Question 53: During the coking cycle, how are drum skin temperatures used to monitor drum wall condition?
Frank Tracy (ConocoPhillips)
Monitoring drum wall conditions during the drum cycle is best performed using strain gauges. Each strain gauge location will typically be fitted with gauges in both the axial and hoop directions and have an associated skin thermocouple. These can be seen in the photograph.
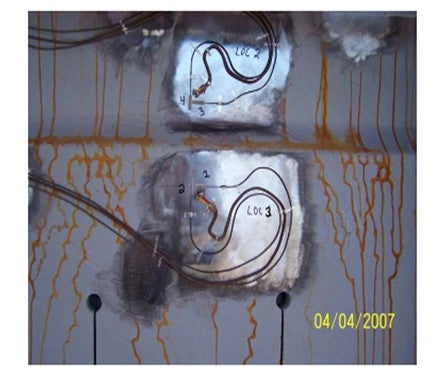
The largest stresses typically occur during the water quench portion of the drum cycle. Strain gauges allow a refiner to minimize stresses during this critical portion of the drum cycle by adjusting quench water rates. However, this is a longer-term project as you must evaluate enough cycles to have representative data for evaluation before making an operating change and then collect enough data afterwards to make a meaningful comparison.
Selecting the locations for strain gauge installation is something that requires some careful consideration. Strain gauges can be retrofit onto existing drums and are recommended as part of new coke drum installations. Typically, it is only necessary to fit strain gauges on one drum in each set of identical drums receiving the same feed since all drums will behave similarly.
Skin temperatures alone do not provide the same information as strain gauges. They can be used to help ensuring adequate back warm. They may be useful, if strategically deployed, to possibly identify uneven quenches.
We have used or are currently using strain gauges at several of our cokers and plan to use them at some additional locations.
Eric Thraen (Flint Hills Resources)
We have conducted several coke drum stress studies using outside consultants. Coke drum skin temperatures and strain gauges are included in the stress studies. The strain gauges are used primarily for these engineering studies, while the temperature indicators are used by the operating personnel, along with quench water flowrates and coke drum pressure rate of change during the drum cooling step to manage the rate of cooling so as to meet the targeted coke drum lifecycle. Quench water flow and coke drum pressure are included in the coke drum cooling program as added checks to ensure against too rapid quenching during the cooling cycle. The minimum coke drum preheat prior to switching feed into a drum is based on strain studies by the outside consultants. Although the stresses during water-cooling are generally highest, a minimum drum preheat is also established to prevent excessive stresses during the drum heating cycle.
Eberhard Lucke (Commonwealth E&C)
Drum skin temperatures are mainly monitored in the critical areas around the drum skirt attachments and the first 1-2 circumferential welds from the bottom in the cylindrical portion of the drum. The data from these skin temperature elements can be used in the DCS to monitor the change in temperature over time during the critical stages of the drum cycle, the drum quench and the drum warm-up/switch. Keeping the dT/dt in a certain range will minimize the thermal stress on welds and drum wall and will increase the lifetime of the coke drums. These dt/dt values can be integrated into the control scheme for the quench water ramp function, the warm-up controls and the drum switch control, depending on the degree of automation you have in your unit.