Question 59: How does improper control of desalter washwater and brine affect crude unit overhead pH?
HODGES (Athlon Solutions)
Guidelines around the addition of desalter washwater were historically 3 to 5% on volume based on crude charge. Some years back, with a shift towards heavy Venezuelan and unconventional crudes, the trend pushed up towards the 7 to 10% range or higher. As an ancillary note, this has caused some more refiners to adopt a brine recycle strategy, as we just discussed. Common sources of the desalter washwater are stripped sour water, vacuum hot well, atmospheric, overhead accumulated water, and surface water. Ammonia levels should be monitored. Guidelines are unique and specific to the design, crude slate, and operational philosophy of the specific desalter. There is no one rule that fits all. Your process chemical suppliers should be able to design and carryout proper surveillance, testing, and ionic simulation to assist in bracketing the operational envelope for ammonia content in the washwater.
In general, ammonia guidelines are less than 50 ppm to avoid an emulsification impact on the desalter, or less than 20 ppm to avoid crude tower salting, fouling, and corrosion. Caustic can be added to the sour water stripper to improve ammonia stripping. Hot well water contains free and heavily emulsified oil. When setting your washwater rate, you should take into account the oil content of the hot well water that is coming into your desalter with makeup water; otherwise, it would be artificially low.
In newer, deep-cut vacuum units, we have noted a greater content of emulsifiers in the hot well water that must be addressed through either operational or chemical management techniques. Lastly, your process chemical supplier should run a full battery of lab testing on the washwater to check for the presence of known bad actor species such as tramp amines and others. These results should then be fed back into your overall washwater management and crude tower corrosion management practices.
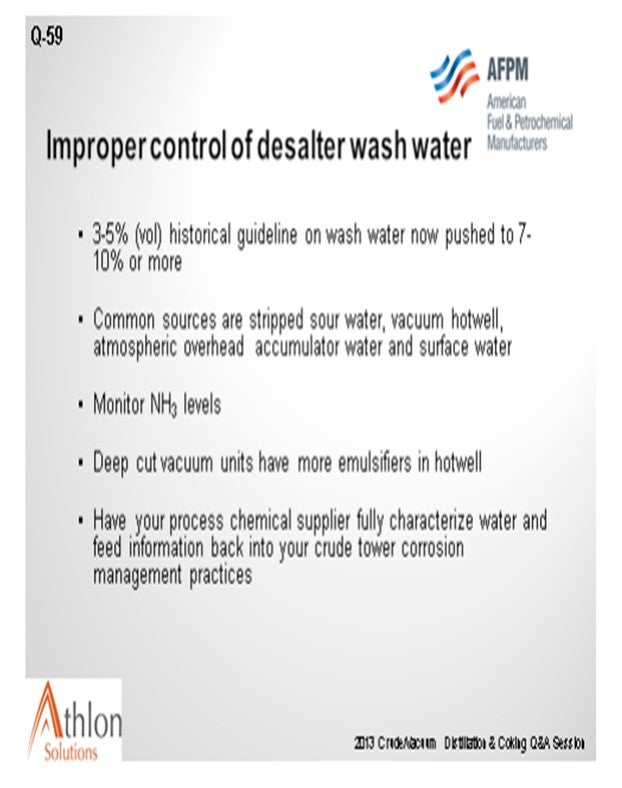
PRIBNOW (CITGO Petroleum Corporation)
Improper control of washwater and brine will lead to emulsions, which will result in carryover and poor desalting. As I mentioned, when we start having carryover and upsets, our crude tower is going to become upset, which could result in the tower pressuring up.
Ways to Properly Control Washwater: Stephen mentioned many of them including 1) lacking enough fresh washwater, 2) excessive mixing of the water and oil at the mix valve, and 3) injecting the washwater further up in the pre-heat. If too much water is injected upstream, it will count as mixing. Tight emulsions may be created that are hard to break.
Vacuum Condensate: I think you called it ‘hot well water’. We all have our different lingo. If there is an emulsion or those bad actor components exist, there will be problems in our desalter, high solids in the washwater, and excessively high washwater pH. Our sulfur plants have sent the desalter high pH sour water. We will see that high pH in the desalter, which results in formation of a stable emulsion. Monitoring your incoming pH is important.
Finally, when we mud-wash, we do not take fresh water away from the water being injected for desalting. Every time fresh washwater is taken away, desalting stops. The level of chlorides will then increase going into the crude tower.
We just talked about brine recycle. Do not recirculate solids or emulsifying agents like oil. We have found that it will just create havoc with both desalters.
Poor Salt Removal: We start seeing a decrease in our overhead pH due to the concentration of the chlorides. If we see high pH in our desalter, our experience is that partitioning of the amines and ammonias into the oil phase enters our crude tower and then creates a higher or elevated overhead pH. Also, we have experienced salting of our top trays in the crude tower.
BILL CATES (Hunt Refining Company)
I will caution you about the use of the water off the sour water stripper, if you are putting in caustic. You have to watch to make sure that the operators are not getting overzealous with the caustic condition; because once you get sodium content in that water up to about 300 to 350 ppm, it will start to make sodium naphthenate. For folks that do not know, that is a very good tight agent for making the emulsion.
SHENKLE (Flint Hills Resources, Ltd.)
One data point from us with tight oil processing: We have seen a decrease in neutralizer usage in crude overheads. We do have units with brine acidification. We use vendor-supplied, inhibited acid for desalting and amine partitioning to the water.
VILAS LONAKADI (Foster Wheeler USA Corporation)
Steve, you mentioned the sources of the washwater, one of which was the surface water. Has anyone seen that the desired oxygen in this water has led to corrosion, or has anything been done to de-aerate that water being used, apart from the stripped water?
HODGES (Athlon Solutions)
That is a great question, and the answer is yes. The oxygen in surface water can and does contribute to problems in your atmospheric tower. For instance, crude units that run cold at the top generally have corrosion in their naphtha pumparound circuit which requires the use of a filming inhibitor in the pumparound return. If you are running sour crude and then add oxygen from your surface sourced washwater, you will make elemental sulfur in your tower. Further, if you have the presence of iron sulfide in your atmospheric tower, you will form a rubbery deposit in your tower. This has been happening as long as I have been in the industry since the 1980s. Think of it like a three-legged stool with the legs being elemental sulfur, iron sulfide, and filmer. If you take any one of those three away, you will not have a problem. If at all possible, try to avoid oxygenated water because of the problems that it can incur.
CHRISTINE SHOROKEY (Monroe Energy, LLC)
What is the panel’s experience with water injection points? If you are injecting 7 to 10% waterwash, is a portion of that in your pre-heat train?
HODGES (Athlon Solutions)
Good question. Our opinion and Best Practice are a bit contrarian. We like putting all of it ahead of the cold pre-heat train into the crude charge pump. We have case history after case history of the positive effects on this. We see tremendous benefits not only in elevated levels of desalting efficiency from a salt removal perspective, but also solids removal. Of course, you must have a demulsifier that is capable of handling the emulsion that this technique will create.
SLOLEY (CH2M Hill)
On the question of injection points, I am not aware of anyone using any special quills when injecting the water into the crude. It is really just an elbow connection. At the moment, the industry practice on water injection locations varies. It’s close to even numbers of plants putting all the water downstream of the cold train versus putting some of the water into the crude upstream of the cold train. When injected upstream of the cold train, water injection is typically downstream of the crude charge pump. Injection upstream of the crude charge pump is a minority position in the industry as a whole. Whether it is attractive or not is a different question. It is just an observation of what people do. There are a couple of issues with injecting the water early in the process. Of course, it increases the volume and the pressure drop to the unit. A lot of people have pushed for higher capacity. They find it the hydraulic constraints, so they want to avoid that.
The next issue is that depending on the water sources, sulfate, and carbonate content of the water, the technical risk there is really that the sulfates and carbonates become less soluble at higher temperatures. So there have been people who had deposits in their cold train equipment because of that. It is fairly easy to do the analysis on the water and make sure you do not have that problem, or do not do it if you do have carbonates. It is easy to avoid though.
RUSSELL “RUSTY” STRONG (Athlon Solutions)
Back to the question from the floor about oxygen, specifically about the corrosion issue: Back in 1988, Richard Horvath and Hans Schutt, with Shell Oil, presented a paper on one of their refineries where they identified the firewater (oxygen saturated) being used at the desalter was directly the cause of an ammonium bisulfite corrosion in the overhead line of their crude tower. What they found, demonstrated in the lab, and confirmed in the field was that the SO2 (sulfur dioxide) half-reacted with ammonia and formed a bisulfite salt that was actually quite corrosive in the overhead. Evidence is clear that it does happen, but not at every refinery.
PAUL FEARNSIDE (Nalco Champion Energy Services)
On the oxygenated water, do not assume that if you are using stripped sour water or good quality vacuum condensate water that it is oxygen-free. I had a number of cases where the seals were worn across the actual desalter water pump, or they had failed. The makeup water coming to the pump had less than 50 ppb oxygen. Leaving that pump, the water had as high as 2 ppm oxygen. The only way to catch that is to test for oxygen on your crude overhead water analysis. Do not just focus on chlorides. There are other acidic species; namely, SOx (sulfur oxide). So, to catch them, we monitored and analyzed for increased SOx and then went back and found that the pump seals had actually been failing.
VILAS LONAKADI (Foster Wheeler USA Corporation)
Is the corrosion deeply observed only in the crude tower overhead, in the desalter, and/or elsewhere because of this desired oxygen?
HODGES (Athlon Solutions)
Question 60 is about corrosion in the oxygenated water. I think our observation has been that generally, the negative impact of oxygen is limited to the crude tower and crude tower overhead. There are many other factors to consider where you may have, in fact, internal corrosion at the desalter and the brine water circuit. But in my observation, that has not generally been directly traced back to the use of oxygenated water.
GLENN SCATTERGOOD (Nalco Champion Energy Services)
High pH desalter washwater is typically caused by ammonia in the stripped sour water. This ammonia will exit the desalter along with the BS&W in desalted crude. The ammonia will distill into the crude tower overhead, promoting ammonium chloride salt deposition and leading to NH4Cl and HCl corrosion in the overhead, top pumparound, and top tray section of the distillation tower. This is the same mechanism observed with amines coming in either with the washwater (due to amine recycle of internal amine containing slops) or crude oils treated with H2S scavengers that generate amines.
DENNIS HAYNES (Nalco Champion Energy Services)
Desalter washwater mixing with the crude determines the effluent water pH. If the effluent water pH is low and a portion of this carries over with the crude, any acidic components in the basic water (BW) with the oil will carry through to the distillation column and increase potential for corrosion. Low pH of either desalter washwater or effluent can elevate corrosion rates in the desalter vessel and associated piping, requiring the addition of a corrosion inhibitor. If the resultant effluent water pH is high, it may stabilize the emulsion in the desalter causing water carryover and/or oil carryunder. Proper effluent water pH control (implied as washwater pH control) is important for reliable and stable desalter operations.
PHILIP THORNTHWAITE (Nalco Champion Energy Services)
The correct volume of washwater is critical to good desalting, and the use of low volumes can impact significantly on desalting and dehydration efficiencies. Increased salt in crude levels will result in elevated levels hydrolysable chlorides; and while these can be controlled to a degree with caustic, elevated levels of chlorides in the overheads will lead to low pH excursions and increased levels of aqueous corrosion. Although these low pH conditions can be mitigated with increased neutralizer dosing, the subsequent threat of salt formation is increased.
The quality of the desalter washwater is another important consideration; and if SWS (sour water stripper) bottoms are used as the washwater source, it is critical to ensure that ammonia content is minimized as this can significantly increase the risk of salt fouling in the top sections of the main fractionator and overhead condensing section. The high pH of the SWS bottoms will promote the partitioning of the ammonia into the oil phase where it will be passed into the main fractionator. Based on the partial pressures of ammonia and chlorides, there may be an elevated risk of salt formation and deposition on the top trays of the main fractionator, top pumparound, overhead line, and condensers. The deposition of ammonium chloride salts can lead to pitting corrosion and, in the worst case, fouling of equipment that begins to impinge of optimum performance of the unit.
Another consequence of using ammoniacal water as desalter washwater is that the ammonia will end up in the condensed water and increase the sour water pH. With elevated levels of ammonia, the pH of the overhead sour water can often be in excess of pH 6.5; and since May, refiners still dose neutralizer to achieve a pH in the range of 5.5 to 6.5, it is not uncommon to find that neutralizer dosing rates have been significantly reduced or even turned off. In these instances, it has been found that corrosion rates in the overheads condensers can increase significantly, even though the sour water pH is elevated. This is because ammonia is a very poor dew point neutralizer since it will not partition into the water phase until the bulk of the water has already condensed. Therefore, in these instances, it is recommended to continue to dose the neutralizer at a sufficient rate to neutralize the amount of chlorides present.
In order to mitigate against high ammonia levels in the washwater and also tramp amines present in the crude, some refiners choose to use desalter acidification programs to aid the partitioning of the ammonia and/or amine into the desalter effluent brine. Sufficient acid is injected into the washwater to maintain a desalter effluent pH in the region of 5.5 – 6.0 in order to maximize the removal efficiencies. When using acidification strategies, the choice of acid is critical. The most appropriate acid should be used to minimize the carryover into the crude unit overheads. Acids, such as acetic and glycolic acid, can end up in the overhead resulting in difficulties in controlling the overhead pH. This problem arises because the combination of these weak acids and the neutralizer, which is a weak base, results in overhead sour water that is highly buffered. Due to this buffering effect, a disproportionate amount of neutralizer is needed to achieve the desired pH. In such circumstances, careful control of neutralizer dosing is vital to ensure that both the risks of aqueous corrosion and salt formation are minimized.