Question 61: Extensive use of upstream H2S scavengers in crude oils can cause salt deposition in atmospheric tower overhead systems, as well as on atmospheric tower trays, particularly when trying to operate at lower naphtha endpoints. What adjustments in desalter operation are used to mitigate amine salt deposition?
DION (GE Water & Process Technologies)
H2S scavengers may cause salt deposition in atmospheric towers. Triazine, the most common scavenger, is made by reacting formaldehyde with an amine, such as MEA (monoethanolamine), and creates an MEA-based triazine; similarly with methylamine-based triazine. One of the byproducts from the reaction of triazine with the hydrogen sulfide is an organic amine. The organic amine, and any unreacted amine from the manufacture of triazine, can increase the amine loading in the overhead, move the salt point, and increase amine salt corrosion risk.
Additionally, the triazine itself can decompose. An MEA-based triazine may decompose to MEA in the crude unit furnace and increase the MEA loading in the overhead. The salt risk is from both a byproduct of triazine reacting with hydrogen sulfide and from the decomposition of triazine in the crude unit furnace. One method to minimize overhead salt issues is to inject an acid upstream of the desalter to achieve an acidic effluent brine pH. An acidic environment will protonate some alkyl amines, thus creating an ionic compound like RNH3+ (protonated alkyl amine) instead of RNH2 (alkyl amine). The ionic species increases its partitioning to the water phase, thereby driving more organic amines into the effluent brine. The partitioning coefficient for those materials is dependent upon the R (alkyl group). In general, the more carbons on the amine, the less likely it will partition into the water phase.
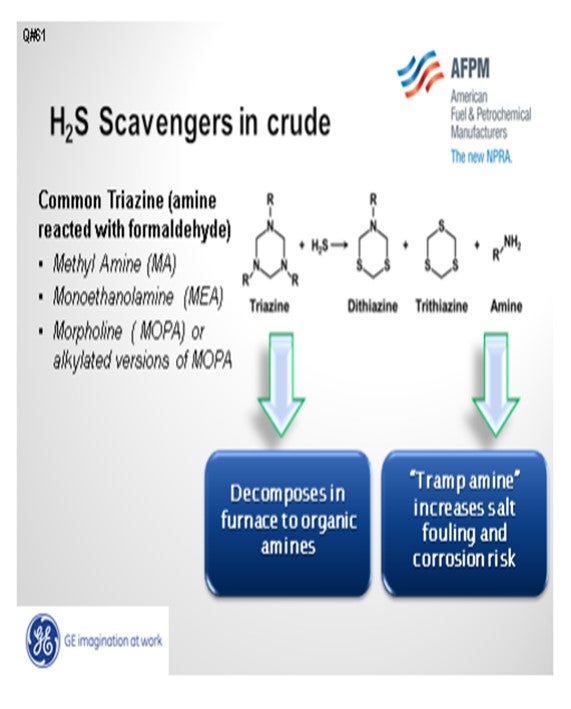
LEE (BP North America)
The primary H2S scavengers used in the industry, as Mike mentioned, are methyl triazine and ethanol triazine. Between the two triazines, we favor the use of methyl triazine due to the lower amine salt point temperatures for the salts that can be formed downstream with the free amine byproducts.
As far as desalter operation impacts from H2S scavenger use, methyl triazine H2S scavengers react to form monomethylamine byproducts. Literature and operating data support that a large portion (greater than 80%) of the amine byproduct will be solubilized into the desalter water if the water is between 6 pH and 8 pH. Lower amine partition percentages will be seen at the higher pH range. The amine partitioning can be improved by lowering pH or even acidifying, as Mike mentioned, but we have not done any of those practices ourselves within BP. As far as dithiazine byproducts, the ethanol dithiazine is reported to be water-soluble, and the methyl dithiazine is reported to be oil-soluble. We do not have any independent quantifiable data to elaborate on these literature reports. High water solubility of the byproducts will support maximizing desalter washwater usage in general.
Reducing the chloride content of the desalter crude will, in turn, suppress the amine salt point of the system. Desalter optimization parameters include maximizing washwater rate, making washwater quality enhancements (particularly pH and ammonia content), conducting mix valve pressure drop optimization, optimizing demulsifier use, optimizing grid voltage settings, and achieving the optimum, usually meaning maximum, operating temperature on the desalters.
VIJAY KRISHNAN (CITGO Petroleum Corporation)
Mike was talking about the use of acids. I would like to know how many people on the panel or in the audience use sulfuric acid to control or reduce pH.
PUI-NANG LIN (Flint Hills Resources, LP)
We have not used sulfuric acid for pH control in desalter application, but we have used it in other applications. We had a very bad experience because this inorganic acid is not buffered, so it is easy to over-inject and get results in a very low pH.
DION (GE Water & Process Technologies)
1,3,5 triazine-based products are commonly used commercially to treat a wide variety of petroleum products throughout the oil production and refining industry to reduce the volatility of hydrogen sulfide (H2S) in these products, making them safer to transport and store. The use of certain chemicals can provide health and safety benefits in shipping petroleum fluids but may also have side effects that are detrimental to refinery operations.
Triazine is a generic term for a small class of chemicals that contain a six-member ring with alternating nitrogen and carbon atoms. Differences between triazine compounds are derived by the atoms bonded to the nitrogen, but not included in the ring structure. Various amines are reacted with formaldehyde to form the triazine. Commercial triazines are comprised of formaldehyde and primary amines including, but not limited to:
• methyl amine (MA),
• monoethanolamine (MEA), and
• morpholine (MOPA) or alkylated versions of MOPA.
The triazine H2S complex that partitions to the oil phase or is carried over in the desalted crude BS&W can decompose in the crude unit furnace. The decomposition products typically contain an amine that adds to the partial pressure in the overhead and, depending on the amine, can form high salting amine chloride deposits.
Impact on Refinery Processes: High triazine levels in crude oil (greater than 1,000 ppm) have been found to negatively impact desalter performance in simulation studies. Triazine that remains in the oil phase will quantitatively decompose to amines at high temperatures in the crude furnace. Depending on the amine used to produce the triazine, a portion of the amine released in the reaction of H2S with triazine will remain in the oil phase and pass through the crude furnace and into the atmospheric tower. Contingent on the level of chlorides present in the desalted crude, amine chloride salts will form and can deposit in process equipment and cause fouling and corrosion. The amine chloride salts are insoluble and heavier than the hydrocarbon fractions and are corrosive to most metals at these temperatures. The type of amine used in the triazine determines where the salt deposition may occur based on the salt point at the specific operating conditions in a specific unit. MEA is known for forming a hydroscopic chloride salts above the gas oil section of the crude tower and is primarily a corrosion problem in the naphtha pump around section and overhead. Should MEA triazine or the sulfur containing reaction product survive the furnace and flash zone, additional concerns include increased sulfur content of the side cut products and fouling. Generally, MA chlorides will deposit in the overhead line or condensers and cause poor distribution, fouling and corrosion in the overhead system. These deposits and resulting corrosion and fouling may negatively impact the performance of the atmospheric tower and result in lost throughput or unplanned outages.
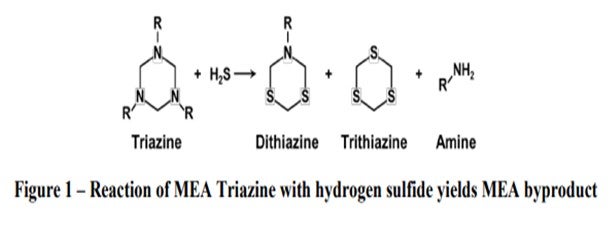
The reaction of triazine and H2S forms heavy sulfur compounds. The ratio of the dithiazine and trithiane that are formed depends on the relative ratio of reactants present. In most cases, dithiazine is the predominant species. Trithiane is more difficult to form, but it is more likely to form in the presence of excess H2S and/or low pH conditions. Both of these molecules can decompose in the crude furnace and distill into the refined product cuts. Dithiazine is hydrocarbon soluble and most remains in the oil phase. It distills at ~300°C (572°F) and may distill into middle distillate cuts. Some has been found to decompose to form CS2 (carbon disulfide) and free amine. Trithiane is generally insoluble in water and hydrocarbon. These solids that are dispersed in oil can sublime at >250°C (482°F).
1. Effects on Wastewater Treatment Plant (WWTP): All of the amines from triazine and reaction products will eventually flow to the WWTP. The amount of nitrogen will be the same regardless of amine since the stoichiometry of the triazine reaction is dependent on the number of Formaldehyde molecules that are consumed and not the molecular weight of the amine. These amines are readily consumed in the wastewater plant but may result in sudden microorganism growth and reproduction, followed by depletion of the oxygen supply. If the oxygen supply cannot be replenished, the microorganisms die from lack of oxygen and must be repopulated. The impact to the WWTP can be minimized by either limiting the blend ratio of triazine-treated crude oil or inoculating the WWTP with Nitrification organisms.
2. Carbon Disulfide: Field Experience demonstrates a 10-time increase in CS2 content in naphtha produced from triazine-treated crude. This is expected from any triazine since the CS2 is formed when the dithiazine cleaves, as shown below
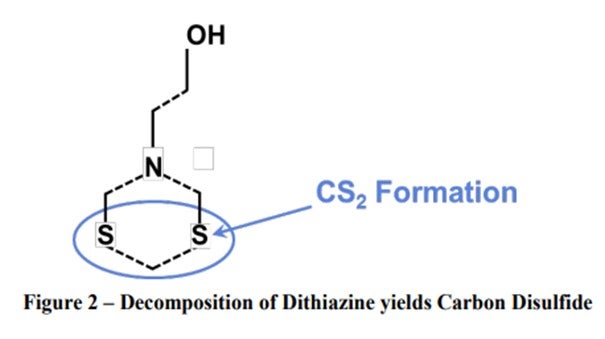
Small amounts of carbon disulfide and dimethyl sulfides may be formed as a result of thermal decomposition or reactions with other chemical species or the reaction product of MEA triazine and H2S. This does not create a problem for most refiners but could be a problem in petrochemical plant reactions because it is a catalyst poison. There are very few refineries in the world that send naphtha directly to petrochemical processes and may be affected.
The impacts of triazine-treated crude can be mitigated in several ways. The crude buyer must request information on treatment levels if they suspect that crude oil cargoes have been treated for H2S. Once this information is obtained, the crude blend rate can be controlled to limit the amine content in the crude.
Alternately, an acid can be added to the crude and/or desalter washwater to maintain an acidic effluent brine pH. The reduced pH protonates amines and creates an ionic compound that is more soluble in the bulk water phase, thereby extracting amines from the crude into the effluent brine. The types of amines and extraction efficiency will be dependent on the type of amine involved. In general, the more carbons there are on the amine molecule, the less efficient the extraction. For example, ammonia will be easier to extract than MEA and MEA easier to extract than DMEA.
If possible, the best solution is removing the potential processing hazard completely. The refiner may request that the crude producer or broker use a non-amine based H2S scavenger such as a select GE Water & Process Technologies’ non-amine ProSweet* product to completely eliminate the potential impacts of H2S scavenger treatments across the entire refinery.
RANDY RECHTIEN (Baker Hughes)
When amine-based H2S scavengers are present in crude oils, desalter operating conditions affect the extent to which amines partition to the desalted crude. The key operating parameter is desalter water pH. At higher pHs, higher levels of amines partition to the crude and increase the risk for amine-HCl salt formation in the atmospheric tower and overhead system. The application of desalter acidification additives, such as Baker Hughes EXCALIBUR™ program, can successfully decrease amine levels in desalted crude. In conjunction with an EXCALIBUR™ program, the potential for amine/HCl salt formation can be determined using Baker Hughes TOPGUARD™ Corrosion Risk Monitor.
BASHAM (Marathon Petroleum Corporation)
Control of the desalter water pH is key. Amines will partition between oil and water depending on pH. Amines will go with the water at lower pHs, and conversely stay with the oil at higher pHs. This can lead to cycling up of amines in the system.
DENNIS HAYNES (Nalco Energy Services)
Elevation of washwater flow rates, injection strategies (moving towards a more dominantly primary versus secondary injection where possible), not using desalter washwater with an elevated amine loading, and pH control of desalter washwater are all strategies that will assist to certain degrees.
SAM LORDO (Nalco Energy Services)
Acidification of the desalter washwater, typically using organic acids, can be done and achieve some success in extracting amines from the crude oil. This does have its downside, though, and has to be monitored closely or one could end up with additional acid loading on the overhead circuit. This additional acid loading could result in additional neutralizers being used, which could then also raise the salting temperature of the chloride salts. A thorough review of the system to be treated should be conducted so that the proper acid is chosen and the side effects are minimized.