Question 57: What are the desalter conditions that may require acidification? If needed, what types of acids do you use and what issues arise downstream?
BRADEN (NALCO Champion)
Under normal operations, having a consistent crude slate and a washwater pH between the 5 and 9, acid addition is not normally required, despite what gravity of crude the refinery is using. There are three situations for having a good conversation with your chemical vendor, if you think you need acid addition. One is removal of tramp amines. The second is metal removal; specifically, calcium or iron. Third is the use of high pH washwater. Typically for acidification, the washwater should be greater than a pH of 9. You may want to go a little lower than that, but that is a discussion you should have with your vendor.
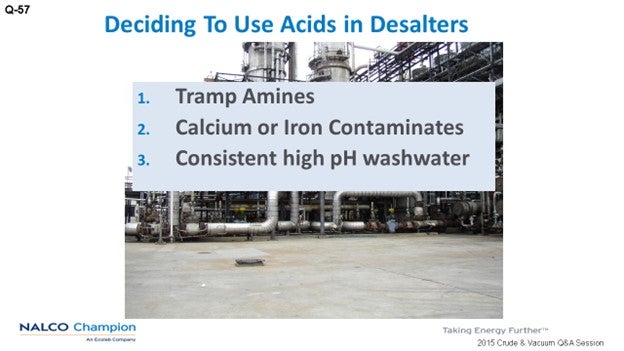
The tramp amines that are particularly of interest are those coming in with the light tight oils. Usually that can be the result of the reaction of triazines and H2S and come in with the crude. You will also have the overhead neutralizing amines used to react with the HCl (hydrogen chloride) in the overhead water. This overhead is often used as desalter washwater.
The second category is calcium and iron. Calcium typically comes in with high calcium crudes that contain high amounts naphthenic acids, and most refineries will want to remove the calcium. Some refineries want to remove the calcium; other refineries will choose not to remove it. So, if you want to remove the calcium, you will need to use acid.
The third situation is the high pH washwater. These are normally the situations when you need acid.
The key here is what acid you use. You do not use an inorganic acid; you have to use an organic acid. Vendors will select certain acids for different situations. The upside is that you can control the pH. In some situations, you need to reduce the pH to less than 3.5 to remove calcium from calcium naphthenates. At this low pH, corrosion is a major concern; so, you will need to inject a corrosion inhibitor prior to the injection point of the organic acid into the washwater line to the desalter. The pH will increase to 6 because the acid will have been neutralized in the desalter.
The other aspect is that some of the organic acids used will partition to the oil phase. Therefore, you will need more neutralizing agent for that acid, because it will distill up into the overhead section of the distillation tower. And the third item is, since the organic acid is water-soluble, an increase in the COD (chemical oxygen demand) in your wastewater treatment plant will occur. So those are some positive aspects of acid use, because you do remove the contaminants from crude oil. However, there are some side effects as well.
ALLRED (Suncor Energy, Inc.)
Much has been written on this topic. Your chemical service vendor can provide a lot more details on the specific types of acids that are appropriate, as well as their impacts. The three main reasons, as Michael mentioned, are to add acids to the desalters to partition tramp amines into the water phase, to control metals such as calcium, and to reduce the high pH that is affecting your water. There is a good write-up in the 2012 AFPM Q&A on this topic. Question 61 has a lot of details.
I want to add a little personal experience. We recently started an acid injection at one of our desalters to partition some tramp amines, and the performance was not what we expected it to be. So, after we did a little investigating, we found that one of the sources of our washwater for our desalter was well water that was really high in alkalinity. It had a high calcium carbonate content that was buffering the acid. So as soon as we realized this, we pulled out the well water and just injected a fresh, clean source of washwater for our desalters. The acid injection started having the intended effect. So, it is very important for you to understand your washwater in the first place. Our current chemical injection is just a test, and we have yet to determine if we want to continue this [process?] or if removing the source of high alkaline water will be enough.
I think it is important that you have a holistic approach. When you add an acid injection in your desalter, you also need to keep an eye on your overhead streams and the condensed water coming out of your overhead boots, because you could start to see impacts there as well. The same principle that will have you partition your amines can also have an effect on the overhead system and cause your overhead amines to start staying in the water. If you are using sour water as a source of desalter the water, you could end up recycling it as well. So, you just must keep an eye on amine concentration in your desalter to make sure that you understand that impact.
LUIS GORDO (Amec Foster Wheeler)
Processing of Canadian or other crudes (if their amine content is high), along with usage of stripped sour water, can lead to high pH water, making it necessary to inject acid into the makeup water for pH control. High naphthenic acids, in conjunction with high pH water, results in the form of soapy liquid, which makes it harder to break emulsions, resulting in poor desalting. Optimum desalter water pH is 6.0 to 8.0; however, with naphthenic acid crudes, pH in the range of 5.5 to 6.0 is recommended. If necessary, desalter water pH can be lowered by adding dilute hydrochloric acid to desalter water upstream of the desalter. Dilute sulfuric acid is sometimes used for this purpose but should be avoided to prevent formation of hard sulfate scales. Excessive injection of hydrochloric acid will lead to compounded crude tower overhead corrosion issues.
DENNIS HAYNES (NALCO Champion)
Tramp amines removal and some soluble metals removal (specifically calcium although iron and others have been mentioned) are reasons to use acidification at the desalters. Many acids have been used; however, many of the applications have included acetic, glycolic, and citric. All of these organic acid-based removal agents contribute to COD in the wastewater treatment plant, as has been discussed at previous AFPM Q&A sessions. All agents will carry decomposition downstream and go overhead in fractionation columns to some degree (directly or due to thermal decomposition), and this will result in reduced pH requiring adjustment to overhead corrosion control management. It has also been determined that glycolic acid generates foulant material in the crude unit hot preheat due to either self-polymerization or formation of calcium glycolate particulate. Additionally, citric acid application may precipitate calcium citrate in desalter vessels and effluent lines in cases where calcium loading, and citrate amount are sufficient.
PHILLIP THORNTHWAITE – Nalco Champion
Desalter acidification has been shown to be an effective means of resolving difficult emulsions in desalters while enhancing the effectiveness of the applied demulsifier chemistries. Some of the reasons that refiners may turn to using acidification additives are:
-
Enhancing desalter oil water separation (reduce oil under carry and water carryover),
-
Extracting amine/amine salt contamination from crude oil, and/or
-
Removal of contaminants [e.g., oil soluble metals; acid soluble particulates, calcium carbonate (CaCO3)]
Acidification additives typically are either mineral acids (e.g., sulfuric acid) or simple organic acids (e.g., acetic acid, glycolic acid, or citric acid). There are both positive and negative impacts associated with most of the acids used as adjunct chemistries to acidify desalter washwater.
The partitioning of acids to the oil phase and the acid/acid salt concentration in the brine droplets contained within the desalted crude led to acids being carried downstream of the desalter. Once downstream of the desalter, these materials can have several notable impacts on a crude unit. Organic acids, such as acetic and glycolic, are known to distill and/or decompose into the overhead system of the crude tower while the use of sulfuric acid can lead to an increase of SOx acids overhead. This increase is noted by an increase in corrosion and neutralizer demand. The injection of acids into the desalter washwater line to control brine effluent pH to 5.5 to 6.0 can result in a desalter washwater inlet pH of less than 4, and metallurgical upgrades or reliable corrosion inhibitor additives need to be used to protect the washwater system and mix valves.
Metal salt solubility will inevitably become an issue if an inappropriate organic acid is applied as a metal's removal additive. Metal salt deposition can result in the fouling of preheat exchangers downstream of the desalter, as well as in brine effluent coolers, not to mention the fouling of desalter vessels.
In summary, desalter acidification can be utilized to improve desalter performance and contaminant removal. However, a careful review of the system and establishing a comprehensive chemical management program implementing good controls prior to feeding acidic additives should be conducted to prevent unwanted downstream impacts such as corrosion and fouling.
RALPH WAGNER (Dorf Ketal)
Crude desalters that are operating with a high brine pH – generally greater than 8.0 – will typically experience salt removal and dehydration efficiency losses and oil carryunder issues due to stabilized rag growth at the oil/water interface. The increase in brine pH can be driven by ammonia and amines in the washwater and tramp amines in the incoming crudes. Acidification of the washwater can be used to improve emulsion resolution and facilitate amine portioning to the brine and for metals removal (such as calcium and iron) from the crude. Possible acids for use in the desalter include hydrochloric, sulfuric, acetic, citric, and glycolic acid.
While acidification can be used to lower the aqueous phase pH in the desalter, there are numerous issues with the use of mineral and most organic acids in the crude desalter. First, the injection facilities for handling acids must be expensive, upgraded metallurgies engineered specifically for the application. This usually has to include a pH controller since these acids can quickly drive the pH much lower than is desirable. These acids will tend to cause scaling issues in the desalter and downstream brine coolers, so the injection of an adjunct scale inhibitor is often required (or included in expensive “proprietary” organic acid products). The acids will frequently partition into the oil phase where they will travel to the crude atmospheric tower overhead and contribute to corrosion activity.
Patented non-acid technology is available to U.S. refiners that can be used for tramp amine removal, metals removal, and emulsion resolution in the desalters. These non-acid chemistries will maintain the desalter brine pH safely between 6 and 7 while utilizing standard chemical injection equipment (no metal upgrades or engineering). Amines and metals are reacted into water-soluble forms that are removed in the brine with minimal impact on the WWTP.
MICHAEL BRADEN (NALCO Champion)
Under normal desalter operating conditions, with a consistent crude feed and a washwater pH in the 5 to 9 range, acid addition is typically not required regardless of the API gravity of the crude. There are some situations where acid addition is warranted:
-
Removal of tramp amines;
-
Metal removal: specifically, calcium and iron; and,
-
High pH (> 10) washwater.
Tramp Amines
The primary function of amine- and nitrogen-based compounds in the oil and gas industry is to reduce the vapor phase concentration of H2S so that the product can be safely shipped and stored. In the refining industry, these compounds are principally used to control the pH of the aqueous environment in the crude overhead condensing equipment, control the pH of condensed steam, and sweeten or remove H2S and CO2 gases from various refinery gas streams.
The presence of these compounds, their reaction products, and their chloride salts can have a potentially serious impact on some refinery operations, equipment integrity, and refinery profitability. The principal refinery operations that have been impacted by these compounds have been the desalter, crude fractionation and condensing equipment, and the wastewater treatment plant. It has also been well established that the source of these compounds can be traced to many different points. They can be present in crude oil, refinery slops, and stripped sour water; as desalter washwater or overhead accumulator water (as desalter makeup or wet reflux to the tower); or in some cases, in the stripping steam used in the towers. The impact of some of these amines, like those being added to control pH in the overhead condensing system, can be controlled by properly selecting an amine that is suitable for the process conditions, equipment, and environment or by applying a properly designed and implemented overhead corrosion control program. The other amines, like triazine, that are used to scavenge H2S from crude oils are monoethanolamine (MEA), diethanolamine (DEA), methyldiethanolamine (MDEA), and diglycolamine (DGA) which are used to sweeten refinery gas streams.
Calcium and Iron Contaminants
Calcium naphthenate is an organic salt that can form in oil production systems that are handling a crude oil with a high acid number (TAN). The problems caused by calcium naphthenate range from oil-treating problems and poor water quality to heavy deposits that can plug lines and valves. “Calcium” naphthenate is really a generic term. The deposits formed will usually contain calcium, sodium, magnesium, iron, and other metal naphthenates, and possibly asphaltenes, scale, and other solids.
Naphthenate salts form when naturally occurring naphthenic acids in the crude oil come in contact with metal ions (such as calcium) in the produced water under the right conditions of pH and temperature. Naphthenic acids are found in many crude oils but can be troublesome in higher concentrations. The industry standard for measuring the amount of naphthenic acid in a crude oil is an ASTM test that generates a total acid number or TAN value. A TAN of greater than 0.5 will decrease the price that refineries pay for a crude oil because of the corrosion that such acids cause in refinery systems. A TAN of 1.0 or more means that the crude is high in acid content and that the formation of calcium naphthenates is a possibility.
High TAN crudes are currently being produced in several major regions including the North Sea, the Gulf of Mexico, California, Venezuela, West Africa, and China.
Organic acid addition will transfer the calcium ion from the naphthenate to the organic acid (ion exchange). The calcium/organic acid complex should be water-soluble, thus transferring the oil-soluble calcium to a water-soluble calcium complex.
Iron contaminants are usually found in the crude as either ferric (+3) or ferrous (+2) ions and are normally the result from corrosion. The iron compounds usually found in the crude are iron sulfide, ferric oxide, or ferrous oxide. Precipitation of these materials can cause plugging of heat exchanger trains, tower trays, heater tubes, etc. In addition, these materials can cause corrosion to any surface on which they are precipitated. In some crude oils, the iron ions are trapped inside the asphaltene aggregate and can only be removed by precipitating the asphaltenes (which can lead to a different set of issues).
High pH Washwater
Although the quality of washwater is very important for good removal of chlorides, solids, and other contaminates, if the pH is >7.5 on a consistent basis, then an acid program should be considered. In many cases, buffered desalter washwater containing high amounts of ammonia (washwater should have less than 50 ppm ammonia) or tramp amines are the root cause of high pH issues.
High pH in the washwater will cause NH3 or amines to partition to the oil phase, which can lead to ammonium or amine chloride salt deposition in the atmospheric column. In addition, high pH washwater promotes the formation of emulsions in the desalter when the basic compounds react with naphthenic acids to form naphthenate salts; e.g., sodium or ammonium naphthenate, which are essentially soap molecules.
A thorough analysis of the washwater is recommended that includes inductively coupled plasma (ICP) for cationic ions, amine analysis, anionic ion determination, organic acid analysis, pH, BS&W, total suspended solids, and other tests.
Types of Acids Used
In each of the areas discussed above, acids are employed to mitigate the contaminant or pH issues and transfer it to the desalter brine. A decision to use an acid must discuss the advantages and disadvantages of the acid to be injected into the system.
Normally, acids are injected into the desalter washwater and combined with the crude using the desalter mix valve to thoroughly blend the water and oil phases. Generally, acids such as acetic, glycolic, malic, and citric have been used with success with one or more of the situations listed above.
All of the acids listed are reasonably inexpensive. However, all of the acids will lower the pH of the washwater. Typically in the calcium or iron situations, the pH must be lower: to at least 3. Once mixed with the crude oil, the acid is neutralized by an ion transfer mechanism and the pH rises to 5 to 6, which is within the normal range for desalting.
One issue is that the low pH will enhance corrosion of the washwater line from the addition of the acid to the mix value. A corrosion inhibitor should be used to protect the washwater line. Once the acid is neutralized, a corrosion inhibitor is not necessary.
Another issue is that the acids will partition into the oil phase and thus will cause corrosion in the atmospheric tower overhead. A robust monitoring of the corrosion rates and pH is necessary to keep the overhead acids neutralized.
When using citric acid for calcium removal, the refinery must be aware that calcium citrate is essentially oil- and water-insoluble and will precipitate once formed. This acid is good for pH control and iron removal.
Polymeric organic acids have also been employed for calcium removal; however, the calcium complex of the polymer is insoluble at desalter temperatures and will precipitate.
Another concern is the added carbon oxygen demand (COD) to the wastewater treatment plant. All of the organic acids and the corresponding metal salts will increase the COD of the water phase and may be a challenge to the refinery’s biological treatment system.
BRUCE ALLRED (Suncor Energy U.S.A.)
The three main reasons to add acid to the desalter are to partition tramp amines from the oil phase into the water phase, to control metals such as calcium, and to reduce a high pH that is affecting oil water separation. Much has been written on this topic, and your chemical service vendor can provide details on what types of acids are available and their potential impacts and side effects.
I wanted to add a simple caveat based on some recent experience. We recently started an acid injection trial on a desalter in one of our crude units to better partition tramp amines. Performance was not as expected until we realized that the source of desalter water included well water that was particularly high in alkalinity (measured as CaCO3). This was buffering the acid, making it ineffective. Once this source of water was removed, the injection started having the intended effect.