Question 60: What has been done to address corrosion problems either inside your desalter or in the brine handling circuit?
SHENKLE (Flint Hills Resources, Ltd.)
Historically, we have not had corrosion problems in our brine circuit or desalters, so we do not do anything specific to address this question.
HODGES (Athlon Solutions)
Some refiners have used acids in the desalter washwater as a means to assist in emulsion resolution. We always look for other solutions as this practice may present other challenges including operator exposure, corrosion to the desalter internals/water circuit, and additional acid load to the atmospheric tower. When required, using weaker non-mineral acids usually makes the most sense and does not contribute as greatly to overhead corrosion.
Corrosion in the effluent brine/makeup water heat exchanger is overlooked in most every desalting system. We recommend the following Best Practices: First of all, many operators get tired of messing with this exchanger, so they bypass it: bad idea. You must run your effluent brine and makeup heat exchanger. Bypassing the system because it is difficult to keep online is not a good operating choice. Secondly, we have not seen any advantage with high metallurgy exchangers here. Carbon steel is cheap and allows you to keep a spare in the warehouse for replacement when it leaks. Lastly, have your specialty chemical supplier run a periodic chloride balance to make sure you are not leaking. Leaks often go undetected and can significantly degrade the desalting efficiency if you are leaking across your brine water exchanger.
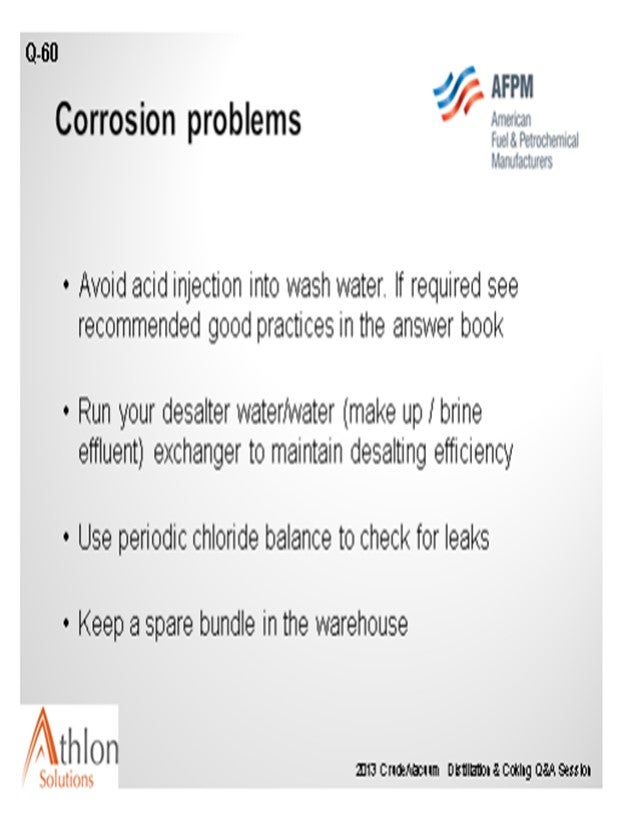
SLOLEY (CH2M Hill)
If you look over the crude unit and find an abandoned exchanger, it is almost certainly the water/water exchanger for recovering heat from the brine to the fresh desalted water. This exchanger has major corrosion problems. Keeping this in service without leaks often requires either Inconel or Hastelloy materials. I think the panel is giving two approaches here. Build it cheap and replace it often or build it really expensive and make it work. Either way, you are both trying to address the problem of leaks. They are both legitimate approaches, but they do involve some level of commitment of capital or attention of the operation.
SAM LORDO (Nalco Champion Energy Services)
The use of specially designed corrosion inhibitors can successfully mitigate and control desalter washwater, desalter brine, and desalter vessel corrosion due to low pH excursions, either from crude contaminates or acidification programs.
DENNIS HAYNES (Nalco Champion Energy Services)
In cases where the corrosion is due to low pH washwater and low pH effluent, filming corrosion inhibitors have been successful in reducing corrosion. In cases where the desalter washwater is neutral or basic yet the effluent becomes low pH after washing the crude, there are rare applications where caustic is used to increase the washwater pH so that the resultant brine effluent pH can be control to acceptable levels. In cases where the corrosion is due to oxygen contamination of washwater sources, lining the desalter has been attempted; yet, the optimal solution is to eliminate the source of oxygen.