Question 56: Some crude tower overhead deposition appears to be linked to corrosion treatment programs (i.e. filming corrosion inhibitors and neutralizers). Have you confirmed this and what are the potential mechanisms that can lead to this deposition?
Doug Meyne (Champion)
Corrosion inhibitors (filmers) have been known to cause deposition in several different ways. Generally, the cause is injection into an overhead that is too hot, flashing off the carrier, or injection of neat chemical, flashing off its solvent. Even if the solvent doesn't flash off completely, filming inhibitors lose solubility at higher overhead temperatures (>280F) and the carrier stream concentration can get high enough to precipitate the filmer active ingredients. Once that precipitation occurs, there are several scenarios listed below that can unfold.
1)Corrosion inhibitors can lose their solvent and begin to slowly dehydrogenate in the presence of the flowing hot vapor, particularly without a slipstream. Depending on the process environment (T, P, V), a dehydrogenated filmer can accumulate in a localized region and become a coke-like material that can become a foulant.
2)Elemental sulfur can be formed in the process oil from unrelated events. If an unsaturated bond is created in the filmer by dehydrogenation, there becomes an opportunity for cross-linking with sulfur, forming a rubberized foulant coating the inside of the pipe. This rubbery compound is not uncommon in overheads, and, in at least one instance, it has been seen to have become thick enough to increase pressure drop in the overhead line.
3) A crude unit filming inhibitor is usually an amine. Fixed in place due to deposition by solvent loss, it can react with the HCl in the vapor, forming an amine salt. Being a weak amine, this does not happen quickly as compared to the neutralizing amines in the system. Under normal operations, the small amount of filmer salt of HCl that forms remain mobile in a liquid form and is removed from the system with the rest of the filmer. But once immobilized as a precipitate, it can be, and has been shown to be, corrosive enough to corrode injection quills and even cause through-wall piping failures.
Neutralizers
The route to fouling caused by neutralizers is substantially different than that of corrosion inhibitors. We should ignore those cases caused by some refineries that attempt to use alkaline metal hydroxides, like NaOH, as their overhead neutralizer. Those cases do exist but are rare for obvious reasons.
Neutralizers themselves will not foul. They must be in a salted form to foul; however, even the salted amines rarely foul. Exceptions to this general rule are those that fall into the –diamine category such as ethylene diamine or some of the steam neutralizers currently in use. These form high melt-point, oil-insoluble salts that will accumulate on trays and draw pans and years ago were responsible for a rash of unplanned shutdowns of atmospheric distillation columns. In rare occasions, such as injection into vacuum columns, some of the solid salt formers such as morpholine have caused pluggage in towers, again forcing shutdowns. The larger fouling problem from neutralizers comes from the corrosivity of their chloride salts to most metals. This topic has been discussed extensively over recent years. Below is a brief summary.
•Amine and HCl salts can precipitate from the vapor upstream of the water dew point.
•They precipitate onto cooler surfaces, wherein their hygroscopic nature makes the deposit wet and corrosive. As more salt accumulates, the environment becomes extremely corrosive.
•The process is the following: the salt forms, ionizes in small amounts of water forming H+ and Cl- that corrodes iron to FeCl2 releasing H2 and the amine. The FeCl2 then easily converts to a FeS precipitate, thereby releasing the HCl to cause more corrosion. •The pipe/tube gets thinner, and the deposit gets thicker, with the outer layer comprised of mostly FeS, and the lowest layer, against the metal, rich in FeCl2.
•Deposits can continue to grow until they plug off an exchanger. The deposits will almost always be reported as FexSy or its oxide. •What happens to the amine? With every mol of Cl reacted with FeCl2, a mol of amine is liberated to evaporate away.
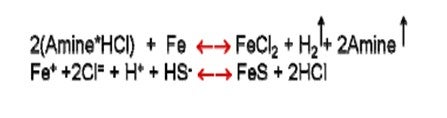
The image below was taken of a corrosion probe in service where salting was prevalent, with the SEM settings set such that HCl fluoresces. The outer layer of the probe deposit has been partially fractured away. On the left side of the image, where the outer layer is missing, the chloride concentration is obvious. In an edge view of the fracture, just right of center, note the presence of chloride largely under the FeS layer, with some small amount seemingly embedded in the FeS at other locations.
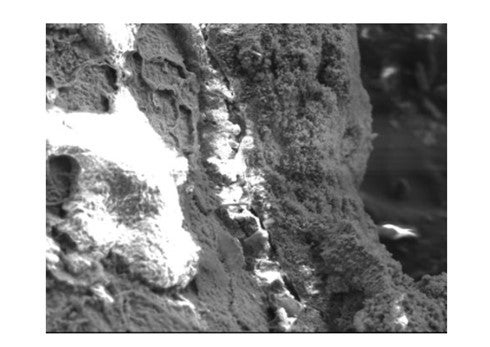
Eric Thraen (Flint Hills Resources)
We have experienced crude tower fouling due to neutralizer salt deposition on two occasions. Both involved the direct injection of neutralizer into a crude tower return stream – top reflux or top pumparound. Neutralizer injection to control overhead corrosion in crude overhead condensing systems is less likely to cause this fouling in the crude tower but care must be taken to control the injection rate within limits so that excess neutralizer is not present in the top reflux stream. Good desalting and well-managed caustic injection limit the chlorides in the crude tower overhead which limits the neutralizer requirement in the overhead system.
Jim Johnson (Marathon Petroleum)
We have experienced pitting from under-salt corrosion in the crude unit overhead exchange in four of our refineries. The analyses of these deposits indicate that the pitting was from chloride salts associated with various amines, including those found in our corrosion treatment programs. The pitting and residual iron foulant has been concentrated in the top/outlet section of the bundle. Three of the systems utilize water wash while the fourth does not, with the foulant pattern being similar regardless. The chloride salts formed by either process amines or from the chemical program are not captured with the water and deposit toward the back of the exchanger above the process outlet. In these exchangers the bottom section has not shown any appreciable corrosion.
Paul Fearnside (Nalco Company)
The vast majority of crude tower OVHD deposition is maybe related to the neutralizer salt deposition temperature. This in turn is determined via the partial pressures of the salt in question. Controlling not only the amount of neutralizer injected, but also the number of chlorides and SOx acids is key to eliminating this. Good, consistent, desalter performance is a must. Caustic injection into the desalted crude must be maintained and monitored at all times to minimize the chlorides. If crude OVHD waters are used as a source of desalter wash water, then determining the number of neutralizers in this water is necessary to understanding the salting potential within the upper tower internal sections, from recycled neutralizers. Oxygen sources into the desalter wash water must be eliminated to minimize the amount of SOx acids present. Use of an ionics simulation model, such as NALCO’s Pathfinder®, routinely is necessary to understanding and maintaining established corrosion and fouling KPI’s.
Sam Lordo (Nalco Company)
The vast majority of crude tower OVHD corrosion caused by chemical additive program can be attributed primarily to the neutralizing agent (organic amine or ammonia) and their salts. Filming amine corrosion inhibitors are not known to be corrosive if applied properly. Neutralizer selection should be done taking in account overhead circuit configuration, metallurgy, operating parameters. Corrosion incidences from neutralizers are generally related to:
•Deposition of the neutralizer salt in the ovhd equipment upstream of the water formation
•Misapplication of the neutralizer, such as, injection without a dispersion medium
To minimize neutralizer salt corrosion the follow steps can be taken:
•Selection of the proper neutralizer is done using simulation programs such as Nalco’s PATHFINDER® program. This lets one select the neutralizer that provides the necessary protection without formation of harmful salts in areas of the circuit that is not adequately waterwashed.
•Use a good simulation program routinely (up to everyday) to minimizing overdosing the neutralizer.
•Minimize the number of acids, such as chlorides, organic acids, etc., by improving desalting and using caustic.