Question 57: What problems are associated with processing crude with high solids content? What steps can be taken to reduce or remove these solids from the crude?
HODGES (Athlon Solutions)
High solids crude processing presents some increasing challenges for refineries running conventional crudes, tight oil crudes, and heavy Canadian bitumens. As you can see in the graph, some of the heavy Canadian solids run as high as 300 ptb (pounds per 1000 barrels). I would like to point out that this is not traditional basic sediment (BS) which can contain other sediments, such as wax and asphaltenes, but rather solids measured by lab filtration. It is important that you collect the proper data. We recommend following the ASTM (American Society for Testing and Materials) guidelines very closely. For instance, some people will add hot water rinse to the test; but it does not call for that, so you will get skewed results. So, follow the ASTM guidelines to ensure good data and interpretability.
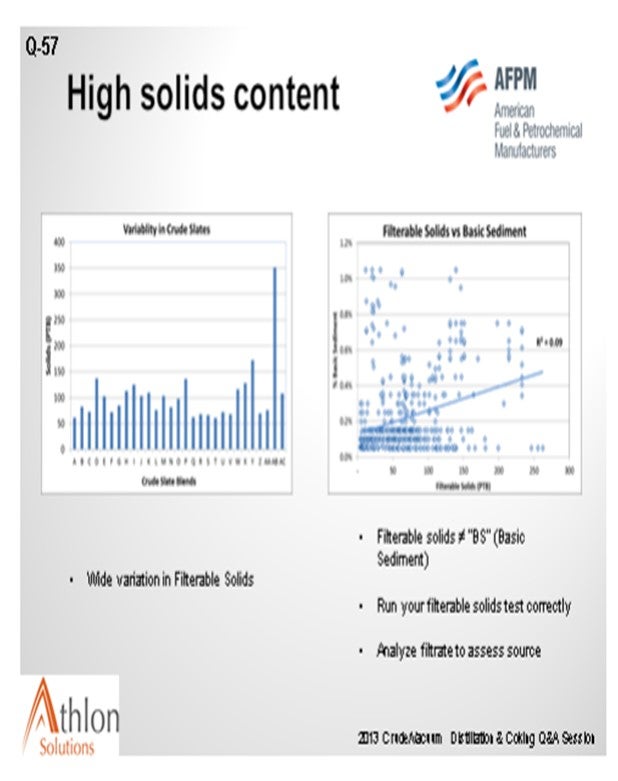
These solids function as surfactants and migrate to the interface in the desalter where they build up and must be purged with the oil or water. Good practices for managing higher solids in your desalter include checking with your process chemical supplier to provide a suitable wetting agent that functions to strip off the oil and allow the solids to drop out of the oil phase and into the water. Running a higher mix valve pressure drop and practicing good mud-wash management are key. Optimized mud-wash practices vary from system to system. In many cases, steam is the preferred mud-wash medium. If water is used, brine recycle is the preferred source over fresh water. Frequency of mud-wash ranges from once a day to continuous. You should verify the duration and frequency off mud-wash with your process chemical supplier. Lastly, if you are using water for mud-wash, you much use fresh water for your mud-wash pump seal flush. If you do not do this, you will have a maintenance nightmare of a continually leaking pump.
The main takeaway I want to put in everyone’s mind is to harvest your solids. It is very common to see refiners go to great lengths to remove these solids in the desalter, and then turn right around return them to the crude charge via API skimmings or other slop handling schemes. You must employ some actual harvesting mechanism, generally at the wastewater treatment plant, such as centrifuge or filter press, or you will never break the solids cycle and achieve good efficiencies and low treatment rates.
SLOLEY (CH2M Hill)
Refiners that have crude with high solids content have no truly desirable disposition for the solids. The least bad outcome is to keep your solids moving until you can shift them into a waste stream. The greatest operating problems occur when the solids stick to equipment or accumulate in the process equipment. Areas with the most solids accumulation include the crude tanks, desalters, and API separators. These are all normally considered undesirable even in the crude tanks. The solids build up and reduce crude inventory, which creates a waste that is expensive to handle.
Many plants have introduced mixing systems to prevent the solids accumulation in the crude tanks, but that shifts them downstream. Both jet mixing through the recirculation pumps and mechanical agitator systems have been used for this. Overall, tank mechanical mixing has shown better success because jet mixing and other recirculation systems often suffer from poor fluid flow patterns in the tanks, which then lets solids build up in areas. This is especially acute in large tanks. Note that the shipping and transportation system has installed lots of these systems which, again, shift the solids downstream to become our problem.
Solids problems in the crude unit include fouling at the pre-heat train and loss of desalter performance. Practical methods to keep the pre-heat train operating include using specialized exchanger designs, maintaining the fluid velocity, and adding chemical additives to keep the solids suspended in the oil. Significant success has been seen in exchanger design with the use of helical baffle exchangers. Otherwise, keeping fluid velocities above 5 to 7 feet per second (fps) also helps prevent fouling in conventional exchangers.
The desalter should be the major point of solids rejection in the refinery which will end up in the brine from the desalter. Wetting agents will improve shifting the solids into the water and are often critical. If you do not work on mud-wash systems, velocity is low enough in the desalter that the solids will build up there and mud will accumulate. That will reduce residence time and operating margins available and make desalter operation difficult. So, mud-wash systems use some type of recirculation with water and have shown great success in removing the desalter mud. Plants often use intermittent operation, but it should be scheduled. We recommended that it be done on every shift or at least every day.
In high solids crudes, the desalter may need to be set up to have multiple mud-washing zones that control the number of solids in the brine at any one point. They also stabilize the rag layers, making the desalter level control more difficult. If the solids are not removed in the desalter, the only remaining choice is to keep them moving. They will actually end up in the vacuum residue which will go to delayed coking, deasphalting or to asphalt product.
The composition of the solids may create problems with these product specifications. However, except in extreme cases, the solids content in the vacuum residue does not particularly add to the problems of vacuum residue handling that are not inherent in the fluid itself. Solids in these streams make the residues unattractive for fluid cracking or fixed-bed hydrocracker feed.
MARIA ELIZABETH MARSIGLIA (Petróleo Brasileiro S.A.)
You mentioned that the BS&W and filterable solids are measured differently. Of course, we agree with you. But regarding the filterable solids, to which protocol are you referring? Is it the ASTM 4807? In that case, I want to ask you a question regarding the membrane pore diameter, which is 0.45 microns. In Petrobras, using ASTM 4807, we have noticed that filterable solids sometimes do not follow up to metals measurements. We suspect that we may need to use a smaller pore, a solution that was mentioned yesterday by the Hydrotreating Q&A panelists who touched on the subject. So, I would like to know your views regarding the membrane pore size. Does that influence what you see in this solid's measurement?
HODGES (Athlon Solutions)
That is a great question. In my personal experience, I have seen some variability of membranes from manufacturer to manufacturer. So, I encourage you to investigate that through a series of tests to determine the one in which you have the most confidence. In terms of the pore size itself, perhaps ASTM could consider revisiting the specification. I am very data-driven; so, my belief is that in order to have great data, you must have consistency in your testing. In my mind, it is very important to rigidly follow the exact test procedure and make sure that your lab technicians have good process and hygiene in order to repeat those tests reliably. Over time, it has been my experience that process will give you some very good information. Again, just make sure that:
1) you do not take shortcuts in the tests;
2) you are very careful about hygiene on your filters;
3) you are drying and cooling them properly;
4) you are desiccating them properly; and
5) you are getting your proper tare weight in order to record your filterable solids.
XIOMARA PRICE (GE Water & Process Technologies)
My comment is about reducing pore size. Of course, you will get more solids; so, your ptb for solids will be higher. You have to be careful. If you are capturing many solids that have small particle sizes, those particle sizes may not be as significant, with respect to fouling. The reason is that when looking at dispersants from a treatment perspective, you are examining chemistries that are keeping particles small enough so they can continue moving through the system. So, it depends on what you are evaluating, as well as the significance and size of the material you are reviewing. You will get more solids when you use the smaller particle size filter, but you have to look at how significantly it is contributing to the problems downstream.
VICTOR TAILOR (Commonwealth Engineering & Construction)
Is anyone considering a two-stage desalter at the design stage instead of one desalter, and can this mitigate the solids? Sometimes refineries make a change from one-stage desalters to two-stage desalters that remove these high solids. That’s one criteria; there may be others.
SLOLEY (CH2M Hill)
If I understood the question correctly, you are asking if refiners have considered revamping from a one-stage to a two-stage desalter with the main objective of the change being the reduction of solids content in the desalted crude. I am sure refiners have done this. Experience shows that the major driving force in going from one desalting stage to two desalting stages is typically the corrosion issues rather than the solids content of the crude. Residence time tends to be very important for solids removal. Some refiners have added a second desalter to reduce solids content of the desalted crude. However, the added desalter is typically a parallel desalter. This gives an overall system with multiple parallel desalters, but desalting is still single stage. Two-stage desalting certainly reduces solids content, but there are other factors that are more important.
HODGES (Athlon Solutions)
I concur with Andrew. I think that in most systems that are well-designed and treated with proper chemistry and operating parameters, you will be able to remove most of the solids in one-stage desalting. Two-stage desalting or triple-stage desalting is typically employed for other reasons. I do not see a trend for justifying the addition of desalting vessels or stages based upon solids removal.
SAM LORDO (Nalco Champion Energy Services)
I have a comment on the types of filter paper. Everyone needs to be aware that you really have to look at the quality of the paper you are using. Some nylon papers are required by ASTM; however, there are a couple of upgrades. One of them is good to only about 80°C; another to about 160°C. The filter paper with the lower temperature limitation will result in lower values because the pores open up when the temperature increases; so, you have what appears to be less solids. In actuality, a lot of solids were not captured; rather, they passed through the filter paper. Another method is to use a filter paper with a smaller pore size, such as 0.2 and 0.1 micron. By using the smaller pore sizes, one can determine the solids distribution between crude with a higher degree of accuracy and, in some cases, identify or verify solids related issues that are not readily obvious from using the standard filter paper of 0.45 micron.
PRIBNOW (CITGO Petroleum Corporation)
Going back to the other question, during the last turnaround at CITGO Lemont, we actually did install a second desalter, which was gigantic compared to our other one. We did see some increase in the number of solids coming out, but that was not our primary justification for installing it.
UNIDENTIFIED SPEAKER (Shell Global Solutions U.S.)
I agree that you must be very careful with the way you analyze your solids in the sample, but I struggle with the nature of solids in crude. How do you show that you are getting a homogenous representative sample from a crude source in the first place?
HODGES (Athlon Solutions)
That is a great question and a challenge for many. Getting a representative sample on both sides of raw crude and desalter crude is not intuitively obvious. The Best Practice is to have a flow-through loop that is continuous, and which can then be purged properly to capture your sample. From time to time, I have observed operators catching samples. They will open up the sampling port and then throttle back on the valve and put the bottle under the tap. As soon as you change the wash rate profile coming out of the sample, you completely change the nature of distribution that you will get on the contaminants in that sample. So, in summary, it is very important to use a Best Practice of having flow-through continuous lines that you can safely sample with proper containment, which you can do without changing the velocity of the sample while catching it.
PAUL FEARNSIDE (Nalco Champion Energy Services)
Has anyone seen any foaming issues in the crude unit because of lack of solids removal?
PRIBNOW (CITGO Petroleum Corporation)
Yes.
VILAS LONAKADI (Foster Wheeler USA Corporation)
On one of the graphs that was shown, you had about a 300 ppm (parts per million) of solids for the extreme end. We are running the crude which has almost 800 ppm. Although we are now discussing problems that happen afterwards in the desalter, is there any technique being used to take out the solids before they reach the crude unit? I mean, maintaining velocities and desalter problems: Yes, we can tackle that later. But if the solids can be used, is there any way to remove the solids other than settling in the crude tanks?
HODGES (Athlon Solutions)
Settling in the tank, I think, is the fallback position. Tankage dewatering, as it is sometimes referred, can allow you to get a first pass on both the water and some of the solids. The challenge is whether you are set up to do that at your tank farm system. What do you do with the water that comes out? I am personally not familiar with any specific pre-treatment other than conditioning your crude as you are loading it into the tank and letting it settle for dewatering purposes. But yes, I pity you because that is quite a high solids content that you need to run; so good luck with that.
SHENKLE (Flint Hills Resources, Ltd.)
In response to the previous question, we had one particular instance of some foaming in the crude tower, but there was no definitive evidence of it being solids related. Typically, we do not have foaming issues in our crude towers.
CHRISTINE SHOROKEY (Monroe Energy, LLC)
I have seen a horizontal vessel that allows residence time with the Chevron-type filter in between the tank farm and upstream with the crude charge pumps to help remove the water in the solids. You capture the mess upstream.
GLENN SCATTERGOOD (Nalco Champion Energy Services)
High solids crude (greater than ptb) will affect the desalter performance which can then affect hot pre-heat exchanger fouling and overhead corrosion downstream of the desalter. To address the effect on the desalter, oil-coated solids will concentrate at the oil/water interface inside the desalter, reducing the residence time for either the oil or water phase. The heavier solids (less than 40 microns) will settle to the bottom of the desalter, potentially taking oil with them. This oil-coated solid will contribute oil to the wastewater treatment plant either continuously or during the desalter mud-wash. The severity of this issue can be decreased by using an effective and robust emulsion-breaking chemical with good “solids wetting” capability, along with increased mix valve delta P and a higher volume of washwater, all designed to disrupt the oil coating protecting the solid particle found in high solids crudes.
DENNIS HAYNES (Nalco Champion Energy Services)
Solids in crude can deposit in equipment and reduce heat transfer, set up at oil water interfaces, and stabilize emulsion. When solids continue downstream with reduced crude, they may cause problems with contamination, plugging, or poisoning of upgrading processes (depending on the composition of the solids). Solids may be removed, to a degree, via the desalting process by maximizing washwater; optimizing mix valve, time and term of mud-wash, and position of desalter interface; and/or, adding removal additives.
PHILIP THORNTHWAITE (Nalco Champion Energy Services)
The finely divided solids found in crude oils, commonly described as filterable solids, have long been known to contribute to the formation of stable emulsions at the oil and water interface. These oil-coated solids migrate to the interface where they accumulate, thus preventing the water droplets in the crude oil from coalescing into larger droplets and then stabilizing the emulsion band at the interface.
This emulsion, if left unresolved, can grow to the extent where it will begin to negatively affect effluent quality. Wastewater operations can also be impacted due to the higher loading of oil and oil-coated solids in the desalter effluent. Wide emulsion bands in the desalter can also result in reduced desalting and dehydration efficiencies, which can lead to more chlorides in crude tower overheads that will potentially form higher levels of hydrochloric acid (HCl) and result in increased corrosion rates. Furthermore, reduced dehydration in the desalted crude leads to significantly higher energy consumption.
Poor solids removal from the crude oil can also lead to higher fouling rates in hot pre-heat exchanger networks and crude unit furnaces leading to increased furnace fuel gas usage, and potentially reductions in crude charge. Further downstream, the solids can contribute to foaming in pre-flash vessels, accelerate fouling in the convection section of visbreaker and coker furnaces, and have negative impact on catalysts in residue FCC units.