Question 53: With respect to hydrotreating, what is the typical (CO + CO2) impurity in hydrogen produced from pressure swing adsorption (PSA): 10 ppm or 50 ppm? What problems can be expected if the (CO + CO2) exceed this value? If the hydrotreaters can handle higher than (CO + CO2), is it possible to run the PSAs harder and produce more hydrogen?
SIVADASAN (UOP LLC, A Honeywell Company)
UOP has designed around 1000 PSA units. For most of the refinery applications, the impurity limit has been set to less than 10 ppm. The table shows a comparison between specs when relaxed from 10 to 100 ppm. H2 recovery was also checked when specs were tightened from 10 ppm to 1 ppm. You can see that the delta hydrogen recovery is not that much – about 1%, but relaxing the specs has an effect on the downstream hydroprocessing unit.
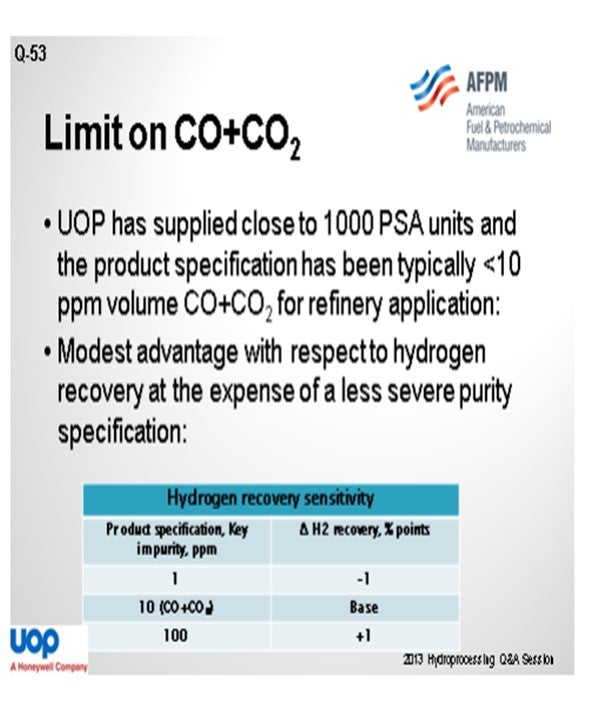
These carbon oxides may get absorbed on the catalyst’s active surface and affect the HDN and hydrogenation reactions. They can also undergo methanation reactions in the reactor if present in higher concentrations. Some of the partial reaction products from the methanation reaction and un-reactive carbon oxides reduce the hydrogen partial pressure and increase the deactivation rate of the catalyst. If these carbon oxides increase in percent levels in a short period of time, there will be the risk of getting a temperature excursion. However, the main concern is temperatures less than 200°C. Carbon monoxide reacts with reduced nickel to produce nickel carbonyl, which causes health and safety issues when you are trying to open your reactor flanges or valves during the shutdown of the unit.
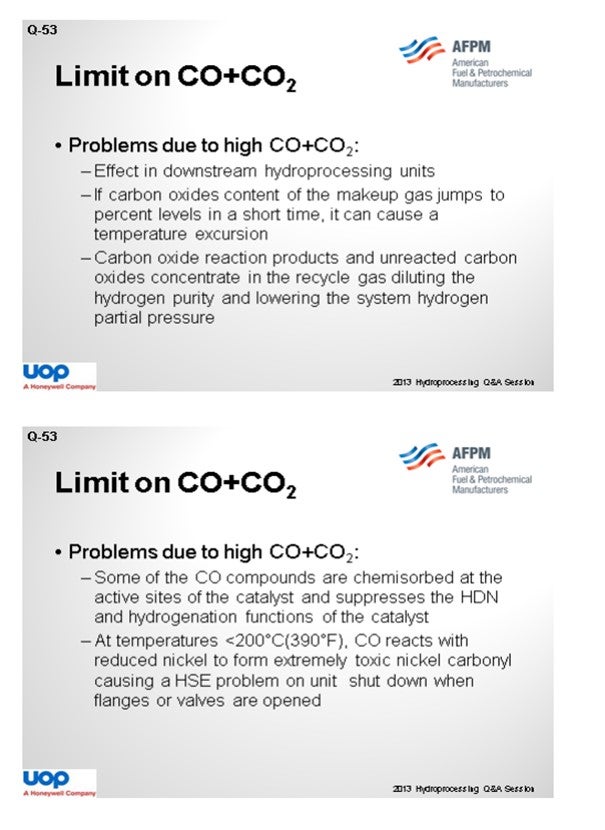
GATES (Motiva Enterprises LLC)
For PSAs, the design of a 10 to 50 ppmv (parts per million by volume) slip is common. A downstream noble metal catalyst may require a lower value. Base metal hydrocracking and hydroprocessing catalysts can typically tolerate a higher slip. But as was already mentioned, you will want to maintain a constant slip. If the CO and/or CO2 suddenly spikes up, you may have temperature instability in your reactors. Increasing the slip can increase the hydrogen recovery by increasing the adsorption time on the PSA; but really, it is limited overall by the adsorbent. There is some concern for hydroprocessing units that CO or CO2 in the gas going to the unit can form nickel carbonyl at shutdown. So, make sure you reduce the CO that might be in that reactor, as well as the temperatures, before you open up any flanges or change the atmospheres.
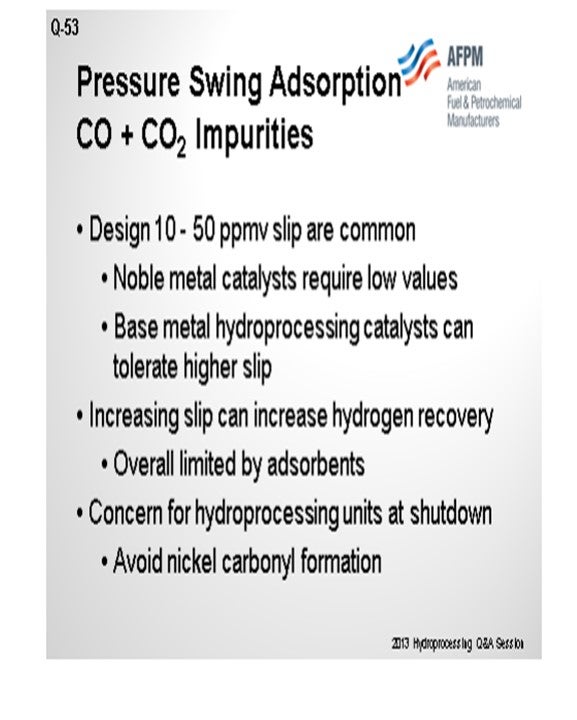
SHARPE (Flint Hills Resources, LP)
CO is a temporary catalyst poison which inhibits the HDS reaction more so than HDA (hydrodealkylation). The effect is not visible at 5 ppm; CO is insignificant at 15 ppm. CO2 has about 50% less of an impact than CO. The recommended mitigation is to increase your purge and/or reduce CO in the makeup hydrogen. I have a bullet on the slide suggesting you consult with your catalyst vendor about the recommended maximum for your unit. I have seen guidelines from less than 20 ppm to less than 50 ppm to 100 ppm; so, it seems to be catalyst-specific.
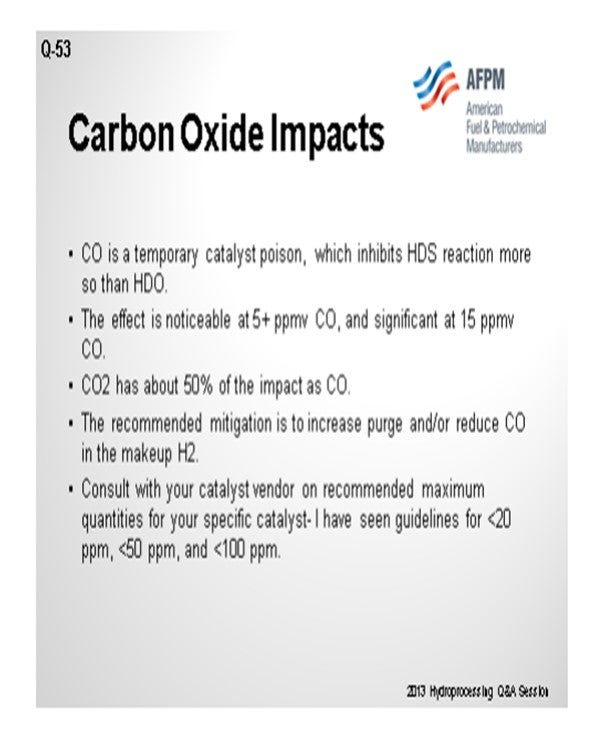
RAJESH SIVADSAN (UOP LLC, A Honeywell Company)
High hydrogen purity is obtainable with a PSA process (99.9%+). However, a very modest advantage, with respect to hydrogen recovery, can be gained at the expense of a less-severe purity specification. The table below shows the impact of the CO levels on the hydrogen recovery in a PSA. As can be seen, the delta recovery is small for a relaxed specification. UOP has supplied close to 1000 PSA units, and the product specification has been typically less than 10 ppm volume CO+CO2 for refinery applications.
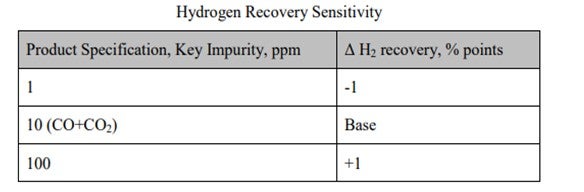
Ni catalyst is great for methanation reactions (exothermic). Consequently, there is a concern that it can experience a temperature excursion upon the carbon oxides spiking up. If the carbon oxides content of the makeup gas jumps to percent levels in a short time, it can cause a temperature excursion. CO is worse than CO2 because it adsorbs more strongly, reacts with more heat release, and is not readily sponged out of the recycle gas into the separator liquid.
However, there are also some process/catalyst activity effects which are outlined below:
• Some of the CO compounds are chemisorbed at the active sites of the catalyst, and this suppresses the HDN and hydrogenation functions of the catalyst. This activity impairment is only temporary as the chemisorption is fully reversible.
• Methanation and shift reactions occur in the hydrocracking environment, and the methanation reactions can result in substantial exotherms.
• Carbon oxide reaction products and unreacted carbon oxides concentrate in the recycle gas diluting the hydrogen purity and lowering the system hydrogen partial pressure.
• At temperatures less than 200°C, CO reacts with reduced nickel to form extremely toxic nickel carbonyl. This is a problem on unit shutdown, and any flanges or valves are opened. To avoid exceeding the eight-hour exposure limit nominally requires less than 10 ppmv CO in the makeup hydrogen during cooldown to below 200°C.
CHRIS STEVES (Norton Engineering)
10 ppmv (CO + CO2) in the product stream from an H2 PSA unit is a typical design condition. If (CO + CO2) exceeds this value for short periods of time, then, initially, there is no major impact on the life of the adsorbent. However, extended off-spec operation, which is anywhere from several hours to a full shift at levels approaching an order of magnitude higher than design, will start having an impact on adsorbent life. H2 PSA vessels are typically a multi-layered packed bed with the upper layers sensitive to impurities being removed in the lower layers. Common examples are water vapor/C3+ hydrocarbon removal in the alumina/silica gel pre-layers and CO2 removal in the activated carbon layer below the zeolite.
Off-spec impurity levels in the product are often a tell-tale sign that strongly adsorbing impurities being contained in the lower layers of the packed bed may be moving further into the adsorbent mass than intended. If the CO2 breakthrough wave is allowed to slip from the activated carbon layer into the zeolite layer during off spec operation, then adsorption-desorption working capacity of the zeolite layer for CO removal will progressively decrease over time. Once contaminated, an adsorbent layer is very difficult to regenerate, even with the vessel offline. Special care should be taken with off spec operations during warmer conditions as adsorption-desorption capacity will decrease with increasing temperature based on the equilibrium isotherm.
Running the PSA with higher H2 recovery, and hence higher (CO + CO2) levels, needs to be weighed against adsorbent life based on progressive contamination. When the source of feed gas is from a steam methane reformer, there is little margin for increased impurity levels. Verify that the CO slip from the SMR (steam methane reformer)/water gas shift reactor train is within normal operating limits; otherwise, the PSA will consume more H2 than design for the internal regeneration steps to decrease CO level. Another option is reloading the upper layer in the vessel with a zeolite that offers higher working capacity for CO removal. With off gas PSA systems where the source of feed gas is a H2-rich stream from a different process unit, consider bypassing a portion of feed gas around the PSA unit to achieve the desired H2 purity level. If downstream equipment is insensitive to all species present in the feed, and if hydrogen partial pressure is the primary driver for PSA cleanup, then running the PSA at design impurity levels with bypass will maximize adsorbent life while maximizing H2 recovered from the feed. An additional consideration with off gas PSA systems is tail gas compression downstream of the buffer drum if the destination is a fuel gas header at elevated pressure. Significant increases in H2 recovery can be achieved when the tail gas from a PSA vessel is discharged at pressures approaching 3 to 5 psig.