Question 54: What recent innovations have you made to instrumentation that has application in FCC units?
FOOTE (CHS Inc.)
I will just share some of what we have done that has impacted and improved safety, reliability, maintainability, and operability in the last 10 years on our cat units. One innovation has been adding vortex and ultrasonic flow meters in slurry service. I think we have installed six in our main column bottoms circuits. The advantage of these flow meters is that they do not require any flush oil addition. We have seen good reliability and accuracy with them. We also found that the ultrasonic meters have a better turndown than, say, the vortex meters, but we have yet to inspect them after a five-year run. I suspect that they will look just fine, because they are still reading reliably. The second innovation we applied is smart accelerated valve positions. Having this feature has improved the control ability of our operations. ‘Position read back’, ‘advanced diagnostics’, and ‘partial stroking’ functions that we already discussed are the types of smart valve positions which are nice to have on control valves.
Next is electronic remote sensor or pressure differential transmitters. Traditionally, for pressure differential and reactor level, we have installed the dP transmitter above the highest tap and then run the impulse lines down to lower taps. Sometimes those impulse lines can be 100 feet long; some systems are longer. This application takes a different approach. It basically installs two pressure transmitters that are factory-matched and electronically linked. You put a pressure transmitter at your two taps, and those two are linked, which then provides your electronic remote sensor. We recently implemented the application on our reactor head and stripper project that will be installed this spring, and we have dramatically reduced the number of impulse lines running along the structure. We are excited to see the outcome. I believe there is another refiner who has done a similar application, too. I think those impulse lines really make me nervous when you are using small bore piping. If one of them comes loose, it could result in a bad situation. So, reducing small bore piping is a big deal to me.
Modern hydraulic power units for FCC slide valves: We talked about the benefits from a safety perspective. We have also seen a control benefit from the control systems on two of our units that we have modernized. The controllability of critical parameters around slide valves has really improved and made us able to operate our full-burn unit – in compliance for CO (carbon monoxide) – with a highly hydrotreated feed. It is also worth mentioning an automated UT (ultrasonic testing) inspection technique called AUT (automated ultrasonic testing). Your Inspection Group may refer to it as such. Basically, it is just an automated UT external inspection of pressure vessels that are online. It is limited to vessels that are 350°F or less, but we have been able to identify anomalies. It has really cut down our pressure vessel discovery work during turnaround and generated a big benefit to us in the last 10 years, in terms of value. We just do not have very many pressure vessel “Aha!” moments during turnaround anymore.
MALLER (TechnipFMC Process Technology)
As far as innovations in instrumentation, our standard on the reactor regenerator remains to be the purged pressure taps. So, nothing has changed there, and we do not really see anything new coming. The remote sensor mentioned by Mr. Foote is very interesting and could warrant further investigation.
For level instruments, we have seen guided-wave radar-type level instruments becoming more popular, particularly for interface level measuring. Nuclear-type level instruments have been applied in a main fractionator bottom service, and that subject will be talked about later in another question. Nuclear-type level instruments have also been applied to catalyst hoppers. It seems like it should be feasible to apply them for the reactor/regen level, but I am not aware of anywhere it has been done successfully yet.
Lastly, I agree with Darin’s point about the ultrasonic flow instruments applied in slurry service. I have seen those working well, and it seems to provide a good deal of improvement in terms of reliability.
BHARGAVA (KBC Advanced Technologies, Inc.)
In addition to what the panel members just said, we have focused more on the data quality. From the perspective of monitoring the FCC, we think having good mass balance closures is most important. Good mass balance closure not only helps us monitor the unit; but when we do step tests or test runs, we are able to find small changes in the operation of the unit that help us identify the most profitable operation. We have installed Coriolis meters as a way to get better mass balance closures. In addition, we have started recommending and installing tunable diode laser spectroscopy meters for flue gas analysis. These meters allow you to improve the flue gas analysis composition detection into parts per billion, if needed. We have been looking for CO in very small levels, because knowing these levels helps improve the flue gas analysis.
From an equipment care and conditioning perspective, we are installing more and more wireless vibration monitors for compressors and pumps in the FCCs. And finally, Yokogawa has a list of EJX transmitters for pressure differential measurements. These transmitters are much more accurate than what you have in service today.
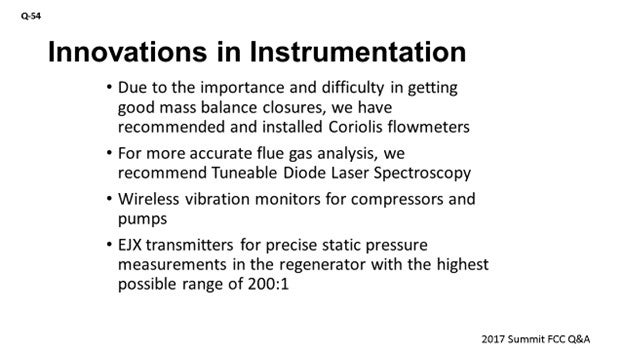
DAVE FERGUSON (Tracerco)
Sanjay, where are you installing the Coriolis meters?
BHARGAVA (KBC Advanced Technologies, Inc.)
The Coriolis meters are being put on the external boundary of the FCC to allow us to look at the feed meters, gasoline meters, and diesel meters to get the mass balance closures. These Coriolis meters are expensive, so you are better off installing them across the mass balance boundary.
PAUL DIDDAMS (Johnson Matthey)
I have a question for the audience. Is anyone using online feed analyzers these days? How many people are using an NIR (near-infrared), NMR (nuclear magnetic resonance), or some online feed analyzer? Is anyone doing that? None. Interesting. Okay. Thanks.
DARIN FOOTE (CHS Inc.)
In our FCCUs, we have employed a few noteworthy instrumentation advances that have improved safety, reliability, maintainability, or operability in the past 10 years.
-
Vortex and Ultrasonic Flow Meters in FCC Slurry Service: We have a combination of these our main column bottoms flow circuits. These meters have proven to be reliable and accurate and do not require flush connections like traditional orifice meters in slurry service. The ultrasonic flow meters have proven to be more accurate in low-flow applications. For vortex-type meters in horizontal mounting, applications ensure that the electronics are installed remotely or side-facing to ensure that the heads do not overheat from the hot process lines. For ultrasonic flow meters, pay close attention to the manufacturer’s insulation details for hot service.
-
Smart and SIL-Rated Valve Positioners: Position read back, advanced diagnostics, on control valves has improved control and reliability. SIL-rated positioners on SIS valves allows for partial stroke testing which can extend time between SIS testing intervals. This is important as we extend unit run lengths.
-
Electronic Remote Sensor Pressure Differential Transmitters: These are two matched and certified pressure transmitters that calculate pressure differential electronically as opposed to a single dP transmitter with impulse lines from two separate locations. This application has dramatically reduced the number of impulse lines on the FCC Rx/regen/stripper system.
-
High-Speed Pressure Transducers: Some operators have installed high-speed pressure transmitters in standpipes where fluidization problems exist. These transmitters are only used for short periods of time and typically do not send data to the plant historian.
ALEX MALLER (TechnipFMC Process Technology)
For level measurement, guided-wave radar level instruments have been gaining popularity and been successfully applied in numerous services, especially for interface levels. Nuclear-type level instruments have been more or less accepted in other processing units in refineries and have made their way into the FCCU for severe services, such as main fractionator bottoms level, and for hopper levels. Attempts have been made to apply the nuclear types of instruments to measure catalyst levels in the FCCU reactor or regenerator with varied degrees of success. On the structure, the standard for level remains dP-type instruments utilizing purged taps.
For flow measurement, ultrasonic type flow meters have been successfully applied in slurry service where a standard orifice plate-type instrument may face reliability issues. We have also seen ultrasonic flow meters successfully used for measurement of flow in flare headers.
SANJAY BHARGAVA (KBC Advanced Technologies)
Due to the importance and difficulty in getting good mass balance closures, we have recommended and installed Coriolis flowmeters. For more accurate flue gas analysis, we use Tunable Diode Laser Spectroscopy, wireless vibration monitors for compressors and pumps, and EJX transmitters for precise static pressure measurements in the regenerator, with the highest possible range of 200:1.