Question 55: What strategies do you employ to purge solids from recovered oil at the wastewater treatment plant (WWTP) to avoid recycling solids back to the crude unit?
BRADEN (NALCO Champion)
Oh, yes, solids: the bane of the refinery. The crude unit wants them out of the crude oil, and the wastewater treatment plant would prefer not to have them. So essentially, we are talking about wastewater treatment solids. Some people call it recovered oil; some people call it slop oil; and some people call it skimmed oil. So, if I interchange these definitions, what I mean is recovered oil from the wastewater treatment plant.
A little background here: This oil will be chemically stabilized due to the chemical treatment of the primary wastewater treatment program. It is a water-in-oil emulsion. The solids and the water itself are chemically emulsified in the oil. So, if you do nothing and send it back to the crude unit, you will get massive upset. One barrel of untreated slop oil or recovered oil will give you back two barrels. So essentially, the refiners must ask the question, “What are you going to do with the skimmed oil?” First, if the refinery has a coker unit and the coker is not making anode-grade coke, then you could send that material as a coolant to the coker. Again, everyone has to be on board with that. The second option is to sell the skimmed oil to a remediator or have them buy it from you.
But typically, this recovered oil has a good dollar value for the refinery. Therefore, the refinery will want to recover the oil by removing the water and the solids. There are two methods for recovering the oil that are viable for the refinery. One is tank treating. For tank treatment, the tank should be heated and have agitation. You will need a chemical additive to resolve the chemically stabilized emulsion. Do not be shocked if the chemicals needed to resolve the emulsion may be up to 3,000 to 5,000 parts per million. You will need to add the chemical, thoroughly mix the chemical with the oily emulsion, and then let it stand at a minimum of 140°F (but no greater than 180°F) for about 72 hours (about 3 days).
As a result, some solids will fall out. You will have a water layer and an oil layer. In between the oil and water layers, you will always have a rag layer. You will have to make a decision about what to do with that rag layer. It will contain a lot of emulsion and solids. Some refineries will put the rag layer into a different tank and wait another day, even though the oil itself will have less than 2% BS&W (basic sediment and water), just delaying the decision about what to do with the solids.
The other way is to remove the solids from the system entirely, which is your goal, by using a centrifuge method. This method is very similar to a tank method, although you do not wait for the separation. You use heat, chemicals, and agitation. You need to let the treated slop oil stand for one to three hours, and then it is sent to a two-phase or a three-phase horizontal bowl centrifuge. A three-phase centrifuge is better.
In the waste oil stream going to the centrifuge, you will have to add a high molecular weight cationic polymer, usually emulsion polymer made down to a 0.5 to 1.0% solution. This chemical will take out solids in the rag layer, as well as the solids that fall out in the centrifuge. Because the centrifuge separates by specific gravity, that rag layer has its own specific gravity versus the other three. You will have solids, water, rag, and oil. So, the emulsion polymer will mix the solids and the rag layer together, resulting in a specific gravity which is higher than water. Therefore, you will then have solids plus the rag layer, water, and oil. The solids go out in one end, and the liquid goes out the other.
In a three-phase centrifuge, the operator controls the flow rate of the waste oil stream and the chemical polymer injection. The BS&W on the recovered oil is typically less than 1%, and you can send the solids to a non-hazardous landfill, if the oil content meets the required specifications of the landfill. Or if it does have too much oil on the recovered solids, the refinery could send it to a hazardous landfill.
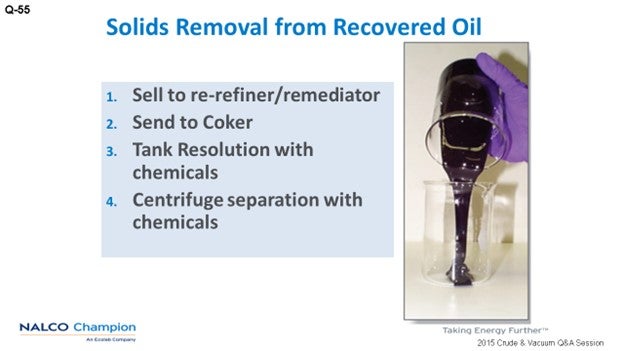
ALLRED (Suncor Energy, Inc.)
We have a full-time three-phase separator onsite in the refinery. It is owned and operated by a third party, and it is in operation Monday through Friday during the daytime hours. It is used primarily for our wastewater treatment system, collection of solids, and recovery of the oil in the water. We have found that just keeping the solids out of our system is well worth that expense. We have polymer and heat that helps remove those solids. There are sometimes when we do tank cleaning and keep this unit in operation around the clock to handle the solids coming out of the tank. By working through the weekends and extra hours, we are able to remove the solids and keep up with the daily needs of the wastewater treatment system. We have found that having that three-phase separator onsite all the time has been well worth it for us.
WEBER [Marathon Petroleum Corporation (MPC)]
We also have an outside third party who manages the solids. I do not really have anything else to add.
NAGASHYAM APPALLA (Reliance Industries Ltd.)
I have two questions. The first is: Has any refinery deployed the system of skimming the rag layer online? If so, what is the destination for the skimmed rag layer? Secondly, you have talked about deploying centrifuge separation, but a centrifuge works on the principle of the particle size. If the particles are very small, say less than 10 microns, does chemistry really work for coagulating and dropping the particles in a cyclone?
BRADEN (NALCO Champion)
To clarify your second question first, you are asking about removing the 10 micron-sized particles? Typically, wastewater treatment can remove down to 4 microns. Filters can get below that if you have the right filter system. But as a centrifuge, it really depends on the polymer you select and the agitation. Because you feed the emulsion polymer based on the flow, it is tough to say that the degree of particle size is removed. We have not really measured the particle size that is recovered in the crude. We do know that the filterable solids are very low using a 0.45-micron filter, but we have not looked at particle size. The primary goal for a refinery is to look at their specification of less than 2% BS&W. That is a normal specification for recovered. For some refineries, the minimum BS&W could be a little higher or a little lower. Could you repeat the first question please?
NAGASHYAM APPALLA (Reliance Industries Ltd.)
If the solids are bound to create a problem at the interface by forming a rag layer, it does not allow the emulsion to separate. So, the best way is to skim out the rag layer online. Has anyone deployed continuous skimming of the rag layer online and routing it to some destination? Where is the best destination to route the rag layer?
BRADEN (NALCO Champion)
Some refiners will have a rag layer drawn on their desalters to remove an increasing rag layer volume in the desalter. At Nalco Champion, we recommend using the correct desalter emulsion breaker that will allow the rag layer volume to remain at steady state. For Nalco Champion, an increasing rag layer volume is a sign of a poor emulsion breaker selection. Our goal is to have no oil carryunder and a steady-state rag layer.
WATTS (LyondellBasell)
For our refinery, we manage the rag layer by adjusting the mix valves, washwater, and desalter chemistry to minimize the potential for oil undercarry. We don’t skim the interface to remove the rag layer. The question he is asking is: If you have a rag layer at the desalter, rather than trying to bleed it all out the bottom, do you have a skimmer at the interface to continue to remove the rag layer? And if you do that, what is the destination for that material?
BRADEN (NALCO Champion)
Good question. [Laughter] Usually the rag layer is put into a different tank, and we wait for it another day. This rag layer is normally not chemically stabilized and can be fairly easy to separate; however, it may take a secondary emulsion breaker to drop the solids and release the oil.
SAMUEL LORDO (NALCO Champion)
We are referring to what is commonly called “cuff draw”, which is a pipe located at the interface. You pull off that pipe and actually send it to a different tank, as Mike indicated. Typically, you can treat it as it goes to the tank, which is preferable, rather than building inventory in a slop tank. The reason is that it then it becomes more of a challenge to handle. You would pull the rag out of the desalter and send it to a separate tank. Sometimes it is a brine tank, so you can mix the emulsion with water and flip the emulsion a little. So, there are a couple of strategies you can utilize with the cuff draw, but they are gaining popularity with the high solid crudes.
BRADEN (NALCO Champion)
Usually that is not chemically stabilized, so it is easily separated.
ALLRED (Suncor Energy, Inc.)
I just have a quick comment about the second question. Our trigger point is 1% BS&W. So, when we run it through the centrifuge to recover the oil, we test that oil. If it is greater than 1%, we will send it back through the centrifuge. If it is less than 1% BS&W, we will send it on to a crude tank.
JAMES PROROK (Husky Energy, Inc.)
Nalco treats our desalters, and we do a draw of the cuff layer to remove iron. We still make petroleum-grade coke for anodes. So that drawing a cuff pulls out the iron. We take the cuff, which is about 10% oil and 90% brine, and send it to the free water separator, which breaks the oil and water mixture, leaving us with a high solids oil. The oil goes to a storage tank, which feeds the centrifuge. The oil from the centrifuge still has a significant number of fines. We pilot-tested a ceramic membrane for a final polishing step to get the fine solids out of the oil.
MICHAEL BRADEN (NALCO Champion)
Recovered oils in this explanation will be called “slop oils.” Slop oils are formed during the clarification of the oily wastewaters from the process units, such as desalters. These chemically induced oil emulsions will usually contain free water, emulsified water, and oil-wet solids. Emulsions of this type are very stable. Recovered oil is the oil that is separated from the water and solids from the WWTP skimmings.
The slop oils have the following characteristics: They are highly viscous, have a low API gravity, and contain 10 to 60% water and 10 to 40% solids. Oil skimmings and slop oils are hazardous and cannot be landfilled without oil reduction. Stricter regulations are driving customers to more recycling and treatment of these types of waste streams.
Typically, the BS&W requirements for recovered oil is less than 2%.
Slop oils are usually stored or used in one of the following ways: holding tanks, mixed with crude oils, incinerated, sent to the coker unit, or treated. Untreated slop oil brings lots of water into the system that may not be able to cope with either the water or the steam generated in the process. Treating the slop oils to remove the solids and water and obtaining the recovered oil is the recommended method.
Why treat slop oil streams?
-
Removes solids from the crude cycle;
-
Minimizes wastes;
-
Recovers oil, thus recovers money;
-
Restores storage tank capacity;
-
Oil-free solids can be incinerated at a lower cost; and,
-
Reduces disposal and operating costs.
There are four options available to remove solids from refinery system:
-
Send the entire oily skimmings stream to the coker unit (if the refinery has one and is not producing anode-grade coke);
-
Send the entire oily skimmings stream to a remediator;
-
Chemically treat the oily skimmings onsite via a heated tank and send the rag layer to a hazardous material landfill; and,
-
Chemically treat the oily skimmings onsite via a heated tank and centrifuge.
All of the methods will cost money; however, the last two will bring revenue to the refinery.
There are other technological attempts to separate oil, water, and solids from WWTP skimmings. These technologies include microwave, ultrasonication, and evaporation. Unfortunately, these methods either do not resolve the emulsions or remove the solids from the crude; plus, the cost of implementation makes these methods prohibitive.
The two most common methods involve chemical and mechanical treatment of the slop oil to remove solids. Both involve chemical emulsion breakers, heat, and agitation. However, one method uses gravity separation and the other uses centrifuges and additional chemistry.
-
Resolving Slop Emulsions in a Tank – Gravity Settling
This method requires a heated tank and some form of agitation to thoroughly mix the chemical additive to the slop oil. Heat reduces the bulk viscosity and helps coalesce the water droplets. The chemical helps resolve the oil-in-water emulsions and water the solids. The chemical can be injected on the suction side of a transfer pump or added to the tank that has mixers. Once the chemical is mixed with the slop oil and put into a heated tank, time is needed to allow the water, solids, and oil to separate, which may take up to 72 hours or more. Warning: There will always be a rag layer. No matter how much chemical is added or how much time is allowed for separation, resolving the slop oil emulsion in a tank always leaves a rag layer. This rag layer consists of water, oil, and oil-wet solids. The recovered oil will have a BS&W of less than 2%. The water will have solids and very little oil.
So, the question that every tank breakage application must answer is: What is to be done with the rag layer? Some put it away to a holding tank to avoid the question for another day. Others send the material to a coker (if they have one onsite), and different refineries will pay the landfill costs for hazardous materials. However, the rag layer must not be removed with the oil phase since this will cause severe upsets in the desalter.
-
Resolving Slop Emulsions with a Centrifuge
This method is very similar to the one described above; however, the difference is that a two- or three-phase horizontal bowl centrifuge is used for the separation process. Essentially, centrifuges separate by specific gravity: solids > water > rag layer > oil. Notice that the rag layer has specific physical characteristics. Furthermore, the use of a chemical additive to that combines the rag layer with the free solids will increase the specific gravity of this mixture to greater than water. Thus, one will have solids, water, and oil separation with no rag layer.
The process is similar to the tank breakage method. Chemical addition (water-in-oil emulsion breaker), heat, and agitation is needed to help resolve the emulsion. Once the chemical is sufficiently mixed throughout the slop oil and heat applied, the slop oil is left standing for a short period of time (one to three hours). Then the stream is sent to a horizontal centrifuge for separation.
At this point, the stream will separate into four layers: solids, water, rag layer, and oil. However, the rag layer can be removed by the centrifuge by using a high molecular weight, high cationic-charged emulsion polymer. This polymer is injected into the centrifuge feed (as a 1% solution in water) “on the fly.” The polymer will combine the solids in the rag layer with the water-wet solids, thus producing a layer that has a higher specific gravity than water. When the polymer-treated stream is centrifuged, only three layers are separated: solids, water, and oil.
A three-phase centrifuge will separate solids, water, and oil into three streams. There is an inner scroll into the horizontal bowl which forces the solids to go in the opposite direction of the liquids. For the liquid phase, there is a weir placed at the oil/water interface, separating the two layers. This weir, as well as the polymer addition, is controlled by the centrifuge operator. Final results are a good cake solid, clean water, and recovered oil with a maximum of 2% BS&W. Often the BS&W is lower than 1%. The recovered oil can be blended with the desalter feed stock having very few, in any, issues in processing. The cake solids can be landfilled; and depending on the amount of oil left on the solids, can be landfilled in a non-hazardous disposal site. More importantly, the solids have been removed from the refinery cycle.
PHILIP THORNTHWAITE (NALCO Champion)
The reprocessing of recovered oils (or slop oils) through the crude unit desalter frequently results in upsets resulting in the “solids cycle” in which many refiners often find themselves. A major consideration is not to be too ambitious with the volume of recovered oil added to the crude charge since too high a level can quickly precipitate a desalter upset. It is recommended to slowly introduce the recovered oil to the crude charge while closely monitoring the desalter (e.g., try lines and the electrical system) so that any deterioration can be observed, and operational changes made to avoid an upset. However, there are some cases where “trickling” in the recovered oil is not possible.
In most cases, treatment strategies to clarify the oil is recommended, thereby resolving the complex emulsion to provide a better-quality oil that can be processed with reduced risk. It is possible to chemically treat the recovered oil with specialist slop oil demulsifiers to maximize the resolution of the complex emulsion and to drop increased amounts of solids and water in the slop tank prior to processing on the crude unit. The use of specialist solids removal additives as part of the desalter chemical program can also help to safely process the recovered oil. Not all recovered all streams can be treated chemically, and heavy, viscous emulsions will be difficult to resolve. In some cases, the only effective way to clarify the oil so that it can be processed safely is to utilize a three-phase centrifuge to separate the hydrocarbon, solids, and water. However, this is a costly undertaking and the economics of this operation have to be reviewed.
Lastly, if the refinery has a coker, it is possible to route the recovered oil directly to that unit and avoid the crude unit completely. However, this may not be possible if premium grades of coke are produced.
BRUCE ALLRED (Suncor Energy U.S.A.)
We have a leased three-phase centrifuge (oil, water, and solids) onsite, operated by a third party, which is used to separate solids from several slop oil and sludge streams produced at the refinery. Oil that is recovered from primary separation (API separators and tanks) in the wastewater treatment system is accumulated in a tank and tested for BS&W. If the BS&W is too high (greater than 1%), the oil is sent to the centrifuge. If the BS&W is low, we send the stream to a crude tank for reprocessing in a crude unit. Some would think this is expensive, but we have found the cost to be well worth it to eliminate problems with recycling and unnecessary accumulation of solids.