complex subject. For revamping an existing unit, the addition of either may help the plant by relieving specific equipment constraints. The successful addition of a preflash unit requires a detailed knowledge of the existing equipment limits which requires a detailed analysis of unit performance based on validated plant data from test runs. No neat guidelines exist for general rules when adding a preflash when specific and complex constraints are involved.
For new units, specific situations merit preflashes. Having a preflash will generally allow for more flexibility to move toward both very light (45+ API° gravity) and very heavy (20- API° gravity). Specific examples where preflashes help unit flexibility are:
-
Very light crudes, limits on heater outlet vaporization: Recovery of very light crudes can be limited by heater outlet vaporization. Excessive vaporization can increase heater coking rates due to low liquid irrigation of the heater outlet tubes. A preflash removes some of the vapor, increasing liquid fraction at the atmospheric heater outlet.
-
Crude blends, asphaltene precipitation: A preflash can selectively remove C5- material from the crude. This may reduce asphaltene precipitation when processing a blend of light crude-heavy crude.
-
Aggressive heat integration, high heater inlet temperatures: A preflash may allow for lower inlet pressures to the fired heater when heat integration is very aggressive. This would be likely when running light crudes over a 525°F inlet temperature or heavy crudes over a 565°F inlet temperature. With current gas pricing in North America, highly aggressive preheat train outlet temperatures are typically not economical. However, the economic basis is different for many European or Asian refiners. Heat integration with extremely light crudes may benefit from a preflash at temperatures below 525°F.
-
Heavy crudes, desalter water removal: With heavy crudes, the desalter may leave a significant amount of water in the crude. A preflash may act as a dehydrator (water vaporizer) upstream of the hot train.
In general, preflash drums have a minimal impact on unit corrosion. They may marginally reduce salt hydrolysis by drying the oil. However, the change is small.
Preflash towers that have separate overhead systems from the crude distillation tower significantly increase atmospheric tower overhead corrosion problems. The preflash tower removes light ends from the atmospheric tower feed. This greatly increases water partial pressure in the atmospheric tower overhead, making aqueous chloride corrosion more severe. The increased corrosion normally holds true even if the removal of light material changes the atmospheric tower pressure profile.
For existing units, adding a preflash drum or preflash tower nearly always makes the unit less energy-efficient. Exceptions include when the unit has a very low atmospheric heater inlet pressure that limits heat integration or if vaporization in the preheat train is already creating large pressure drops.
For new units, the situation is ambiguous. On a constant return basis, adding a preflash tower may either increase or decrease energy efficiency. The result depends upon targeted crude preheat temperature, crude vaporization, crude gravity, preflash type, cost of firing versus cost of steam, product temperature to downstream units, and other factors.
BRUCE ALLRED (Suncor Energy U.S.A.)
At the Suncor Commerce City refinery in Colorado, we have three crude units with three separate preflash configurations. One crude unit has a typical preflash drum with overhead vapor going to the atmospheric tower flash-zone; one unit has a preflash column with an independent overhead condenser and reflux system and a side-cut draw; and, the other crude unit has a unique, convoluted quasi-preflash tower with a single overhead condenser and reflux system which also handles vapor from that atmospheric column that vents back to the middle of the preflash column. Each of these systems has their unique characteristics and limitations.
Preflash drums are useful for removing vapor from the feed to the atmospheric tower furnace. This is done to reduce unnecessary heat absorption into material that is already vaporized and to eliminate difficulties that can be encountered in control valves which would see two-phase flow, particularly in a multi-pass furnace. The use of a flash drum reduces process piping and furnace size due to the lessening of two-phase flow hydraulics. In theory, the optimal location to send the vapor is to the spot on the atmospheric column that most closely matches the vapor steam. However, the reality is that most refineries with preflash drums send the vapor to the flash zone. This is done since preflash drums can be prone to have foaming and carryover of heavier liquid, which puts reduced crude in locations not designed for reduced crude. This leads not only to dark light oil products, but it can also put sulfur or naphthenic acid into places that were not designed for it. The downside to sending the vapor to the flash zone is that the vapor will quench the temperature in the flash zone, so the furnace outlet temperature must be set to compensate. Since the drum, overhead line, and furnace sizes are already fixed in a refinery, there is limited flexibility for opportunity crudes unless the sizing of these components allows for the changes in flow hydraulics, heat transfer, etc.
A preflash column can be a better option if it has its own reflux and vapor recovery. It allows for a side draw of light products and, if adequately sized, may provide flexibility for variable API feeds depending on loading and turndown. The downside to a preflash column is the money required to build, maintain, and operate a separate overhead reflux system. And also, just like a preflash drum, you need to watch out for foaming in the tower and low velocities in furnace tubes, which may cause premature coking of the furnace tubes. If much lighter crude is run, the preflash tower may be too small and still be susceptible to foaming and liquid carryover. For more detailed discussions on foaming in preflash drums and columns, see Question 61 in the 2012 AFPM Q&A Answer Book.
Another option that was highlighted in a recent publication11 has a hybrid option that uses liquid from the atmospheric tower reflux to the preflash column. This article claims that energy efficiency of this arrangement is superior to both the preflash drum and preflash tower arrangements. I have no experience with this hybrid option, but the claim seems plausible.
We have not seen severe problems with foaming any of our three crude units; but if a crude slate that is dramatically different from the normal slate that is fed to one of the units, we have to monitor closely for any signs of flooding or accelerated fouling.
The bottom line is that preflash drums and columns can add flexibility in running opportunity crudes but only to within the limits to which these components are designed.
Having a preflash drum or column increases energy efficiency with removal of the lighter components in the crude to reduce operating pressure/pressure drop requirement in the preheat exchanger train and to reduce furnace duty requirement. However, the reduction of the lighter components with the preflash system will also decreases the amount of flashed vapor in the atmospheric flash zone, which will need to be compensated by increasing the crude heater coil outlet temperature and/or crude tower bottom stripping steam flow. With light crudes, typically a 10 to 20% debottleneck can be achieved in the atmospheric tower, heater, and condenser.
With a preflash drum (as opposed to a preflash tower), the overhead is usually routed into the flash zone for fear of foamovers contaminating products, and the resulting upsets in downstream units. Cyclone separators (also known as vortex tubes/clusters) in the preflash drum are effective against foamovers, but one foamover that gets away from the cyclones causes so much mess, product loss, catalyst poisoning, and economic loss that most refiners shy away and route the overhead of flash drums into the flash zone. When this happens, there is zero unloading of the heater and the tower.
The preflash tower (as distinct from the drum) enables the refiner to recover naphtha (and sometimes jet fuel) that completely bypass the main atmospheric tower. A well-designed preflash tower has a pressure drop measurement and other warning instrumentation that can see a foamover before it gets into the product. The preflash tower also provides a venue for discharging the desalter relief valve without causing tray damage. However, the drawback of a preflash tower is a reduced diesel yield in the atmospheric tower because the light ends help with the stripping of the crude. This effect is usually small but needs consideration. Additionally, with some of the naphtha removed upstream, it can drive the atmospheric tower into a water dew point limitation. This may constrain the amount of stripping steam that can be used and therefore the diesel recovery. (Note that the effect of the higher naphtha boiling point is higher, and reduction in off gases may counter the water dew point issue. You have to study it to be sure.)
Another advantage of using a preflash drum (or a preflash tower) is the removal of light paraffins (C5 minus) which can reduce downstream asphaltene precipitation and fouling.