Question 60: With an increasingly varied crude slate, how are you managing substantial variability in salt levels in desalted crude and overhead neutralizer rates? How can this impact the amount and location of amine salt and other deposition in the atmospheric tower and overhead system?
CLIFFORD (Motiva Enterprises LLC)
The salt loading in the overhead is set by the salt loading leaving the desalters. Two key factors are the salt content of the oil and the salt coming in with the entrained water. With increasing variability of the crude, it is important to focus on the performance of your desalters in order to manage the chloride levels in the crude charge-in before the crude is charged to the unit, rather than responding to it afterwards. There are sites where we try to manage incoming water and salt levels with pretreatment in tankage. Chemical vendors offer various products to do this. The performance of these treatment options is a function of settling time and available tankage. So, there are some limitations around their use. At some refineries, the water content of the crude is managed with BS&W testing and then pumping the bottoms of the tanks to another tank if we cannot manage to get below 2%.
The next point of control is around desalting: optimization of the desalters, mix valves, and washwater rates. As you increase the water, you may get more water breakthrough afterwards. And as you increase mix valve pressure, it may tighten the emulsion. However, there is an optimal point, which is a function of the properties of the crude and the hydraulic loading of your desalters. Chemical vendors also offer various additives to assist with demulsification to improve desalter performance.

Once the salt loading has gone past the desalters and into the unit, you obviously want to focus on maintaining proper pH and monitoring for your chloride content. There are online analyzers available to help with this monitoring.
You also want to monitor your neutralizer addition rates. Tramp amines and other chemicals may be present in your overhead system, which can affect your neutralizer usage. The varying crude slate will also change your dew point as you shift. If you have increased flow rates, it may affect your waterwash performance and your required water to get to 25% liquid water.
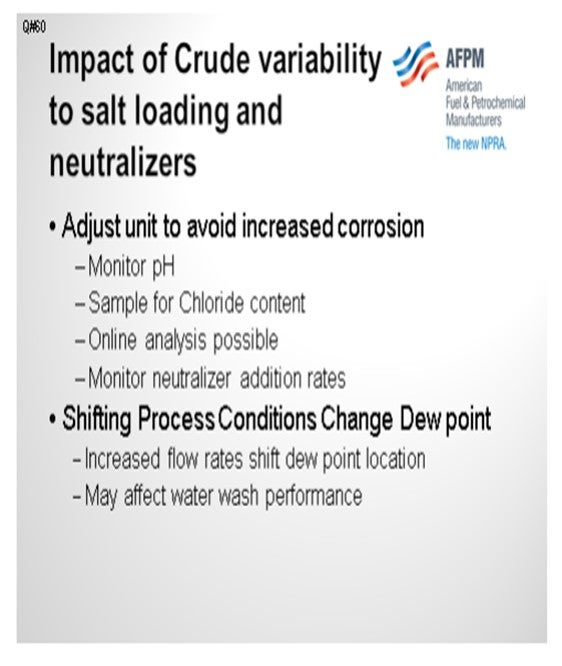
The impact of the increasing neutralizer rates: Many units will recycle overhead waterwash and use it as desalter water, so the neutralizers are being recycled at the end of the desalters. There is a partitioning effect that is a function of the quality of the water and the quality of the oils. Those neutralizers will then carry through the units and essentially function as a tramp amine in the unit, which will have an effect on the salt point versus your water dew point. So, you will see formation of amine hydrochloride salts upstream of water injection, which will then manifest as fouling. Differential pressure will increase, and you can even see corrosion.
The chemical vendors all offer various ionic equilibrium monitoring. With an appropriate amount of sampling, combined with pressure and temperature monitoring, you can model the overhead system and predict salt points and water dew points. With this information, you can vary the neutralizers you are using, as well as their composition, in an attempt to affect the location where that salt point is occurring. One caution is that the ammonium chloride salt point, from the breakdown of nitrogen compounds in the crude, may still be a concern, especially if you have ammonia coming into the desalter via externally supplied waters. Ammonium chloride may actually drive the location of your salt point concerns.
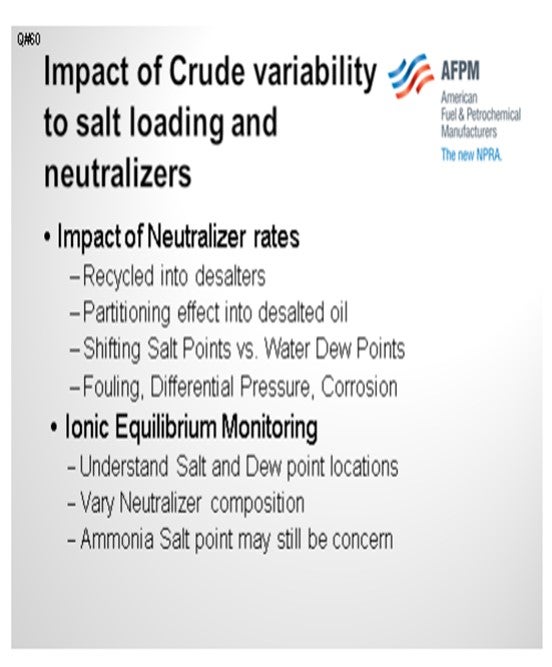
DION (GE Water & Process Technologies)
The overhead salt point is dependent upon the chloride content. In the bottom right-hand corner of the slide, you see a red line on the corrosion rate graph. That red line represents the salt point and will slide to the left or right depending upon many factors, such as the partial pressures of amines and acid species in the overhead. The salt point will continually shift back and forth with varying concentrations of acids and bases in the overhead, including chloride from hydrochloric acid; in general, the greater the volatility of the overhead chlorides, the greater the volatility of the salt point. In such a situation, it is extremely important to minimize high salting tramp amines. Mapping the amines by measuring type and quantity in overhead waters, desalter washwater, effluent brine, and tank water drains can assist in determining the source of high salting amines and stimulate remediation strategies. If warranted, injecting caustic into the desalted crude can reduce the impact of high chlorides in the overhead.
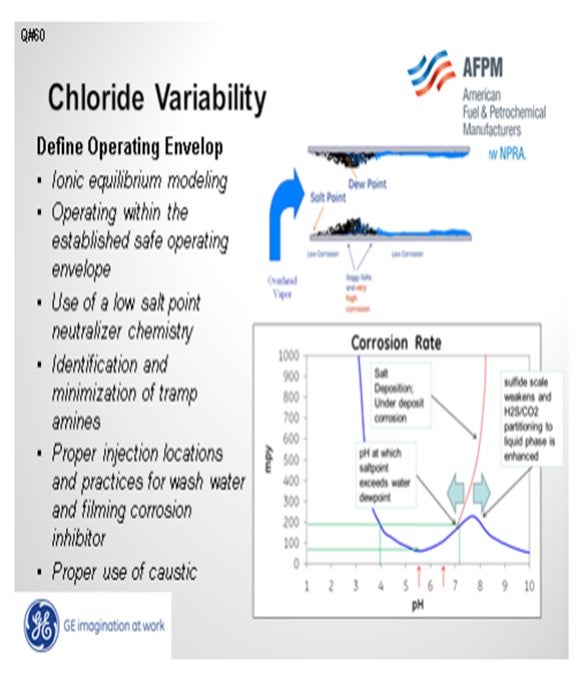
Most important is running the ionic equilibrium model frequently to establish a safe operating envelope. Operating within certain parameters can ensure that the salt point is not upstream of the water dew point. The slide below is an example of documenting the salt and dew point using GE’s LoSalt* ionic equilibrium model. The dew point and salt point were plotted daily. Severe corrosion occurred when the salt point exceeded the dew point. A safe operating envelope was established from the model. Tramp amines were minimized to extend the safe operating environment. Operating parameters, including stripping steam, were controlled to ensure that the salt point would always be below the water dew point.
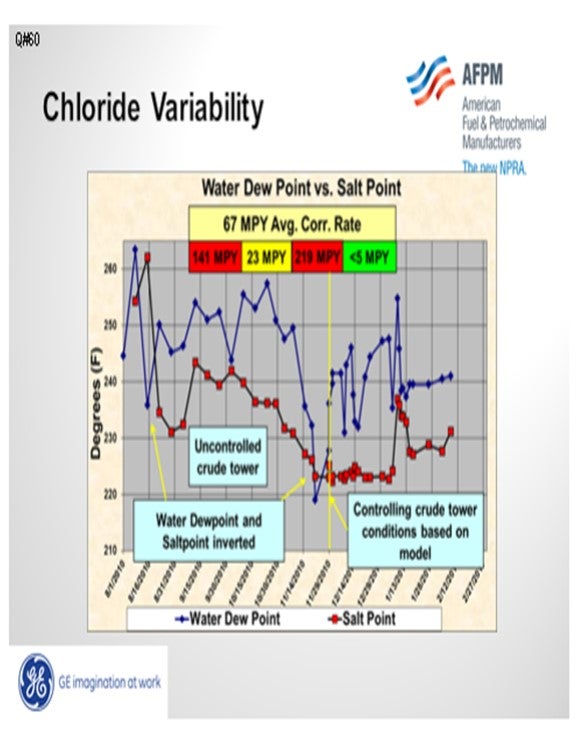
VILAS LONAKADI (Foster Wheeler USA Corporation)
As an alternate to desalters for BS&W removal, has anyone used the gun barrel technology in refineries processing heavy crudes?
DION (GE Water & Process Technologies)
Gun barrel vessels are usually a separation device for the oil field. I have not seen gun barrels in refineries.
SAM LORDO (Nalco Energy Services)
Although it is ideal to have the salt point below the water dew point, in most cases, as long as you are within about 25°F, you are probably okay. I have done a lot of these over the last 30 years. I would say that most of the refiners run with the salt point above the water dew point and still do not have corrosion issues.
HAROLD EGGERT (Champion Technologies) Another commercial: This afternoon there is going to be a P&P on Best Practices for what makes a good waterwash and what makes a bad waterwash. I encourage people to attend that P&P also.
CORY NOYES (Marathon Petroleum Company)
What is the panel’s experience with the online chloride analyzers and adjusting caustic rates based on online chloride sampling? I would like to ask the same question for neutralizers as well.
CLIFFORD (Motiva Enterprises LLC)
I do not have any experience with automation based on online chloride analyzers.
DION (GE Water & Process Technologies)
We are beta testing an automated feed system to control the neutralizer based on the overhead pH. That is an easy measurement, and there is hardly any interference with it. Automating chloride measurement is more complex and must account for interferences from bisulfides. It is still important to understand the operating boundaries to avoid excessive neutralizer feed rates which may move the salt point too far upstream. Automation should not replace defining the boundaries of a safe operating environment and routine monitoring.
SAM LORDO (Nalco Energy Services)
To address the question about automation, Nalco has been field-trialing for over two and a half years. A complete package is now commercially available and being deployed globally. There was an article in today’s AFPM newspaper. If you need to find out more information, please see me. It does work. I fully agree that you cannot just turn it over to the machines. You have to know what is going on. Otherwise, you will have issues.
CLIFFORD (Motiva Enterprises LLC)
Salt loading to the unit is set by two factors, salt content of the oil, and salt coming in with entrained water from tankage. The best option to manage corrosion in the Atmospheric tower overhead is to optimize salt removal prior to the atmospheric tower.
Some sites attempt to control salt via pretreatment in tankage. Chemical vendors offer various products to address this. However this is a function of settling time and available tankage and infrastructure to hold the crude and the water/sediment from the dewatering process. At a minimum Convent requires that a spot sample of the crude be caught and analyzed for BS&W. If the BS&W results are above 2%, then the bottoms of the tank are pumped to another tank until the results are less than 2%.
The next point of control for chloride variability is around desalting. Optimization of desalter washwater rates and mix valve differential pressure is essential. Insufficient water will result in poor contacting with the salts in the oil phase and high salt content in desalted crude. Excess water will increase the loading on the desalter and result in poor dehydration and both high water and salt content leaving the desalter. High water rates may also increase loading on brine treatment units and result in inefficiencies depending on washwater temperature. Insufficient mix valve differential pressure will lead to poor mixing and contacting of the water phase with salts in the oil phase. Excessive mix valve differential pressure will result in a tight emulsion which may not be resolved in the desalter. Various chemical vendors offer products which can help with demulsification. Chemicals are also available which can help with the impact of solids coming in with the feed.
The final option for prevention of salt loading to the atmospheric tower is via caustic injection. The caustic will convert calcium and magnesium chlorides into hydroxides and sodium chloride which has a lower rate of hydrolysis at conditions in typical crude unit furnaces. However, this will increase the sodium loading to downstream units.
To manage overhead corrosion, the pH of the overhead accumulator water streams is analyzed via an online pH analyzer. Samples for pH and chlorides are periodically caught to monitor for changes. Neutralizer addition rates are adjusted to maintain pH within the control range. If the chlorides exceed a predetermined limit, additional troubleshooting is undertaken as it is a sign that excessive neutralizer is being used.
High neutralizer rates can have an adverse impact to unit performance. Crude overhead waters are reused as desalter washwater. Once used as desalter washwater, some of the neutralizer may partition into the oil phase. This along with tramp amines from upstream of the crude units can have an effect on salt formation and corrosion within the crude unit, upstream of the water dew point. Essentially, as amine injection rates increase along with chloride content, the salt point in the atmospheric tower overhead system will get warmer. This may move salt points outside of areas which are designed to handle it. This can manifest itself as fouling, increasing differential pressure across sections of the atmospheric tower overhead or in the column itself or as corrosion depending on the type of salt formed, how close to water dew point it is formed, and other such as the type of neutralizer employed.
It is possible that with an appropriate amount of sampling and data collection, ionic equilibrium models can be built to predict conditions which would allow salt formation, and many chemical vendors offer such services and neutralizer packages tailored to the process conditions of each unit.
Another concern with changing crude slates will be varying compositions, reflux ratios, and cut points in the top section and overhead of the crude tower will alter the water dew point, salt point, and the amount of required washwater. This will impact the amount of water required to maintain sufficient waterwashing or shift the location of water dew point and is especially true if temperatures are lowered in order to maintain previous yield structure of product quality.
DION (GE Water & Process Technologies)
Overhead pH control is, perhaps, the most important aspect of overhead corrosion control and is the single most significant driver of the aqueous corrosion process. The pH is directly related to the corrosivity and provides a direct measure of the [H+] ion concentrations. It is the acidic protons, [H+], that drive corrosion. Furthermore, pH is an indirect indication of salt fouling potential at fixed chloride loading. Chlorides themselves, on the other hand, are only an indirect indicator of corrosion as they do not take into account the neutralization state of all acids present in the system. In general, the measured pH depends upon all the acids and bases present in the system, and it dictates the overall availability of free acidic protons. The balance of total acids and bases is directly related to corrosion rates and salt fouling.
To address aqueous corrosion, neutralizers are injected to elevate the pH and minimize acid attack of the system’s metal surfaces at the initial condensation point (ICP) of water in the overhead. This acid neutralization reaction produces a salt that will precipitate from the vapor phase at a given temperature, depending on the base (amine) involved in the reaction. This neutralizer “salt point,” or temperature at which the first neutralization salts begin to precipitate from the vapor phase, will also affect the fouling and corrosion potential in the overhead system.
Salt points are directly driven by the product of chloride and amine partial pressures and the proper selection of the neutralizer is critical to maintaining overhead system integrity. However, neutralizing amines that are intentionally added to control overhead pH conditions are not the only amine species that play a role in overhead salt formation. Depending on the relative concentrations, the presence of “tramp amines” may play a larger role in overhead salt formation than the injected neutralizer amines. For the purpose of this discussion, tramp amines are defined as any amines, other than the appropriate neutralizer being used, found cycling in the system. Tramp amines that are entering and recycling in the system will strongly affect overhead pH and typically have very high salt points. These amines can make it virtually impossible to either keep salt points below the ICP or to drop the pH to the targeted control range of 5.5 to 6.5.
As the number of hydrolysable salts exiting the desalter increases, the partial pressures of chloride ions present in the overhead increases. This substantially increases the acidic corrosion potential, which is subsequently addressed through increased neutralizer dosage with a resulting higher salt point temperature. Additionally, any tramp amines present in the desalted crude increase the salting potential in the overhead and can drive the salt point temperature even higher. These higher salt points drive the location of neutralizer salt precipitation further and further upstream into hotter areas of the overhead system, possibly even into the tower itself.
To prevent this undesirable condition in the overhead system, there are several approaches that can be employed to keep the system in control. These approaches include:
1. Use of ionic modeling to establish tower operating envelope,
2. Operating the tower within the established safe operating envelope,
3. Use of a low salt point neutralizer chemistry,
4. Identification and minimization of tramp amines,
5. Proper injection locations and practices for washwater and filming corrosion inhibitor, and
6. Proper use of caustic in the desalted crude.
Understanding the dynamics of the overhead system is the first step in properly diagnosing the corrosion and fouling potential of a given unit. The frequent use of a robust and rapid ionic modeling tool will allow for the calculation of the salt point temperature, ICP temperature, and the subsequent prediction of salt point location in the system. GE has equipped field representatives with the GE LoSALT* Ionic Model and trained them to work with the asset operator to develop an operating envelope that will aid the refiner in remaining within safe operating ranges with respect to salting potential across the desalter effluent salt variability range. Where GE has implemented this control and mitigation approach, asset operators adjust tower operating conditions (e.g., overhead outlet temperatures, tower steam injection rates, etc.) to manipulate and control the salt point location in the overhead system.
Once safe operating boundaries are established, the overhead neutralizer injection rate can be automatically controlled with a pH sensor in the overhead accumulator boot. It is important to note that automation without appropriate boundary definition may lead to under deposit corrosion failure from amine salt deposition. For this reason, frequent use of an ionic equilibrium model is recommended, preferentially onsite for quick response to unforeseen changes in operations.
BASHAM (Marathon Petroleum Corporation)
Assuming no change in neutralizer addition, the swing in crude overhead chlorides is most always directly related to desalter performance. However, a refiner may not be seeing widely distributed desalted crude salt numbers even when the crude overhead chloride concentrations are swinging. It is important to ensure a representative sample is obtained.
It has been published in literature, and can be verified by calculations, that a system that has 1 ptb (pound per thousand barrels) of salt in the desalted crude will result in an overhead chloride concentration of approximately 25 ppm. This correlation incorporates several assumptions, namely the salt cation distribution, the efficacy of the NaOH (sodium hydroxide) neutralization, and consistent water influx to the tower. However, it does provide an order of magnitude estimate.
RANDY RECHTIEN (Baker Hughes)
Variations in crude oil quality certainly place more burden on desalter operation. Higher salt content in desalted crude requires more diligent monitoring of both caustic injection rates (where applicable) and overhead neutralizer rates to address correspondingly higher overhead HCl (hydrochloric acid) levels. The effects of higher overhead HCl levels on amine-HCl salt formation can be successfully determined with the Baker Hughes TOPGUARD™ Corrosion Risk Monitor. The TOPGUARD™ monitor is an extension of the Baker Hughes Ionic Model technique, which provides for ongoing monitoring in response to variations in unit operations.
DENNIS HAYNES (Nalco Energy Services)
Optimization of desalter operations and maximization of washwater rates and injection strategies will assist in minimizing swings in chlorides, and automated analysis of overhead aqueous condensate to improve response to swings is important. Elevation of chlorides and/or amines in an overhead system will move salt points to higher temperature areas, so systems with limitations on waterwash should track salt points so operational adjustment can be made to control salt points when required (such as tower top temperatures, pressures, steam rates, etc.).
SAM LORDO (Nalco Energy Services)
Optimization of desalter operation and use of caustic is the best-in-class management of chlorides in the crude column overhead circuit and tower top sections. The frequency of monitoring and level of detail water analysis is also important; the more frequent, the better, Nalco’s new continuous analyzer for crude overhead systems measures pH continuously and chlorides every 30 to 60 minutes. This data then can be used to close-loop control the pH control and caustic injection, respectively. Going to this level of control minimizes the variability impacts of changing and challenging crudes. This information can also be used in conjunction with data management tools and overhead simulations to run dew points and salting deposition temperatures at a near continuous frequency.