Question 55: Leaks in a vacuum system can result in oxygen ingress into the process. What are the panelists’ experiences/practices with respect to safe sampling and monitoring of vacuum system off gas quality?
LEE (BP North America)
Oxygen ingress is a serious concern. For the vacuum units which route the tail gas for processing into a fuel gas header or to downstream LPG (liquefied petroleum gas) recovery unit, we require them to have an online O2 analyzer on the tail gas stream. In addition to identifying that a leak is occurring, the O2 indication alerts operators of a possible hazardous leakage point should pressure in the vessel go positive during an upset or a shutdown. The tail gas samples are also hazardous in that they can contain up to 20% H2S (hydrogen sulfide).
We are not aware of an industry detonation in the ejector area where the O2 is most likely to concentrate. Air leakage into the hotter zones of the vacuum tower, like in the transfer line area or some of the lower and hotter tower draw nozzle flanges, typically results in combustion products like CO2 (carbon dioxide) or CO (carbon monoxide) appearing in the off gas, as well as nitrogen. Depending on the magnitude of the leak and/or the leak point, more or less O2 will then appear in the off gas, which is the leak hazard indication we are measuring. Besides the process safety aspect of the O2 monitoring, we have seen instances of O2 and fuel gas creating significant burner pluggage issues due to polymerization products. An online O2 indication also provides a means of unit health monitoring that will help mitigate long duration periods of this issue.
If the particular vacuum unit routes the tail gas directly to fuel gas burners, then an O2 online analyzer is not required. In this configuration, flame arrestors are employed to prevent backflashing as a source of ignition. Monthly tail gas samples are then required for unit health monitoring. Because of the hazardous nature of the sampling, personnel conducting this activity are required to have appropriate PPE, or personal protective equipment. H2S monitors preclude inadvertent inhalation. Therefore, samples need to be taken at positive pressure somewhere after the third stage of ejector or equivalent. Where possible, we do have closed speed loop sample connections.
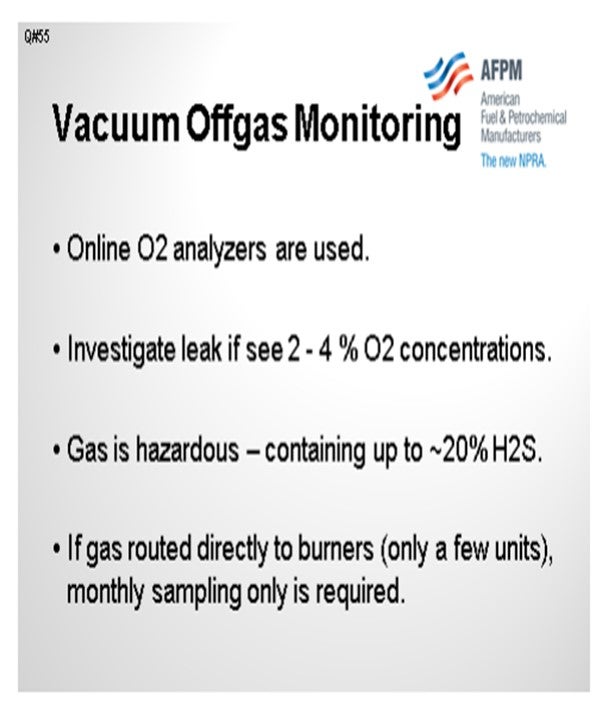
O2 analyzers have been installed in several units over the past five years based on these criteria. O2 levels of about 10% O2 are considered to be at the minimum O2 concentration or MOC (management of change) to support combustion and if an ignition source is available. If the tail gas O2 content reaches a concentration of 2% to 4%, investigations and risk assessments are commenced on identifying and troubleshooting potential leak sources prior to potential shutdown should the operating conditions reach near 10% MOC. Calculations are performed to determine the actual MOC at the particular tail gas composition from the unit of interest, but a 10% MOC is fairly typical.
This table shows some recent off gas analysis taken during troubleshooting of an air leak we had. It provides a magnitude of some of the light ends seen in the vacuum off gas. You can see that there is a range of light ends, olefins, and hydrogen. One interesting anecdote is that we actually had a helium tracer test done on one of our vacuum units; and surprisingly, the hydrogen content threw off the vendor analyzer equipment readings. However, hydrogen is a fairly common compound you will see in vacuum unit off gas.
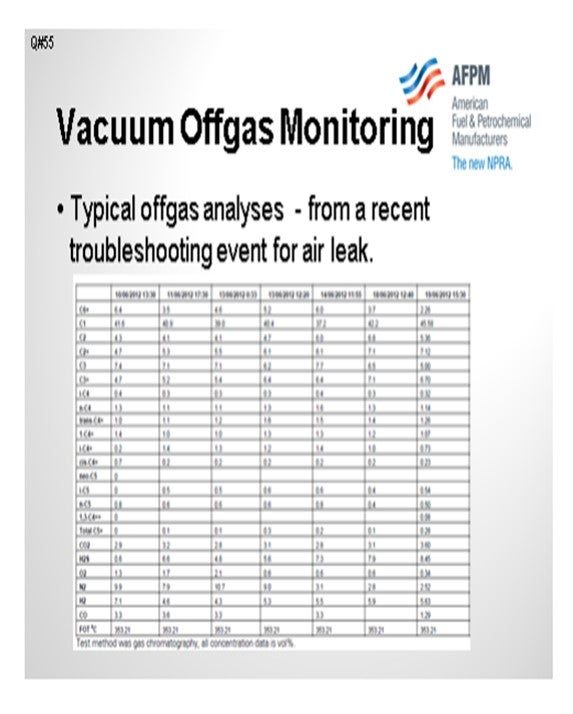
CLIFFORD (Motiva Enterprises LLC)
I want to add onto what Howard said. We typically sample the vent gas downstream of an amine absorber. Be careful because your amine selection may absorb CO2 from the sample, so it is important to look for nitrogen and/or oxygen. Proper sampling techniques are important to avoid H2S exposure if you are sampling it upstream or if you have a process unit upset. You also want to get a representative sample and ensure that the sample cylinder is not contaminated with air, which could lead to a false positive.
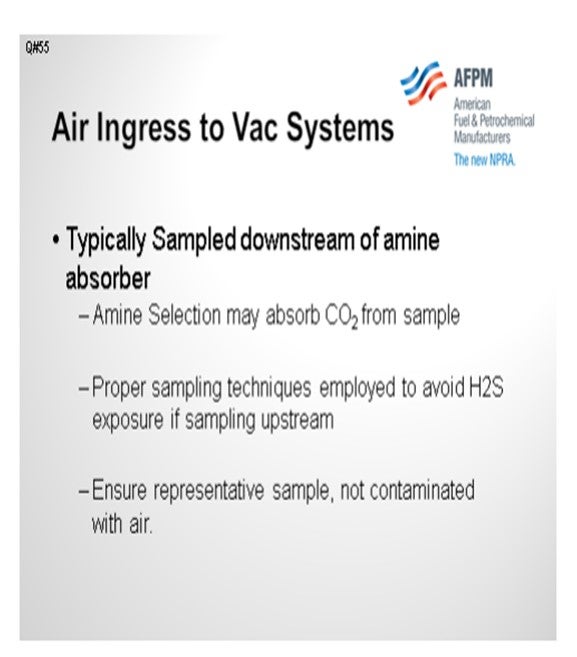
VILAS LONAKADI (Foster Wheeler USA Corporation)
In order to avoid any unsafe condition, do you have any automatic system that would alert the operator and cut in inert gas when the oxygen content in the vacuum off gas goes high?
LEE (BP North America)
It is not automated, but we do have some vacuum systems where fuel gas and nitrogen injection facilities dilute the off gas down to the lower O2 level. You are still going to get a little of natural leakage anyway. In one instance, there was such a small amount of cracked gas production with a low furnace temperature and a low cracking feedstock that the natural amount of O2 leakage actually caused the O2 concentration to go up into a high range. So that is where we inject the fuel gas for dilution, but it is not an automated system.
CLIFFORD (Motiva Enterprises LLC)
Samples of the vacuum off gas are periodically caught and analyzed via GC (gas chromatography). Samples are caught downstream of an amine absorber. The particular amine used at this site will absorb carbon dioxide, so attention should be paid to nitrogen, oxygen, and carbon monoxide. The presence of oxygen may indicate a leak in the cold section of the vacuum tower and the presence of nitrogen without oxygen may indicate a leak in the hot section. However, it not always the case that the oxygen is consumed by a leak in the hot section, so consideration for both areas must be considered. Also, it is important that proper sampling techniques are followed both to avoid exposure to the gas, which may be high in H2S if the amine scrubber is not performing adequately, and to ensure that a representative sample is caught and residual air that may be left in the sample container does not contaminate the results with false O2/N2 content.
BASHAM (Marathon Petroleum Corporation)
Due to the high H2S level in this sample, coupled with the pungent odor, purging the sample device to the atmosphere is not an acceptable option. For routine sampling, several (but not all) of our refineries have installed continuous sampling devices as standard practice. At the locations where the vacuum tower off gas is not routinely sampled a clear plastic sample bag is used. The bag is rolled up tightly to expel any air and then filled with the process gas. Any liquids in the sample can be seen in the bag before they potentially damage gas chromatograph equipment.
Regarding the concern for oxygen intrusion, it would take a significant amount of air to reach the LEL. The vacuum jets could not move this amount of air and would “break”, losing vacuum.