Question 57: Advanced (Closed)-Riser Termination Systems have been around since the 1990s. Explain any technology improvements you have seen based on experience and learnings.
TRAGESSER (KBR)
Advanced Riser Termination Systems are, by definition, a way to quickly terminate the reactions occurring in the riser. The goal is to rapidly separate the catalyst from the hydrocarbon vapors and then quickly minimize the time the hydrocarbon vapors are at reaction temperature before being quenched in the main fractionator. If these two goals are accomplished, post-riser reactions are minimized. The most undesirable of these reactions is thermal cracking reactions that reduce gasoline yield and increase dry gas make.
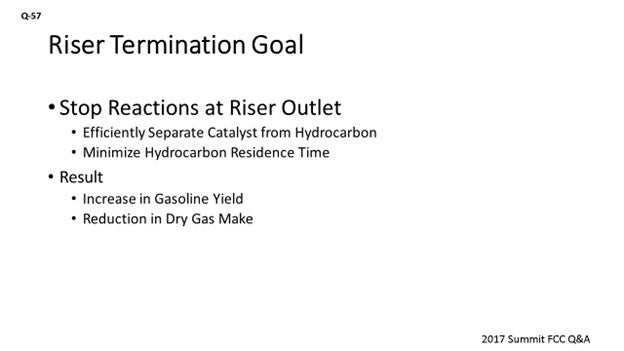
Riser termination systems have evolved from the early days of riser cracking that commonly used inertial separators where the riser hydrocarbon product and catalyst were discharged into the reactor where non-desirable post-riser cracking reactions occurred. The next major advancement was to add efficient catalyst separation devices – such as riser cyclones to the end of risers – to quickly separate the catalyst from the hydrocarbon products. While this terminated that catalytic cracking, it still allowed the hydrocarbons to undergo thermal cracking reactions as they were discharged into the large disengager vessel, which resulted in long hydrocarbon residence times.
Just a little history: In the mid-1980s, Mobil recognized a need to eliminate these undesirable thermal cracking reactions that occurred in disengager and developed the first Advanced Riser Termination System – commonly called ‘closed cyclones’ – where they coupled the riser cyclones directly to the upper cyclones. Mobil pioneered the use of advanced riser termination and installed it in eight of their own units in the late 1980s. In 1990, KBR formed an FCC alliance with Mobil and began licensing the technology. While Mobil’s development and commercialization worked out many of the issues prior to KBR’s involvement, there have been improvements in the technology since then, which I will discuss.
Many of the improvements in KBR’s 27 years of experience have been operational-related. For example, we have been able to reduce startup steam requirements by lowering the required riser cyclone inlet velocity requirement without any negative impact.
One of the keys to a successful startup is to avoid overloading the cyclone system during initial steam circulation. This means making small increases in catalyst circulation and letting things stabilize before making another increase. Once feed is in the unit and cyclone velocities are increased, then the system becomes very stable and resilient.
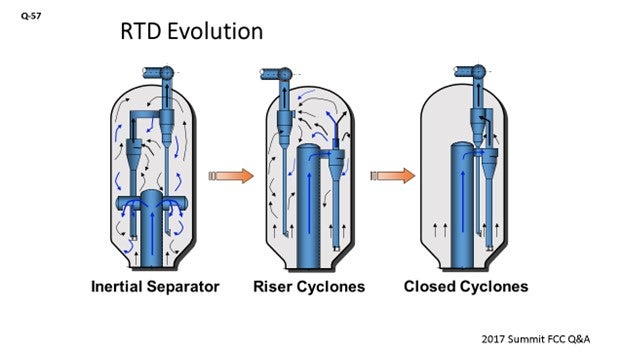
One improvement that has been developed is referred to as ‘self-stripping closed cyclones’ where small holes are placed in the lower cone section of the riser cyclones where the stripping steam flows through. The purpose of this modification is to eliminate the small 2% underflow of hydrocarbon that is normal for a closed cyclone system. This improvement further reduces thermal cracking, thereby increasing the gasoline yield. Another version of this process is referred to as ‘direct stripping’, where external steam is supplied separately to the cone section and the normal cyclone hoods are maintained. This gives the operator flexibility to optimize the cyclone stripping steam.
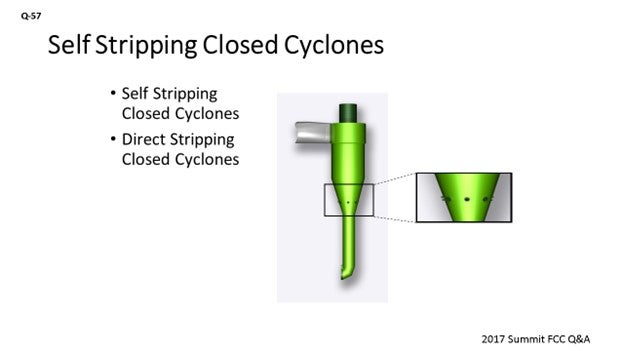
Another change we are implementing on newer projects is to use an intermediate plenum between the riser cyclones and the upper cyclones, as shown in the figure. The main reason for this change is that it allows the catalyst to be redistributed to the upper cyclones and makes the system more resilient to an upset of a primary riser cyclone. Another advantage is that it allows the use of a different number of upper cyclones than that of the riser cyclones. This can have a layout advantage, especially on larger units where we can have two large riser cyclones and maybe four or five upper cyclones. Due to the ability to use smaller upper cyclones, the required vertical space will be reduced as a result of the cyclones being shorter compared to the layout of a system with two large upper cyclones.
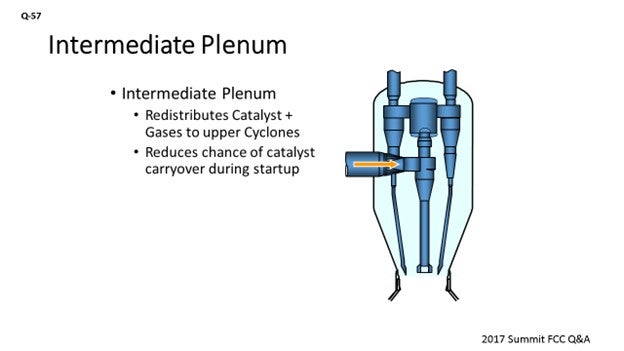
MALLER (TechnipFMC Process Technology)
The evolution of our technology at TechnipFMC is similar. We initially had the inertial separator, which had vented gas tubes to the upper reactor section to be close to the reactor cyclone inlets. Now we have a totally closed system. What is shown on the slide is the RS2 (riser separator) technology. One important point I want to make is that the ability to maintain ease of operation during startup, shutdowns, and upsets – without the risk of massive catalyst carryover – is important. With this technology, the diplegs are very large and not prone to flooding. It is essentially an inertial separator, so there is not a high velocity requirement to maintain adequate separation; therefore, there are no emergency steam requirements for startup. If we get enough velocity to transport catalyst, it is enough velocity to achieve good separation. Therefore, the RS2 does not experience any massive catalyst carryover events during startup.
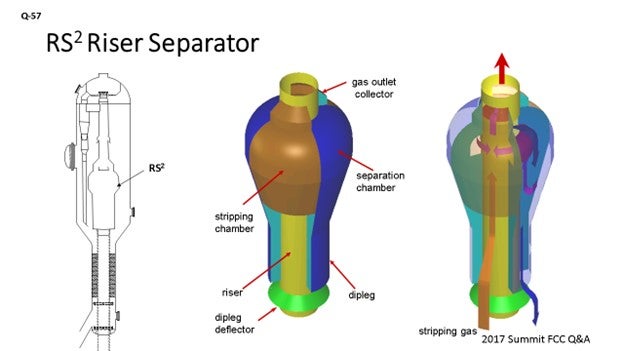
Our recent improvements: We are now learning that we have more units go through turnarounds. Unfortunately, the cycle for these lessons on reliability is every five years when a unit shuts down. We are currently making mechanical and reliability improvements to each situation when we see the requirement. We have made some changes to the slip joint design that allow for the independent thermal expansion of the lower section versus the upper section. We are also working continually with the cyclone vendors to try to improve the overall system efficiency for catalyst collection.
DAVID HUNT [Shell Global Solutions (US) Inc.]
I would like to add that in the FCCs we operate at Shell, as well as at several of our third-party customers, the cyclone technology uses what we call a ‘coke catcher’ which keeps coke from falling into the reactor cyclone dipleg and potentially blocking the dipleg during the run. Other developments in our Shell cyclone system include the use of a vortex stabilizer in the secondary cyclones to control the vortex and avoid dust bowl/dipleg erosion.
ALEX MALLER (TechnipFMC Process Technology)
The primary goal of a modern riser termination system which considers the close coupling of the primary and secondary separating devices is the reduction of residence time and, thus, the minimization of undesirable thermal cracking reactions. This post-riser cracking usually translates to dry gas yield at the expensive of other, more valuable products. By revamping an older type of system to a close-coupled advanced system, we have seen a typical reduction of dry gas yield of about 20% with corresponding increase in liquid product volume.
Another important goal of a modern riser termination system is the efficient separation of catalyst particles from the reactor gasses, implemented with the aim of preventing excessive catalyst accumulation in the main fractionator bottoms circuit. This goal is important for all modes of operation, including startup/shutdown and transient periods. The system we have now is extremely efficient during normal operation, but most notably retains very high levels of efficiency at all times when catalyst is circulating. The primary separator is a positive pressure type, and the diplegs are very large and not prone to flooding. This arrangement ensures that any velocity sufficient to transport catalyst up the riser is enough to achieve adequate separation. No emergency steam is required. No massive catalyst carryover events have occurred on any of our installations.
Our focus for technology improvements in recent years has focused on the reliability, as well as incremental improvements to the above-mentioned primary goals. For reliability, we have updated the design for the slip joint that ties together the upper cyclone portion of the system to the lower termination device. The new slip joint design has proven to be extremely robust without any issues reported on any units.
MATTHEW WOJTOWICZ (Honeywell UOP)
Evolution of UOP’s Vortex Separation Riser Termination Technology
Before evolving to the vortex separation riser termination technology, UOP gained experience with all types of riser termination technology. Since 1983, UOP’s designs for riser termination devices have focused on reducing the post-riser vapor residence time in the reactor vessel. Since many of UOP’s efforts have involved technology upgrades in existing units (revamps), a variety of mechanical systems have been implemented to accommodate the wide variety of existing reactor sizes and styles. All of the UOP designs emphasize operating flexibility and mechanical reliability.
UOP’s current riser termination design incorporates the state-of-the-art vortex separation technology to minimize the vapor passing into the reactor vessel and thereby minimize non-desirable reactions.
In 1995, UOP commercialized the VSS™ (vortex separation system) technology which was specifically designed for higher capacity units with an internal riser while maximizing hydrocarbon containment, operating flexibility, and mechanical reliability. UOP’s VDS™ technology offers the same benefits for units with external risers. The VSS technology has evolved since it was initially commissioned in 1995. These enhancements have further improved hydrocarbon containment, operating flexibility, and mechanical reliability. A few of these enhancements are summarized below.
Hydrocarbon Containment Advantage
Vortex separation technology represents the highest hydrocarbon containment technology available, as it provides more than 99% containment of the hydrocarbon product vapor relative to only 94 to 97% for the next best system (direct-connected cyclone systems). The containment advantage is based on the quantity of hydrocarbon product vapor that is entrained with and adsorbed on the catalyst discharging from the first-stage cyclones. This hydrocarbon is equivalent to as much as 6% of the riser vapor. The hydrocarbon carryunder spends relatively long residence times in the reactor vessel before finally exiting out through pressure equalizing tubes.
The vortex separation technology is designed to eliminate the hydrocarbon flow that exits at the bottom of the conventional riser separation devices, as well as efficiently separate the catalyst from vapor exiting the riser. The top of the stripper and the bottom of VSS chamber are integrated with each other thereby allowing the riser and stripper vapors to be contained. These vapors are prevented from entering the reactor vessel where they can undergo nonselective thermal cracking due to long residence times. The containment advantage of the VSS technology is illustrated in Figure E-1. Since the original implementation in 1995, the design has been tweaked to further improve hydrocarbon containment. The bed level has also been optimized further improving yields.
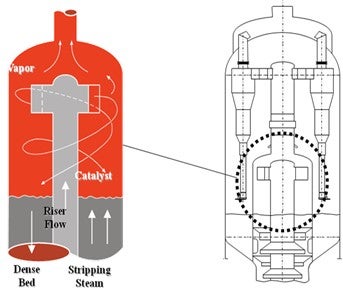
Figure E-1. VSS Hydrocarbon Containment Advantage
The superior hydrocarbon containment performance of the vortex separation technology provides improved yield performance over all competitive systems. The hydrocarbon not contained by the primary separation device undergoes significant nonselective thermal cracking due to long residence times in the reactor vessel. This results in a significant increase of dry gas, as well as major losses of gasoline, LCO (light cycle oil), and overall product olefinicity. Dry gas production – at the expense of the gasoline and LCO production – represents an opportunity loss which limits the profitability of the FCC unit. Additionally, the reduced olefin content of the gasoline will result in a reduction in the octane of final FCC gasoline product. The VSS technology reduces nonselective, post-riser cracking and can help maximize the profitability of the FCC unit through improved gasoline selectivity, improved gasoline octane, and reduced dry gas.
Operability and Reliability Advantage
UOP has significant experience within fluid catalytic cracking technology and has garnered a reputation for designing technologies for maximum operability and reliability. The vortex separation technology offers clear operational advantages over previous generation riser termination devices (RTDs), including ease of startup, turndown flexibility, reduction in reactor coke formation, and reduced incidents of severe erosion of internal components.
During FCC unit startups, operations can experience pressure upsets which quickly send large amounts of catalyst into the reactor vessel. Pressure upsets of this kind are known to quickly overload other RTD designs and send large amounts of catalyst to the main column, causing costly high-catalyst makeup rates and problems in the main column or the main column bottoms product. Conversely, the vortex separation technology can easily handle pressure surges and reduce the risk of catalyst carryover through the use of its unique primary separation design. This operational advantage manifests itself as smoother and more robust operation of the FCC unit during upsets and is relatively more forgiving during unit startups.
Not only does the vortex separation technology offer process and operability advantages, but it also can provide several reliability advantages. Coke formation in a reactor is largely influenced by the reactor technology and appropriate use of steam. The coke produced in the reactor space can build up on the reactor walls or refractory, pressure equalization openings, and other flexible joints, which can lead to either equipment failure or increased maintenance costs. The latest vortex separation technology creates a hydrocarbon-free environment in the dilute phase of the reactor by maximizing riser hydrocarbon containment. Coke has been completely eliminated from the reactor annular space. The vortex separation technology has been used as a process revamp improvement, as well as a technology upgrade to address coke formation.
UOP’s design methods include several considerations and features which have dramatically reduced the incidents of severe erosion of internal components over time. Internals are designed with appropriate orientation and velocities to minimize erosion potential in critical areas such as cyclone inlets. UOP also specifies proven refractory- and abrasion-resistant lining materials in these areas which often survive a run with only small sections requiring repair. Utilizing these design methods, the vortex separation technology offers improved mechanical reliability of the reactor internals, improved unit availability, and reduced maintenance costs over the next best RTD alternative. Also contributing to the high mechanical reliability of the technology is the fact that over 95% of the catalyst separation occurs in the low-velocity VSS chamber, meaning that less than 5% of the catalyst will enter the higher velocity cyclones. There are multiple refiners with UOP’s latest VSS technology who achieve 99+% onstream efficiency with minimal maintenance required to internals following a campaign of more than five years.