Question 55: What is considered the best-in-class design for coker main fractionator wash zones? Have refiners seen good performance and target run lengths using grids in this service?
Ralph Goodrich (KBC Advanced Technologies, Inc.)
Cokers today are normally designed to operate to maximize liquid yield from the unit. This will require the coker to operate at as low a recycle as possible while still maintaining the required product specifications for the heavy coker gas oil (carbon content, metals, asphaltenes, etc.). For a low recycle operation a spray chamber is the best-in-class.
Although it has been shown in the past to work in some units, there are some reliability issues as the grid requires frequent cleaning/replacement. In addition, any packing such as grid in the wash zone will require sufficient wash oil to maintain a minimal wetting rate to avoid coking in that section. This additional wash will increase the recycle thereby losing liquid yield. Thus, what we typically see today from the licensors are spray chamber designs which provide both higher reliability and lower recycle rates.
The lack of grid or other contact surface does tend to increase the Heavy Coker Gas Oil (HKGO) backend distillation and contaminants, but the improved reliability overrides the quality falloff.
Dual spray headers should be provided to further improve reliability and each should be sized for 50 to 75% of the total required wash rate. Wide angle full or hollow cone sprays (7 to 20 psi, 120° spray angles) should be specified with the hollow cone sprays providing the lowest recycle option. The smaller free passage area compared with a full cone spray, however, may make the nozzle more susceptible to coking.
The spray pattern requires sufficient overlap between the sprays but not as much as that required with a grid design. This allows the design to include fewer nozzles, larger free passage areas, and larger droplets resulting in a lower tendency for nozzle plugging and entrainment.
We have also seen some more novel designs recently which add more equipment in this section of the tower to both help clean the gas oil product and minimize the recycle.
The following slides illustrate the general progression of coker wash zone design modifications corresponding to the increased incentives to reduce recycle.
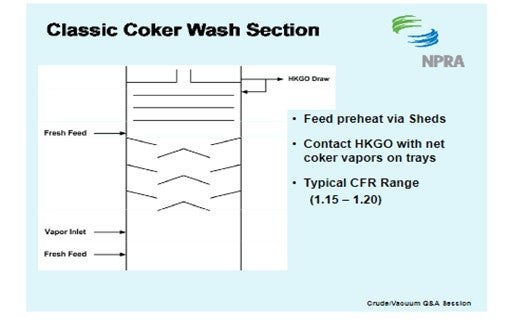
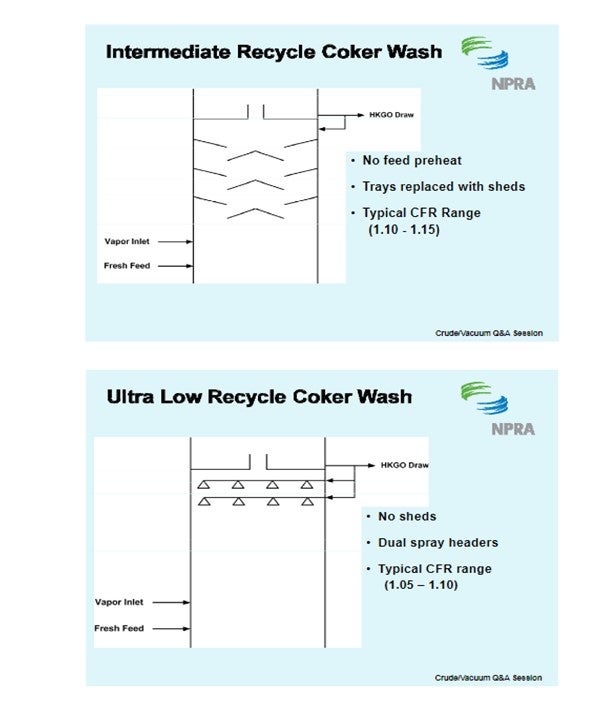
Frank Tracy (ConocoPhillips)
ConocoPhillips-designed cokers utilize an open chamber wash zone. Wash oil is delivered through dual spray headers equipped with hollow cone nozzles that provide redundant spray coverage. We do not have any experience using grid in this service.
Eberhard Lucke (Commonwealth E&C)
The answer to this question depends to a certain degree on the type of coker operation and the respective operational parameters. For an anode grade operation with a decent wash oil rate and higher recycle ratios, my experience with structured grid in the wash zone was excellent. We just had to make sure the liquid flow to the grid was always above the minimum required for wetting the surface area. In fuel grade operations with very low recycle ratios and minimized wash oil flow rates, I preferred the open spray chamber design.